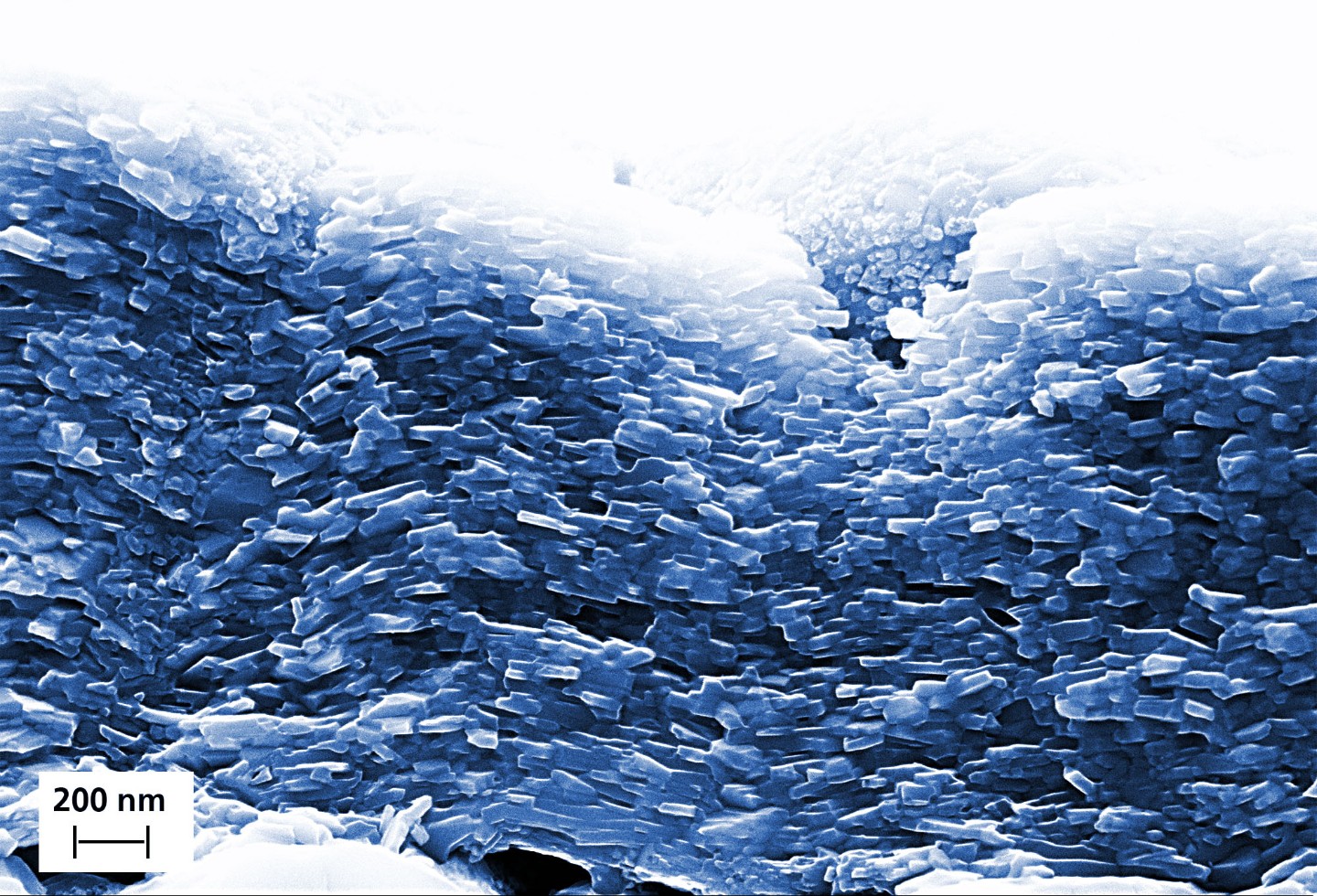
Wasserstoff kann langfristig Benzin und Diesel als Treibstoff für Fahrzeuge ablösen. Er kann auch Erdgas beigemischt und in Gaskraftwerken zur Energieerzeugung genutzt werden. Oder er kann Strom und Heizwärme in Brennstoffzellen erzeugen und so die Umwelt schonen. Denn Wasserstoff ist ein weit umweltfreundlicher Energieträger als fossile Brennstoffe – sofern er aus erneuerbarer Energie wie Wind- oder Solarstrom hergestellt wird – weil bei seiner Verbrennung als Abfallprodukt nur Wasser entsteht. Außerdem lässt sich Wasserstoff sehr gut speichern.
Bis Wasserstoff in großem Umfang eingesetzt werden kann, gibt es allerdings noch ein paar Schwierigkeiten zu überwinden. Eine davon ist, dass atomarer Wasserstoff, insbesondere bei hohen Temperaturen, Metalle verspröden lässt. Das kann wiederum dazu führen, dass Bauteile versagen, denn er sammelt sich ausgerechnet an jenen Stellen im Bauteil an, die besonders beansprucht sind: an Schweißnähten oder in Bereichen, die unter Spannung stehen.
Wasserstoffbarriere vereint Stärken von Keramik und Metall
Der Physiker Lukas Gröner hat in seiner Promotionsarbeit am Fraunhofer-Institut für Werkstoffmechanik IWM, MikroTribologie Centrum µTC, und am Institut für Mikrosystemtechnik der Universität Freiburg im Breisgau nun spezielle Beschichtungen für Bauteile aus Stahl entwickelt und getestet, die das Eindringen von atomarem Wasserstoff nahezu komplett verhindern: sogenannte MAX-Phasen-Materialien, an denen international seit mehr als zehn Jahren geforscht wird.
„MAX-Phasen haben verblüffende Eigenschaften, weil sie Merkmale von Keramiken und Metallen vereinen“, erklärt Lukas Gröner. MAX-Phasen seien, wie Keramiken, unempfindlich gegen Angriffe durch Sauerstoff und sehr hitzebeständig. Zugleich seien sie elektrisch leitend wie Metalle. Im Gegensatz zu reinen Keramiken seien sie jedoch nicht spröde und zerbrechen deshalb auch nicht. Gröner hat nun dünne MAX-Phasen-Beschichtungen hergestellt, die den Stahl sehr gut vor Korrosion und Versprödung durch Wasserstoff schützen.
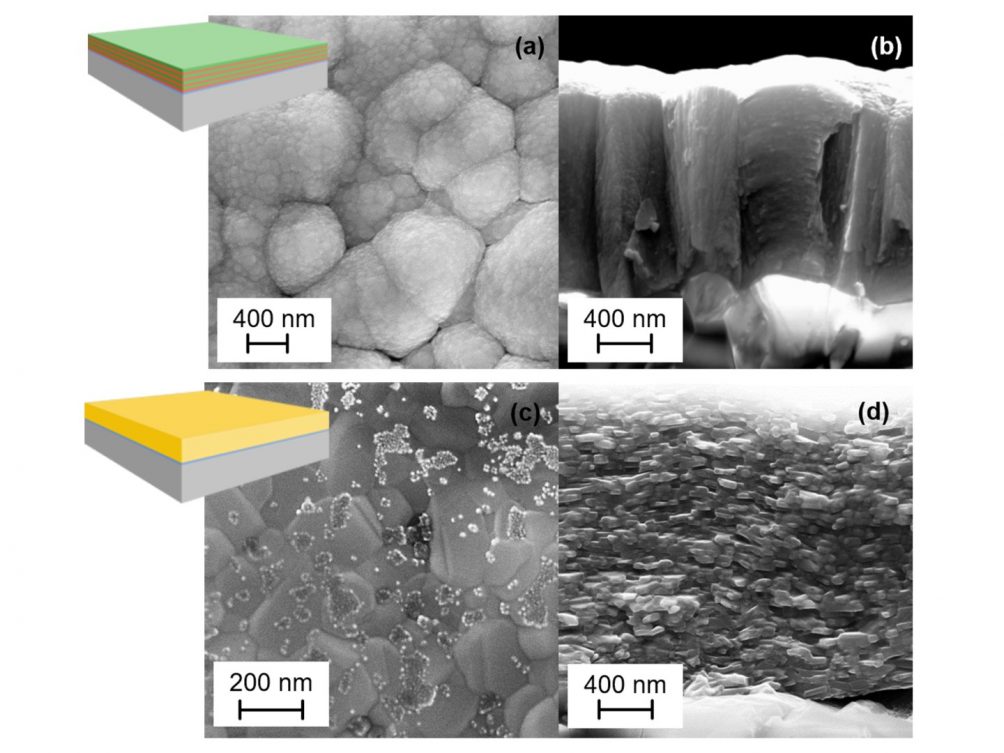
Neuer Prüfstand misst Barrierewirkung
In einem selbstentwickelten Prüfstand für blechförmige Proben testete Gröner wie gut die MAX-Phasen-Schicht das Eindringen von Wasserstoff ins Metall verhindert. Dabei verglich er unbeschichtete Stähle mit MAX-Phasen-beschichteten Stählen. So habe er erstmals das Eindringen des Wasserstoffs genau quantifizieren können und den sogenannten Permeationsreduktionsfaktor (PRF) als Maß für die Barrierewirkung bestimmen, sagt der Forscher.
Es stellte sich heraus, dass Stähle mit einer MAX-Phasen-Schicht, die nicht erhitzt wurden, den Wasserstoff immerhin 50-mal (PRF 50) besser zurückhielten als unbehandelte Stähle. Besonders eindrucksvoll seien aber die Ergebnisse für die beschichteten Stähle gewesen, die erhitzt worden waren und eine α-Al2O3-Schicht gebildet hatten. Die Barrierewirkung dieser sogenannten MAX-Phasen-Schicht ist 3.500-mal größer als die von unbehandeltem Stahl. „Das sind Werte, die den Anforderungen der Industrie absolut genügen“, betont Lukas Gröner.
Praktische Anwendungstest
Aktuell testet Gröner in Zusammenarbeit mit Kooperationspartnern wie dem Forschungszentrum Jülich, wie gut die MAX-Phasen-Schichten in der Anwendung funktionieren. Die Tests werden zum Beispiel an Hochtemperaturbrennstoffzellen (SOFC) durchgeführt, die mit Betriebstemperaturen von rund 600 Grad Celsius arbeiten. „Die MAX-Phasen-Beschichtungen sind für solche Anwendungen ideal, weil sie die metallischen Bauteile vor Hitze schützen und zugleich den elektrischen Strom ableiten können, der im Inneren der Brennstoffzelle entsteht”, so Gröner.
Die Beschichtung sei laut Gröner auch für Gasturbinen geeignet, da dem Erdgas künftig mehr und mehr regenerativ erzeugter Wasserstoff beigemischt werden solle. Das führt aber dazu, dass das Gas mit höherer Temperatur verbrennt, was wiederum das Risiko der Wasserstoffversprödung erhöht. Deshalb könne eine Bauteil-Beschichtung mit α-Al2O3 hier sehr vorteilhaft sein, betont der Wissenschaftler.
Fraglich ist laut Gröner zur Zeit noch, ob das neue Beschichtungsverfahren künftig von der Industrie als Dienstleitung angeboten wird oder in anderer Form den Weg in den Markt findet. Auch müssten die einzelnen PVD-Beschichtungs-Prozessschritte noch optimiert werden.
Lukas Gröner hat die Ergebnisse seiner Arbeit in der Zeitschrift Materials veröffentlicht.
Titelbild: REM-Aufnahme der Bruchkante einer Ti2AlN-Schicht mit plättchenartigem Gefüge. © Fraunhofer IWM