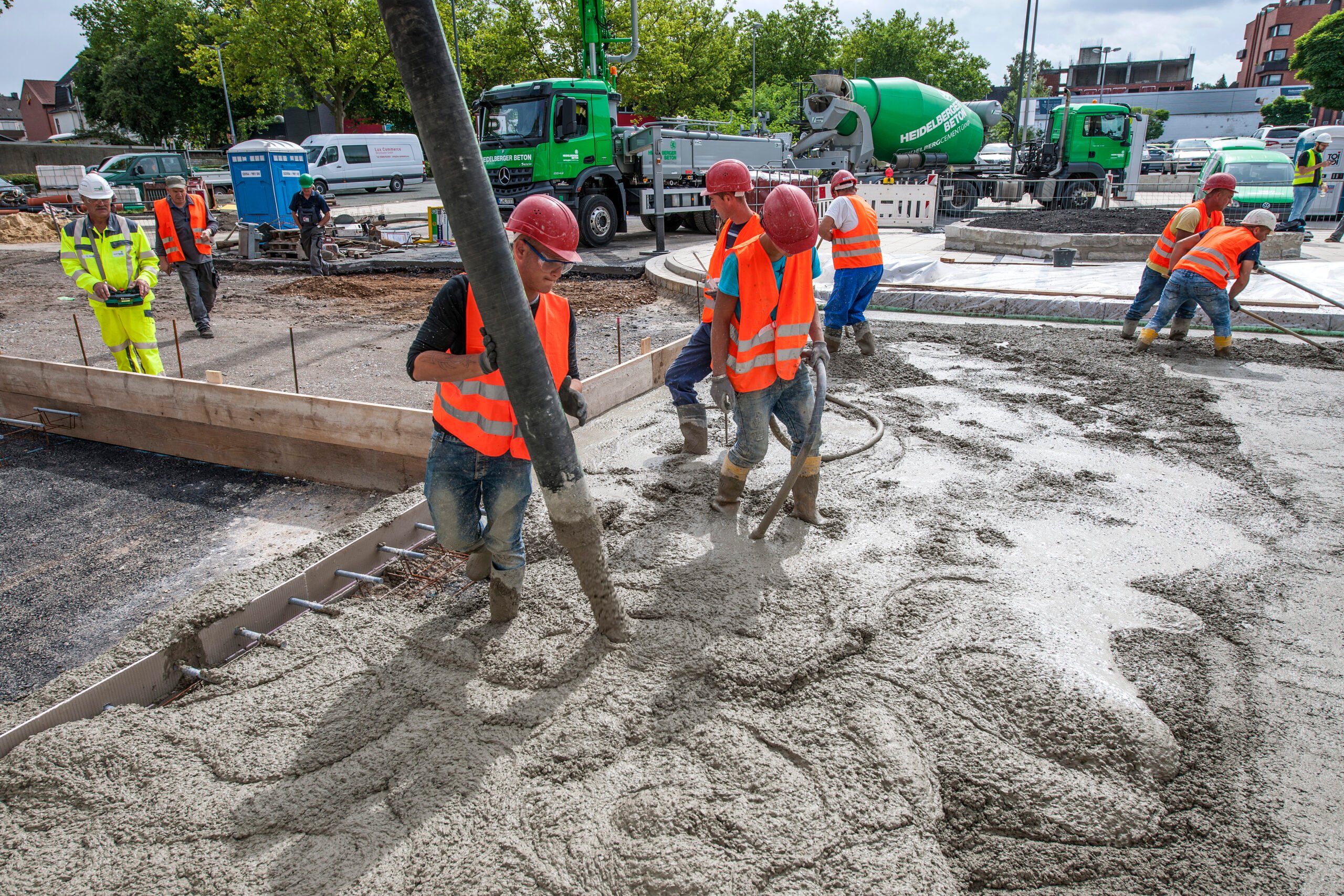
Two thousand years ago, the Romans discovered that if they burnt lime together with volcanic ash and brick they could create a strong, resistant, and durable material perfect for structures such as bathhouses and water pipes. The mix, better known as concrete, eventually became the most popular construction material.
Since the Roman Era, the concrete industry has undergone several changes, but there is still room for improvement. Today, the environment is under the magnifying glass, and the concrete industry aims to create more durable, greener concrete. The question is, can concrete ever be sustainable?
Why is concrete so important?
Concrete is one of the most used building materials in the world. From housing to bridges, roads, and dams.
What makes concrete unsustainable?
Producing cement, a common binder for concrete, causes high CO2 emissions.
How can we make concrete greener?
Some ways include:
- Reduce or replace the amount of cement in concrete with other materials.
- Carbon capture at cement factories.
What else can be done besides changing the recipe for concrete itself?
- Use different materials for concrete reinforcement. This could help in the construct ion of buildings that last longer with no corrosion. But first the amount of conventional Portland cement must be reduced.
- 3D printing cement. It can reduce the amount of concrete needed for construction, but the concrete itself must also be sustainable.
Can concrete be fully sustainable?
In principle, sadly no. As for any other material that draw on non-renewable resources and is
not 100 percent recycled. But it is possible to make concrete less unsustainable. That is what researchers and the concrete industry are currently working on.
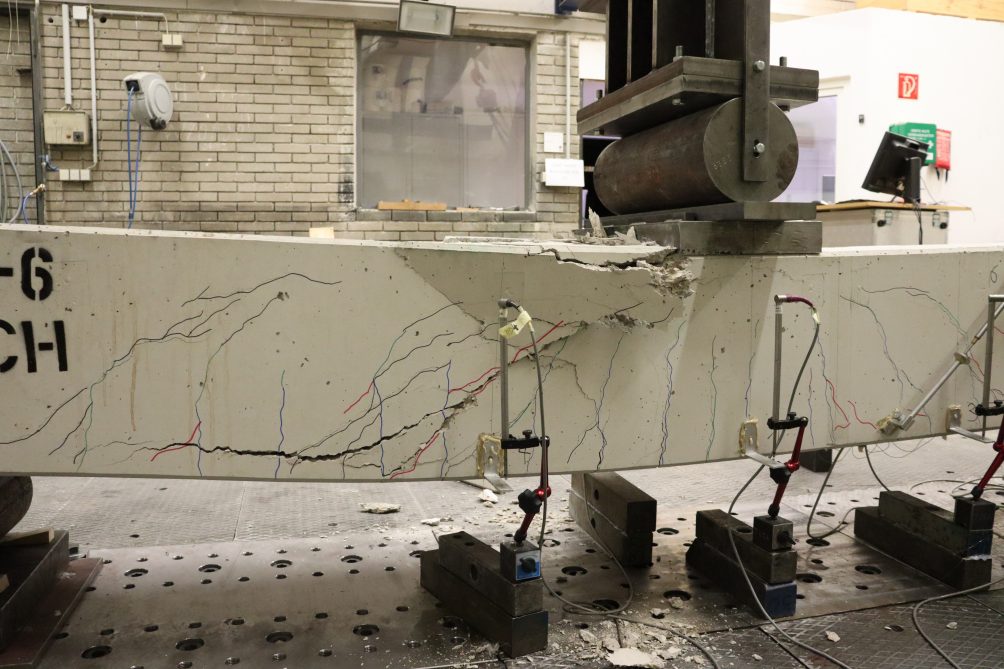
Most convenient, but major polluter
Concrete has several advantages. It is resilient and durable, requiring little maintenance once built. Its resistance to water and heat makes it a safe material for the fundamentals of a wide range of structures; from houses and buildings to roads, dams, and bridges. With this versatility, it is also handy that the ingredients used to make concrete are both abundant and cost-effective.
But concrete is also responsible for 8 percent of the world’s CO2 emissions. According to the German international broadcasting platform Deutsche Welle: “If concrete was a country, its annual pollution would only be topped by the US and China.” As much as 90 percent of concrete CO2 emissions come from producing its cement, a key ingredient in concrete production. Raw materials, including limestone and clay, are burnt in a cement kiln at 1450 °C, emitting between 0.5-0.9 kg CO2 per 1kg cement produced. While this might not seem like too much, cement is heavy and the numbers add up.
High CO2 emissions during the production process are not the only problem concrete faces. Rebar that is used in construction is prone to corrosion, and is the cause of most of the serious damage on concrete structures. Also, the raw materials used to make concrete do not have an endless supply. With these challenges, it is no wonder that the concrete industry is doing their best to find new ways to make concrete. This effort is a partnership between research and industry.
How concrete is made
Concrete is made by mixing a binder, usually cement, and water together with aggregates such as gravel, sand, and crushed rocks. The world does not have an endless source of these materials, but they are abundant. According to Harald Justnes, chief scientist at the Cement and Concrete Research Institute (a department of SINTEF ), there is little need to worry that we will run out of raw materials for concrete. A local area could be depleted of its materials, but not the entire Earth. However, the world is running out of one important ingredient: sand. Therefore, substitutes such as manufactured sand, quarry dust, or even glass powder are being looked into.
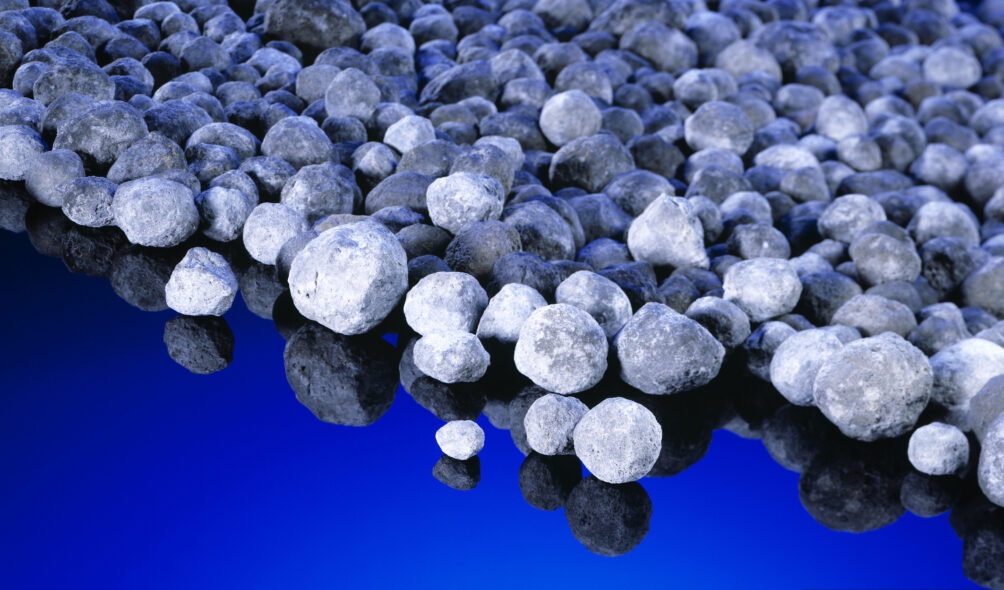
Cement is the most commonly used binder in concrete, but a portion of it can be replaced with supplementary cementitious materials (SCMs) such as fly ash. This is preferable because cement production is responsible for about 90 percent of the CO2 emissions from concrete. Clinker must be burnt at 1,450 °C using fossil or waste-derived fuels. The high temperature means a lot of CO2 is released in the process. A total of 40 percent comes from burning fuels, while 60 percent comes from removing CO2 from the raw material fed into the kiln. This is comprised of calcium carbonate for 80. The clinker is then milled together with SCMs, for instance fly ash and gypsum, to regulate the setting properties. Only then it is called cement.
Carbon capture: Not unique, but effective
Carbon capture is not a unique invention for the concrete industry, but it is a useful one. According to the Federation of the European Precast Concrete Industry BIBM “the cement industry has a strong focus on carbon capture as its key technology. This amounts to 42 percent of the CO2 emissions it intends to cut down on by 2050.” Some companies have chosen this approach, such as the German company HeidelbergCement, which aims to build the world’s first carbon-neutral cement plant in Sweden. This means an emission reduction of up to 1.8 million tonnes of carbon dioxide each year once the plant is built.
Replacing portions of the cement
Researchers also aim to reduce CO2 emissions by changing the building material itself, for example, by replacing a portion of the cement or blending it with SCMs. By swapping out the traditional cement with other material, CO2 emissions from kilning the cement are reduced. This would not just mean lower CO2 emissions, but also a reduction in the primary energy input by 15 percent. This is also not an entirely new concept. For years, companies have used the zero-emission alternatives fly ash and blast furnace slag. But these materials will not last forever. As coal plants close down, fly ash disappears with it, and we are reaching the end of procurable blast furnace slag in Europe.
Therefore, we must now look for new types of SCMs which will not run out in the near future. The challenge is to find alternatives that retain the strength and reliability of concrete without being too expensive, emitting too much CO2, or draining too much of natural resources. In 2016, researchers at the Austrian Graz University of Technology (TU Graz) found such a type of SCM which can reduce CO2 emissions by up to 30 percent. Researcher Joachim Juhart at TU Graz explains in a press release from the university: “We added very fine mineral powders as a microfiller and thus optimized the packing density of the mix. By this means we were able to add other fillers made from rock powder or even ground-granulated furnace blast slag. The major advantage: The fillers can be produced from various types of rock that are available in the region, so that CO2 emissions during the production process are cut back significantly.”
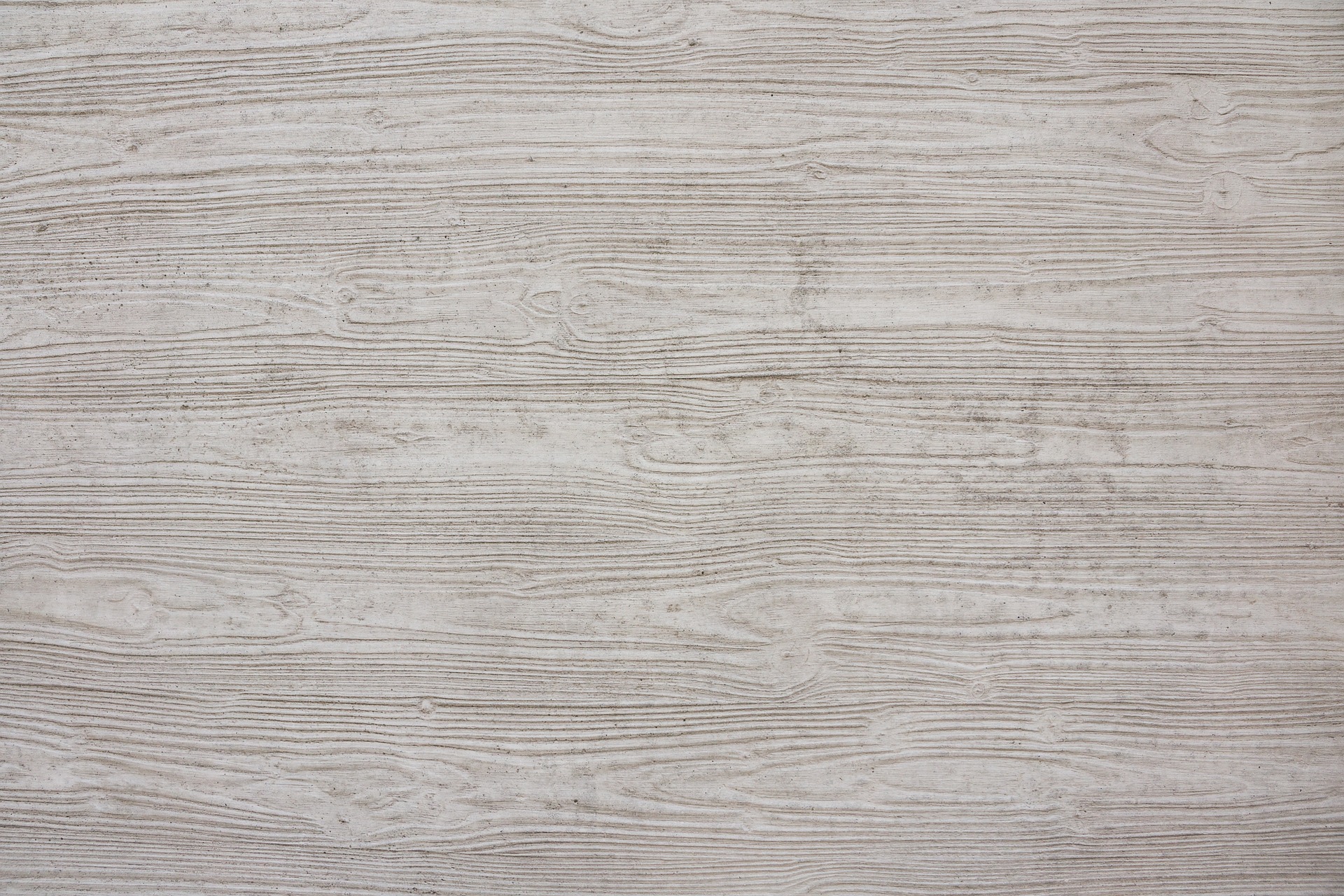
SCMs requires new strategies for construction
Today, concrete has an average clinker factor of 0.72, meaning that 72 percent of the clinker used in concrete is actual cement and the remaining 28 percent are SCMs. Cement cannot be completely removed, but the concrete industry aims to get the clinker factor down to 0.55 by 2050. Besides the research as TU Graz, several other projects are ongoing. For example, since 2014, the Swiss project LC3 has worked to create a new type of cement based on limestone and calcined clay, which reduces CO2 emissions by up to 40 percent.
“When you have large cement replacements, it will take longer for the concrete to achieve its desired strength,” says Justnes. When a structure is made with an environmentally-friendly concrete piece, it must stay in the mold for longer than conventional concrete. Builders will have to wait longer before using the same mold to create a new element, which will slow down production. Or they could procure more molds for the construction site and cast other elements before stripping the first one at a later stage, which would keep up the rate of productivity, but also be more costly requiring higher investment.
But SCMs also bring opportunities for new developments. Concrete has a low tensile strength, but high compressive strength. Structures under tension are reinforced with steel for this reason. As mentioned earlier, these steel reinforced bars (rebars) are prone to corrosion, shortening the durability of a reinforced concrete structure.
“The largest problems we face when building with concrete is the steel that corrodes, not the concrete itself. It accounts for about 80 percent of the cases when concrete needs to be repaired or replaced,” Justnes points out. With higher numbers of replacements of cement with SCMs (more than 50 percent) it is possible to replace the steel with other materials as reinforcements – materials which are not stable in regular concrete.
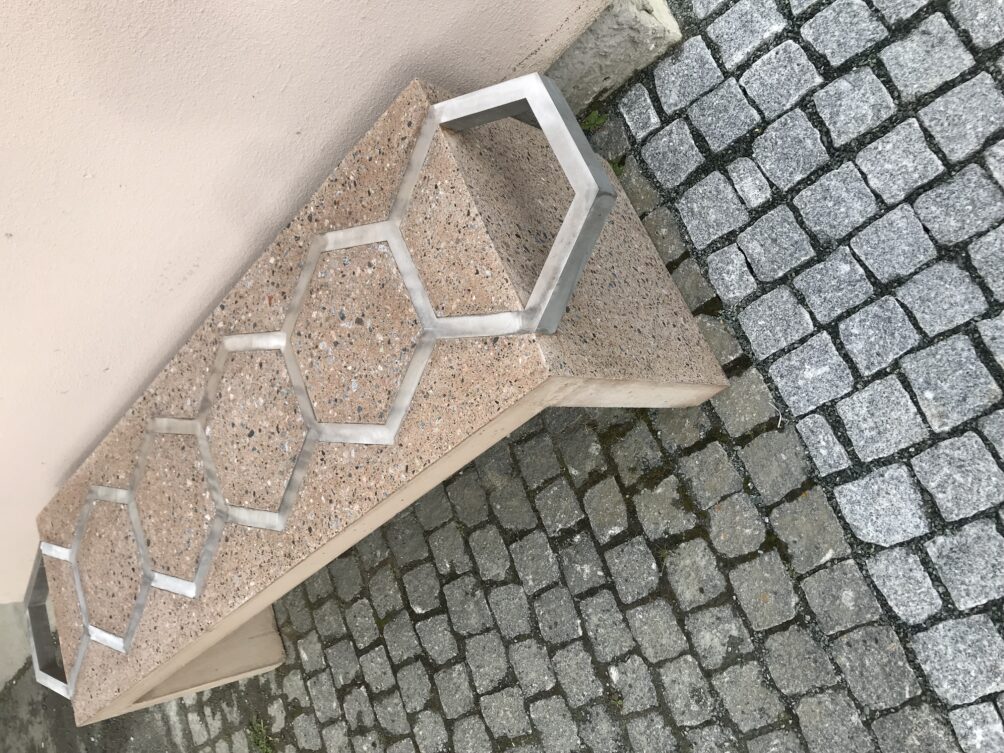
Aluminum rebar
One such material is aluminum. Through the research project Durable Aluminum Reinforced Environmentally-friendly Concrete Construction (DARE2C), Justnes has researched the possibility of using aluminum rebar. This could be used to build structures which have an extraordinary long service life without any need for maintenance.
Conventional cement has a pH value of 12.0-13.8, which causes the aluminum to corrode and produce hydrogen gas. With pozzolanic SCMs, the pH value is lowered to 9, which is beneficial for the durability of the aluminum. The end result is a type of concrete that emits less CO2 during production, and that does not need replacement or repairs as often as today’s concrete structures. Less cement may also be needed in the production process. With conventional cement, the rebar needs a cement coating of a minimum of 50 millimeters to avoid fast corrosion. Aluminum rebar only needs a coating of 20 millimeters for mechanical grip, and its surface can also be exposed for decorative or practical purposes.
Aluminum is not the only possible type of rebar in future. Glass fiber reinforced polymer is also considered an alternative, but they are not as ductile as metals.
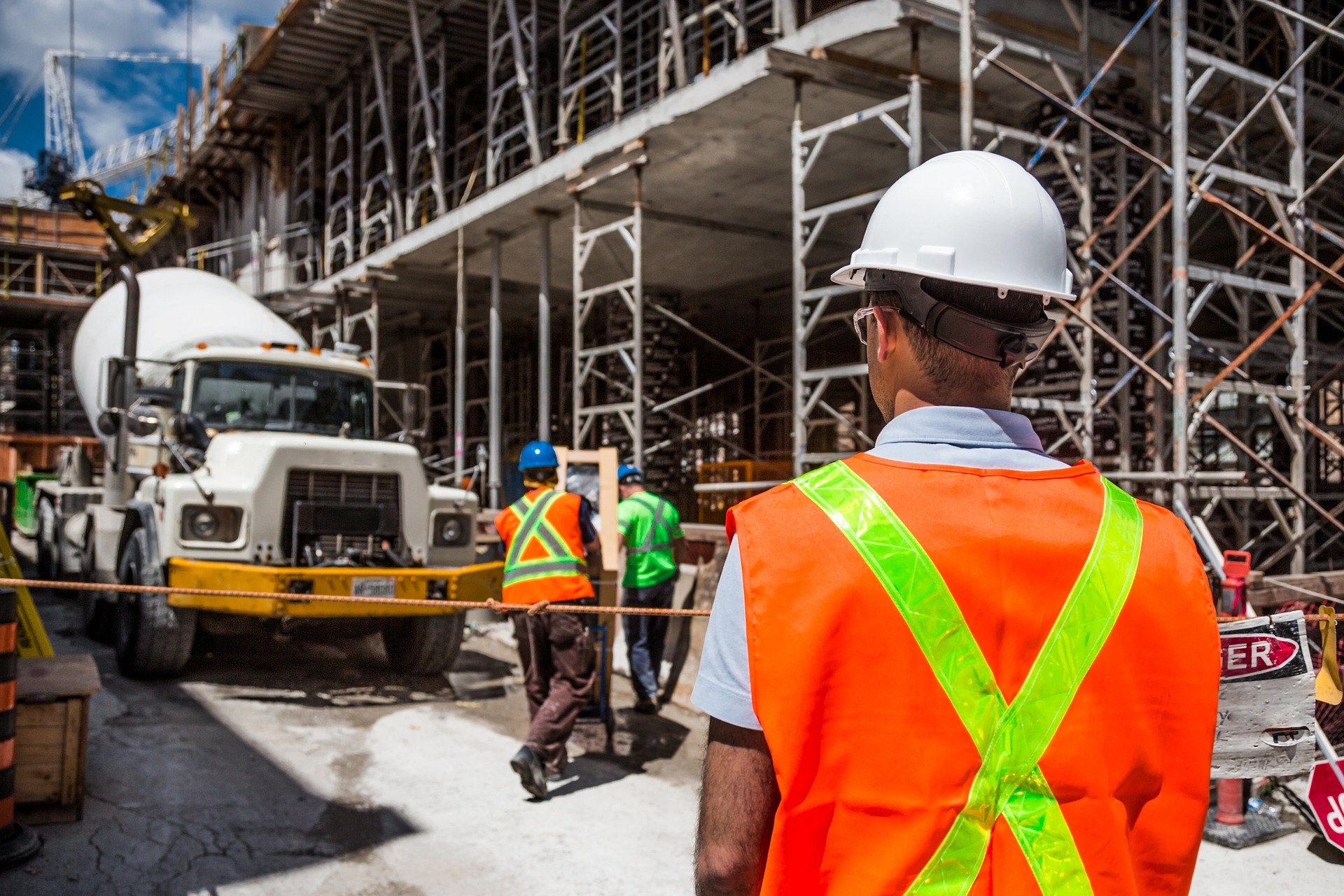
Removing cement from concrete completely
Another way to make concrete more sustainable is by eliminating cement altogether. This is what researchers on geopolymer concrete aim to do. Geopolymers are used as a binder instead of the cement. They can also be referred to as alkali-activated materials, where furnace blast slag, fly ash or even calcined clay can form the basis.
“One problem with using this option is that it has no defined standard,” Justnes says, and cites an example: “If you want to use an alkali-based geopolymer to make a wall panel, you can get technical approval for that wall panel, but not for the geopolymer itself”. A defined standard could be set, but making such a standard will take time.
One company who focuses on this is Finnish Betolar. Their Geoprime® solution, which replaces cement as a binder, is made using side streams from other industries, such as pulp and paper, mining and forestry. Their solution allows them to make concrete that reduces CO2 emission by up to 80 percent compared to conventional concrete.
It is not yet known whether geopolymer concrete or concrete with reduced quantities of ordinary Portland cement is the most sustainable option. Various universities are researching the two different solutions. According to Salet, we can eventually compare the two solutions in a life cycle assessment to see which is the more sustainable option. But it will take a couple of years until the technology is ready for comparison.
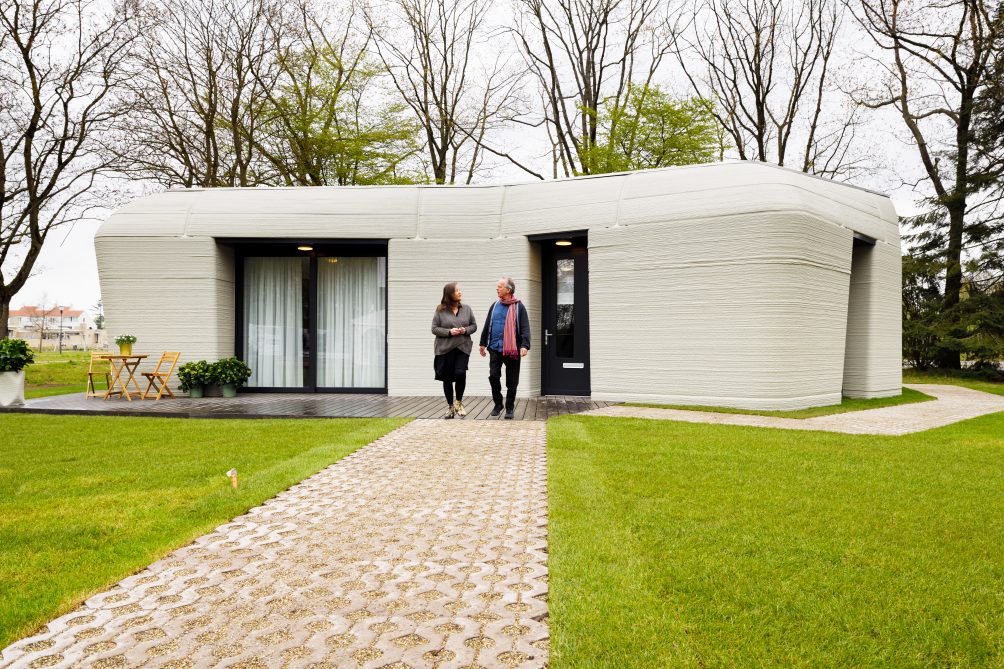
3D printing concrete
In 2021, Elise and Harrie Dekkers moved into their new 3D-printed home in the Dutch city of Eindhoven. The couple became the first ever to live in a house constructed this way. Their house is part of ‘Project Milestone’, a triple helix project planning to 3D print five concrete houses to prove that it is possible.
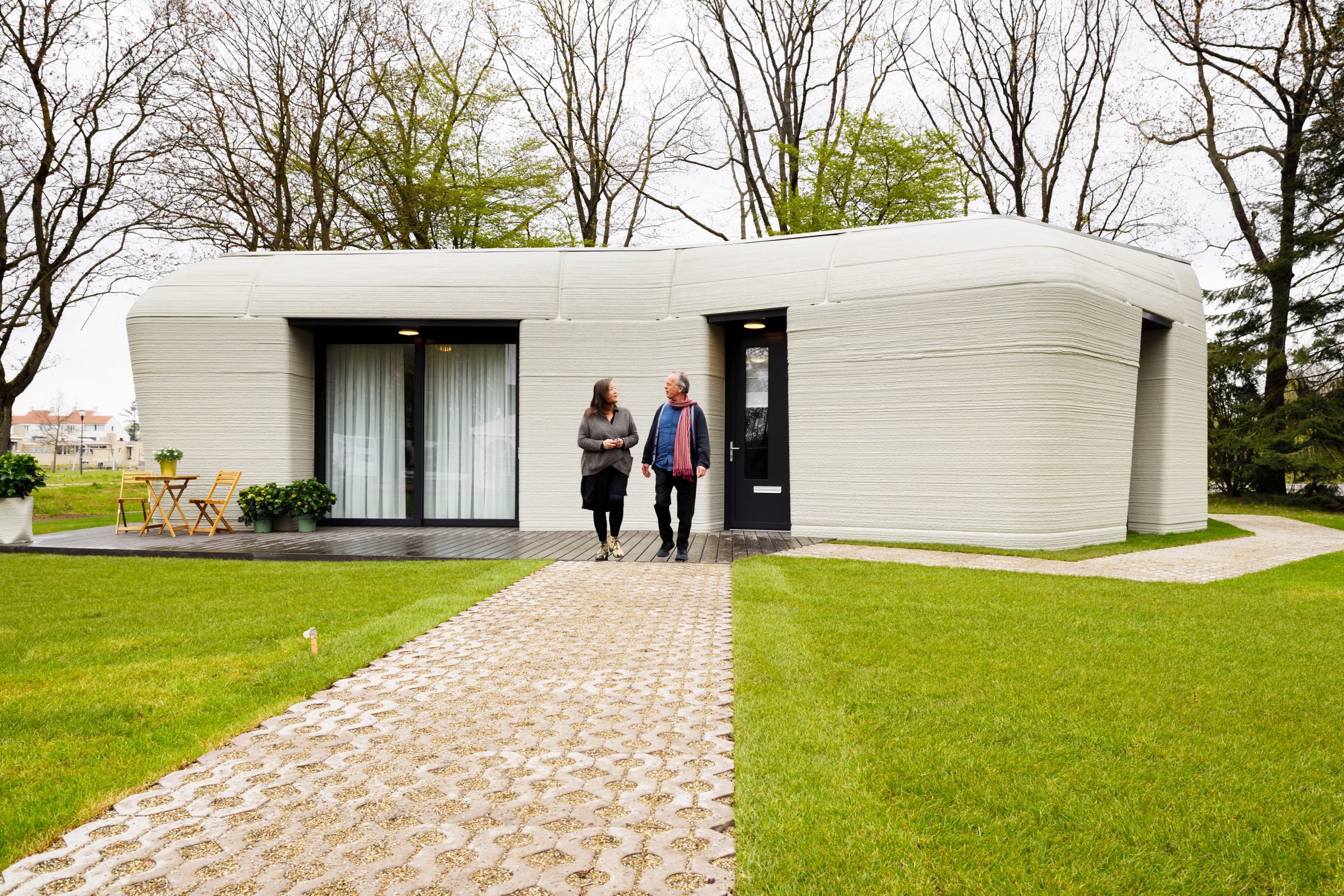
3D printed concrete is said to improve productivity and lower the labor force needed for construction. Construction is digitalized, which means it can go faster between a design that it drawn up until it can be made in real life. 3D printing can also be better cost-wise. It could be as much as 78 percent more profitable than a house built with conventional cement, according to a United Arab Emirates study comparing the two building construction techniques.
Conditional sustainability
Innovative and with several advantages, 3D-printing concrete can become an important construction method in the future. But is it sustainable?
It could be, depending on the production methods. Concrete is printed in layers stacked on top of each other to form a certain structure. This is more complex than regular concrete construction, but it also allows the builder to use concrete more wisely.
“In a beam, column, or wall, there’s a lot of places where there is concrete, but structurally, so strength-wise, there’s no need to place the concrete there. A robot is able to place concrete only where it is needed,” says Theo Salet, Professor of Structural Design/Concrete Structures at TU Eindhoven.
Support us!
Innovation Origins is an independent news platform that has an unconventional revenue model. We are sponsored by companies that support our mission: to spread the story of innovation. Read more.
At Innovation Origins, you can always read our articles for free. We want to keep it that way. Have you enjoyed our articles so much that you want support our mission? Then use the button below: