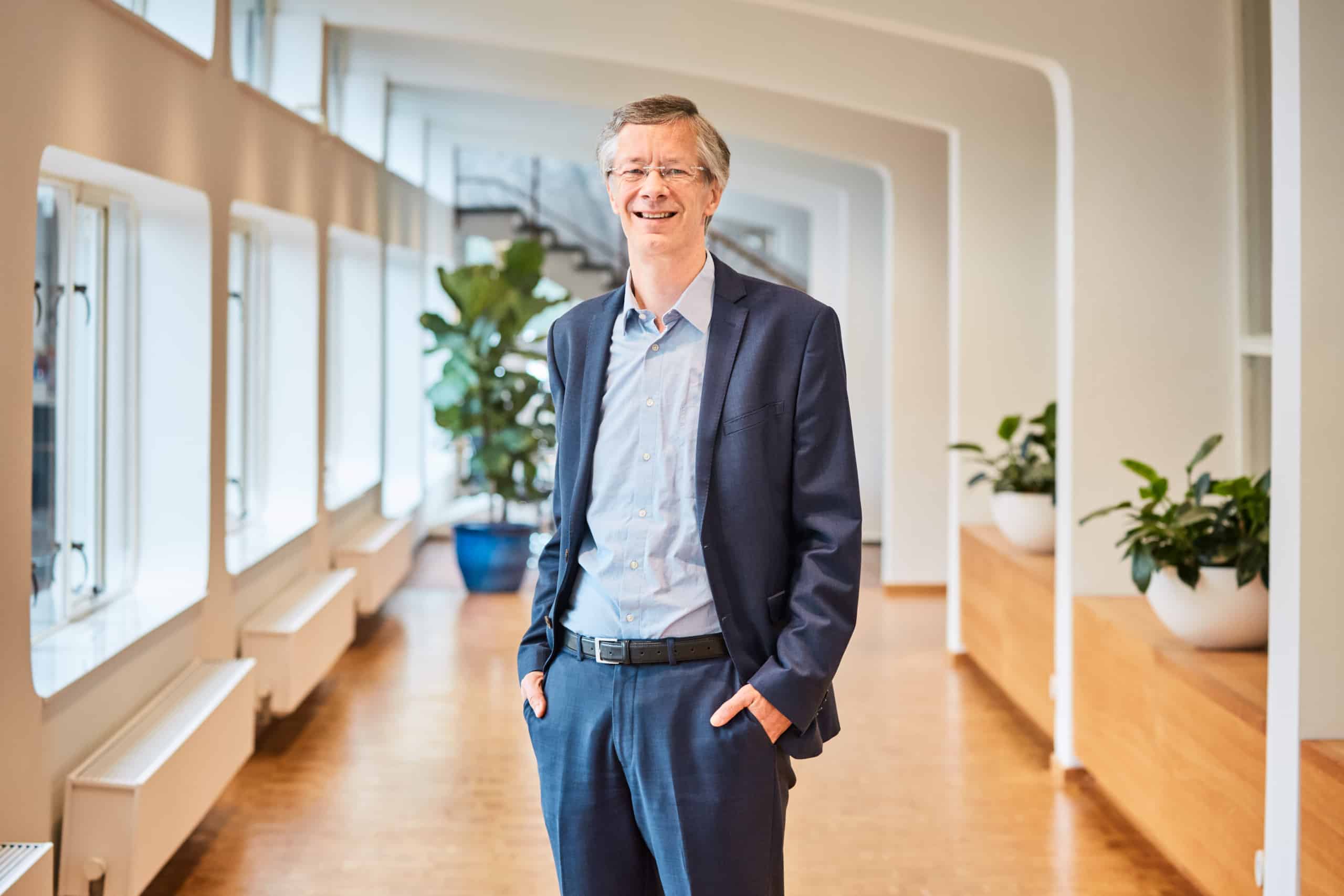
He’s a mathematician, a chess player and the father of three children: meet Johan Kos, a principal R&D engineer principal with NLR, the Netherlands Aerospace Centre. Close on thirty years ago, he made the switch from the academic world to the aerospace sector. Since then, Johan has been working behind the scenes on new technologies for making aviation more sustainable.
- Johan Kos, a senior R&D engineer at the Royal NLR, is working on sustainable aviation technologies;
- He led the TRANSCEND project, which focused on alternative aircraft fuels and propulsion methods;
- Johan believes mathematical models play a crucial role in conveying clear messages for industry and policy decisions.
One example of that is the European Clean Sky 2* project TRANSCEND, for which Johan took the initiative and had the role of project leader. The project, which NLR carried out together with TU Delft, looked at how alternative aviation fuels and new aircraft propulsion techniques – including propulsion using liquid hydrogen – could help reduce the environmental impact of aviation. The conclusion was harsh but clear: a shortage of European raw materials for sustainable aviation fuels (SAF) will inhibit green aviation in Europe from 2035 onwards. This shortage means that emissions of greenhouse gases in 2050 will only be forty per cent lower than in a scenario in which aircraft are flying solely on fossil kerosene, whereas sufficient availability of SAF could double that percentage.
Getting a clear message out there
It shows very nicely why Johan loves his work so much. “We now know that making green raw materials available has to be made a priority. Mathematical models can genuinely help create a clear message and get it out into the open, where European policymakers and companies can do something with it. That’s indispensable, particularly when several options are on the table and it’s not certain what their impacts and consequences will be – as is the case right now for sustainable aviation.”
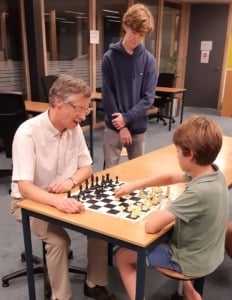
A dedicated chess coach
Thinking things through and analysing them – two crucial facets that permeate not only his work but also his hobby. In his free time, Johan is a dedicated chess aficionado and coach. He has been playing chess since he was ten and now shares his love of the game with children of all ages, who he gives coaching sessions for once a week. “I really like being able to pass on my love of the game to the next generation. It’s a target group who sometimes find it difficult to fit in with other hobbies. If they’re enthusiastic about it when they head home, I’m delighted.”
From a mathematician to an aerospace engineer
Johan’s career began as a mathematician, when he got his doctorate in 1995 from VU University Amsterdam on time-dependent problems in linear operator theory. During that period, he took a series of courses about mathematical system theory and control theory; the general field of application for modelling systems using various techniques was something that intrigued him in particular. Browsing through a newspaper, he saw a job advert from NLR and decided to apply. One thing led to another. When Johan started at NLR in 1995, he knew absolutely nothing about aviation technology. He had no idea how an aircraft was built, let alone what role research projects played. Thirty years later, that has changed; as a principal engineer, he has handled several projects – some of them international – and he finds his job getting more interesting every day.
When asked if anything ever goes wrong, his answer is clear. “All the time. When you’re doing research, you’re always feeling your way in the dark to some extent – you never know beforehand what the results are going to be. But that’s what makes our work so interesting, creating a clear understanding and getting the best results. On top of that, it’s a sector where there’s a lot of momentum. Ten years ago, I wouldn’t have thought for a moment that hydrogen was going to play such a big role. In the aviation sector, we’re working on a new revolution: flying on liquid hydrogen with fuel cells and electric propulsion, or by direct combustion. This aim is for the first aircraft to hit the major markets by 2035. I’ll be sixty-seven then, so it’d be nice if that happens before I retire.”
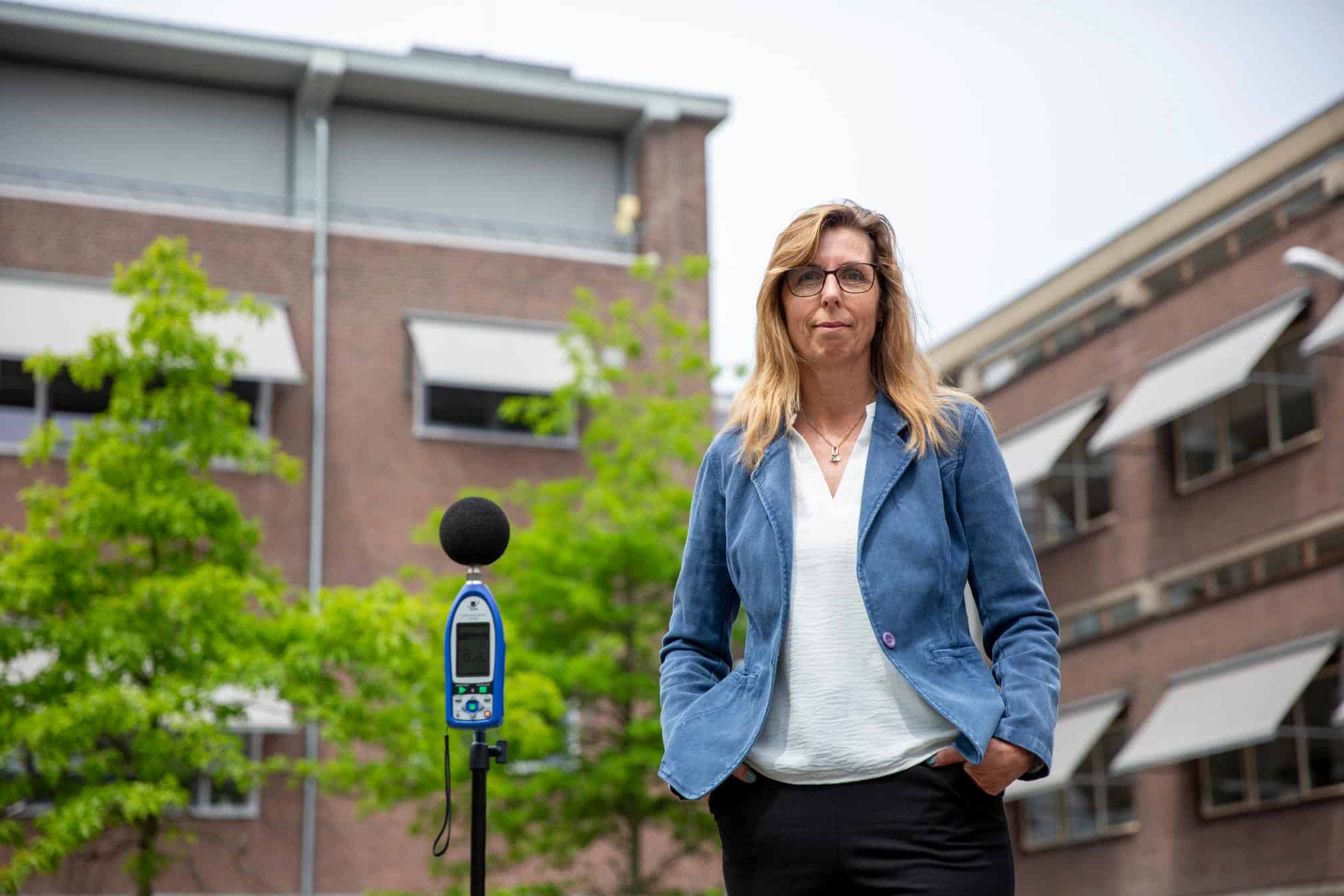
Sustainability as a priority
The efforts to hit sustainability targets mean that sharing knowledge and collaborating are indispensable. “Now more than ever,” says Johan. “Working together is the only way we’ll keep pushing the boundaries of technology.” This joint approach can be seen clearly in the STUNNING project, in which Johan is the project coordinator for NLR’s part. The consortium, which includes GKN Fokker, TU Delft and SAM|XL, is working with Airbus and numerous European partners to study the use of thermoplastic composite for constructing the fuselage of a new generation of large aircraft for short-haul and medium-range flights, targeting producing at least sixty to a hundred aircraft a month.
I work in a sector where there’s a lot of momentum. Ten years ago, I wouldn’t have thought for a moment that hydrogen was going to play such a big role.
Johan Kos
These thermoplastic composites are carbon fibre-reinforced plastics that are heated under pressure to temperatures of four hundred degrees and then cooled (consolidation) to give the products their final properties. That is a much higher process temperature than is used for thermoset composites, which are currently widely used in the fuselages of larger planes. The sector is banking on the new thermoplastics, though. “The material should provide the same strength and lifespan as aluminium, but it’s a lot lighter and that lets planes fly more sustainably and efficiently,” explains Johan. The aim is to reduce the fuselage weight by more than ten per cent. On top of that, thermoplastic parts can be welded together, which is a major plus point compared to thermoset composites that always have to be joined mechanically, which increases the production costs and adds to the weight. Furthermore, the curing of thermoset composites is an irreversible chemical process, which makes recycling awkward. That is not the case for thermoplastics, so reusing this type of material is easier.
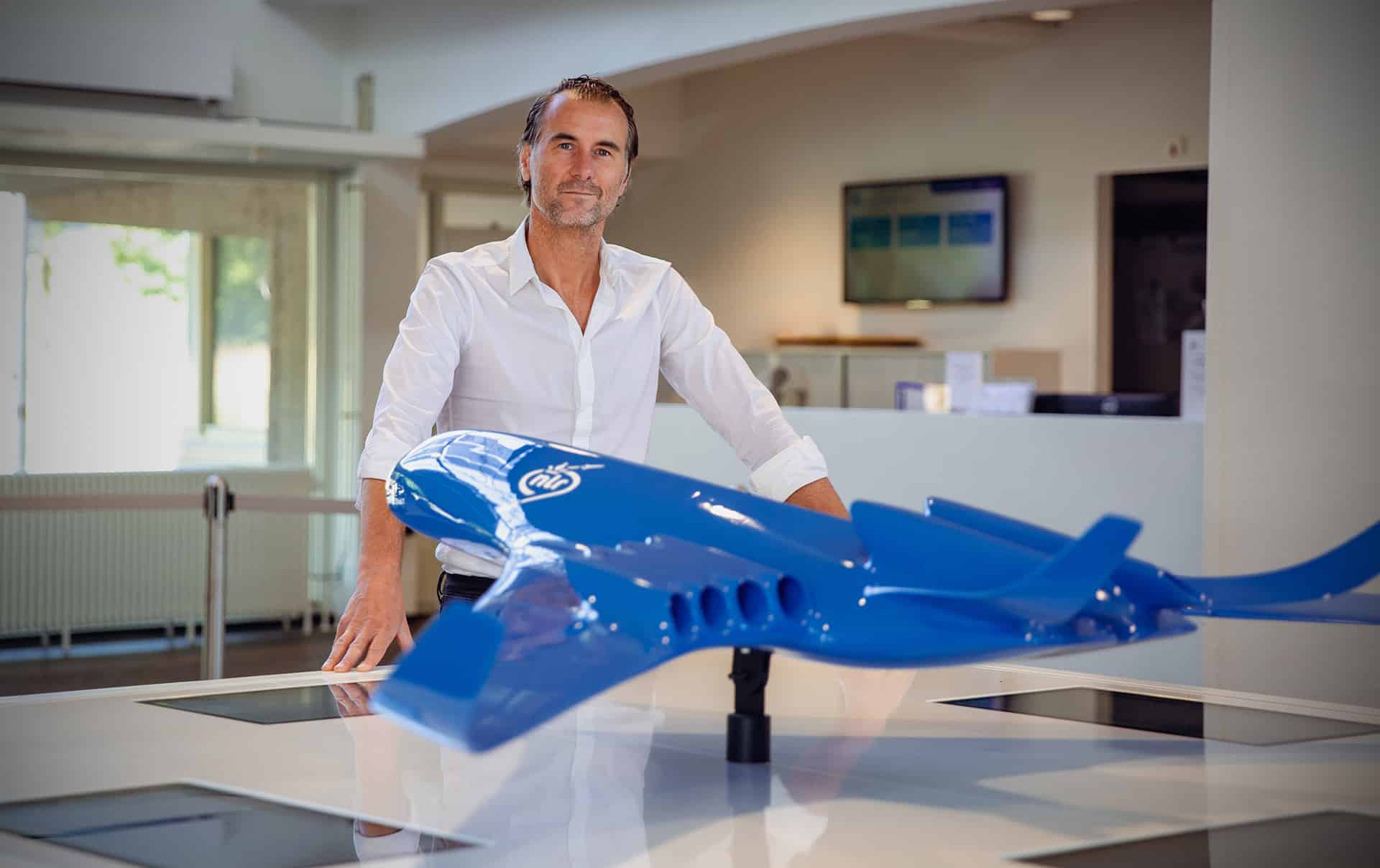
An unforgettable phone call
The cooperation resulted in a thermoplastic lower half of a fuselage eight metres in length and four metres wide – the biggest thermoplastic object ever made for aviation. NLR made the skin of the lower half as a single piece. “We started automated placement of the skin in its correct shape. It consists of layers of narrow strips of carbon fibre-reinforced thermoplastic, laid in different directions. Without our partners – DLR and the EMOTION consortium (TU Munich, Ostseestahl and Alpex) – the consolidation step would never have worked. Their innovative consolidation mould and autoclave helped us develop our knowledge further of how to make large objects from thermoplastics.”
As well as developing the large fuselage part, NLR has worked with GKN Fokker and Airbus on the technology for making, simulating and testing local reinforcement of fuselage components, welding technology based on induction heating and technology for integrating systems into the fuselage. The moment when Johan got a call from Germany (where the skin was being consolidated by NLR in an autoclave belonging to DLR) saying that they had managed to create the object is one that he won’t forget in a hurry. “It was during the coronavirus epidemic, so unfortunately I wasn’t able to be there in person. I went and had a look a week later though, with the people involved from Airbus and the EMOTION consortium.”
The complete multifunctional fuselage demonstrator is expected to be ready at the beginning of 2024, once the upper and lower halves have been welded together. “We can genuinely look forward to commercial aircraft being made using these thermoplastic structures. That’s what’s so nice about working for NLR: you’re doing research, but you really do see it applied in practice too. Our research can become the future of production.”