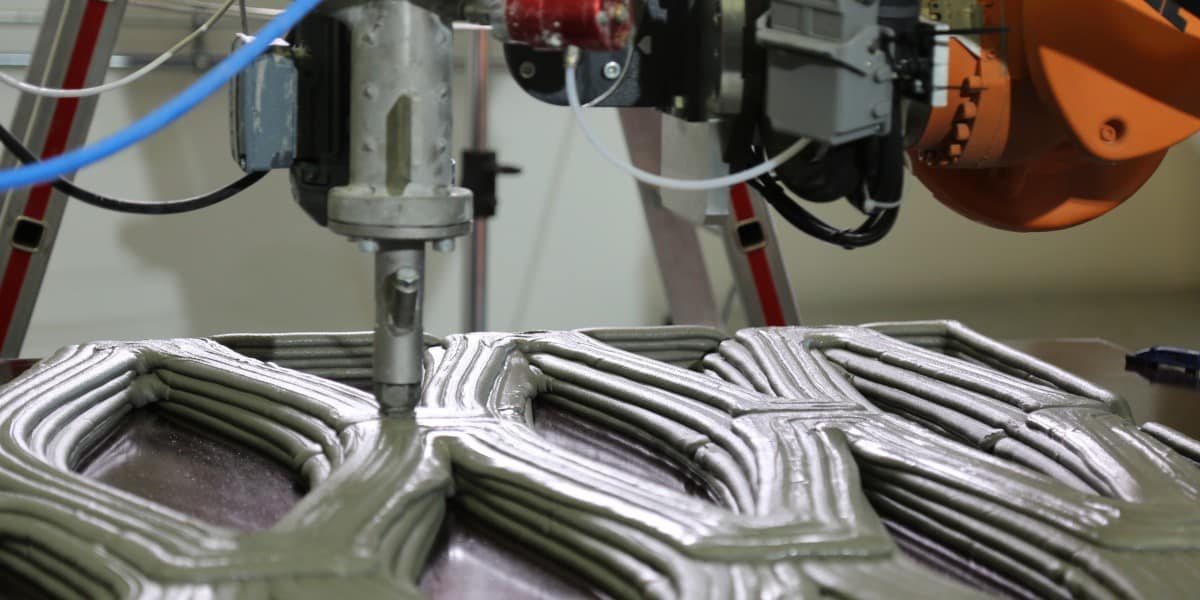
Das Haus aus dem 3D-Beton-Drucker ist noch Utopie, könnte aber das Bauwesen enorm vereinfachen. An der TU Graz wurde eben ein Projekt abgeschlossen, in dem zukünftige Einsatzfelder der Technologie getestet wurden. Leitmotiv war der ressourcenschonende Einsatz von Rohstoffen.
Viele Forschungsteams beschäftigen sich mit dem 3D-Druck von Beton und alle stehen vor ähnlichen Problemen, erklärt Stefan Peters, der Leiter des Instituts für Tragwerksentwurf an der TU Graz. Im Wesentlichen gehe es um die Zusammensetzung des Betons und die Art der Maschinen, die für den 3D-Druck einsetzbar sind. Wenn diese Probleme gelöst seien, habe die Technologie das Potenzial, den Betonbau von Grund auf zu ändern, so der Wissenschafter.
Effizienter Ressourceneinsatz
Er selbst forscht in einem interdisziplinären Team, welches das ressourcenschonende Potenzial des 3D-Beton-Drucks nutzen möchte. Beton ist der meist eingesetzte Baustoff weltweit. Die Zement- und Stahlproduktion verbraucht große Mengen an fossilen Rohstoffen wie Kohle und Öl. „Aktuellen Berechnungen zufolge sind die fossilen Rohstoffe Kohle und Öl nur noch gut hundert Jahre in der heutigen Form nutzbar. Hinzu kommt, dass die Herstellung der gängigen Baustoffe große Mengen an CO2 freisetzen. Mit einem effizienteren Ressourceneinsatz könnte hier viel eingespart werden“, erklärt Peters.
Unflexible Schalenbauweise
Konventionell werden Betonfertigteile in Schalenbauweise gefertigt. Dabei handelt es sich um eine Art Gusstechnik: Flüssiger Beton wird in eine zuvor gebaute Schalung gefüllt und verfestigt sich in gewünschter Form. Das Verfahren ist einfach, schnell und zuverlässig. Die gefertigten Bauteile sind sehr robust. Problematisch am Verfahren ist ein Mangel an Flexibilität, der sich in einem hohen Ressourcenverbrauch und eingeschränkten Designmöglichkeiten äußert:
- Um das Verfahren wirtschaftlich zu halten, werden aus einer Schalung immer gleiche Bauteile gefertigt – auch wenn es nicht notwendig ist, immer gleich viel Material zu verbauen.
- Die Herstellung von individuellen oder geometrisch anspruchsvollen Schalungen ist teuer und oft nicht rentabel. Deshalb werden diese oft schon im Planungsprozess ausgeschlossen.
Als Beispiel für die Schalenbauweise nennt Peters ein klassisches Deckenelement, das europaweit für Millionen von Quadratmetern eingesetzt werde. Dieses hat ein Volumen von rund dreißig Zentimetern, eine Spannweite von rund acht Metern und wird von Stützelementen getragen.
Individuell planbarer 3D-Druck
Dieses Deckenelement war eines von zwei Fallbeispielen im Forschungsprojekt. Im 3D-Druck können individuell geplante Elemente auf Basis eines digitalen Modells umgesetzt werden. Peters und sein Team überlegten, an welchen Stellen Beton einzusparen sei, ohne an Performance zu verlieren.
Im zweiten Fallbeispiel sollte ein verschnörkeltes Fassadenteil, das in einer Schalung nicht produzierbar wäre, dreidimensional gedruckt werden.
Basis für das Forschungsprojekt war die rechnerische Untersuchung der beiden Elemente und die Prüfung eines sparsamen Rohstoffeinsatzes.
Anschließend mussten die Fahrwege des Druckroboters ganz genau berechnet werden. „Das ist so, als würde ich ein Haus zeichnen, ohne dabei den Stift abzusetzen“, erklärt Peters.
In dem grundlagennahen Forschungsprojekt forscht ein interdisziplinäres Team aus Architekten, Bauingenieuren, Maschinenbauern und Materialtechnologen. Auch Industriepartner waren eingebunden, die in ihrer Gesamtheit den gesamten Produktionsweg eines Betonfertigteils abbilden.
Maschine und Betonmischung
Um die neue Bautechnik zu überprüfen, wurde ein Drucker gebaut. Der geeignete Druckkopf entstand in Kooperation mit einem Firmenpartner. Die Betonmischung wurde trocken in einem Big-Bag positioniert, mittels Schneckenpumpe aufbereitet und durch einen langen Schlauch zum Druckkopf transportiert. Der Druckkopf legt den Beton in Bahnen ab.
Fordernd war die Optimierung der druckbaren Betonmischung und vor allem das Erreichen einer pumpbaren Konsistenz. „Der Beton muss im Fluss durch die Druckdüse noch transportfähig sein und darf auch bei kurzen Pausen nicht verkleben. Gleichzeitig darf er, an seinem Bestimmungsort angekommen, aber nicht mehr verrinnen und muss mit der zuvor aufgetragenen Schicht eine Bindung eingehen“, erklärt Andreas Trummer vom Institut für Tragwerksentwurf der TU Graz. Mittlerweile habe man eine feine Mischung gefunden. Die gröbsten Teile sind maximal drei Millimeter groß.
Auch die Verbindung zwischen den einzelnen Betonbahnen war erst nach mehreren Versuchen zu erreichen.
Mitte November waren alle Probleme gelöst und das Team war mit den Ergebnissen der ersten Druckversuche im Institut für Konstruktiven Ingenieurbau zufrieden.
Kooperation mit Wirtschaftsunternehmen
Bis das Haus aus dem Betondrucker kommt, wird es noch einige Zeit dauern. „Wir als TU Graz sind aber ganz vorne dabei, wenn es um die zukünftigen Einsatzfelder der neuen Technologie geht. Denn darüber haben sich bisher nur sehr wenige Gedanken gemacht“, sagt Peters. Nachfolgeprojekte sind bereits in Planung.

Das Projekt lief unter dem Titel COEBRO (Additive Fabrication of Concrete Elements by Robots) und wurde von der Österreichischen Forschungsförderungsgesellschaft (FFG) und Partnern aus Wissenschaft und Wirtschaft über das Bridge-Programm finanziert. Bridge fördert die Zusammenarbeit von Forschungsstätten und Industrie, um praxisnahe Grundlagenforschung zu ermöglichen und neue Forschungsfelder zu erschließen.
Neben dem Institut für Tragwerksentwurf, dem Institut für Betonbau und dem Labor für konstruktiven Ingenieurbau waren folgende Unternehmen beteiligt:
- der Energie- und Automatisierungstechnik-Konzern ABB
- die Anlagenbaufirma Hage
- das Chemie-Unternehmen Sika
- der Schalungs- und Gerüstbauer Peri
- der Fertigteilspezialist Kirchdorfer
Auch interessant:
Europas erste industrielle 3D-Betondruckerei befindet sich in Eindhoven