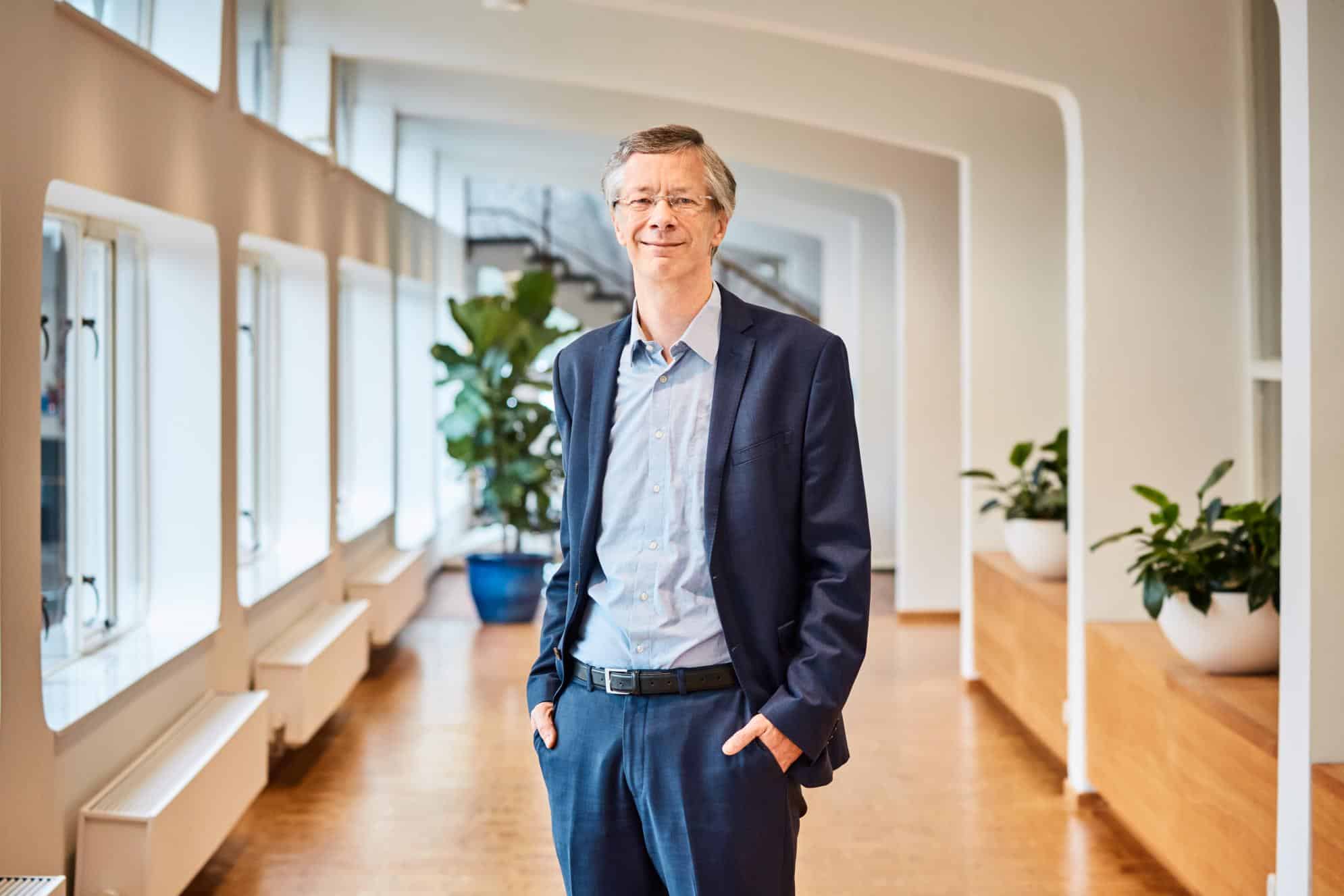
What will aerospace vehicles look like in the future? And how can we ensure these new vehicles meet social and economic needs? New research, such as the one on hydrogen-powered planes, is looking into how to make aircraft more sustainable. But there are also much less visible developments crucial to sustainable aviation development, for instance, in high-capacity wiring for electrical aircraft or lightweight thermoplastic materials.
The Netherlands Aerospace Center (NLR) plays a vital role in conducting research and turning knowledge into value. NLR does this through nine strategic programs. For the series “The Aviation of the Future,” Innovation Origins speaks with all programme leaders.
For the third episode, we spoke with Johan Kos (programme leader Development of air and space vehicles) about the impact of aviation on society and the environment.
What does the knowledge programme involve?
“Through this programme, we are helping the development of aerospace vehicles for both civil and military applications. If you look at civil aviation, there are major challenges relating to climate impact. We’re using this programme to try to help, creating lighter structures by using lighter materials, with more sustainable propulsion and the associated system innovations. It’s important for us that Dutch industry – and in due course its clients – can physically implement the solutions.”
“The good thing about working programmatically is that cooperation with other parties, such as companies, is genuinely part of the development process. We’re working towards a common goal and that leads to better results.”
About the programme leader
Johan Kos is a principal R&D engineer and the programme leader of the Aerospace Vehicle Development programme. He obtained his PhD in mathematics and first came into contact with the field of aerospace through NLR.
“I think everything that’s happening in this area is very interesting. Making aviation more sustainable while at the same time meeting global air transport needs is a major challenge for Dutch manufacturing industry.”
Could you give an example of the projects you’re working on?
“In current aircraft for short to medium distance, the fuselage is made of aluminium. We’re now investigating whether it’s possible to make the hull out of carbon fibre-reinforced thermoplastic, a composite material. This can be recycled more easily than aluminium and this new material could make the fuselage up to ten per cent lighter. The intention is that this material will be used in new Airbus aircraft.”
“We recreated part of the lower half of a hull from thermoplastic, including integrating some of the systems. One advantage of thermoplastics is that they can be joined together relatively easily by welding. You don’t need coupling pieces or components made from other materials. Part of the research therefore focuses on finding the best welding techniques. The properties of thermoplastic compounds make them suitable for modular construction: pieces of the fuselage equipped with systems and interior parts can be assembled in a factory and then joined together in the final assembly. That lets you work much more easily and efficiently because you don’t get in each other’s way at the final assembly.”
“Within the STUNNING consortium, we’re working on the lower half of the hull, up to the level of the passenger cabin floor. Several European companies are involved in this consortium, including NLR, Delft University of Technology and SAM|XL, all led by GKN Fokker. It’s part of Clean Sky 2, a European cooperative programme. The upper half of the hull has also already been made through the same programme. We’re now working on connecting the upper and lower halves.”
“Within the consortium, NLR was responsible for developing the aircraft’s skin, the outer layer that goes around the hull. The skin is only a few millimetres thick. It has to be extremely strong because it is the interface between the inside and outside air. We’ve managed to make a skin section of four by eight metres as a single piece of thermoplastic. That had never been done before. The larger the skin sections are, the fewer welds are needed – making the skin more lightweight and the production more efficient.”
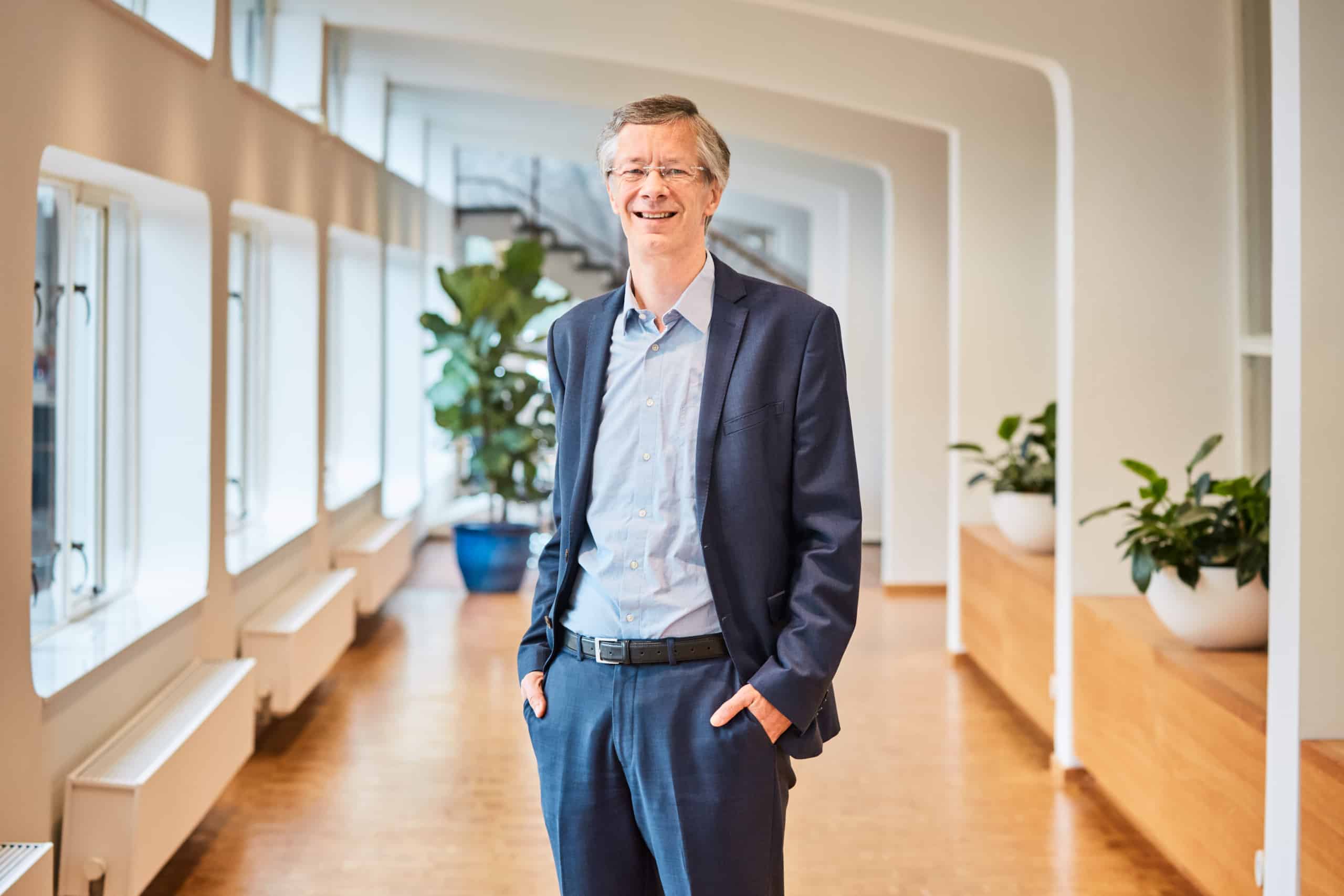
New technology
“Aircraft manufacturers want to market a new aircraft in 2035. The new technology we’re investigating now should help achieve that. It may sound a long way off but the development process is lengthy. We need to be sure of the qualities of new materials and the structures we make with them before using them in an aircraft, of course.”
“You can think of the developments in thermoplastic as the building blocks for a new aircraft. The aircraft is lighter, so it uses less fuel. Fuselages made from thermoplastics can be used both in kerosene vehicles and in aircraft with new forms of propulsion. If we start flying on hydrogen in the future, it will have consequences for the fuselage design: the fuel tanks are in the wings in many kerosene-fuelled planes, whereas the tank for liquid hydrogen in a hydrogen aircraft would probably be in the hull. We’re also investigating the possibility of making such a tank from lightweight composites. In this process, we’re developing facilities to test the materials and structures at temperatures below twenty kelvin.”
“NLR also participates in various projects within the European partnership called Clean Aviation, the successor to Clean Sky 2. There is a lot of emphasis on propulsion technology, aircraft powered by hydrogen combustion, hybrid electric concepts and improving fuel efficiency. One of the studies NLR focuses on is high-power wiring in hybrid electrical aircraft. Another is looking at the integration of fuel cells. NLR’s contribution is in temperature control of these systems, making use of experience gained in the space sector. There is also attention for the integration of components for hydrogen propulsion into the composite construction of aircraft. This also fits in with the way knowledge was built up in previous projects within the Aerospace Vehicle Development programme.”
It’s important that Dutch industry can use our research to physically implement the solutions
Johan Kos
New spacecraft
“In addition to developments related to aircraft, we’re also working in this programme on developing new spacecraft. There are various projects relating to small satellites in lower orbits. For example, we’re looking into ways of avoiding redundancy – duplication – of processors. Duplication takes more power and reduces performance, so we’re now looking into alternative components with higher reliability. NLR is developing a radiation test facility to explore which modifications are effective and which are unnecessary. These are all studies yielding results that aren’t immediately striking but could be very important for the future.”
What is the purpose of the programme?
“NLR wants to use this programme to give the Dutch aerospace industry a competitive edge in the development and production of new aerospace vehicles. Key aspects of that are efficiency (including cost-efficiency), safety and sustainability. It is about not only aircraft but also about spacecraft such as satellites. We’re also focusing on knowledge development for the Defence Department. We look at what new technologies mean for Defence. In addition to the development of the aerospace vehicles themselves, we’re also looking at regulations relating to new technology and aircraft.”
NLR as a source of inspiration
“We do a lot of research at NLR into what is and isn’t possible in the aerospace industry. It always starts at a very small scale and then expands further and further. We’ve been studying thermoplastics for more than fifteen years and now we have a large-scale prototype that aircraft manufacturers can really move forward with. This makes NLR a source of inspiration and sparring partner for aircraft manufacturers and the other parties involved.”
Changing dynamics
“We don’t build complete aircraft in the Netherlands but we do develop and supply components. The rise of new technology also creates opportunities for companies that were not previously active in aviation, which makes it more interesting. As a result, NLR also regularly has to deal with start-ups and SMEs. Working with them is very different than with a major player like Airbus. These dynamics make the work interesting and lead to good results.”