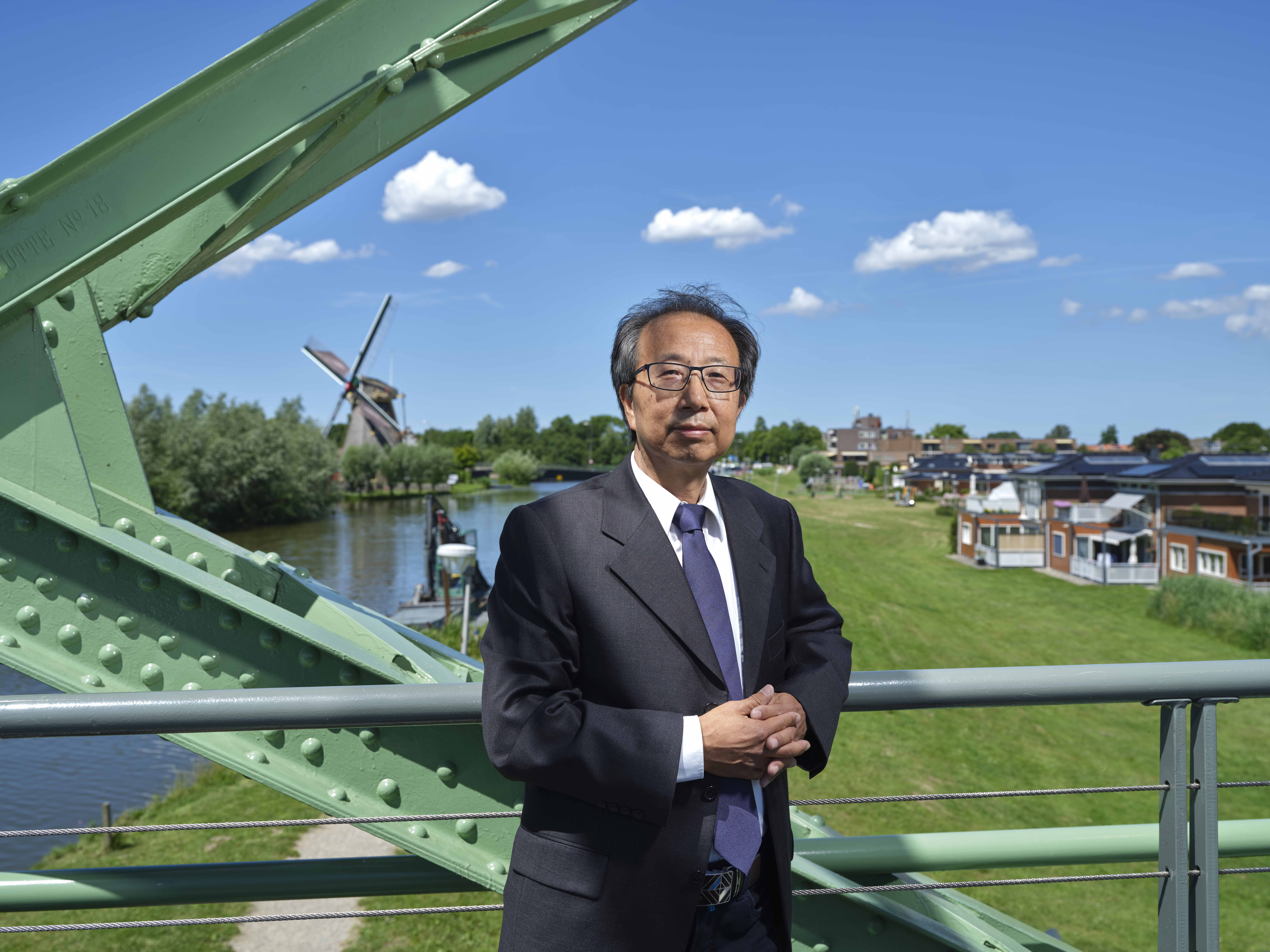
“I call the last 150 years the steel age. It is one of the most important materials ever. At the same time, we live in a time when much more sustainable steel production is more important than ever.” It is precisely these two challenges that come together in Yongxiang Yang’s work. He heads TU Delft’s Metals, Production, Refining, and Recycling group, focusing on metals production and recycling, and recently on making steel production more sustainable with hydrogen.
- Hydrogen’s role in Direct Reduced Iron (DRI) production offers a more sustainable path for the steel industry.
- Hydrogen-based steel production is seen as a viable long-term solution for carbon-free steel production by McKinsey and the International Energy Agency.
- Transitioning to hydrogen-based steel production faces challenges, including energy requirements and the need for infrastructure development, necessitating collaboration between industry, governments, and regulators.
This McKinsey report and the International Energy Agency’s (IEA) Iron and Steel Roadmap see hydrogen-based steel production as a technically feasible and economically viable long-term solution for carbon-free steel production.
Direct reused iron
To understand how this works, let’s go back to the basics of steelmaking. The material is made from iron ore and steel scrap. Steel metallic iron is needed, so iron ore is processed into agglomerates (small balls or sinters), is reduced by using carbon in cokes, and melted in blast furnaces under temperatures of up to 2000 degrees Celsius. The liquid iron is thus produced from the ore, called “hot metal”. The hot metal, together with steel scrap, is then further refined to liquid steel. Blast furnace ironmaking releases much CO2, contributing to approximately 75 percent of total CO2 in steelmaking.
Sustainable steel
Our society is built on steel. We make bicycle bridges, pipelines, and cars from it. In 2021, 1.9 billion tons of steel were produced worldwide – an all-time high in global steel production—or the low point because every ton of new steel produced is associated with 1.9 tons of CO2 emissions. At seven percent of global CO2 emissions, it is one of the industries with the most significant carbon dioxide emissions.
Yet we need it because there is no alternative to steel. So there is only one thing to do: make the life cycle of steel greener. In this series, we look at how scientists from TU Delft and industry are making the life cycle of steel – from production to processing, application, and recycling – more sustainable. Today: the role of corrosion technology in making steel more sustainable.
An alternative ironmaking process is the direct reduction of iron ore. The product is direct reduced iron (DRI): DRI is typically made using natural gas. This process releases thirty percent less CO2 than the blast furnace process but is still far from the EU and the Netherlands’ 2030 and 2050 climate targets. Yang is investigating the use of hydrogen to convert iron oxide into solid iron. The DRI can then be melted in an electric arc furnace (EAF) for raw steel or joined to a Basic Oxygen Furnace (BOF) steelmaking route. By using hydrogen to replace natural gas or carbon in ironmaking, nearly no CO2 is released in this process: oxygen, in this case, does not bind to carbon (so it ends up as CO2) but to hydrogen.
Using hydrogen DRI in steelmaking is one of many options. Steelmaking via direct electrolysis using green electricity is also being studied, but it will take longer to become applicable in industrial operations. CO2 capture and storage or utilization is another option to extend the current carbon-based blast furnace process, but this is not a final solution. Yang expects the DRI made with hydrogen to be used commercially from 2030 onwards.
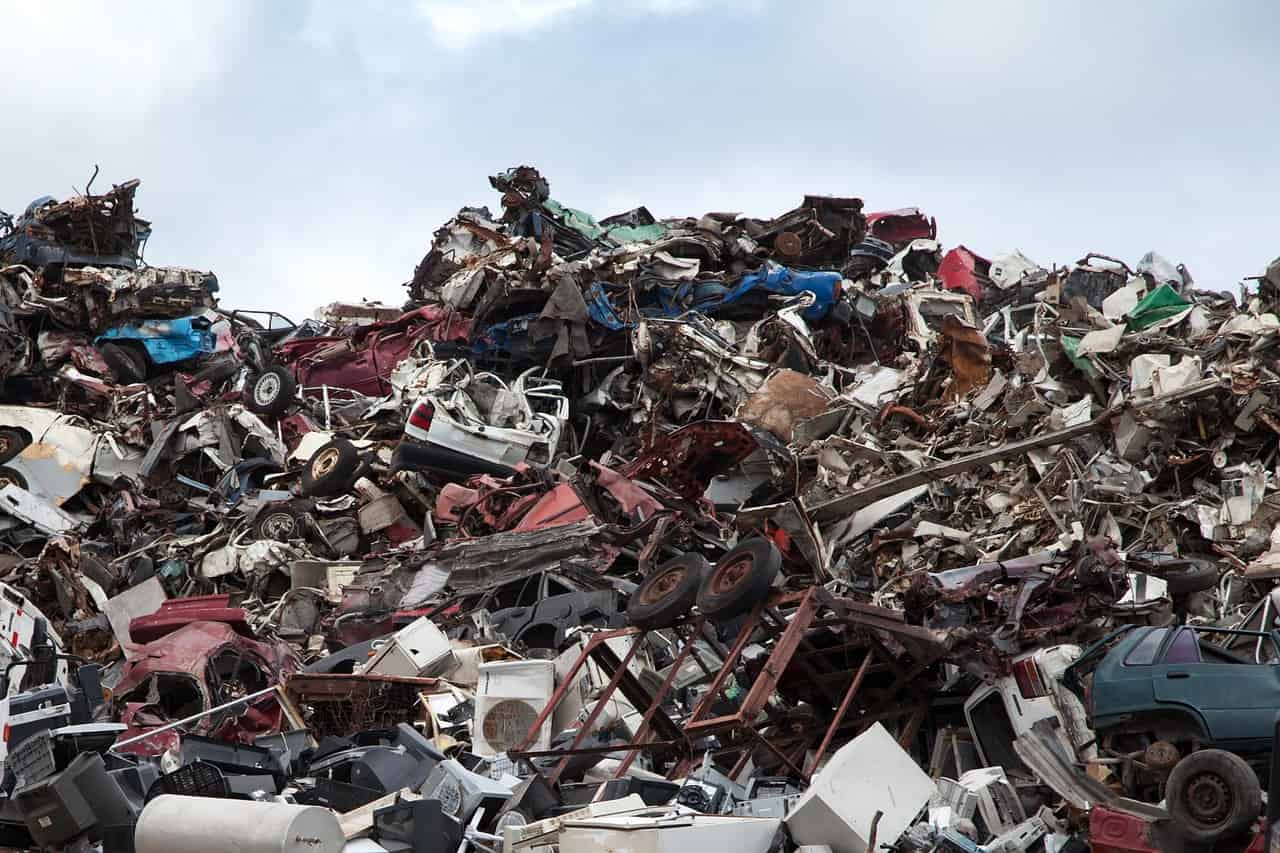
Green hydrogen
Two years ago, Tata Steel, which produces some seven million tonnes of steel yearly, announced it was switching to green hydrogen in ironmaking. The company wants to be carbon-neutral by 2045 and has invested 65 million euros in designing new plants to produce steel using hydrogen; building them will cost many times more. By 2030, the first phase of this green steel plan should be operational; one blast furnace and one cook and gas plant will go out of operation. “Replacing our blast furnaces with a hydrogen-based direct reduction process will be one of the biggest industrial operations in the history of the Netherlands. Those blast furnaces are the heart of our business, and we are taking that away,” says Tim Peeters, manager of the Iron and Steel R&D department at Tata Steel.
Funding for this project will largely come from Tata Steel itself. But the company is also in talks with the government about co-financing through the so-called ‘maatwerk‘ route.
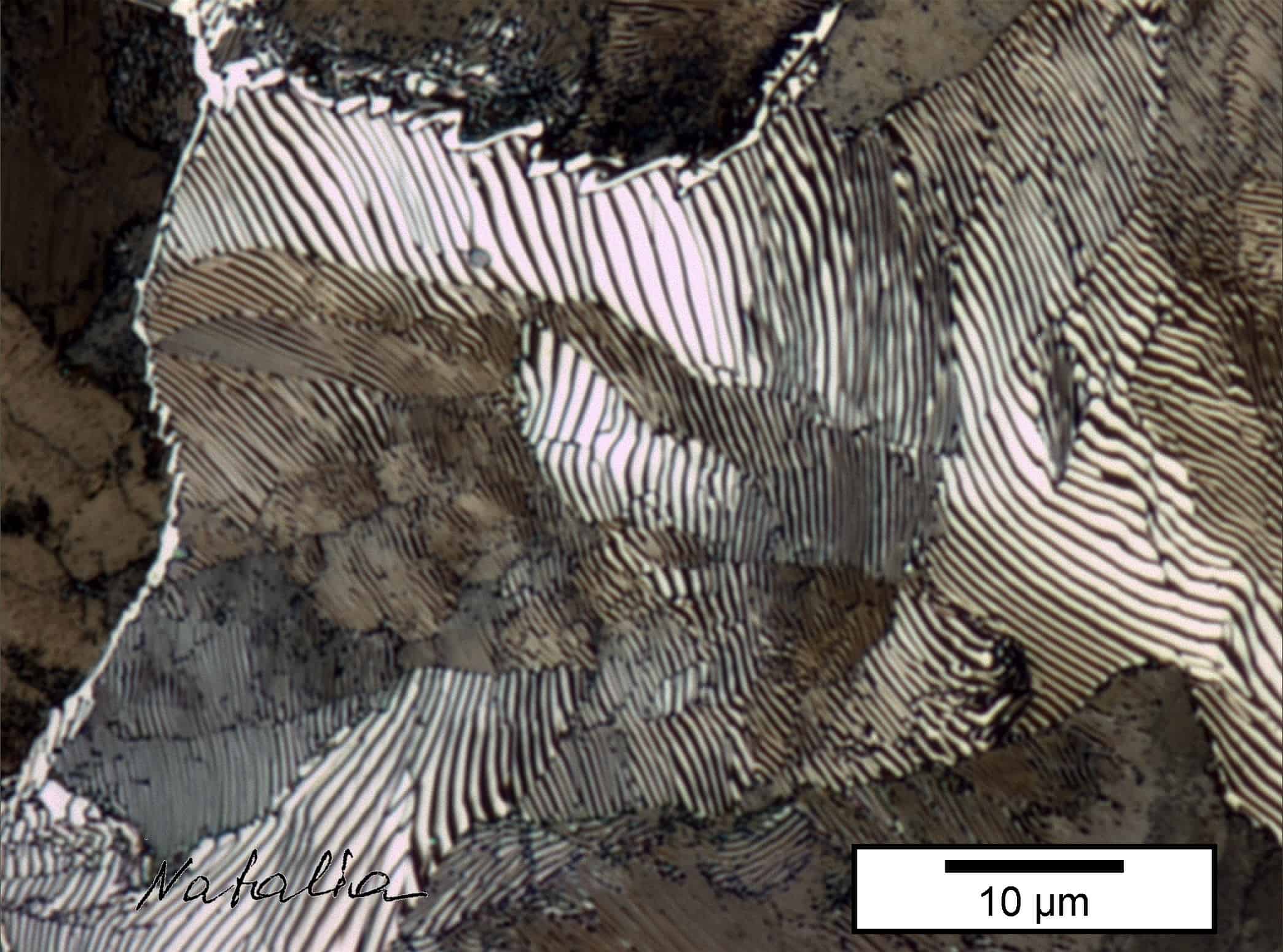
Challenges
In Sweden, a pilot plant (HYBRIT) has been established to develop hydrogen-based DRI production further. DRI will be produced commercially with hydrogen via hydropower plants; in the Netherlands, electricity must come from offshore wind turbines. Meeting the energy needs of this green steelmaking technology is also directly the biggest challenge. “The temperature in the DRI shaft furnaces must constantly be around 1,000 degrees Celsius. Together with the chemical requirement of hydrogen as a reducing agent, the process guzzles huge amounts of energy. Finding a constant energy source that provides adequate power is crucial,” according to Yang. Far too little green hydrogen is produced for the industry in the Netherlands. To illustrate, having enough hydrogen using water electrolysis for the steelmaking sector alone requires 21 billion kWh yearly. In 2021, wind turbines in the Netherlands produced only 15.4 billion kWh, merely 70 percent of the electricity needed to power H2 production in steelmaking.
“And on top of that comes all the infrastructure,” Peeters adds. “We must build new plants by 2030 and have enough green hydrogen available. We cannot but trust that the Dutch economy will be able to implement the hydrogen network in parallel with our transition.”
One thing is clear: as promising as green hydrogen is for more sustainable steel production, it is practically and logistically a huge operation. The shift to greener steel production is not a task that the steel industry can do alone but requires a concerted effort by regulators, governments, and industry stakeholders.