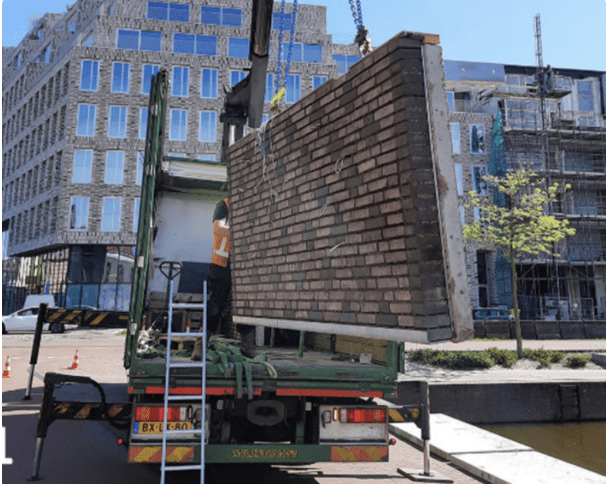
Het huis van de toekomst is groen en circulair. Straks bouw je een huis met stenen die gebakken zijn met waterstof. Deze bakstenen kun je vervolgens ook nog eens cementvrij stapelen. Vergeet ook het interieur niet, dat is straks gemaakt van milieuvriendelijk plastic.
Voor het bouwen van huizen zijn bakstenen nodig en om die te maken wordt veel gas verbruikt. Een gemiddelde steenfabriek verbruikt circa zes miljoen m3 aardgas per jaar. De bouwsector is al decennia bezig om de schadelijke emissies terug te dringen. Steenfabriek Rodruza, energiebedrijf Essent en waterstofspecialist HyMove slaan hun handen nu ineen om de baksteenindustrie te verduurzamen met waterstof.
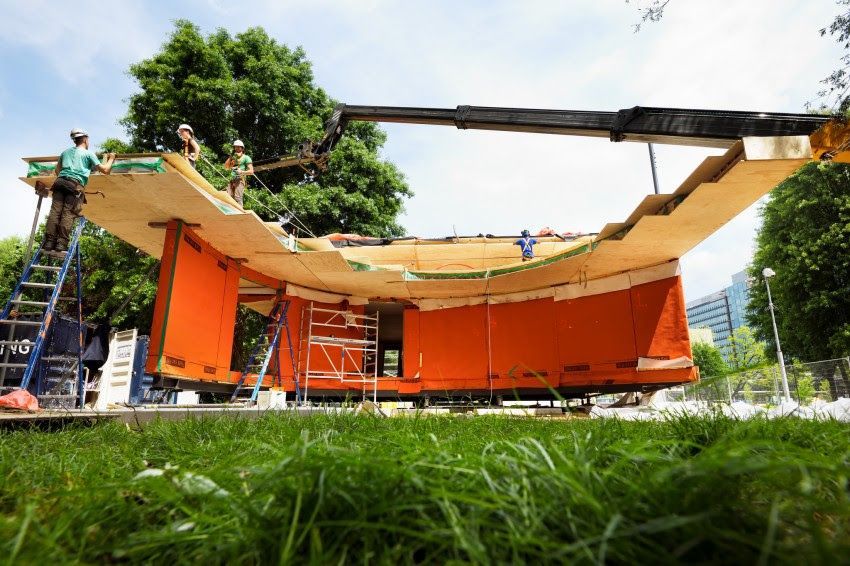
Kortetermijnoplossing
HyMove gaat over de applicatiezijde van het samenwerkingsproject. Het bedrijf is gevestigd in Arnhem en levert systemen voor brandstofcellen op basis van waterstof aan diverse bedrijven in Europa. Volgens Tina Pan, operations manager van HyMove, kwam de samenwerking met Essent en Rodruza tot stand na een project waarbij het bedrijf de brandstofsystemen promootte.
“De techniek om waterstof betrouwbaar en veilig om te zetten in elektriciteit hadden we onder de knie. Alleen de logistieke kant van de waterstofvoorziening niet. Daarover hadden we al een tijdje contact met een leverancier. Zij leveren waterstof door gebruik te maken van Liquid organic hydrogen carriers (LOHC), een organische olie. Waterstof kan daarin veilig opgeslagen en vervoerd worden”, vertelt Pan. “Op elke locatie kun je de waterstof eruit halen. De olie kan vervolgens weer terug gebracht worden voor hergebruik. We vonden dit een grote kans.”
Volgens Pan is het transporteren van waterstof naar industriegebieden via de huidige pijpleidingen de beste optie. “Momenteel gaat er aardgas door deze leidingen, maar het zal nog dertig jaar duren voordat alle leidingen geschikt zijn voor waterstof.”
Het is technisch gezien de beste optie, maar lang niet de meest toegankelijke. Er is dus een flexibele noodoplossing nodig. “LOHC is daarom een geschikte tussenoplossing voor sectoren die zo snel mogelijk moeten verduurzamen, zoals de baksteenindustrie.”
Lego-bakstenen
Duurzame bakstenen zijn één ding, maar daadwerkelijk duurzaam bouwen vraagt om een hele nieuwe oplossing. Zo kwam Dennis Deen erachter dat zijn metsel- en steigerbouwbedrijf, waarmee hij acht jaar door de bouwcrisis is gegaan, niet houdbaar meer was. Hij verzorgde de hele ruwbouw voor aannemers en had op het hoogtepunt 100 mensen in dienst.
Na de crisis ging Deen in gesprek met een business coach. Hij liep tegen diverse problemen aan, maar zag de oplossing niet. ‘Sluit jezelf op en maak een business plan’, gaf de coach als tip. Eerst was Deen nog huiverig, want ‘dat heb ik vroeger op school al gedaan’, maar uiteindelijk gaf hij er gehoor aan. Hij liet alles wat hij wist over metselen en bouwen los en begon te brainstormen.
Leerlingen
“Al mijn problemen waren cement-gerelateerd. Met koud weer kan je niet metselen, maar ook tijdens onwerkbaar weer moet ik mijn personeel doorbetalen. Nieuw personeel is ook bijna onvindbaar. We hebben slechts 6500 metselaars in Nederland, terwijl dat er in 1990 nog 26.000 waren. De opleiding duurt ook drie jaar. Ik heb in acht jaar tijd slechts twee leerlingen opgeleid.”
“Ik dacht toen bij mezelf: als ik nou een toverstokje zou hebben, wat zou ik dan willen? Ik heb alle kennis losgelaten en ben vanuit het volgende gaan denken: iedere fabrikant doet mee, het is een opleiding van maximaal een week en het moet voor de architect heel simpel mee te werken zijn in de huidige bouw.” Kort daarna verkocht Deen zijn eigen bedrijf. Na vele slapeloze nachten, ontelbare veiligheidstesten en de investering van een paar miljoen eigen vermogen werd het stapelsysteem Drystack geboren.
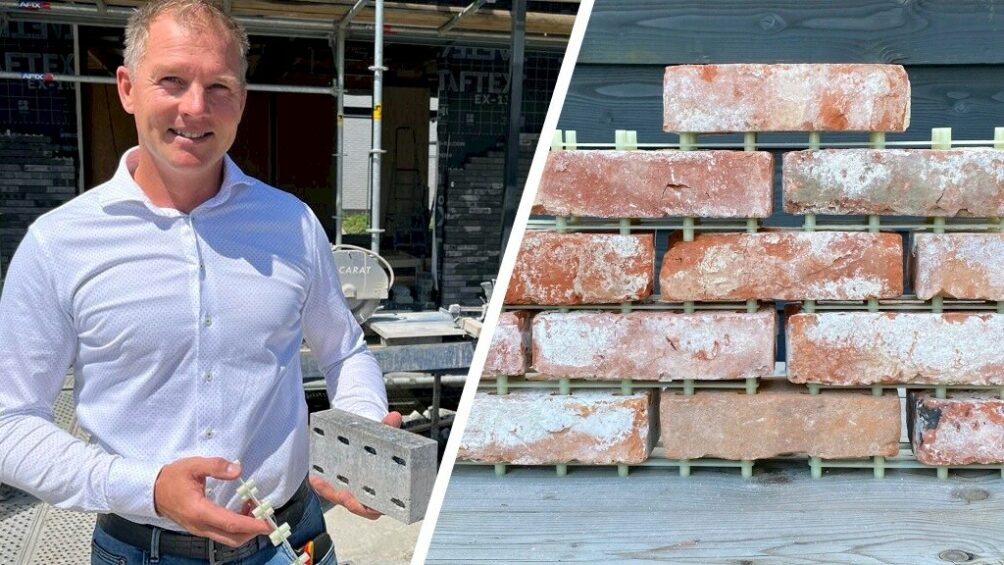
Met Drystack is het mogelijk om zonder cement te bouwen. In de bakstenen worden heel nauwkeurig gaten geboord, zodat ze aan een koppelstuk (de Layer) bevestigd kunnen worden. Zo kunnen hele rijen bakstenen als lego-stenen op elkaar gestapeld worden. Niet alleen gaat het bouwen zo veel sneller, het is ook nog eens duurzaam.
“De techniek die wij toepassen bestaat nergens in de wereld. Architecten kunnen er heel simpel mee werken. Alles wat je met metselwerk kan maken, is ook mogelijk met Drystack.” Naast dat er geen cement meer nodig is, kunnen de bakstenen ook makkelijk hergebruikt worden. “Als je bakstenen verlijmt of metselt, weet je zeker dat die uiteindelijk, na circa vijftig jaar, onder het asfalt verdwijnen. Met Drystack kun je bakstenen, die een levenscyclus van duizend jaar hebben, gewoon hergebruiken. Zo valt alles op z’n plek. Het pas helemaal in het circulaire plaatje.”
Nieuw vakgebied
Deen heeft niet alleen een innovatieve techniek bedacht. Hij heeft een heel nieuw vakgebied ontwikkeld: de stapelaar mét bijbehorende opleidingen. Daarmee heeft hij in een klap ook een oplossing voor een groeiend tekort aan metselaars. “We hebben nu drie opleidingen die ieder een week duren. Je hebt basisstapelaar, assistent stapelbaar en teamleider. Ik wil dat Drystack uiteindelijk de standaard wordt voor baksteenverwerking wereldwijd. Die doelstelling durfde ik nooit uit te spreken, maar we hebben nu een mooi team, grote investeerders uit de bouwindustrie achter ons staan en al zes baksteenfabrikanten die op onze machines staan te wachten. We kunnen nu echt door!”
Voor ieder interieur
Wie een duurzaam huis wil bouwen, moet natuurlijk ook op zijn of haar interieur letten. Daar hebben onderzoekers van de Royal Institute of Technology (KTH) in Stockholm iets op gevonden. Zij hebben een bio-plastic ontwikkelt op basis van hout. De onderzoekers hopen dat dit nieuwe materiaal het huidige, schadelijke plastic, dat gebruikt wordt in interieurs en constructiematerialen, kan vervangen. Het meest opmerkelijke aan dit materiaal is dat de stof zeer hard is. Dat komt door het hoge gehalte aan vezels die erin zitten. Een unicum, want niemand was er tot nu toe in geslaagd om zo’n sterk bio-plastic te ontwikkelen. Daarnaast is het natuurlijke plastic ook eenvoudig biologisch afbreekbaar.
Circulariteit
“Afbreekbaarheid zorgt voor circulariteit”, vertelt Peter Olsén, een van de onderzoekers. “Aan het einde van de levenscyclus kunnen we het plastic oplossen met water waardoor we alle grondstoffen weer hebben om het plastic opnieuw te maken.”
Toch heeft de biologische afbreekbare eigenschap van het plastic ook een keerzijde. “We kunnen geen buitenpanelen maken van afbreekbaar plastic, want het is niet bestand tegen langdurige blootstelling aan het weer. Meubels zijn er wel geschikt voor. Het is ook heel makkelijk om ze in te zamelen en circulair te hergebruiken.”
Eindeloos
De nieuwe bio-plastic moet dus nog wel geoptimaliseerd worden, voordat het grootschalig kan worden ingezet. “Zodra we de afbreekbaarheid van het plastic kunnen aanpassen, opent dat de deuren voor toepassingen buitenshuis. Bijvoorbeeld door het plastic zo te ontwikkelen dat het alleen afbreekt met een chemische oplossing en niet in het milieu.”
Olsén heeft daar alle vertrouwen in: “We staan nu op het punt waar we moeten gaan nadenken over hoe we onze materialen ontwerpen. Hoeveel cycli mag het materiaal meegaan? Moeten we het ontwerpen voor langdurig en duurzaam gebruik of juist kort en circulair? De mogelijkheden zijn eindeloos.”
