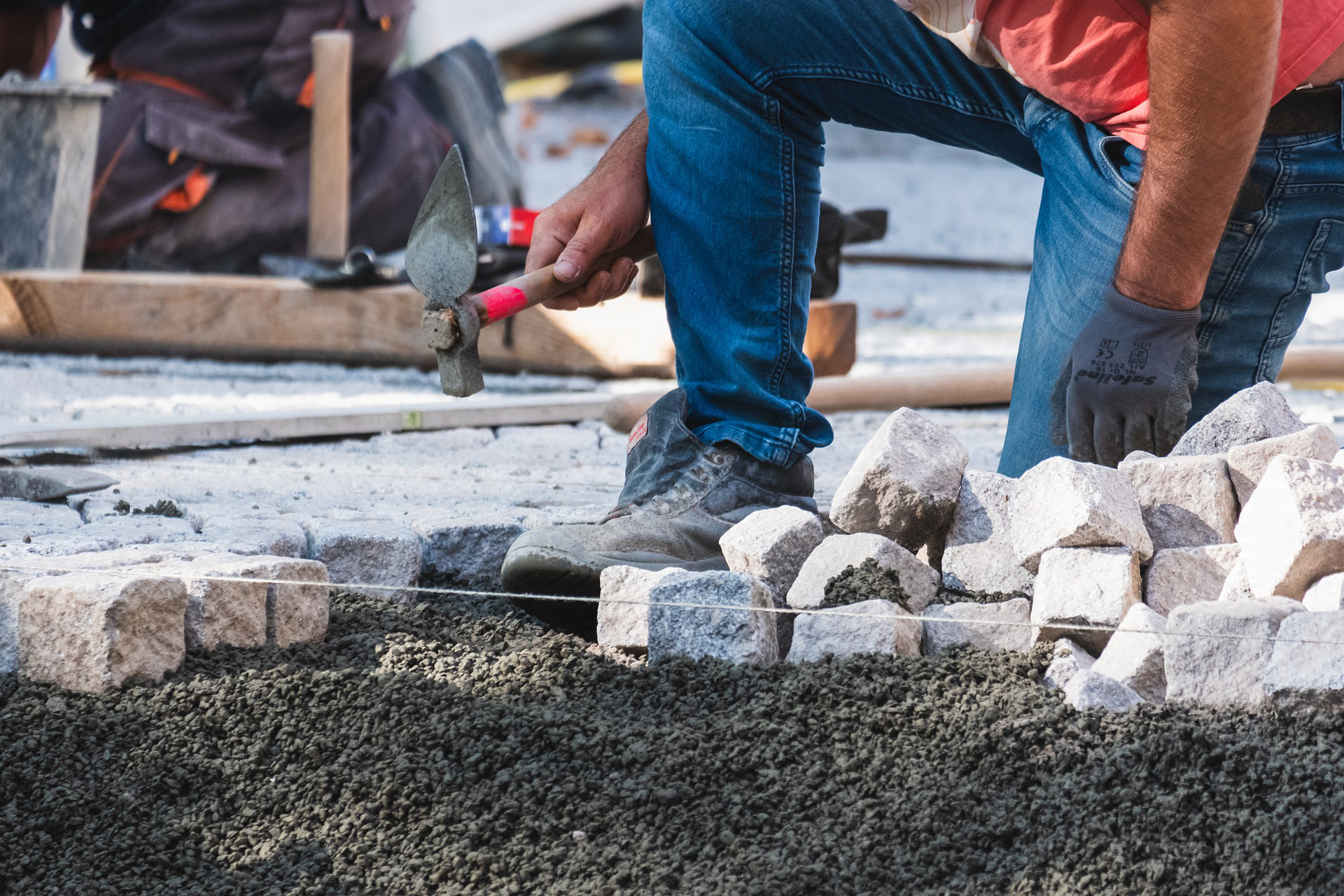
Houses, bridges, and tunnels, what do they have in common? They are made – as indeed most other constructions – out of concrete. It’s a reliable and cheap-to-produce material, existing in a different version since the Romans’ age.
Yearly, the world produces over four billion tonnes of concrete. This production accounts for eight percent of global CO2 emissions. However, there’s the elephant in the room called climate change – you might have heard of it. It’s time for more sustainable alternatives to concrete.
Making concrete starts with mining raw materials composing its mixture – gypsum, limestone, and clay, to name a few. Then, these substances get crushed to a fine powder – raw meal during the grinding phase.
The raw meal goes inside a cement kiln – a long rotating cylinder – where it gets heated up to 1450°C. This step of the process serves to dissolve chemical bonds and recombine them into new compounds. The end product of this process is called clinker, which is later mixed with gypsum and additives to get cement. The grey powder is now ready to be used in construction sites, mixed with gravel, water, and sand.
For two reasons: mining and energy consumption. Mining raw materials generate emissions and impact directly on the environment. Heating machinery up to over 1400°C needs high energy inputs.
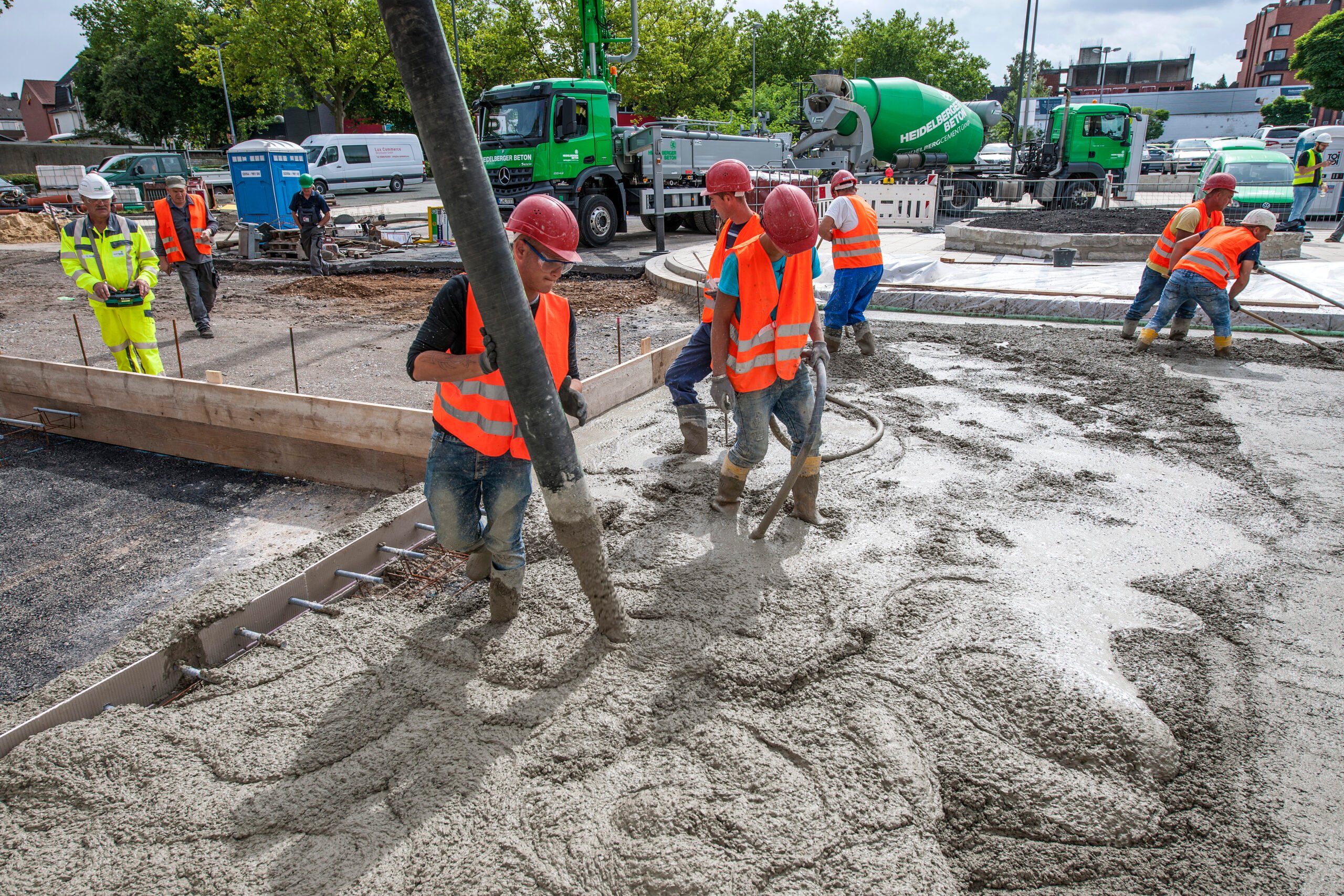
Biomass ashes for sustainable concrete
Biowaste treatment plants burn agricultural and wood waste, obtaining biomass ashes as a byproduct. These work out well as fertilizers. Furthermore, several studies highlighted their potential as binders – materials to unite – for making eco-friendly concrete.
Scholars from the Politecnico di Torino, Italy, found out that biomass ash derived from woodchips and straw – if adequately treated – could create more sustainable concrete.
Additionally, researchers from the University of Zagreb pointed out that wood biomass ash that uses up to ten percent of it in a concrete mixture doesn’t have a significant impact on the material’s consistency. Wood biomass waste will increase in the following years. What about using it in the concrete mix?
Learnings from history
The Finnish company Betolar also uses inorganic materials for its CO2-free concrete formula. Flying ashes from biomass and coal combustion are also part of the mix. In addition, more byproducts from several industries – such as metal, mining, and energy – get into the blend, but the whole formula is a secret.
Although using ashes as a cement component might seem like a recent breakthrough, it is not. Romans combined volcanic and fly ash with lime to form mortar. This same recipe is behind the construction of still-standing monuments such as the Colosseum. Following this path, Betolar develops its formula for resistant, sustainable concrete.
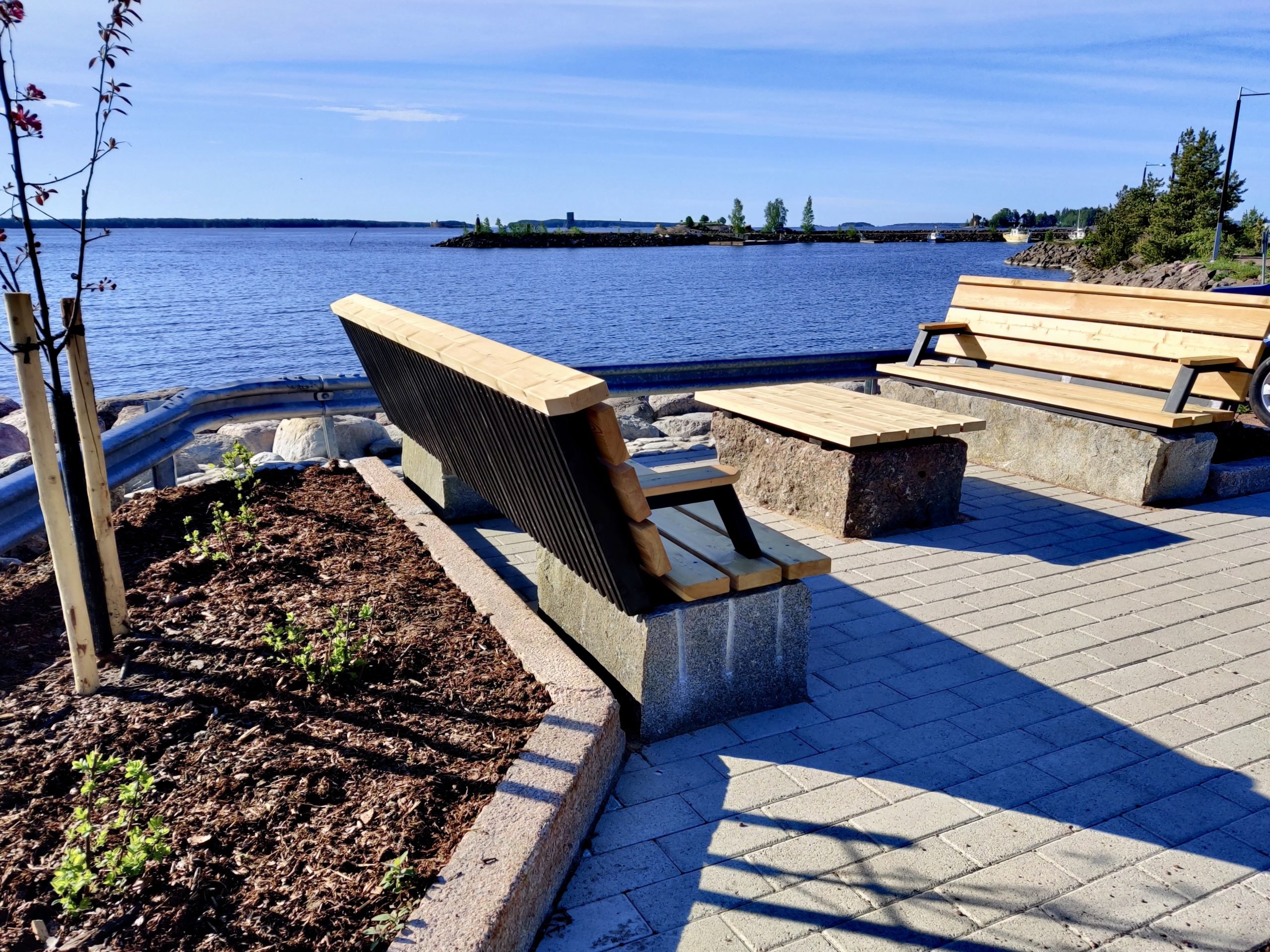
Mixing cement at room temperature
As mentioned above, limestone – in chemistry, calcium carbonate, CaCO3 – is one of the main cement components. Heating it to 1450°C makes it an effective binder. As the reaction occurs, calcium carbonate splits into calcium oxide – CaO – and CO2 – which sums up the one emitted by burning fuel to heat the furnace.
Scientists at Mainz University found a way to do this differently. Instead of burning calcium carbonate, they thought of grinding it with sodium silicate. The result is an intermediate product mixable with caustic soda before being able to act as a binding agent with stones, sand, and water. The main advantage of this procedure is that grinding can happen at room temperature, cutting out of the process furnaces, and using 10 percent of the energy dissipated for heating a cement kiln.
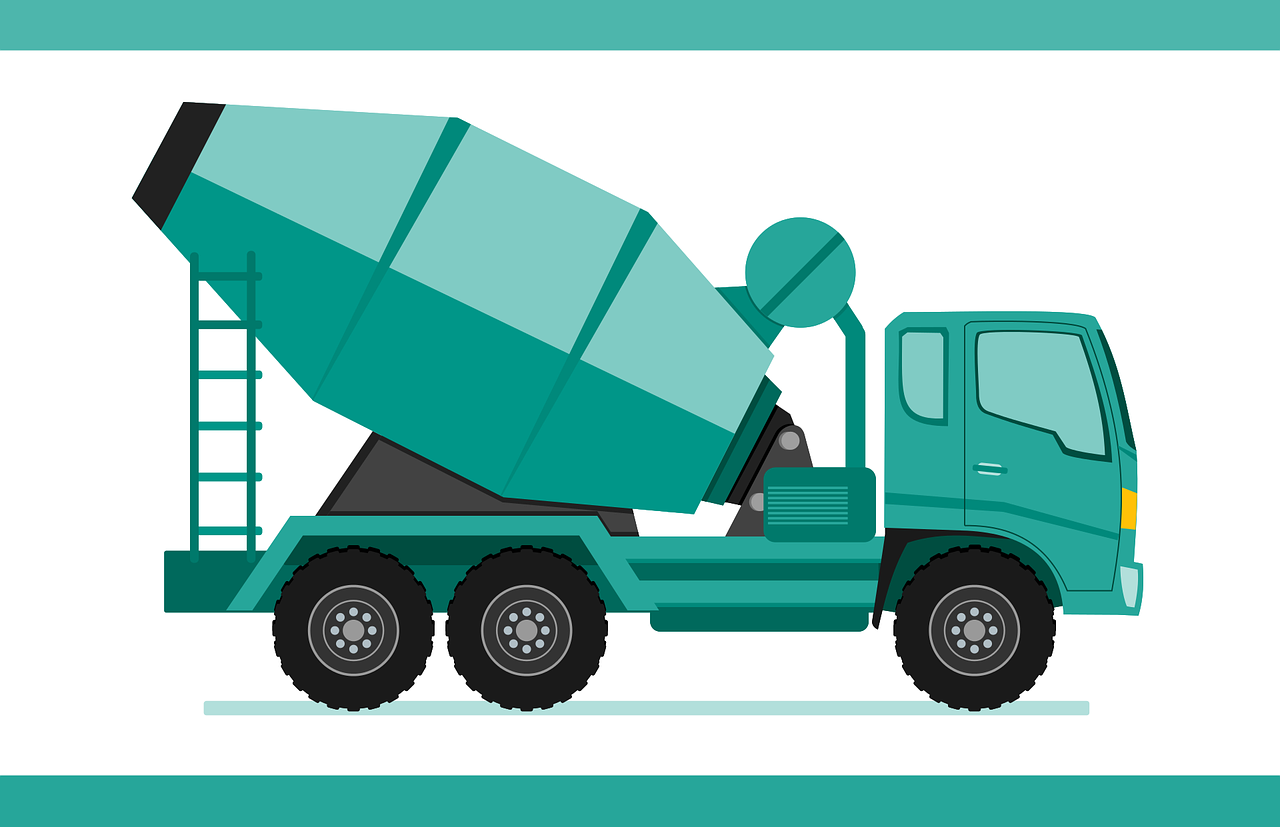
Building with sustainable concrete
As new building concepts emerge – with wood or 3D printing, for instance – concrete still remains the go-to option for most dwellings. European researchers know that and will keep investigating ways to make concrete greener.