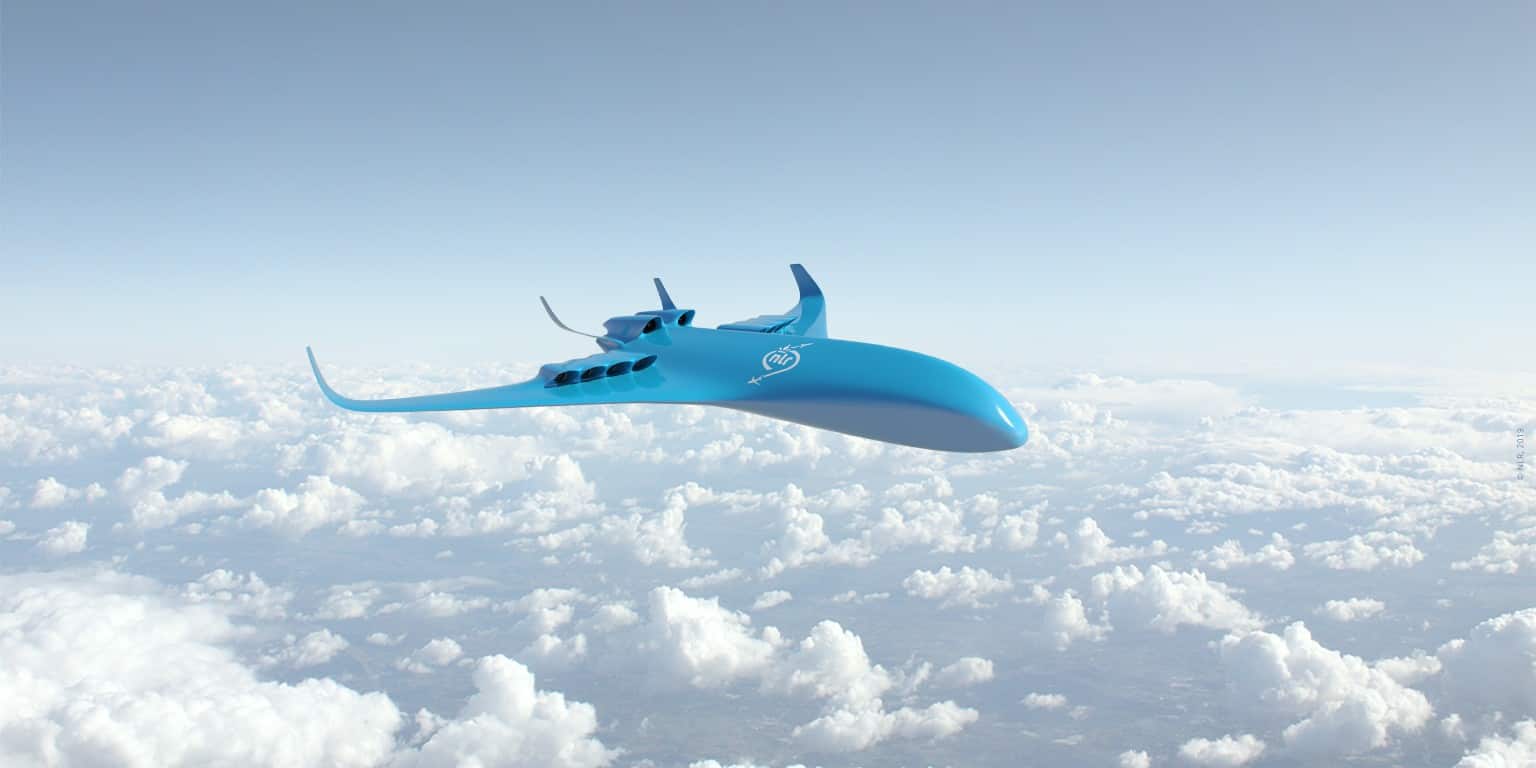
To make flying as efficient and sustainable as possible, the aviation sector is always on the lookout for ways of making aircraft as light as possible. Fatigue – the point at which a material gives way under a low but varying load – plays an important role in this. The service life of an aircraft is largely determined by the risk of failure due to fatigue. Now that advanced lightweight materials and structures are gaining ground, the topic has become more urgent than ever.
- The aerospace industry is increasingly focused on extending the life of aircraft, mainly due to the application of advanced, lightweight materials and structures;
- The ICAF 2023 conference focused on fatigue and the integrity of structural materials, focusing on new materials such as 3D-printed metals and fibre-reinforced plastics;
- Pioneering research presented a new formula for more accurate predictions of the service life of metal structures and the use of automation, digitisation and simulations to enable more efficient and sustainable maintenance.
“When it comes to the weight of an aircraft, we are by definition operating right on the limits of what is possible,” says Marcel Bos. “If a commercial plane is too heavy, it’s not efficient and it won’t be attractive in commercial terms. Using new, advanced materials lets us keep pushing the boundaries of what is permissible.” Bos is the head of the Aerospace Vehicles Integrity & Lifecycle Support department at the Netherlands Aerospace Centre.
Every two years, research institutes, universities, partners from the industry, aircraft users and regulatory authorities from seventeen countries meet up at ICAF, a leading international conference that focuses on fatigue and the integrity of material structures. Bos is the general secretary of ICAF (the International Committee on Aeronautical Fatigue and Structural Integrity) and he was also responsible for organising the 38th annual event, which was held at the end of June in Delft. “Unlike the situation seventy years ago, when the use of metal was just starting in aircraft construction, we now have a good understanding of how fatigue works. The biggest challenges now, in 2023, are in particular the advent of new, advanced materials and personnel shortages in aircraft maintenance.”
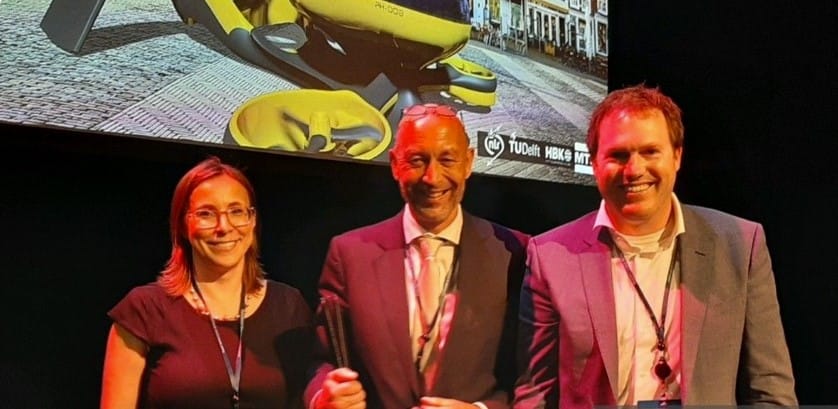
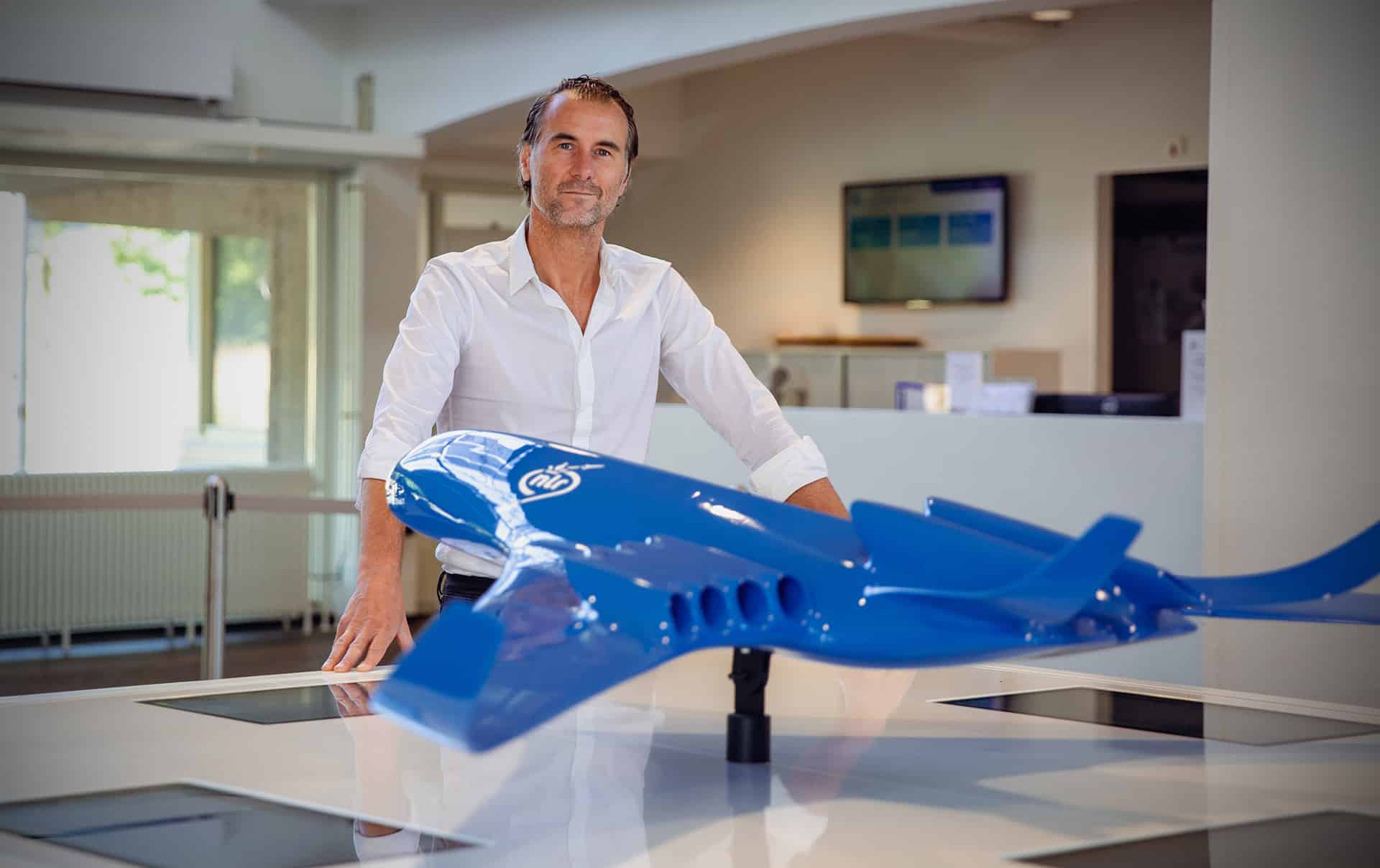
The effect of new materials on fatigue
One question that was widely discussed at the ICAF conference was how much effect new materials – such as 3D-printed metals and fibre-reinforced plastics – could have on aircraft’s lifespans. Fibre-reinforced plastics do not become fatigued as metals do under varying tensile stresses, for example, but they are affected by compressive loads. And there is a risk in the 3D printing of metals that small cavities are left in the material, which can ultimately act as the starting point for fatigue cracks.
To allow predictions to be made of exactly how metal structural components will behave, the sector still relies on Paris’ Law, a theory on crack growth dating back to the sixties. That law turned out to be insufficient in many cases. It is for instance not good at predicting the lifespan of a metal structure under fluctuating patterns of variable loads, such as those caused by turbulence in the case of aircraft.
Ground-breaking research: increasingly accurate lifespan predictions
At ICAF, Emiel Amsterdam, a senior scientist at NLR, presented the research results of the PRediction Of Fatigue in engineering alloys (PROF) project. This involved NLR working with TU Delft, Airbus, Embraer, the Royal Netherlands Air Force and others. Amsterdam, the project leader, developed a new formula that involves not only the potential elastic energy (as Paris’ Law does) but also the size of the plastic strain field. Looking at the elastic energy in a spectrum of fluctuating variable loads allows better predictions of a structure’s lifespan.
“That lets us use metal structures for longer, improving their sustainability,” says Bos. “After seventy-five years, we’re finally getting to understand properly how fatigue works. Currently, we have to carry out material tests for every spectrum, but this new theory will in future let us work out the lifespan for any random spectrum of stresses. On top of that, this knowledge will let us design materials that are more resistant to fatigue.
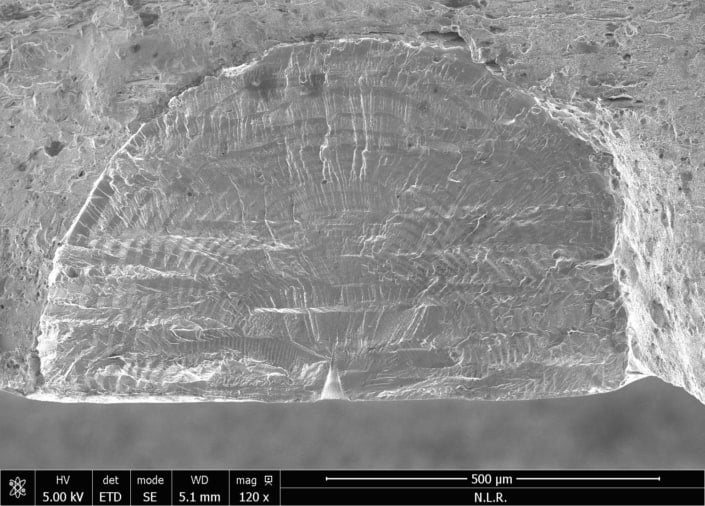
Automation and digitalisation
The answer to the shortages of aircraft maintenance staff may well lie in automation and digitalisation. One of the many examples is the use of thermography for inspecting aircraft for potential damage. When a small amount of heat is applied to the structure, an inspector with an extremely sensitive camera can see the spots where the structure responds differently: the material warms up differently at the locations where there is damage. This technology allows an aircraft to be inspected with relatively little use of staff.
“The development of fibre optics is very promising too,” says Bos. “The fibres are glued into the plane at various critical structural elements. Special reading equipment then lets you see what the forces and deformations are at those points. That will soon let us monitor the health of an aircraft much better and make predictions.”
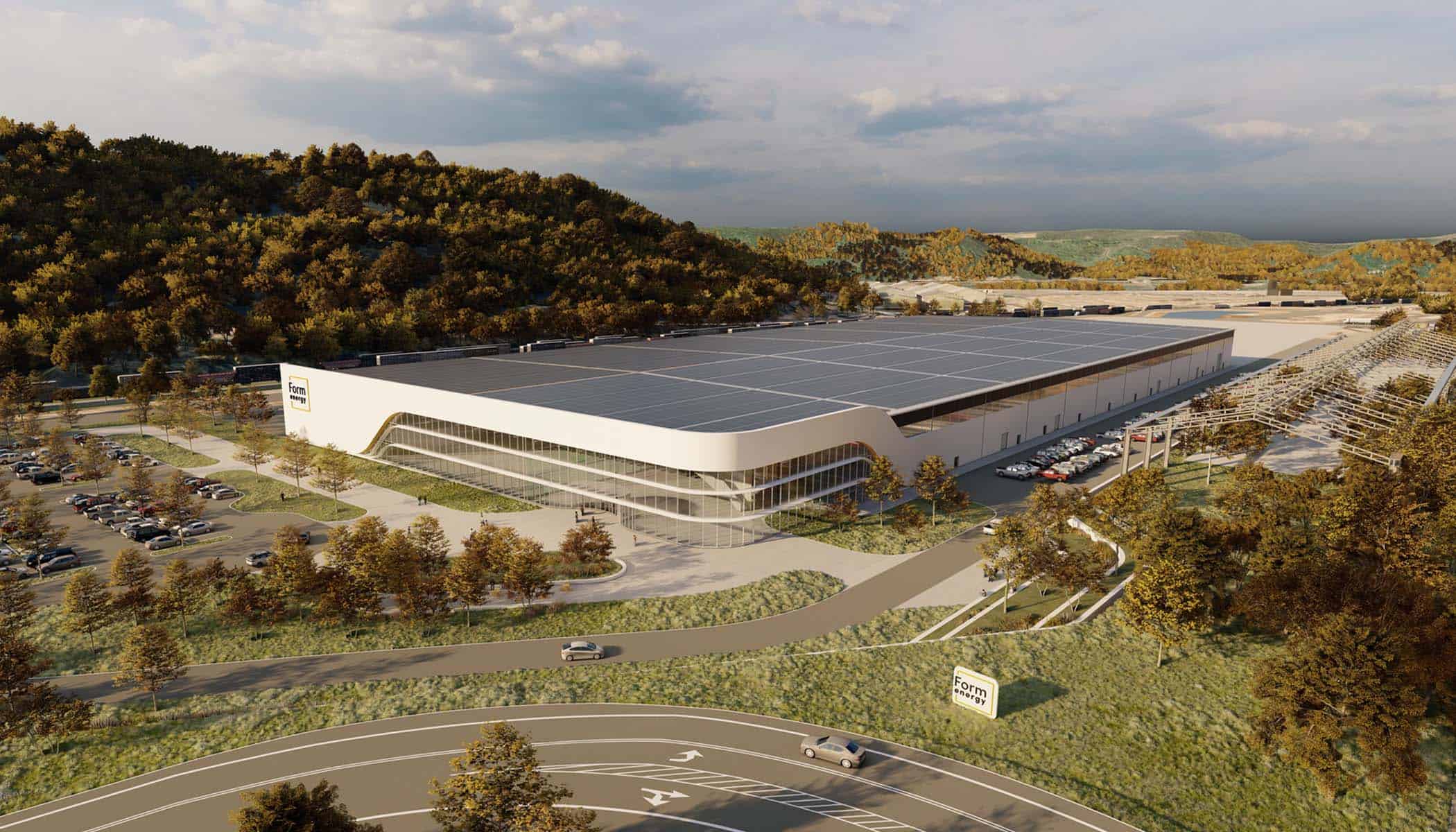
From pen and paper to digital engineering and virtual testing
In areas where inspection data is still logged using pen and paper, digital engineering is also going to make a major difference. Using all the data that is gathered by sensors, algorithms will be able to make very accurate predictions. Bos also has high expectations of the flow of data between aircraft users and aircraft manufacturers.
“If they give each other details of how aircraft are being used and the effect that has on the maintenance, it’s a real benefit. If your helicopter never does more than simple sightseeing trips, it’s completely different to it having to land regularly on the deck of a pitching and rolling ship. Because digitalisation is letting us get all that information onto the table, we can take the conditions into account much better when developing and producing an aircraft.”
Simulations – also referred to as ‘virtual testing’ – were another subject that was widely discussed in Delft. Using advanced computer models, the structure of an aircraft becomes just one part of the aircraft as a complete system. Where the material itself was studied in the past, simulations now can for instance also include how much heat the engines and onboard systems emit and the way that affects the structure. “Bringing all those systems together for the testing certainly makes for some complex tests,” says Bos, “but the results are much more complete.”
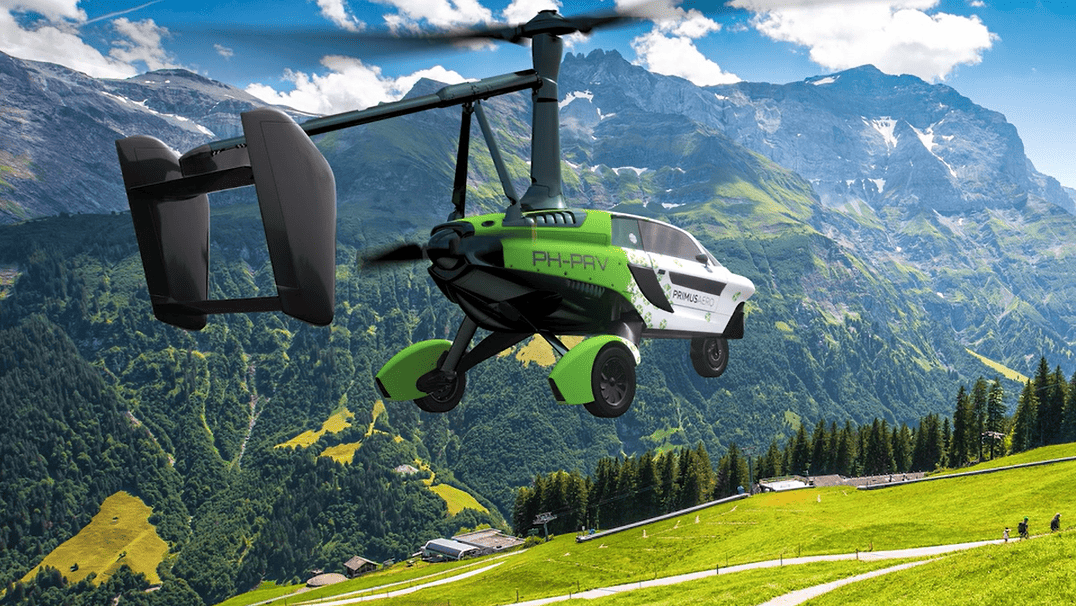
A driver for sustainable aviation
And don’t forget the transition from fossil fuels to climate-neutral drive systems, of course. That also has a major effect on the safety of a structure because it can be associated with very different stresses. “Take hydrogen. That’s still liquid at –253°C, but metals are much more susceptible to damage at those temperatures. And in general, environmental conditions such as temperature and humidity – not to mention the presence of hydrogen – can affect fatigue. Research is needed to see how much influence the temperature and the hydrogen actually have.”
Ligeia Paletti, an R&D engineer and management consultant for the circular economy, sustainability and innovation at NLR, gave a paper at ICAF. Paletti states that there is a direct relationship between the sustainability and the structural integrity of a structure; after all, the more tolerant it is to damage, the longer the service life of an aircraft. And the lighter it is, the more efficiently (and therefore sustainably) it will fly. “The transition to becoming a climate-neutral sector is an opportunity to support other disciplines within the aerospace sector in terms of knowledge, models and technology.”
“The transition to becoming a climate-neutral sector is an opportunity to support other disciplines within the aerospace sector in terms of knowledge, models and technology.”
Marcel Bos
More efficient, faster, less labour-intensive
Ultimately, these technologies should make aircraft maintenance more efficient, faster and less labour-intensive. However, these developments are only being used to a very limited extent in practice as yet.
“Inspectors currently check a helicopter’s rotor blades by tapping them all the way along the surface with a small hammer. If they hear a dull sound, that means damage. Hugely labour-intensive, but it’s a thoroughly reliable process. Modern thermography and fibre sensors can do it much more efficiently. But it first needs to be demonstrably clear that this way is just as reliable. A lot of these new developments are currently in that phase.”
That a lot is going to change is clearly an understatement. “ICAF has been around since 1951 already. Although we’re getting to understand fatigue better, all the recent developments mean it’s just as important to think about such things now as it was seventy years ago,” says Bos in conclusion. “Our work is nowhere near done yet.”