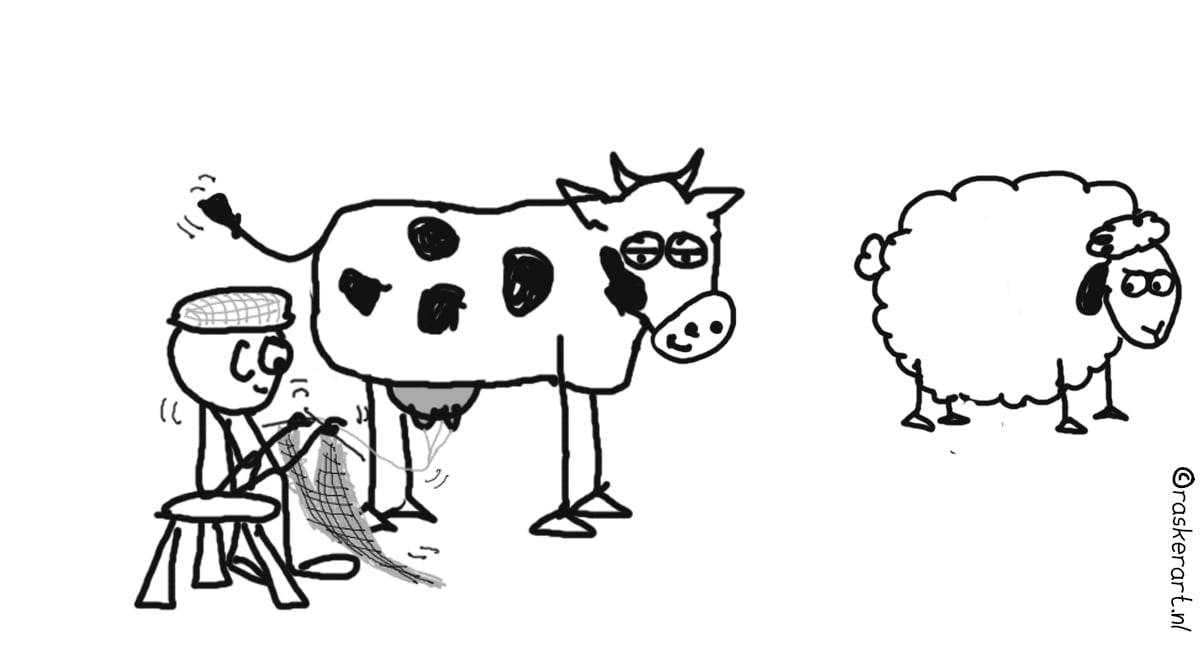
Ein Hemd aus Sauermilchflocken klingt nicht besonders reizvoll. Doch genau das macht die Mikrobiologin und Modedesignerin Anke Domaske. Sie hat eine nachhaltige Methode entwickelt, um Kasein aus Milchflocken zu gewinnen. Im meistgelesenen Artikel der letzten Woche erklärt Domaske, dass die Methode ein bisschen wie Kochen sei. Ein spezielles Rezept, das die Flocken verwendet, kombiniert andere Zutaten wie Bienenwachs, Weizenkleie und Wasser zu einer Art Teig. Dieser wird dann durch eine große Nudelmaschine mit kleinen Löchern gepresst, nur, außer dass statt der Nudeln Textilfasern aus der Maschine kommen.
Die Technik, Textilfasern aus Milchprotein herzustellen, ist nicht neu. Laut Jantiene van Elk, Bibliothekarin des Textilmuseums in Tilburg, gibt es sie seit den 1930er Jahren. „Normalerweise würde ich Sie auf ein Buch verweisen”, lacht van Elk am Telefon. Dann erklärt sie: „Es ist eine halbsynthetische Faser und wird als Ersatz für Wolle verwendet. Milchwolle ist viel weicher als normale Wolle. Das Milchprotein wird über alle möglichen Schritte und chemische Verbindungen zu einer langen Faser verarbeitet.“
Das Neue an Domaskes ‚Rezept’ ist, dass keine Chemikalien verwendet werden. Außerdem wird der Rohstoff, der die Grundlage für das Textil bildet, in der Regel weggeworfen. Untersuchungen der Universität Berlin haben ergeben, dass die Deutschen etwa zwei Millionen Tonnen Milch pro Jahr wegschütten. Und auch die Niederländer können eine Menge entsorgen. Nach Angaben von Milieu Centraal (einem niederländischen Umweltverband) haben die Niederländer im Jahr 2019 pro Person etwa 10 Liter Milch und Milchgetränke in den Ausguss geschüttet. Eine echte Schande, denn Domaske hätte damit etwas anfangen können.
Zellstoff
Die meisten Stoffe werden laut Van Elk aber aus Zellstoff hergestellt. „Man hat natürliche Zellulose von Pflanzen -die bekannteste davon ist Baumwolle – und Bäumen. Die Industrie verwendet dafür alle Arten von Holzspänen. Aber man kann auch aus Bambus Zellulose gewinnen. Dann gibt es synthetische Zellulose aus der Erdölverarbeitung – seit den 1950er Jahren sind alle möglichen Varianten davon erfunden worden. Aber ob man nun natürliche Zellulose oder synthetischen Zellstoff verwendet, der Zellstoff verwandelt sich erst dann in eine Textilfaser, wenn alle möglichen Schritte unternommen und chemische Zellstoffe hergestellt wurden.”
Kann man das nicht nachhaltiger machen? Sicher, was würden Sie über Jalila Essaidi sagen? Die nicht nur eine sehr starke Faser auf der Basis von Spinnenseide entworfen hat, sondern auch Kleidung aus Kuhdung herstellt. Oder schauen Sie sich die Designerin Billie van Katwijk mit ihren Taschen aus Kuhmägen an. Diese beiden Rohstoffe werden allgemein als Abfall betrachtet und werden selten, wenn überhaupt, ein zweites Mal zum Leben erweckt.
Dasselbe gilt für überschüssige Algen, die aus Seen gefischt oder am Strand angeschwemmt werden. Aber der Designer Tjeerd Veenhoven hat bewiesen, dass man aus ihnen auch Textilfasern herstellen kann. Er wurde 2015 mit dem Global Impact Preis ausgezeichnet – einem Förderpreis für nachhaltige Innovationen in der Bekleidungsindustrie. „Mutter Natur hat uns mit Baumwolle eine sehr schöne Faser geschenkt”, sagt Veenhoven. „Aber so wie wir sie jetzt nutzen, brauchen wir unglaublich viel davon. Das ist einfach nicht mehr tragbar.”
Alternative zu Ackerland
Alles begann in einer großen Wanne, in der Veenhoven die Algen gären ließ. Er trocknete sie und behandelte sie dann auf ähnliche Weise wie normale Zellulose, d.h. mit Chemikalien. „Ja, ich weiß. Ich wollte eine Alternative zum Baumwollanbau finden. Immer größere Flächen auf der ganzen Welt werden für den Baumwollanbau reserviert. Um die Ernte dieser Kulturen zu erhalten, verbrauchen die Plantagenbauern viel Wasser, Dünger und Pestizide. Im Internet gibt es Fotos von Seen in China, die in den letzten zwanzig Jahren durch den Baumwollanbau völlig ausgetrocknet sind. Die Zellulose muss nicht unbedingt aus der Baumwollpflanze stammen. Sie kann überall auf der Welt gefunden werden. Sogar in Algen, so dass Ackerland für etwas anderes genutzt werden könnte.”
„Algenstoffe“
Doch trotz der Alternative, die Veenhoven zu bieten hat, sind seine „Algenstoffe” (noch) nicht in Produktion. Es ist zu teuer, Zellulose aus den Algen zu gewinnen. „Im Moment ist die Geschichte stärker als der Business Case. Aber ich bin sicher nicht pessimistisch. Ich bin nicht der Einzige, der daran arbeitet. Immer mehr Start-ups – die viel weiter sind als ich – lassen sich nachhaltigere Alternativen einfallen. Sie werden auch zunehmend von den großen Marken übernommen, das hat wirklich Auswirkungen. Denn die großen Marken sind in der gesamten Kette aktiv.”
Er hat auch noch nicht aufgegeben. Denn um von den Chemikalien, die Veenhoven dabei einsetzt, wegzukommen, forscht er, ob die Cellulose auch auf natürliche Weise aus den Algen gewonnen werden kann. „Enzyme kann man seit Millionen von Jahren auf der Erde finden. Sie bauen Systeme auf natürliche Weise ab. Die Verdauung funktioniert auf die gleiche Art und Weise. Es dauert eine Weile, bis man alles herausfindet, denn jedes System hat seine eigenen Enzyme.”
Der natürliche Abbau von Systemen
Der Einsatz von Enzymen im Gegensatz zu Chemikalien hat eine Reihe weiterer Vorteile. Zum Beispiel kann man biologische Systeme verwenden, die in der Lage sind, immer wieder etwas abzubauen. Veenhoven: „Man muss die Enzyme nur am Leben halten. Aber das ist im Prinzip gar nicht so schwierig. Bei Raumtemperatur machen sie ihre Arbeit sehr gut. Im Gegensatz zu chemischen Prozessen, die oft Wärme benötigen. Daher wird unsere Methode viel energieeffizienter sein.”
Veenhoven geht davon aus, dass es noch fünf bis zehn Jahre dauern wird, bis die gesamte Bekleidungsindustrie auf nachhaltigere Alternativen außer Baumwolle umgestellt hat. „Viele Prozesse sind jetzt knapp davor, umgesetzt zu werden. Es geht darum, den richtigen Business Case zu finden. Außerdem gibt es eine wachsende Nachfrage seitens der Industrie, und die Verbraucher denken immer mehr über Kleidung nach. Aber Veränderung braucht Zeit.“