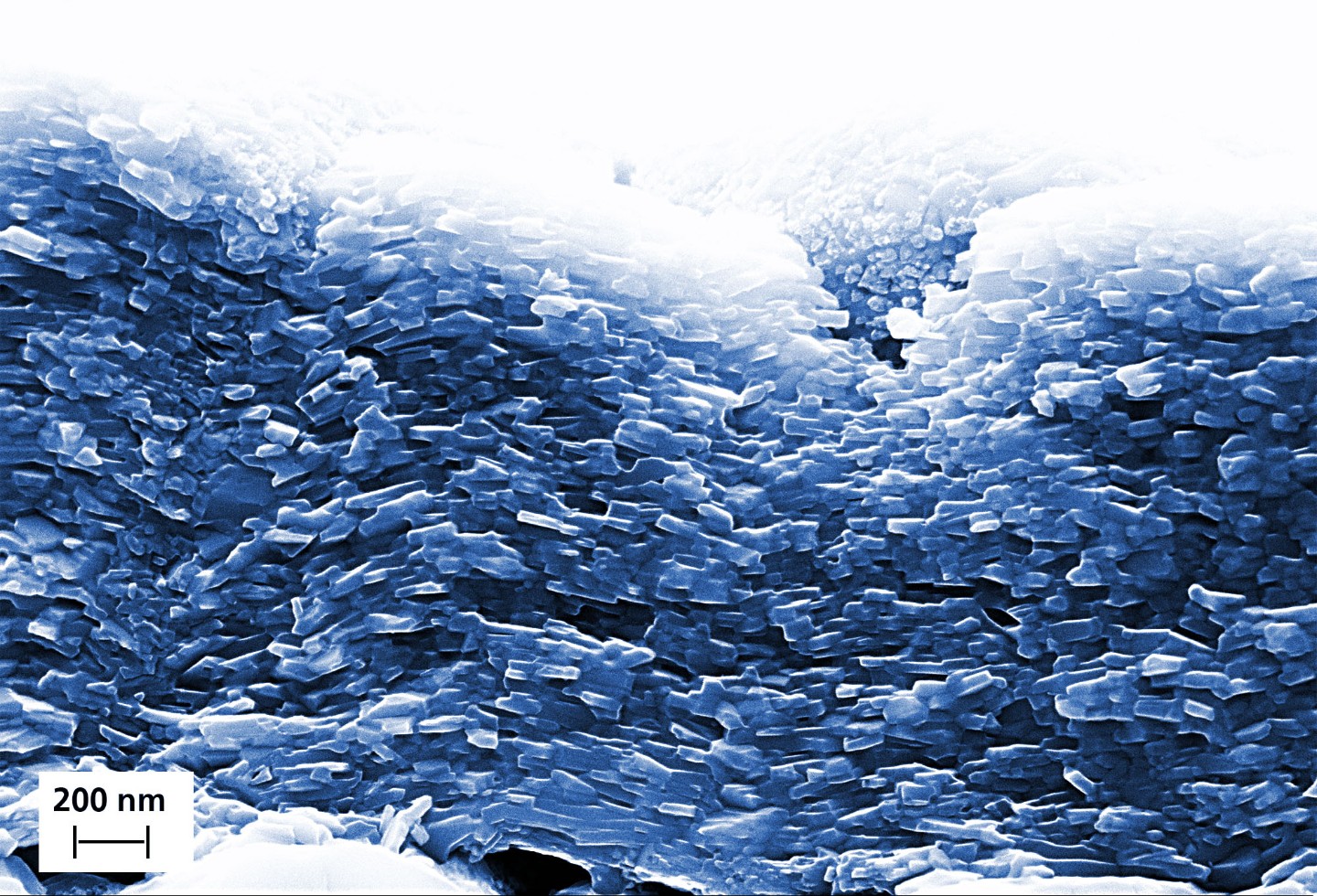
Waterstof staat centraal bij de energietransitie. Ook in Nederland zijn de verwachtingen daarvan groot. Het is milieuvriendelijk en er is een oneindige voorraad van. Probleem is wel dat deze zeer ontvlambare brandstof metalen aantast. Bijvoorbeeld het metaal waar een brandstoftank van is gemaakt. En dat maakt de introductie bij het grote publiek van waterstof als benzine van de toekomst toch moeilijk. Een groep Duitse wetenschappers heeft echter voor dit probleem een oplossing gevonden.
Op de langere termijn kan waterstof benzine en diesel als brandstof voor voertuigen vervangen. Je kunt het ook gebruiken om op een milieuvriendelijke manier elektriciteit en warmte op te wekken in brandstofcellen. Het enige dat vrijkomt bij verbranding is water. Om het echt emissieloos te gebruiken, moet deze brandstof dan wel worden geproduceerd met behulp van hernieuwbare energiebronnen zoals zonne-energie of windenergie.
Totdat waterstof op grote schaal kan worden gebruikt, zijn er echter nog enkele moeilijkheden te overwinnen. Een daarvan is dat waterstofatomen metalen bros maakt, vooral bij hoge temperaturen. Dit kan op zijn beurt leiden tot breuken en scheuren. Vooral in die delen van een metalen onderdeel dat bijzonder belast worden. Bij lasnaden of in gebieden die onder spanning staan.
Waterstofbarrière combineert sterke punten van keramiek en metaal
De fysicus Lukas Gröner heeft nu speciale coatings voor stalen onderdelen ontwikkeld en getest die de penetratie van atoomwaterstof bijna volledig voorkomen. Dat zijn de zogenaamde MAX-fase materialen, die al meer dan tien jaar het onderwerp zijn van internationaal onderzoek.
“MAX-fasen hebben verbazingwekkende eigenschappen omdat ze kenmerken van keramiek en metalen combineren”, legt Lukas Gröner uit. MAX-fasen zijn, net als keramiek, ongevoelig voor aantasting door zuurstof en zeer hittebestendig. Tegelijkertijd zijn ze elektrisch geleidend als metalen. In tegenstelling tot zuiver keramiek zijn ze echter niet broos en breken ze dus niet. Gröner heeft nu dunne MAX-fase coatings geproduceerd die het staal zeer goed beschermen tegen corrosie en het bros worden door waterstof.
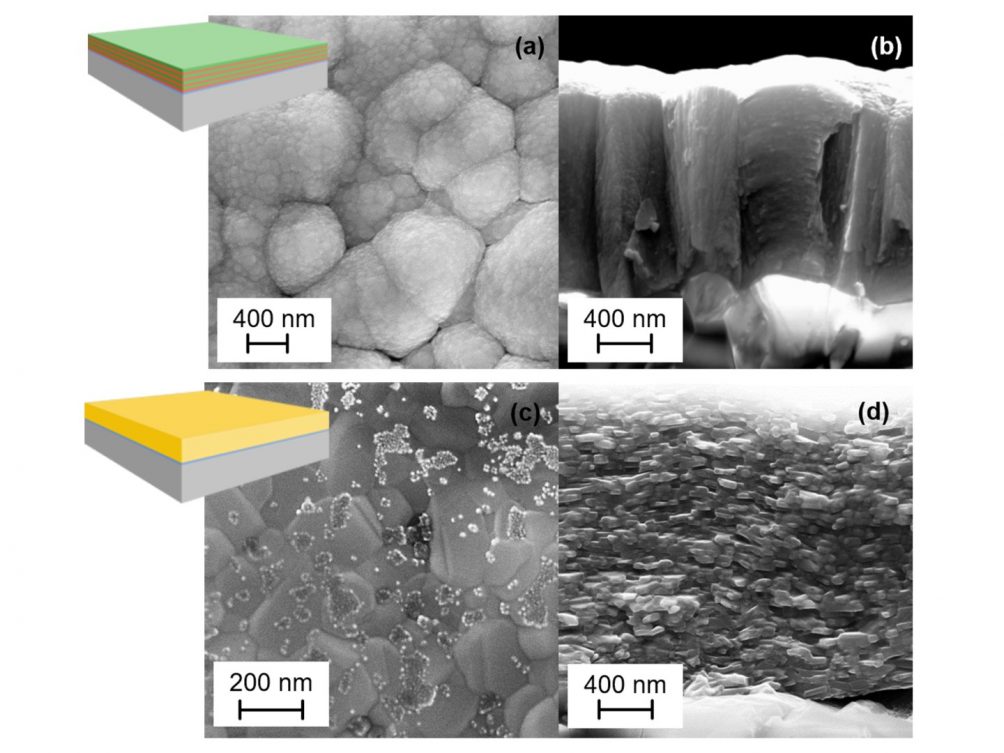
Nieuwe proefopstelling meet de werking van de barrière
In een zelf ontwikkelde proefopstelling testte Gröner hoe goed de MAX-faselaag voorkomt dat waterstof in het metaal dringt. Hij vergeleek onbekleed staal met MAX-fase gecoat staal. Voor het eerst was hij in staat om de penetratie van waterstof nauwkeurig te kwantificeren en de zogenaamde permeatie reductiefactor (PRF) als maat voor het barrière-effect te bepalen, aldus de onderzoeker.
Het bleek dat staalsoorten met een MAX-fase laag die niet verhit werden, 50 keer beter waterstof vasthouden (PRF 50) dan onbehandeld staal. De resultaten waren echter vooral indrukwekkend voor de gecoate staalsoorten die waren verhit en een α-Al2O3-laag hadden gevormd. Het barrière-effect van deze zogenaamde MAX-fase laag is 3.500 keer groter dan dat van onbehandeld staal. “Dit zijn waarden die absoluut voldoen aan de eisen van de industrie”, benadrukt Lukas Gröner.
Praktische toepasbaarheidstest
Gröner test momenteel hoe goed de MAX-faselagen in de toepassing werken in samenwerking met partners als het Jülich-onderzoekscentrum. De tests worden bijvoorbeeld uitgevoerd op brandstofcellen met een hoge temperatuur (SOFC) die werken bij bedrijfstemperaturen van ongeveer 600 graden Celsius. “De MAX-fase coatings zijn ideaal voor dergelijke toepassingen, omdat ze de metalen componenten beschermen tegen hitte en tegelijkertijd de elektrische stroom die in de brandstofcel wordt opgewekt, kunnen afvoeren”, aldus Gröner.
Volgens Gröner is de coating ook geschikt voor gasturbines, omdat in de toekomst steeds meer regeneratief geproduceerde waterstof aan aardgas zal worden toegevoegd. Dit zal echter leiden tot het verbranden van het gas bij een hogere temperatuur, waardoor het risico op waterstofbrosheid toeneemt. Daarom zou een component coating met α-Al2O3 hier zeer veel voordelen kunnen hebben, benadrukt de wetenschapper.
Volgens Gröner is het op dit moment nog de vraag of het nieuwe coatingproces in de toekomst door de industrie als service zal worden aangeboden of dat het in een andere vorm op de markt zal worden gebracht. De afzonderlijke processtappen van de PVD-coating moeten ook worden geoptimaliseerd.
Lukas Gröner heeft de resultaten van zijn werk gepubliceerd in het tijdschrift Materials.
Lees via deze link ook andere IO-artikelen over waterstof als energiedrager van de toekomst.
Foto: SEM-opname van de breukrand van een Ti2AlN-laag met plaatjesachtige structuur. © Fraunhofer IWM