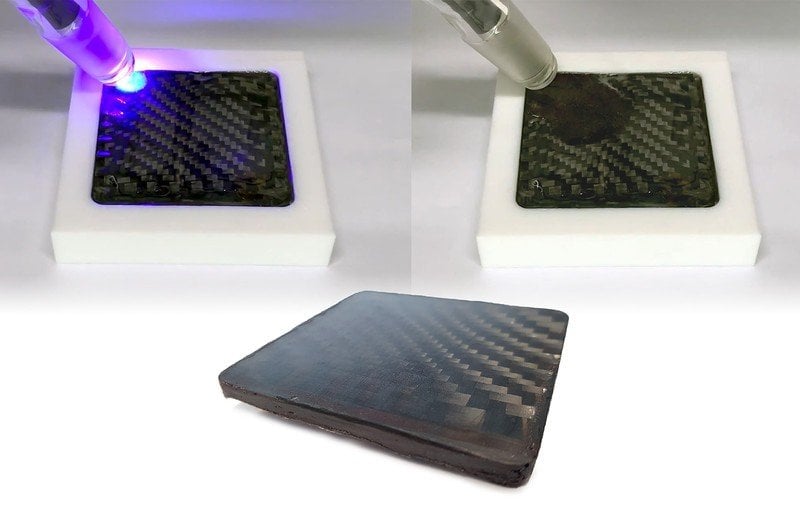
An der TU Wien hat man eine hocheffiziente Technologie für das Aushärten von Epoxidharzen entwickelt. Der Vorteil liegt unter anderem in einem dramatisch reduzierten Zeit- und Energieaufwand. Ein kurzer Lichtimpuls reicht, um die Harze auszuhärten. Laut Forschern tut es sogar eine Taschenlampe.
Epoxidharze gehören heute zu den Standard-Kunststoffmaterialien und spielen in vielen Industriebereichen eine bedeutende Rolle. Man verwendet sie etwa um elektronische Bauteile zu isolieren oder um mechanische Teile zu fixieren. Ein weiterer großer Anwendungsbereich sind Faserverbundstoffe, die aus Karbon- oder Glasfaser hergestellt und von Epoxidharz als Bindemittel fixiert werden. Diese haben ausgezeichnete Materialeigenschaften und werden in Automobil- und Schiffsbau, in der Luft- und Raumfahrt sowie Windenergie eingesetzt.
Komplizierte Herstellung
Problematisch an den Faserverbundstoffen ist deren komplizierte und teure Herstellungsweise. Um die Bauteile auszuhärten, sind sehr große Öfen und hohe Temperaturen notwendig – und das ist oft mit hohen Energiekosten verbunden. Verbreitet ist der Einsatz von Zweikomponenten-Formulierungen. Diese werden vor Ort mühsam vermischt und müssen dann sehr schnell verarbeitet werden, bevor sie dem zeit- und energieaufwändigen Aushärteprozess zugeführt werden.
Neue Formel
Einem Forscherteam um Professor Robert Liska vom Institut für Angewandte Synthesechemie an der TU Wien gelang es, eine neue Epoxidharz-Formel zu entwickeln, die den Energieaufwand nahezu eliminiert und weniger zeitaufwändig ist. Unter Anwendung der Frontalpolymerisation geht das Material innerhalb von Sekunden vom flüssigen in den festen Zustand über. Die spezielle Epoxidharz-Formel wurde von der TU Wien bereits unter dem Namen Curratec patentiert.
Polymerisationsfront
Die Forscher sprechen von einem Bindemittel, das auf Befehl reagiert. Mit Befehl ist ein einmaliger lokalisierter Impuls von entweder UV-Strahlung oder Wärme gemeint. Der Impuls setzt Reaktionswärme frei und löst eine Reaktionskaskade aus. Diese führt dazu, dass sich eine Polymerisationsfront mit bis zu zehn Zentimetern pro Minute durch die gesamte Formulierung bewegt – und eine vollständige Aushärtung des Materials erfolgt. Dieser Prozess funktioniert bei der Isolation und Fixierung elektronischer Bauteile genauso wie bei der Fixierung von Faserverbundstoffen.
„Der entscheidende Vorteil dieser Methode ist, dass man nicht wie bei anderen lichthärtenden Materialien das gesamte Harz beleuchten muss“, erklärt Liska. „Es genügt, irgendeinen beliebigen Punkt mit Licht zu treffen. Der Rest härtet dann ganz von alleine, ohne weiteren Energieeintrag, aus.“

Minimaler Energieaufwand
Christoph Schnöll leitet das Team Curratec und ist für die Kommerzialisierung der Technologie verantwortlich. Er betont die enorme Energie-Einsparung, die bei neunundneunzig komma neun Prozent liegt. Zitat: „Mit unseren neuesten Weiterentwicklungen haben wir sogar erreicht, dass eine einfache Taschenlampe genügt, um die Härtungsreaktion zu starten. Das ist ein absolutes Novum. Wenn man daran denkt, dass anstelle eines großen Industrie-Ofens nur mehr eine kleine Taschenlampe notwendig ist.“
Unterwasserkleber
Den Zeitaufwand kann die neue Technologie teilweise von Tagen auf Minuten oder Sekunden reduzieren. Die neue Aushärtungsart läuft innerhalb des Materials und von der unmittelbaren Umgebung weitgehend entkoppelt ab. Dadurch kann Epoxidharz beispielsweise auch unter Wasser vollständig aushärten. Das Aushärten unter erschwerten Bedingungen kann zum Beispiel die Kanalsanierung oder die Reparatur von Brückenpfählen wesentlich erleichtern. Darüberhinaus fallen auch umweltkritische Reagenzien weg.
Verbesserte Eigenschaften
Umfangreiche Tests zeigten, dass die mit Curratec Frontalpolymerisation hergestellten Materialien konventionell gehärtete Epoxidharze in allen relevanten Eigenschaften übertreffen. Aus Curratec hergestellte Duroplaste bieten zum Beispiel hohe mechanische Festigkeit und Zähigkeit, hohe Feuchtigkeits- , Chemikalien- und Korrosionsbeständigkeit sowie hohe thermische und elektrische Eigenschaften. Wie die Viskositätsmessung zeigte, verfügen die Materialien auch über eine hohe Lagerstabilität.
Damit ergeben sich viele neue Anwendungsmöglichkeiten. Das Forscherteam ist nun auf der Suche nach Industriepartnern, um das Epoxidharzsystem in weiteren Machbarkeitsstudien für definierte Anwendungen zu testen und zu optimieren.
Mehr über Curratec: www.curratec.com
Auch interessant:
Das ressourcenschonende Potenzial des 3D-Beton-Drucks nutzen