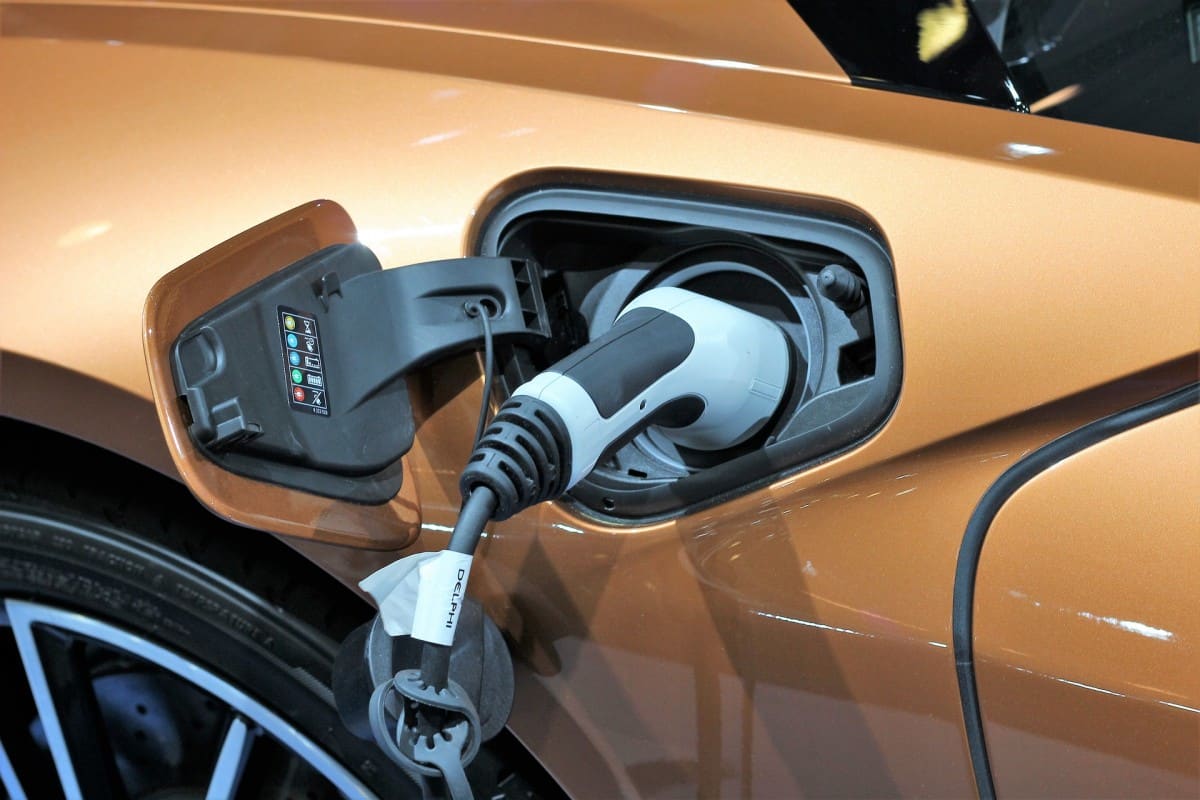
Elektroautos sind gut für die Umwelt. Das ist sicher eine treffende Aussage – besonders wenn der Strom für die Fahrzeuge nicht aus Kohlekraftwerken gewonnen wird. Wie sieht es aber mit den Stromspeichern, den Batterien, der Autos aus? Da gibt s sowohl bei der Produktion als auch bei der Leistung und Haltbarkeit noch reichlich Luft nach oben. Forscher des Fraunhofer Instituts für Werkstoff- und Strahltechnik IWS in Dresden haben nun einen Weg gefunden, um genau diese Schwachstellen der Elektromobilität anzugehen.
Bisher kauften die großen Automobilhersteller die Zellen für die Batterien aus mehreren Gründen in Asien ein. Asiatische Technologiekonzerne haben jahrzehntelange Erfahrungen in der Massenproduktion von Batteriezellen, und in der Produktion wird sehr viel Energie verbraucht. Und die ist in Deutschland sehr teuer.
Um das künftig zu vermeiden, haben die Dresdner Ingenieure ein besseres und auch kostengünstigeres Produktionsverfahren entwickelt, das Energiekosten spart und auch giftige Lösungsmittel in diesem Prozessschritt überflüssig macht: Sie beschichteten die Elektroden der Energiespeicherzellen mit einem trockenen Film statt mit flüssigen Chemikalien.
„Unser Transferverfahren zur Trockenbeschichtung zielt darauf ab, die Prozesskosten in der Elektrodenbeschichtung spürbar zu reduzieren“, betont Dr. Benjamin Schumm, Projektleiter am Fraunhofer IWS. „Die Hersteller können dadurch auf giftige und teure Lösungsmittel verzichten und Energiekosten bei der Trocknung sparen. Außerdem lassen sich mit unserer Technologie auch Elektrodenmaterialien verwenden, die sich nasschemisch kaum oder gar nicht verarbeiten lassen.“

Für künftige Batterien mit höherer Energiedichte werden aber genau diese Werkstoffe benötigt. „Wir denken aus all diesen Gründen, dass unsere Technologie dabei helfen kann, eine international wettbewerbsfähige Batteriezellproduktion in Deutschland und Europa möglich zu machen.“
Ende der klassischen Nasschemie?
Bei der Produktion der Zellen wurden die Batterieelektroden bisher meist in einem aufwändigen nasschemischen Verfahren beschichtet. Dabei wurden die Aktivmaterialien, die später die gespeicherte Energie freisetzen sollen, erst mit speziellen Zusatzstoffen zu einer Paste gemischt. Da hier nicht nur teure, sondern meist auch giftige, organische Lösungsmittel zugesetzt werden, sind zum Schutz der Fabrikarbeiter und der Umwelt aufwändige Vorkehrungen für Arbeitsschutz und Wiederaufbereitung notwendig. Nachdem die Paste auf dünne Metallfolien aufgestrichen ist, findet ein sehr Strom-intensiver Trockenprozess statt. Dutzende Meter lange Heizstrecken trocknen die beschichteten Folien, bevor sie weiterverarbeitet werden können.
Diese umweltschädlichen und teuren Schritte fallen bei der Trockenbeschichtung weg, da das Aktivmaterial mit bindenden Polymeren gemischt wird. Dieses Trockengemisch wird mit Walzen zu einem rund 100 Mikrometer dicken Elektrodenfilm verarbeitet. Der wird dann auf eine Aluminiumfolie aufgetragen wodurch die Batterieelektrode entsteht.
„Auf diese Weise können wir auch Materalien für neue Batteriegenerationen verarbeiten, bei denen die klassischen Verfahren versagen“, schätzt Benjamin Schumm. Dazu würden zum Beispiel Energiespeicher, die Schwefel als Aktivmaterial nutzen zählen oder sogenannte Festkörperbatterien, die statt brennbaren Flüssigelektrolyten ionenleitende Feststoffe einsetzen.
„Diese Batterien werden mehr Energie im gleichen Volumen speichern können als heutige Lithium-Ionen-Batterien“, sagt der Wissenschaftler vom Fraunhofer IWS mit Blick auf die Zukunft. „Diese Festelektrolyte können jedoch im Kontakt zu Lösungsmitteln ihre Funktion verlieren. Um diese Speicher herzustellen, eignet sich daher ein lösemittelfreies Beschichtungsverfahren deutlich besser.“
Einen Meilenstein zur Herstellung von Festkörperbatterien haben die Dresdner Forscher nach eigenen Aussagen bereits erreicht: Sie machten es möglich, „Elektroden mittels Trockenfilmverfahren mit extrem niedrigen Bindergehalten herzustellen.“

Pilotanlage in Finnland
Gemeinsam mit Industriepartnern wollen die Wissenschaftler die Prozesse nun verfeinern und ihnen so zum Durchbruch verhelfen. Sie entwickeln im vom Bundesministerium für Bildung und Forschung BMBF geförderten Projekt „DryProTex“ das trockene Transferverfahren zur Elektrodenbeschichtung gemeinsam weiter. In dem Projekt werden Material-, Prozess- und Anlagenentwicklungen vorangetrieben, „die eine Prozessauslegung zur trockenen Elektrodenherstellung im industriellen Maßstab“ ermöglichen sollen. „Das Verfahren hat das Potenzial, auf lange Sicht die herkömmlichen Prozesse zur pastenbasierten Elektrodenherstellung zu verdrängen“, ist Benjamin Schumm überzeugt.
In einer Pilotanlange im finnischen Espoo hat die trockene Elektrodenproduktion bereits begonnen. „Die Nachfrage für unsere Technologie ist groß, auch in Deutschland“, berichtet Schumm. Elektrodenfolien im Labormaßstab können bereits kontinuierlich mit mehreren Metern pro Minute beschichtet werden und so das Potenzial für die Aufskalierung in den Produktionsmaßstab demonstrieren.
Am 18. und 19, November 2019 veranstaltet das Fraunhofer IWS in Dresden zur Informaton der „Batterie der Zukunft“ die „Carbon Electrode Materials“ und die „Lithium-Metal-Anodes: Processing and Integration in Next-Generation Batteries“.
Das könnste sie auch interessieren:
Münchner Startup stellt Solar-Elektroauto vor
Experten enthüllen: Elektroauto-Studie von Hans-Werner Sinn ist Unsinn
Deutsches Startup Chargery bietet mobiles Laden für Elektroautos an
Neue Kondensatoren sollen Reichweite von Elektroautos steigern