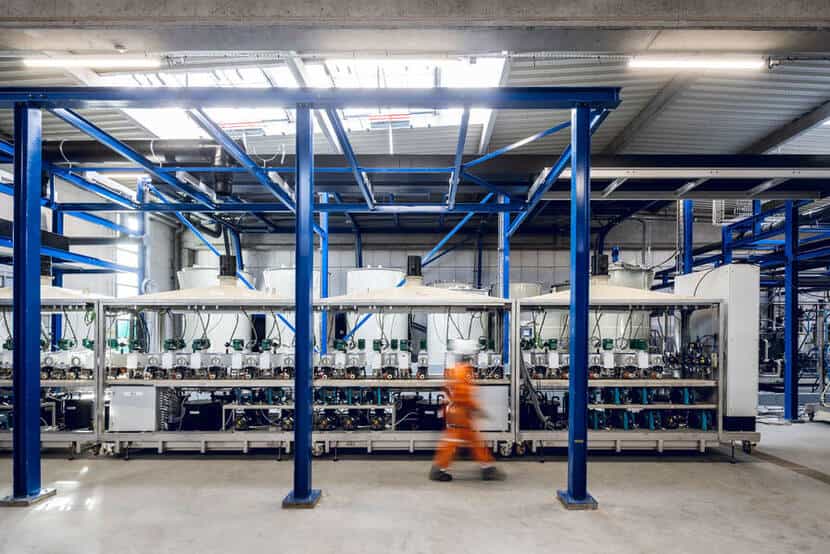
De mijnbouwgroep Eramet heeft 10 miljoen euro geïnvesteerd in zijn R&D-centrum in Trappes (Yvelines) om zijn innovatieve proces voor het terugwinnen van metalen uit afgedankte batterijen te industrialiseren. Het doel is om in de pilotfabriek 250 kg lithium en kobalt en 1000 kg nikkel te produceren. Maar er blijven vragen over het business model voor de toekomstige fabriek in Duinkerken.
- ERAMET start proeffabriek in Trappes als voorbereiding op grotere fabriek in Duinkerken;
- De focus ligt op het terugwinnen van 250 kg lithium, 250 kg kobalt, en 1 ton nikkel per jaar;
- Autofabrikanten moeten aan Europese quota voor gerecycled metaal voldoen;
- Er heerst nog onzekerheid over het businessmodel.
Roze kobaltsulfaatpoeder, groene nikkelsulfaatkorrels en wit lithiumpoeder
Roze kobaltsulfaatpoeder, groene nikkelsulfaatkorrels en wit lithiumoeder: dit is wat er binnenkort uit de proeffabriek van Eramet moet komen voor het recyclen van batterijen van elektrische voertuigen. De 800 m² grote fabriek, die op 14 november werd geopend is gevestigd in het R&D-centrum van de mijnbouwgroep in Trappes (Yvelines) maar de productie is er nog niet gestart. Het is een cruciale stap voor de groep, die een plaats wil veroveren op de fel begeerde markt voor kritieke metalen in elektrische batterijen. Eramet heeft plannen voor twee recyclingfabrieken in Duinkerken.
Quota’s voor gerecycled materiaal
De Europese regelgeving legt autofabrikanten quota’s op voor het gebruik van gerecycled metaal. Ontmanteling en hergebruik van batterijen aan het einde van hun levensduur lijkt steeds belangrijker en onvermijdelijk te worden. “De mijn van de toekomst is de secundaire mijn”, aldus Christel Bories, CEO van Eramet.
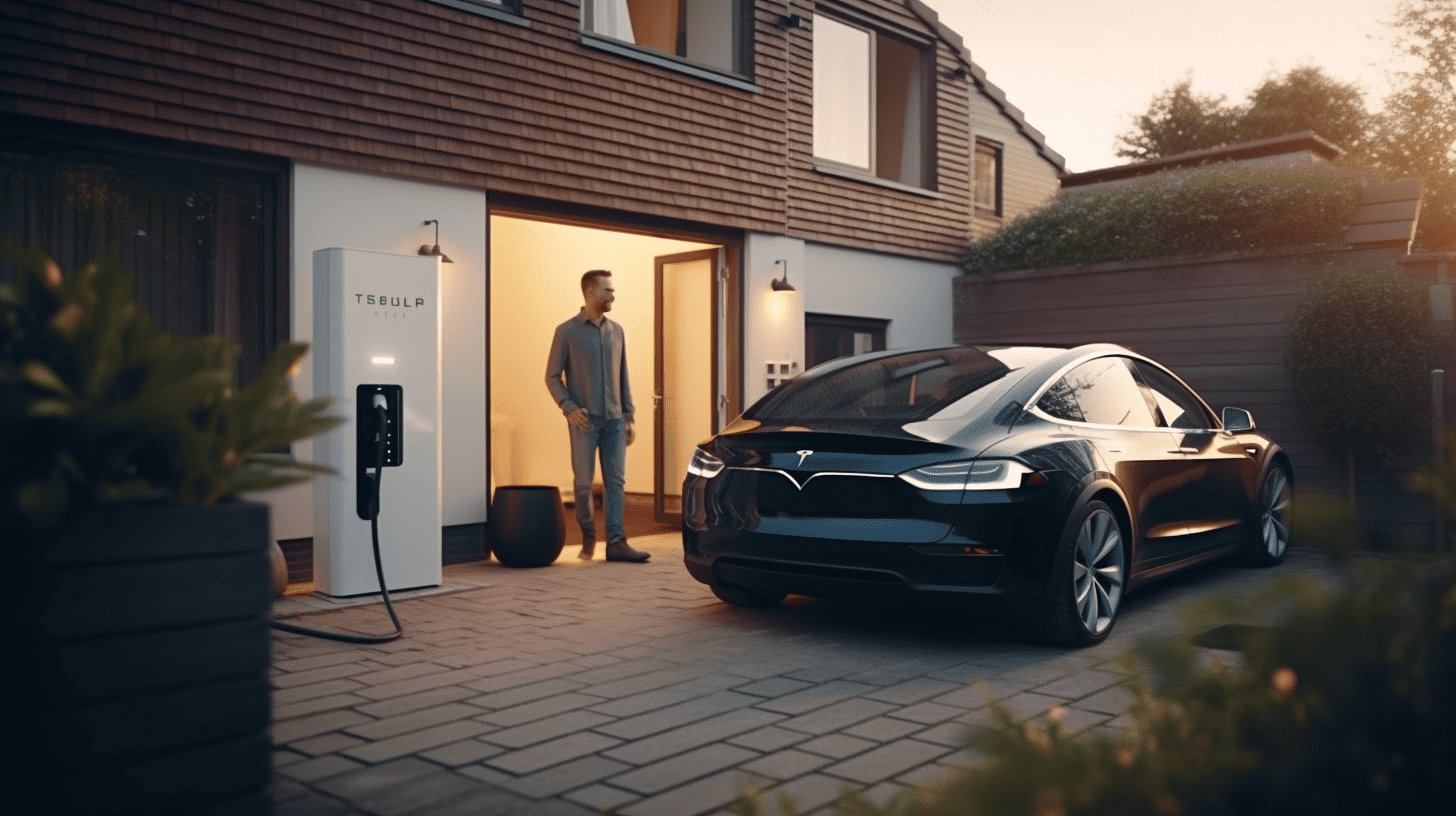
Plannen voor een mega fabriek, 1000 keer groter
Europa telt steeds meer recyclingprojecten. Eramet van zijn kant werkt sinds 2019 samen met de Suez-groep aan dit onderwerp. Suez is verantwoordelijk voor de productie van de zwarte massa, de eerste fase van de recycling, waarbij de batterijcellen worden vermalen tot een zeer fijn zwart poeder nadat de belangrijkste plastic, aluminium en elektrische kabelcomponenten zijn verwijderd.
Eramet is betrokken bij het tweede deel van het proces: de hydrometallurgische terugwinning van kobalt, nikkel en lithium die in de zwarte massa zijn samengesmolten. De kwaliteit en zuiverheidsgraad zijn hoog genoeg om ze opnieuw te gebruiken in nieuwe batterijen.
Deze tweede fase moet op industriële schaal worden uitgevoerd in de proeffabriek in Trappes, waarin ERAMET tien miljoen euro heeft geïnvesteerd, waarvan twee miljoen euro subsidies. Met een capaciteit van 5 ton blackmass is de site bedoeld als een schaalmodel van de toekomstige fabriek die de groep in Duinkerken wil bouwen. Verwacht wordt dat de pilotfabriek 250 kg lithium, dezelfde hoeveelheid kobalt en een ton nikkel per jaar gaat produceren.
Batterijkwaliteit
Om dit te bereiken moet de zwarte massa eerst worden gezuiverd en ontdaan van koper-, aluminium- en ijzerresten, gevolgd door grafiet. “Dit is waar wij het verschil maken. Het is de belangrijkste fase in het bereiken van batterijkwaliteit”, benadrukt Frédéric Martin, hoofd van het recyclingproject bij Eramet, dat twee patenten heeft aangevraagd voor zijn proces.
Een nog te definiëren business model
De proeffabriek zal worden gebruikt om het rendement van het proces te valideren, dat een metaalterugwinning van meer dan negentig procent zou moeten halen. Ook dient het waterverbruik van de toekomstige fabriek bepaald te worden. Het bij wijze van proef geproduceerde lithium, kobalt en nikkel zal naar autofabrikanten en batterijfabrikanten worden gestuurd om te controleren of het aan hun verwachtingen voldoet en om het verkregen materiaal te laten valideren.
Maar er speelt nog een andere factor mee. Christel Bories wil ervoor zorgen dat het recyclen van batterijen rendabel wordt. “We moeten het businessmodel beter begrijpen,” zegt de CEO van Eramet. Er zijn nog gesprekken gaande met autofabrikanten.
De hamvraag is tegen welke prijs fabrikanten en gigafabrieken hun productieschroot zullen verkopen. Celschroot, dat tien tot dertig procent van de productie van een gigafabriek uitmaakt, zal in de eerste jaren waarschijnlijk de belangrijkste bevoorradingsbron voor de recyclagefabriek zijn, hoewel de recycling van afgedankte batterijen ook langzaam op gang komt.
Tweede fabriek: blackmass productie
De beslissing van de twee partners, Suez en Eramet, om een tweede fabriek te bouwen in Duinkerken voor de productie van zwarte massa zal daarentegen waarschijnlijk eerder komen en staat minder ter discussie. Het project, waarin Suez naar verwachting een meerderheidsbelang zal hebben, is veel minder kapitaalintensief. De investering zou begin 2024 moeten worden goedgekeurd en de productie van zwarte massa zou in 2025 van start gaan. Ook aan het bedrijfsmodel wordt minder getwijfeld. De fabriek, waar naar verwachting zo’n honderd mensen zullen werken, zal met name worden toegeleverd door de toekomstige gigafabrieken in de regio Hauts-de-France, met een capaciteit om 200.000 batterijen per jaar te verwerken. “Om veiligheidsredenen is het transport van batterijen complex en duur”, zegt Sabina Soussan, het hoofd van Suez. Recycling dichtbij de bron is daarom essentieel.
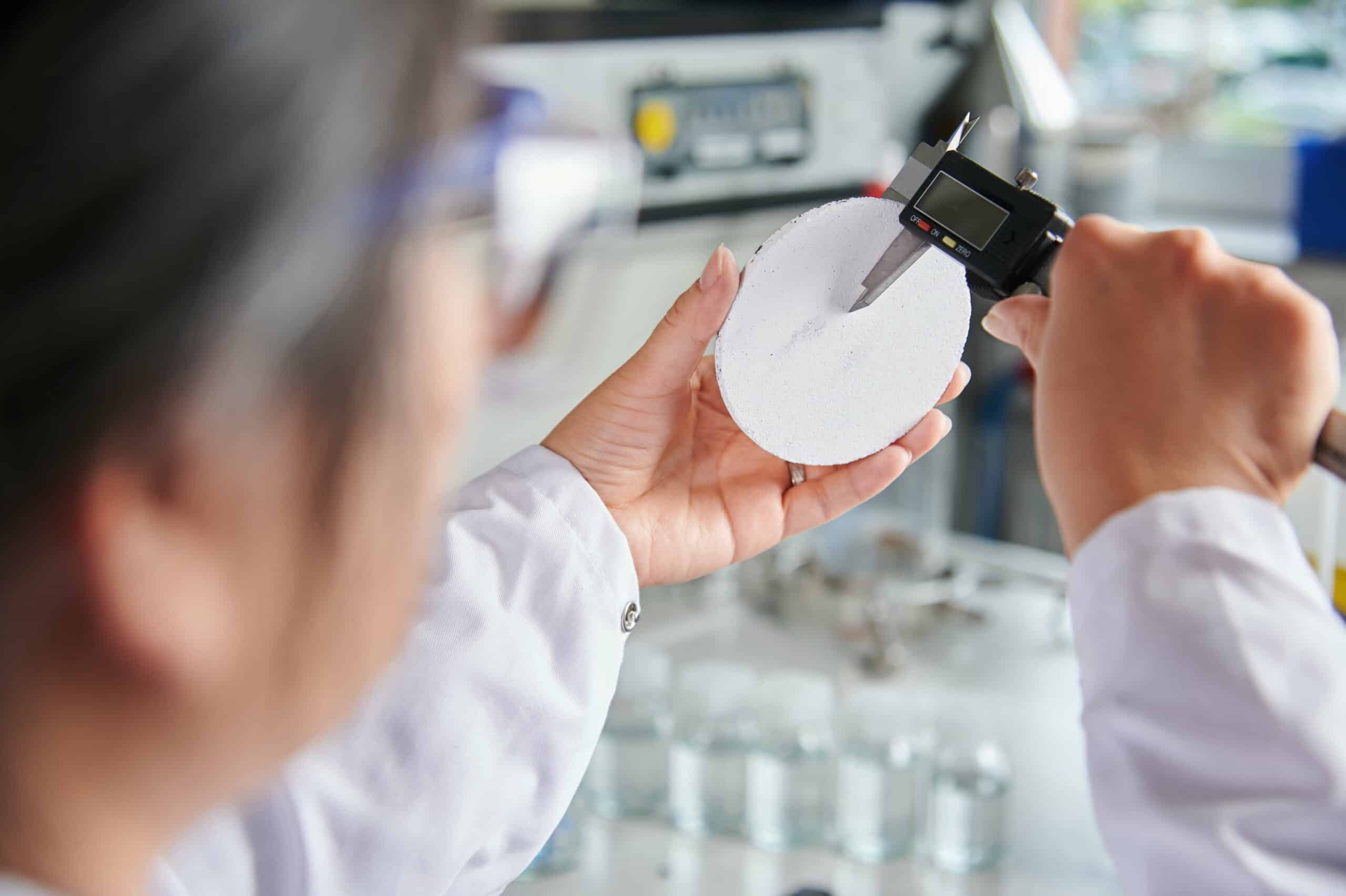