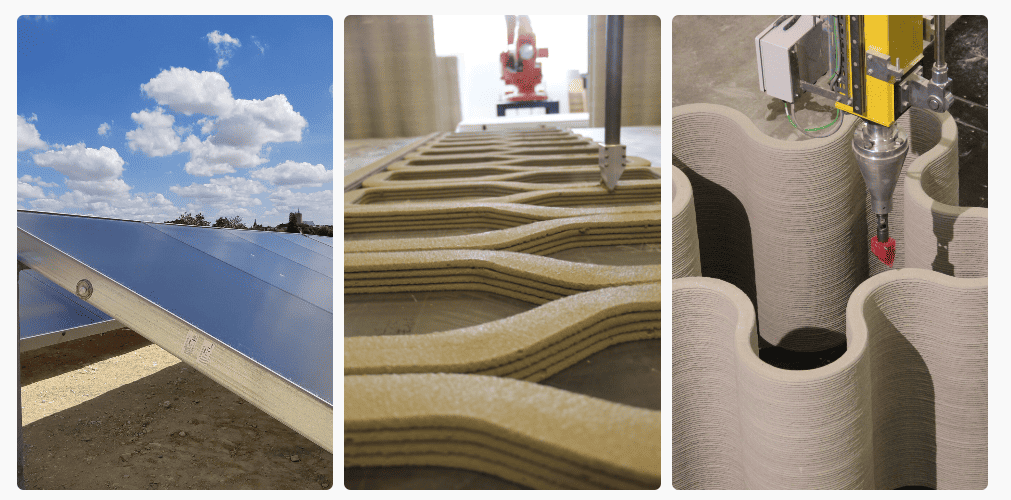
It is one of the biggest challenges in the Netherlands. On the one hand: the housing shortage, which bureau ABF Research announced last week, has risen sharply again (an increase of 75,000 houses in 2022 to a deficit of 390,000 in total). On the other hand: stricter regulations on emissions are causing one construction project after another to halt.
- Zavhy aims to address the enormous housing shortage and strict emission regulations in the Netherlands with 3D concrete printing (3DCP).
- The company has developed two 3DCP systems, RED and FRED, which incorporate structural reinforcement, coarse aggregates, and steel cables, resulting in higher tensile strength and reduced costs for printed concrete structures.
- Zavhy’s 3D concrete printing technology reduces the use of cement by 75% and the CO2 footprint by about 75%, making it a more sustainable option.
A spin-off from Eindhoven University of Technology (TU/e) is working hard to find a solution. And the solution comes in the form of 3DCP. “With this technology, we can build faster and improve the quality of construction. Moreover, the process becomes cheaper and more sustainable because we can use the material more efficiently,” CEO and founder Zeeshan Ahmed of the tech start-up explained to IO last year.
A lot has happened in the past year. The two 3DCP systems Zavhy has developed achieved positive test results, and the start-up closed deals with new partners and introduced an alternative binder for concrete. Reason enough to catch up with Zeeshan and R&D engineer Taco Westerouen van Meeteren.
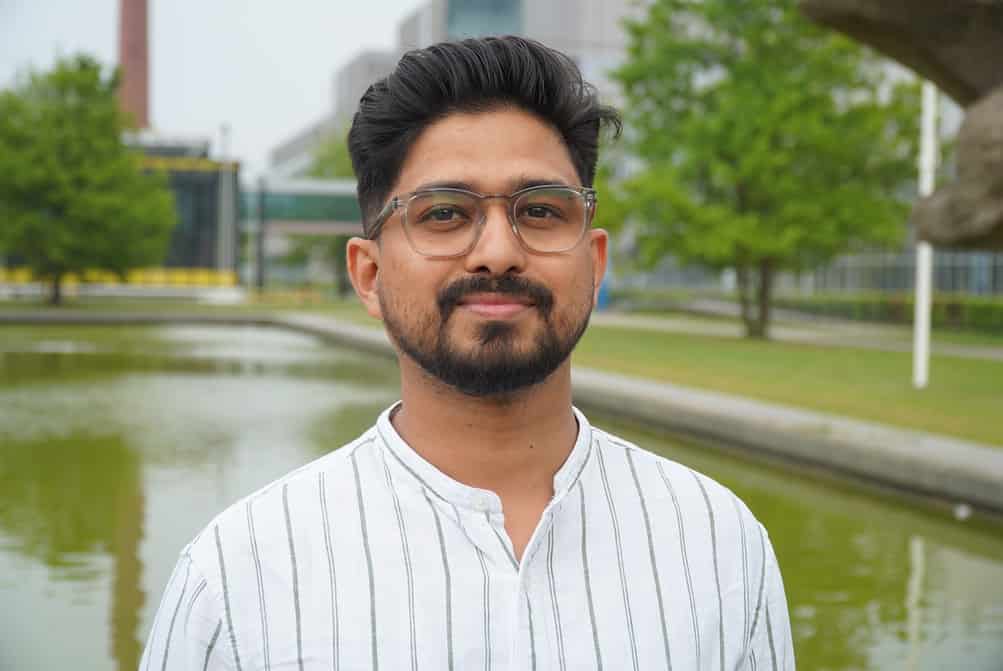
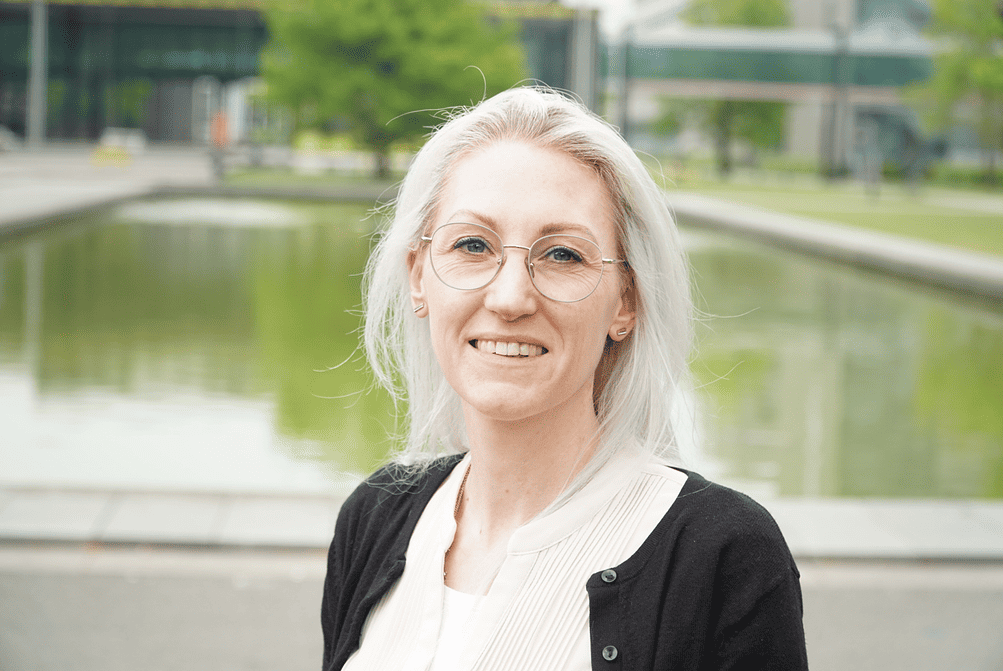
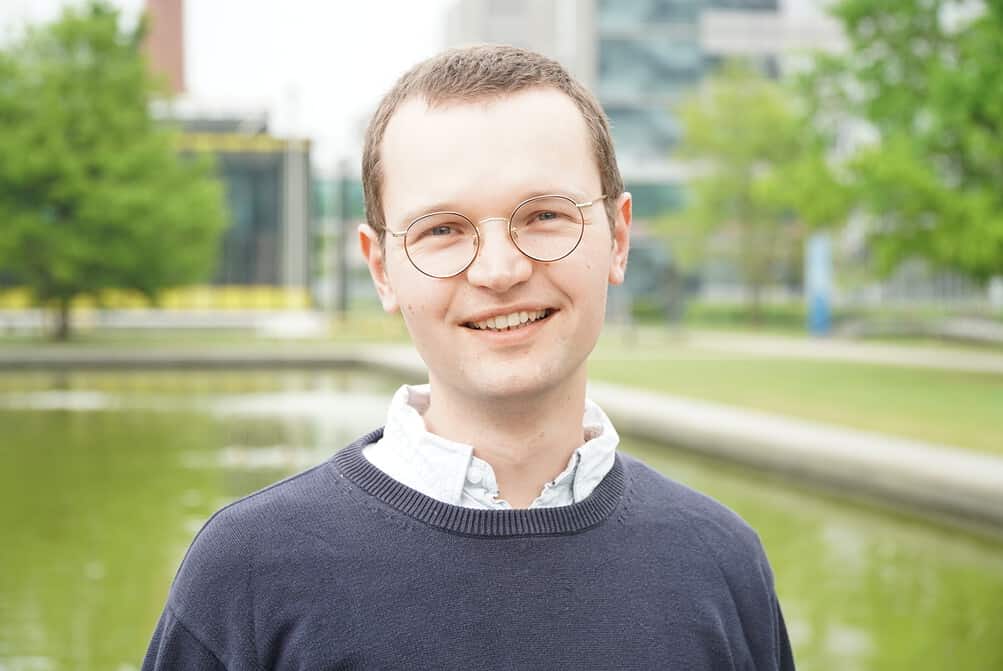
RED and FRED
The idea for Zavhy came about when Zeeshan, during his PhD at Eindhoven University of Technology (TU/e), investigated how to overcome the two major limitations of 3DCP technology – the lack of both structural reinforcement (which provides tensile strength) and coarse aggregate (which improve the properties of concrete).
His research resulted in two revolutionary 3DCP systems: RED and FRED – (Fibre) Reinforcement Entrainment Device. Different from last year, it was unclear whether (F)RED could add sufficient tensile strength to printed concrete structures and whether the application of the technology would bring enough cost benefit; those two obstacles have now been overcome.
“We have proven that we can implement structural steel fibres, coarse aggregates, and reinforcement in the form of steel cables in 3D-printed concrete. We have increased the tensile strength of the printed structure from eight to nine MPa to eighteen to twenty MPa*. Moreover, tests show that the cost of our printed concrete can be reduced by twenty to thirty per cent by adding coarse aggregates*,” says Zeeshan. The RED system has been used to reinforce the 3DCP bridge in Gemert (the world’s first reinforced 3DCP bridge) and the bicycle bridge in Nijmegen, among others.
A major advantage of the 3D concrete printing that Zavhy is developing is that no external formwork is needed, but the reinforcement is incorporated internally into the concrete. “Where normally you need very complicated formwork to make sophisticated forms, now you can add material where needed. This ensures that we need much less material,” Van Meeteren explains.
Substantially reduced CO2 emissions
The start-up also achieved promising results in the area of sustainability. The company managed to reduce the use of cement by 75 per cent compared to commercial 3DCP mixtures. Using alternative binders in the printing concrete, Zavhy reduced the CO2 footprint from 400 to about 100 kilograms of CO2 per cubic meter. Zeeshan: ” Moreover, the binder we use is derived from recycled waste from the metal industry, which additionally contributes to reducing the environmental impact. Large-scale application of our technology can make a crucial contribution to making construction more sustainable.”
A complete 3DCP solution for the construction industry
The young company along with their consortium partners, are working towards offering a complete solution for the construction industry to instigate the growth of the 3DCP market. Zavhy, with its partners, is focused on developing new 3DCP hardware and software technology, contributes to realizing 3DCP construction projects, and finally sets up a production facility where structures and designs can be printed. Ultimately, Zeeshan’s belief in democratizing the technology and sharing it with the industry wants to franchise its technology to support the Dutch government’s goal of building one million houses by 2030. By 2025, the start-up aims to have at least ten other franchises working with Zavhy’s 3DCP technology to address the setbacks of the Dutch construction industry.
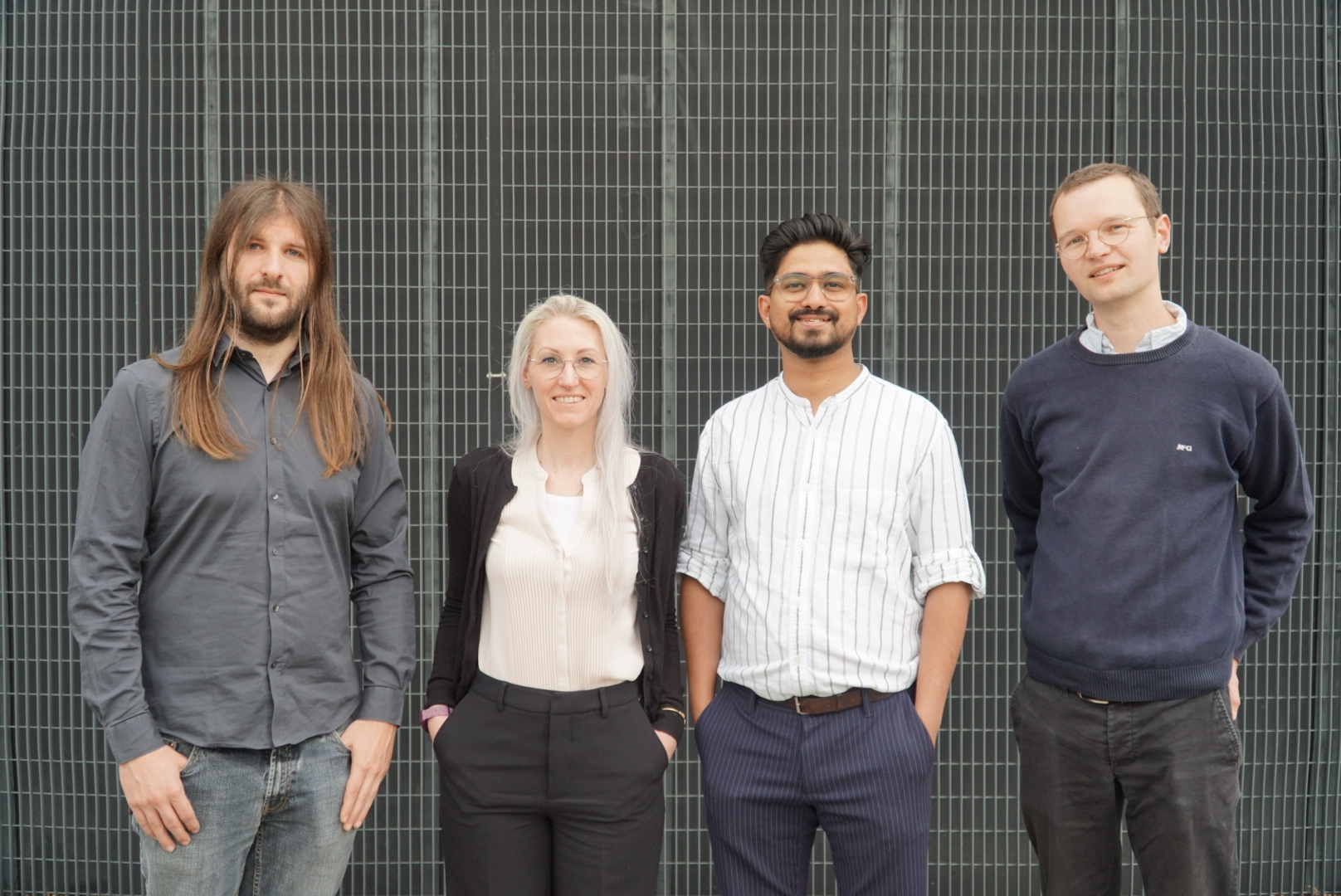
“Due to our promising research results, besides Van Beek and TBRM ES, eight new companies have joined our consortium – ranging from multinational companies like Bekaert and Yaskawa to local Dutch companies – Dekker Group, Remmits GWW, Remix Droge Mortel BV, and IMd Raadgevende Ingenieurs – and innovative TU/e start-ups like AGMAH and Qugate. We see this as an important milestone in attracting the industry to collaborate in offering a complete 3DCP solution for the construction industry. We have one main goal: developing a shared vision of offering sustainable and affordable housing and infrastructure in the Netherlands”, Zeeshan says.
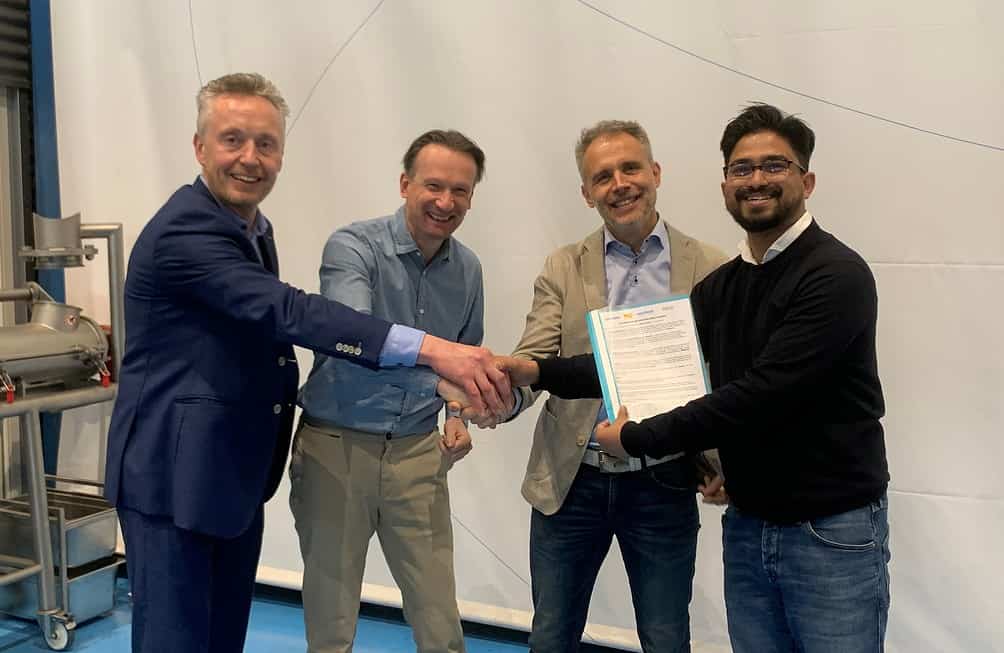
Lastly, the financial support received by Zavhy and the consortium partners from the Dutch Government through the REACT EU, MIT R&D and TTT (Thematische Technology transfer) subsidies was vital in creating the consortium and the industrialization of the 3DCP technology.
The entrepreneur stresses the importance of having companies with backgrounds from the different domains within the 3DCP technology – design and construction, robotics, and materials engineering collaborate and join the consortium. “Only if the technology developed within one domain can work with the technology from the other domains can we apply the 3DCP technology. We are currently working toward developing a new bridge project, which will be an upgrade to the previous bridges in Nijmegen and Gemert on many technological fronts related to improving the strength, sustainability, cost, and environmental impact. But, most importantly, it offers a much-needed solution to improve automation and digitization in the construction of such infrastructure projects.”
* MPa: megapascal. Pascal is the SI unit for pressure.
* Concrete consists of cement, sand, aggregates and water.