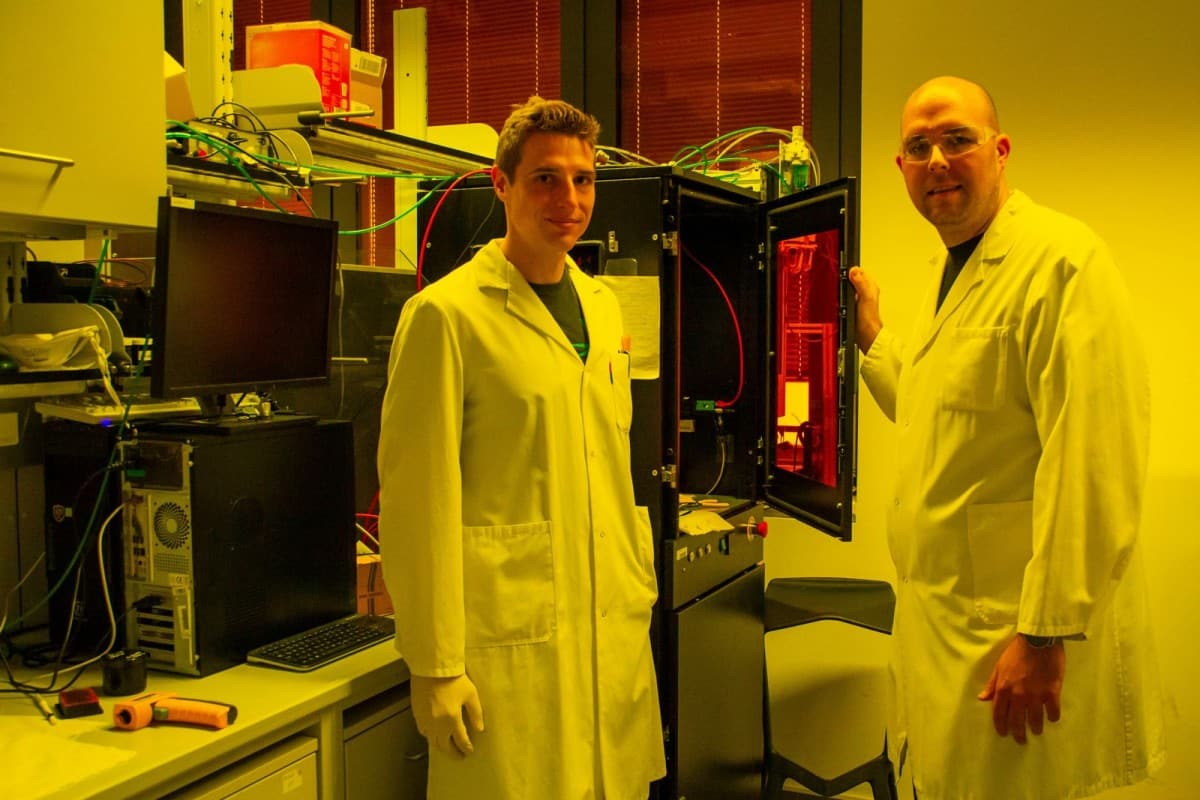
Stefan Baudis will die natürliche Regeneration von beschädigten Knochen mit einem Knochenersatz aus dem 3D-Drucker ermöglichen. Dieser soll biologisch abbau- und aufbaubar sein und somit keinen Fremdkörper darstellen.
Gesunde Knochen sind erstaunlich regenerationsfähig. Ununterbrochen sind bestimmte Zellen damit beschäftigt, diese ab- und wieder aufzubauen. Daher können Knochenbrüche ganz von selbst heilen, erklärt Stefan Baudis von der Abteilung Makromolekulare Chemie am Institut für Angewandte Synthesechemie an der TU Wien. Bei ernsthafter Beschädigung des Knochens durch Unfall, Tumor oder Infektion sind der Heilung oft Grenzen gesetzt. Die betroffenen Patienten brauchen einen Knochenersatz um eine Amputation zu vermeiden.
Individualisierter Knochenersatz
Ein ideales Instrument für den Knochenersatz bildet der 3D-Druck.Verbreitet ist das Verfahren der Fused Filament Fabrication. Dabei werden Thermoplasten aufgeschmolzen, in dünnen Fäden deponiert und Schicht für Schicht zu Strukturen aufgebaut. Ansätze für patientenspezifische Implantate gibt es bereits im Gesichts-, Kiefer- und Schädelbereich. Darunter auch einige, die bereits in der Klinik eingesetzt werden, weiß Baudis. Es handelt sich aber immer noch um Fremdkörper.
Komplett abbaubar
Baudis verfolgt einen radikal anderen Ansatz: Einen Knochenersatz, der biologisch abbaubar ist. Er will dem Körper ein passendes Knochengerüst aus dem 3D-Drucker vorgeben, das von körpereigenen Zellen besiedelt und von diesen zum ganz normalen Knochen umgebaut werden kann. Die Errichtung eines neuen Christian Doppler Labors (CDL) ermöglicht ihm jetzt von der Grundlagenforschung zur Anwendung zu kommen. CDL ist eine Förderinitiative, welche die Kooperation mit Firmenpartnern vorsieht. Das Labor läuft unter dem Titel Advanced Polymers for Biomaterials and 3D Printing und wurde am 25. Juni eröffnet.
Moderne bildgebende Computerverfahren ermöglichen die präzise Vermessung eines beschädigten Knochenstücks. Der benötigte Knochenabschnitt lässt sich genau bestimmen und innerhalb weniger Stunden im 3D-Druckverfahren herstellen und an den Knochen ankleben, so Baudis.
Komplexe Anforderungen
Was einfach klingt, ist aus der Perspektive der Materialwissenschaft eine große Herausforderung. Das künstlich hergestellte Knochengerüst muss komplexen Anforderungen entsprechen:
- Die Zellen, die für den natürlichen Ab- und Aufbau der Knochen zuständig sind, werden durch eigene Blutgefäße versorgt, die den Knochen durchziehen. Um diesen Vorgang auch im 3D-Druckmaterial zu ermöglichen, muss dieses eine poröse Struktur haben. Nur so können die Zellen eindringen und einen funktionierenden Stofftransport vorfinden.
- Das Material muss fest, darf aber nicht zu spröde sein, damit es nicht gleich bricht.
- Das Material muss in überschaubarer Zeit abbaubar sein. Wenn dieses durch den natürlichen Knochen ersetzt wurde, darf vom Gerüst nichts übrigbleiben.
- Im Material sollen bereits Partikel aus Calciumphosphat eingebaut sein, die dann in das natürliche Knochenmaterial umgewandelt werden.
Anforderungen an den 3D-Druck
Last but not least muss das Material für den 3D-Druck geeignet sein. Es muss bei Raumtemperatur flüssig bleiben, bis es mit Licht der passenden Wellenlänge bestrahlt wird. Dadurch wird eine chemische Kettenreaktion ausgelöst, die das Material an den bestrahlten Stellen aushärtet.
Dazu Baudis: „Wir wissen bereits viel über die Chemie der einzelnen Komponenten, die dafür nötig sind. Nun forschen wir an den passenden Materialgemischen, mit denen sich all diese Anforderungen erfüllen lassen.”
Neben dem Materialgemisch soll auch die 3D-Drucktechnologie weiterentwickelt werden. Dabei kann das Team auf viel Wissen und Erfahrung an der TU Wien zurückgreifen. Mehrere Forschungsgruppen sind involviert.
Photopolymerbasierte Systeme
Im Materialgemisch konzentriert sich das Team auf photopolymer-basierte Systeme. Photopolymere entstehen innerhalb von wenigen Sekunden durch die Belichtung von speziellen lichtempfindlichen Harzen. Das heißt, die flüssige Formulierung wird dort fest, wo sie mit Licht bestrahlt wird. Der 3D-Druck wird durch die schichtweise Belichtung dieser Harze in der Stereolithographie ermöglicht.
Dem Knochen sehr ähnliche Materialeigenschaften können durch die Kombination von verschiedenen Monomeren, Additiven und Füllstoffen erzielt werden. Die Monomere werden so gewählt, dass biologisch abbaubare Polymere entstehen. Die Porosität des Knochengerüsts und die äußere Form werden in CAD-Planung gezielt gesteuert und der Situation im Patienten angepasst.
Das Christian Doppler Labor
Die auf den gleichnamigen österreichischen Mathematiker und Physiker zurückgehende Förderinitiative der Christian Doppler Forschungsgesellschaft ermöglicht hervorragenden Wissenschaftern anwendungsorientierte Grundlagenforschung in Kooperation mit innovativen Unternehmen. Die Finanzierung erfolgt durch die beteiligten Unternehmen und die öffentliche Hand. Im vorliegenden Fall war der Fördergeber das Bundesministerium für Digitalisierung und Wirtschaftsstandort (BMDW). Firmenpartner waren KLS Martin, Lithoz und TCC.
Auch interessant:
Biologisches Gewebeimplantat per 3D-Druck
Forschungsprojekt: Per 4D-Druck Blutgefäße herstellen
VIVATOP: Wie VR und 3D-Druck Chirurgen unterstützen
Implantat-3D-Druck: Kumovis gewinnt Münchener Businessplan