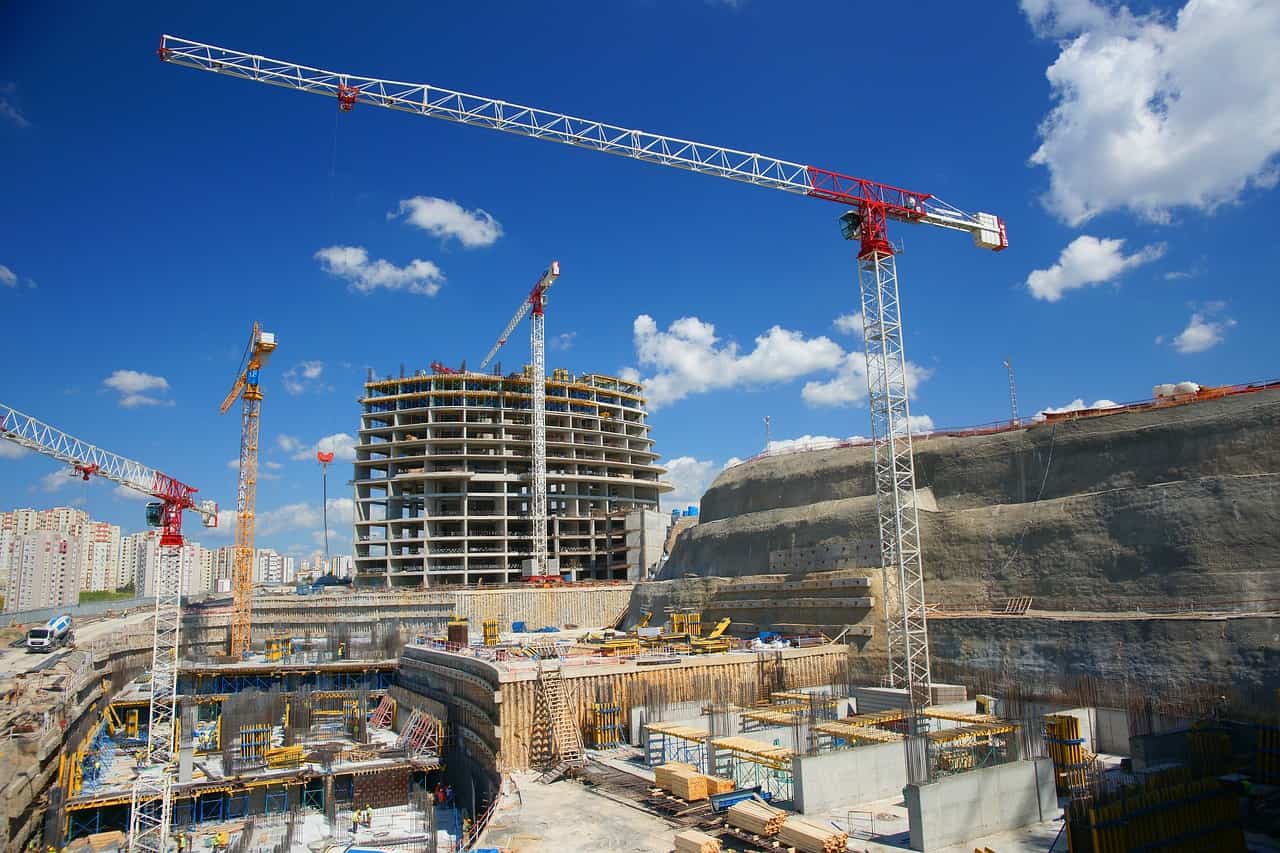
Most buildings around us consist primarily of concrete. The grey mixture has been an essential material in construction for decades. It is easy to work with, and it is strong and long-lasting. Moreover, it is relatively cheap. But there is also a downside. A lot of sand is needed to make concrete, which is becoming increasingly scarce. In addition, concrete is also polluting because it cannot yet be fully recycled. But this is now about to change. “We want to close the loop. Using three different technologies, we can turn concrete waste into new concrete again,” says Francesco Di Maio, Research director of the Recycling Lab at TU Delft.
Research into the different technologies needed to recycle concrete has been conducted at TU Delft for decades. For now, Di Maio does not see any promising concrete substitutes, so he believes recycling is the best option. Concrete recycling has great potential and can lower the carbon footprint of the concrete industry.
- Researchers at TU Delft developed three technologies to efficiently recycle concrete waste.
- The recycled concrete is of comparable quality to concrete from new raw materials.
- To further scale up the technology, a start-up has been established.
- The start-up aims to convert all types of concrete waste into high-quality materials in five years; it is currently seeking investors for further scale-up.
Chunk, sorting, and cleaning
Di Maio and colleagues developed technology (C2CA Technology) that can separate concrete into loose ingredients, such as stone and sand. “Imagine an old building being demolished. The steel – the reinforcement – is removed from the chunks of concrete with a magnet. The concrete chunks are then chopped into small pieces,” Di Maio explains.
Then, C2CA Technology comes into play. “Concrete is made of stone, sand, cement, and water. Our machine – the Advanced Dry Recovery (ADR) – transforms the concrete chunks into coarse aggregates, sands, and a fine powder,” he says. The sand is cleaned in another machine using Heating Air and classification Systems (HAS) technology. HAS was also developed by Di Maio’s group. This machine removes minerals and cement residues from the sand. Finally, a third laser-based technology was developed to measure the quality of materials.
Measuring quality
“The recycled concrete we can make with these technologies is comparable in quality to concrete made from virgin raw materials. It is crucial to demonstrate that to users as well. That can convince people to buy these materials instead of new ones. It creates transparency and trust,” Di Maio points out.
The road to industry
In 2016, a start-up – called C2CA – stemmed from TU Delft scientific research to bring the new technology to the market. Dr. Thomas Petithuguenin, experienced in making the concrete industry more sustainable, was recruited to lead the start-up. C2CA is now working on several large pilots. “We mainly operate on the demolition side of the concrete industry. When a building is demolished, it often goes to a recycling company. That is where our technology comes in,” says the CEO.
The machines to recycle concrete, both for large and smaller parts, are already running at several recycling plants. “We can make a difference, especially in recycling the fine parts like sand and cement paste. That was not easily possible until recently.” The products coming out of the pilot plants are sold by the start-up to companies making a variety of products from concrete. “That makes our company extra strong,” Petithuguenin states.
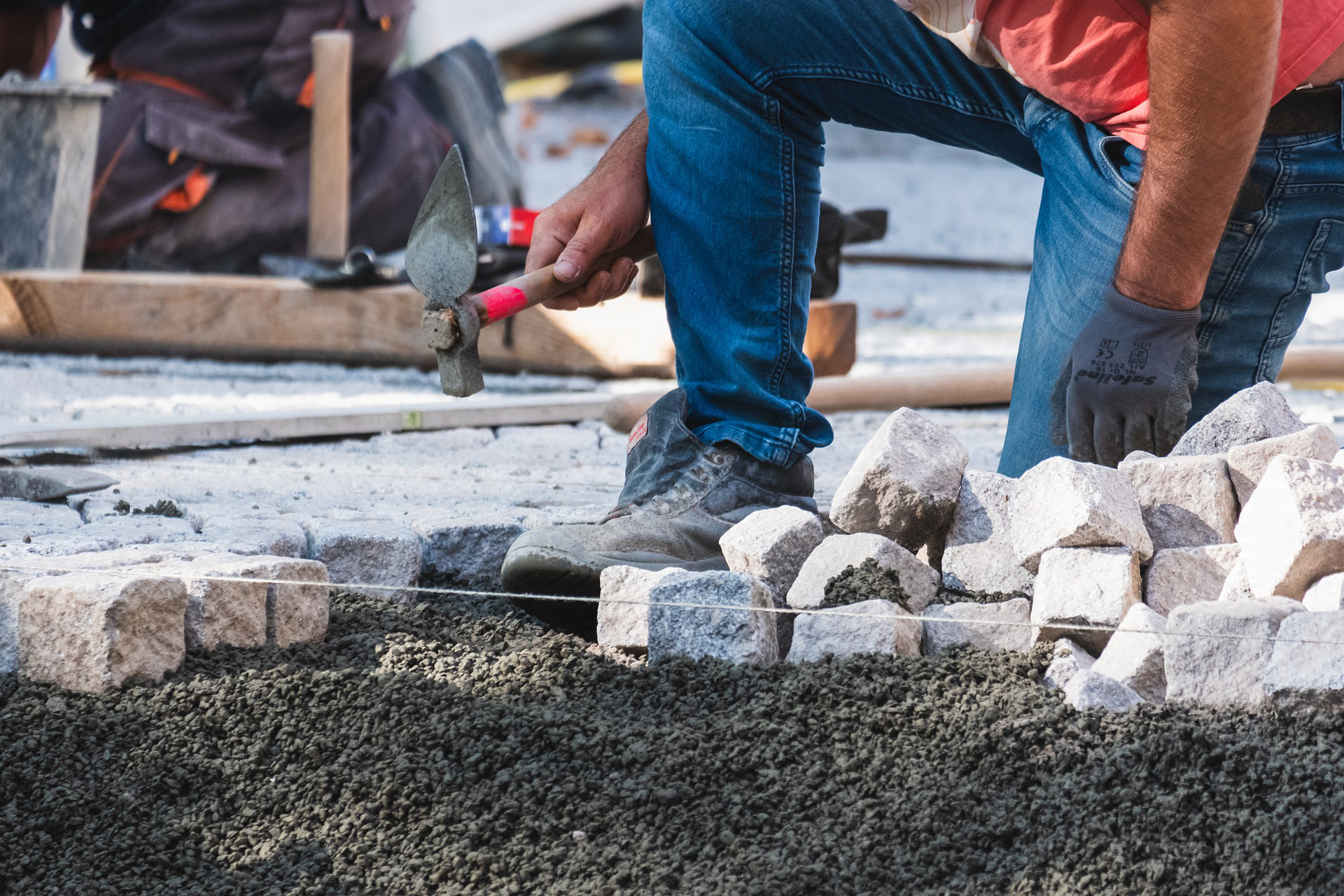
Automation
C2CA’s goal: in five years, to be able to convert all types of concrete waste – regardless of quality – into high-quality materials for new concrete. “In the Netherlands, waste streams are often pretty well sorted. In other parts of the world, this is not always the case. This, in turn, requires different capabilities of our system. Whatever the quality of the input, we want the output to always be of good quality. That is one of the biggest challenges ahead.”
Petithuguenin is currently in an investment round to take the final steps towards scaling up and fully commercializing the product. “We are looking for investors who fit our company and our vision. The technology is new, and developing and scaling up large devices like C2CA takes a lot of time and money. So, it takes some patience and perseverance. On the other hand, there are also huge opportunities. The technology is promising and can make a huge impact. An investor should be able to overlook that.”
Eyes on the goal
Entrepreneurship suits Petithuguenin well. Earlier in his career, he mainly worked for large companies, so it is all new. “At a corporate, everything is well organized, you have a whole support system behind you. At a start-up, none of that is there. Three weeks after becoming the company’s CEO, I was coding the website. I hadn’t thought of that beforehand,” he says, smiling. Yet he says he did not find it unpleasant. He always had a clear goal in mind. “A strong vision for the future is indispensable. I am motivated to make the industry sustainable. If a result is disappointing, you have to be flexible and be able to turn your business around to a different strategy to be still able to achieve your goal in the end.”
TU.Built Environment builds a sustainable future
Together with 4TU.Built Environment, we at Innovation Origins are working on articles about innovation in construction. We are exploring and answering the most interesting and pressing questions around important construction topics. The cooperation between the four technical universities in the Netherlands and all partners plays an important role in this.
Read all the other stories here.
Sharing knowledge
Di Maio and Petithuguenin are working intensively together to develop the technology further. “For instance, we are looking at electrifying the HAS,” Petithuguenin says. Besides the collaboration with TU Delft, the start-up is also looking at collaborations with TU Eindhoven. “It is very nice to share knowledge with different universities. In Delft, research is more focused on recycling and sorting technologies, while in Eindhoven, there is more focus on chemistry and the quality of materials. All these aspects are important for us to get the best product.”
Di Maio’s research group is also working on a new project in which Artificial Intelligence (AI) plays an important role. “We want to use AI to analyze the old concrete chunks and sort them by size. This is still largely done manually at the moment.” Ultimately, the aim is to automate the entire recycling process. “Sensors can be used to analyze which materials come in, a computer supervises the process, and finally, another computer analyses whether the result meets the quality requirements to use it again,” hopes the concrete scientist.
Good for humans and animals
Petithuguenin’s ultimate dream for the future is a network of thousands of plants around the world. In this way, he wants to supply the world with complete concrete so that raw materials from the soil are no longer needed. “Raw materials like sand are not only scarce but taking it from the seabed harms marine life. I think that is an important argument for finding alternatives to this.”