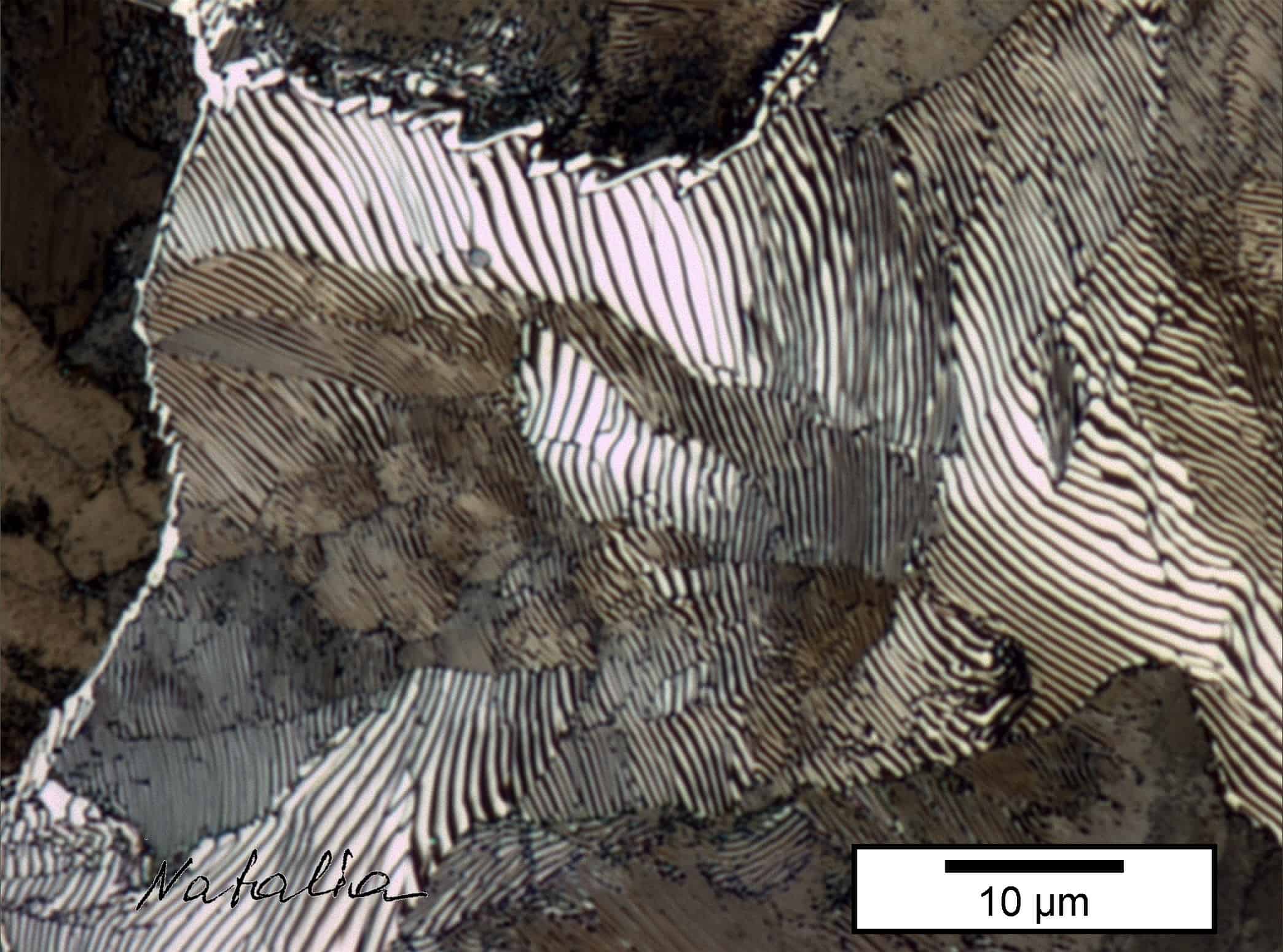
Our society is built on steel; we make bicycles, bridges, buildings, pipelines, cars, and much more. In 2021, 1.9 billion tons of steel were produced worldwide; an all-time high in global steel production and, at the same time, a negative all-time high because every ton of new steel produced is associated with 1.9 tons of CO2 emissions. Steel production is one of the most polluting industries, with a seven percent share of global CO2 emissions.
- Global steel production reaches an all-time high of 1.9 billion tons, but each ton produced is associated with 1.9 tons of CO2 emissions, making it one of the most polluting industries.
- The influence of microstructures are crucial for a greener steel production.
- The development of new, sustainable production technologies and the re-use of steel scrap are crucial for greener steel production, and the industry is increasingly focused on sustainability.
Yet we need it, because there is no alternative to steel, because it combines best of three worlds: it’s flexible, cheap and strong. So, there is only one thing to do: make the life cycle of steel greener. In this series, we look at how scientists from TU Delft and industry make the life cycle of steel – from production to processing, application, and recycling – more sustainable. Today: the influence of microstructures.
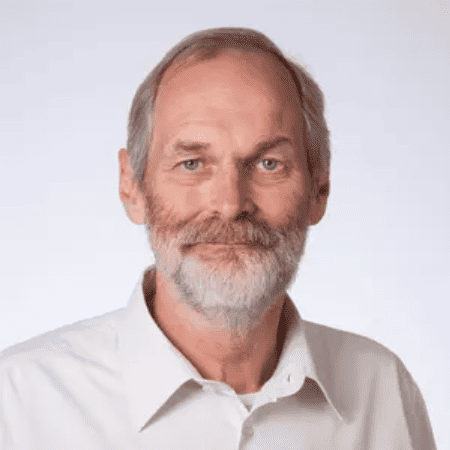
Atomic structures forming crystals
Steel is an alloy (an artificial mixture of a metal with at least one other added element) of mainly iron and carbon and consists of billions and billions of tiny crystals, firmly and densely packed. For steel, the production process – especially deformation, heating and cooling – is at least as crucial as the composition of the alloy. “Steel consists of 96 percent by weight of iron and up to half a percent of carbon. At room temperature, the crystal structure is fixed, but when you heat it, the way the atoms are arranged at microscopic scales within the iron, the microstructure, changes,” explains Jilt Sietsma. He is an emeritus professor of the MSE Department in Microstructures.
“When you look at steel through a microscope, you see all the crystals formed by atomic structures with different orientations. These microstructural components vary in size, orientation and extent. By altering this structure – with heat treatments, possibly combined with changing the chemical composition – you can change the microstructure of steel and produce steel with specific properties,” explains Maria Santofimia Navarro. A professor of Physical Metallurgy, she researches specific microstructures, combining strong and soft microstructural components of steel. These materials are already widely used in the automotive industry, which requires increasingly lighter yet more robust materials.
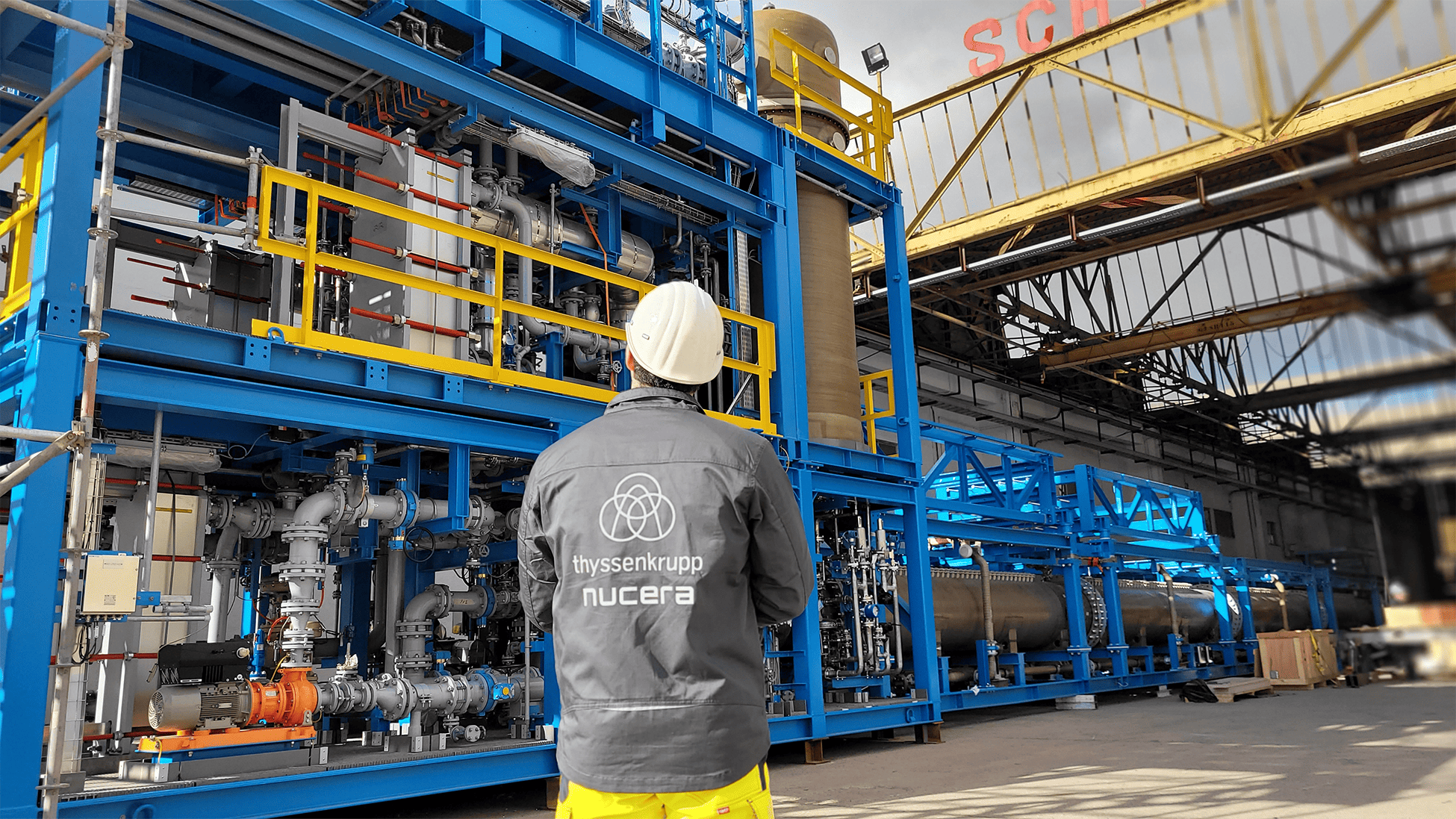
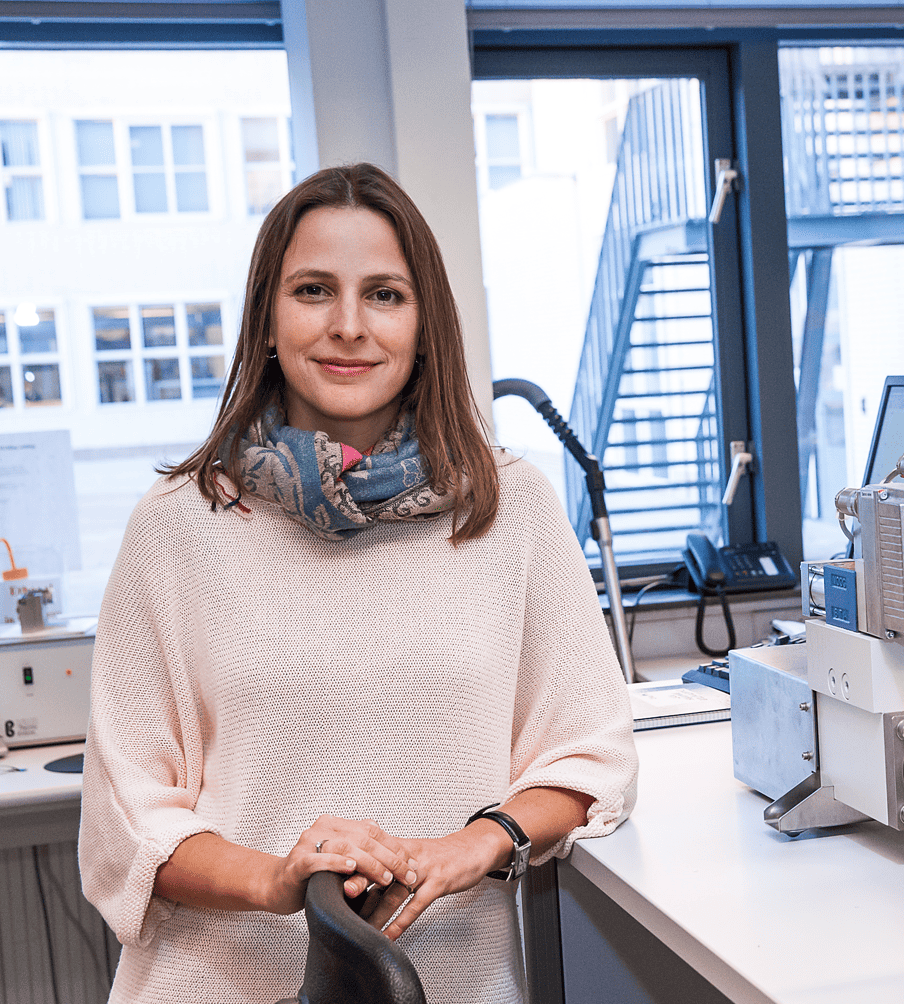
A more sustainable production process
Then, steel is an umbrella term; there are 3,500 different steels for commercial use, each with a unique microstructure. In the laboratory, the possibilities are endless. Among other things, Sietsma and Santofimia’s research group aims to develop fundamental understanding of the processes by which the microstructure forms. Such understanding is the basis to design steel processing to make desired microstructures with a minimum of raw materials, energy use and emissions while maximising the use of scrap.
Santofimia states that the professors work closely with industry, which also partly makes the research so enjoyable. “Here we dissect physical mechanisms, and with that knowledge, the industry can eventually make new steel grades and make them more sustainable.”
The re-use of steel
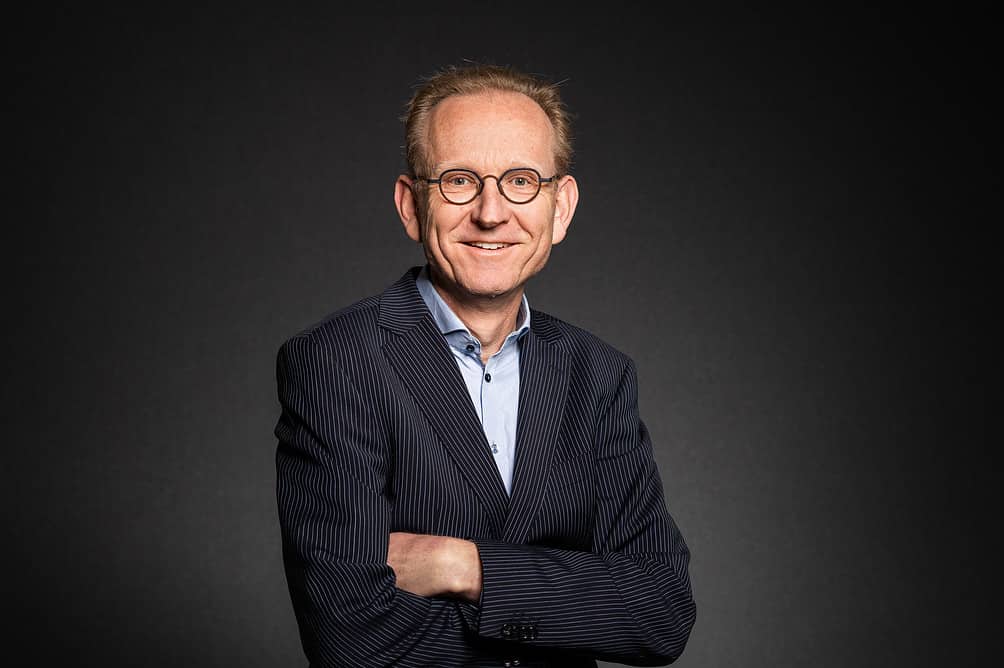
Besides the development of new, sustainable production technologies for “green steel”, reusing steel is also essential. Scrap will become an increasingly important raw material for steel production, Erik Vegter, director of M2i (Materials innovation institute), a network organization specializing in materials research involving industries and universities, also knows. “You can re-use steel very well, but whether you use iron as a raw or used material makes quite a difference. Research into finding good ways to still control the microstructure with changing compositions – and thus ensure a high-quality end product – will become increasingly important in the coming years.”
Santofimia: “We must develop new technologies that tolerate higher element uncertainty. The first step is understanding the precise effect of these uncontrolled elements from scrap on the microstructure formation. Once we know that, we can develop new processing routes in which this understanding is considered so we can aim for these elements to be beneficial instead of detrimental.”
‘Very excited’
Studying microstructures of materials is a topic that has developed relatively recently, compared to 3000 years of steel use. “We have only been at it for a few decades and have already achieved a lot in microstructure control. For instance, we have built up an understanding of the first stage of the formation of crystals, the nucleation stage, in which some tens of atoms “decide” to re-arrange into a new crystal structure. Approximately 75 percent of the steels in use today did not exist twenty years ago. I’m very excited when I think about what we can achieve in the future”, Santofimia says.
“Also, the possibilities that models simulations on fast computers offer us are a huge help,” Sietsma adds to his colleague. “Predictions of microstructure formation based on physics-based models require very extensive calculations.”
In this regard, M2i initiated the DEPMAT project (Data Enhanced Physical Models), which is led by the University Twente and includes Tata Steel, TU Delft and SKF. The aim is to conduct research into modelling microstructure responses to those new manufacturing processes.
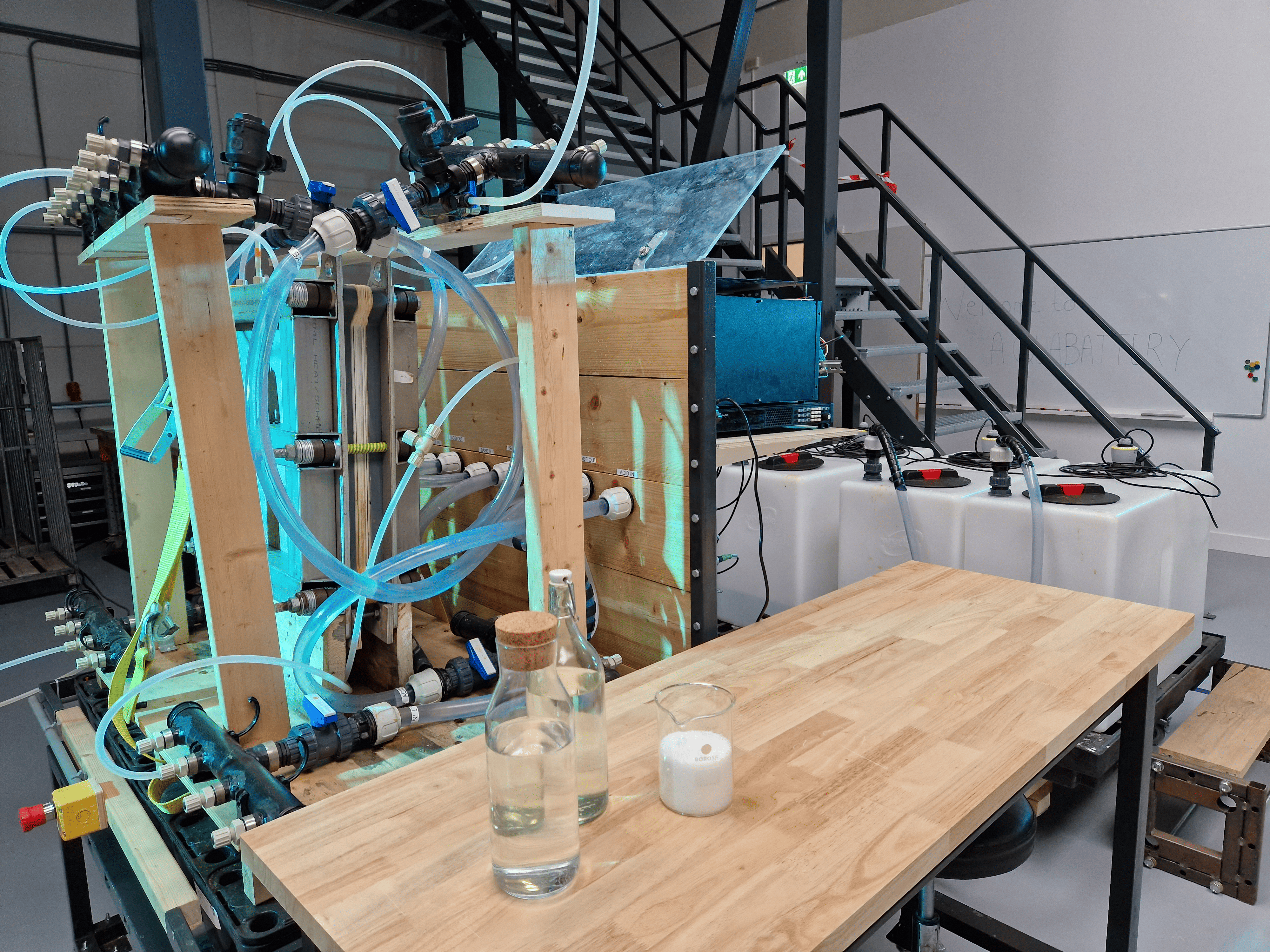
Awareness
Understanding microstructures is a crucial component of greener steel production. A topic that is now a priority in the industry, Sietsma observes. “Previously, questions from industry were mainly related to scarcity, price, and political sensitivity. If a company could no longer import nickel for geopolitical reasons, it would ask us if it could replace nickel with another element. Now questions from industry are mostly about more sustainable production.”
Sietsma should know; the professor has been with the Department of Materials Science and Engineering since 1987. He was recently appointed Knight of the Order of the Dutch Lion in recognition of his contribution to science, industry, and society, emphasizing the societal importance of steel research.
Vegter sees this awareness as the most important step the industry has made in recent years. “Steel companies realize much better than many people know that they must become more sustainable. There is a behind-the-scenes look at how they should go about it on all fronts. An example is Tata Steel’s transition to replace one of its blast furnaces with a DRI (Direct Reduced Iron) process by 2030. This will eliminate the use of polluting coal.”
“Previously, questions from industry were mainly related to scarcity, price, and political sensitivity. If a company could no longer import nickel for geopolitical reasons, it would ask us if it could replace nickel with another element. Now questions from industry are mostly about more sustainable production.”
Jilt Sietsma
During his career, Sietsma saw that sustainability gradually took on an increasing role. “25 years ago, it was mainly about making production as cheap as possible. Back then, my research field was also looked at much more sceptically. Now technology is recognised as the key to a more sustainable world. You can also see that in our student numbers. Where we used to have an average of fifteen Materials Science students per year, there are now about sixty. Almost all of them choose the study to contribute to a world with more sustainable production, use and re-use of materials.”
Cover photo: perlite microstructure. Image: Natalia Luzginova, published in N.V. Luzginova, L. Zhao, & J. Sietsma, The Cementite Spheroidization Process in High-Carbon Steels with Different Chromium Contents, Metallurgical and Materials Transactions A 93 (2008) 513-521.