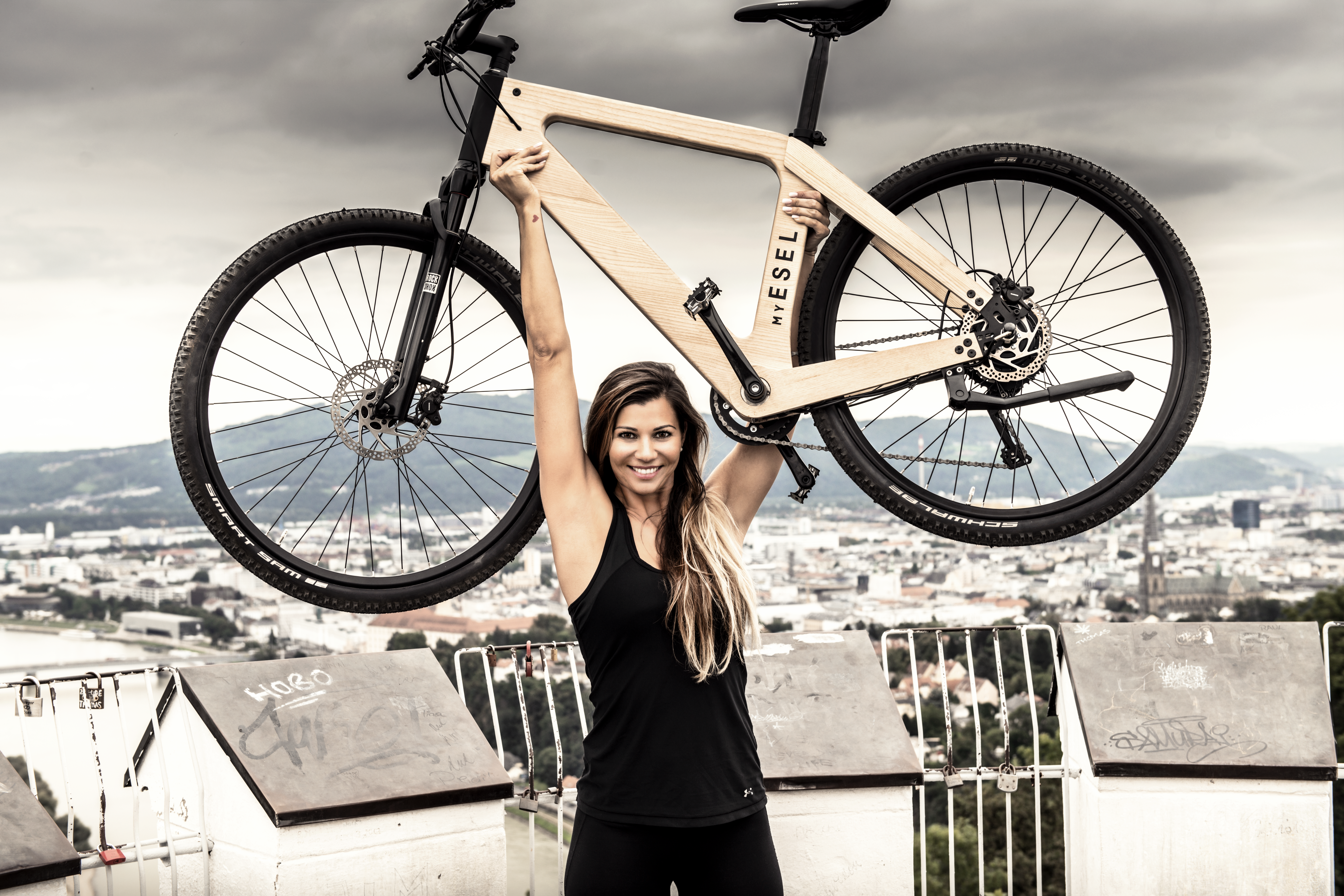
Christoph Fraundorfer bekam vom Radfahren Rückenprobleme und fand heraus, dass es an der Geometrie des Fahrrads liegt. Als Architekt und Möbeldesigner ist er es gewohnt, Probleme zu lösen. Also entwickelte er einen Prototypen – aus Holz – und schaffte es, individuell angepasste Fahrräder seriell zu produzieren; und das zu einem erschwinglichen Preis. My Esel, so der Name seines Start-ups, kam gut an und seit 2019 sind schon 400 Fahrräder aus seiner Produktion auf der Straße.
Christoph Fraundorfer im Interview:
Wie ist die Idee zu My Esel entstanden?
Ich bin eigentlich Linzer und habe während meiner Studienzeit zehn Jahre in Wien gelebt. Radfahren war die effizienteste Mobilitätsform in der Stadt. Aber, obwohl ich eigentlich sportlich bin, habe ich davon Rückenprobleme bekommen. Radfahren soll ja eigentlich gesund sein. Allerdings nur, wenn die Geometrie stimmt und der kinematische, biometrische Ablauf eine optimierte Kraftübertragung ermöglicht.
(Anmerkung: Biometrie ist die Anwendung mathematischer Methoden zur zahlenmäßigen Erfassung, Planung und Auswertung von Experimenten zum Beispiel die Körpermessung betreffend.)
Ich habe beobachtet, wie Andere auf dem Fahrrad sitzen und festgestellt, dass wenige eine ideale Position haben.
Welches Problem löst du mit My Esel und warum ist das wichtig?
Das Fahrrad verkörpert für mich nachhaltige Mobilität und ich habe es immer schon mögen, wenn ein Design intelligent war. Die Intelligenz von My Esel liegt in der individuellen Anpassung an die Körpermaße des Kunden. Die Maßfertigung ermöglicht das bestmögliche Fahrrad.
Unser Fahrrad soll die individuelle Anpassung mit Serienanfertigung kombinieren und trotzdem erschwinglich sein. Mit Holzverbundplatten, aus denen wir mit CNC (computer numeric control) die Rahmenform ausfräsen, wird dies möglich.
Holz ist ein ungewöhnliches Material für ein Fahrrad?
Das scheint auf den ersten Blick so. Die ersten Fahrräder waren auch aus Holz – genauso wie Flugzeuge. Erst seit der industriellen Revolution wurde Holz weitgehend von Stahl und Alu ersetzt, weil das die Serienproduktion günstiger machte. In der Skiproduktion wird bis heute Holz eingesetzt. Jeder Ski hat einen Holzkern, der ihn gleichzeitig steif und robust macht – und Vibrationen und Stöße besser als andere Materialien absorbiert. Ein Effekt, den wir auch bei My Esel nutzen.
Wir haben es geschafft, den Holzrahmen wirtschaftlich herzustellen. Mit CNC ist die Fertigung stärker automatisierbar und dadurch kostengünstiger. Außerdem ermöglicht die Technologie die Produktion vor Ort. Wir stehen im Wettbewerb mit der Asienproduktion und sind preislich konkurrenzfähig. Unser E-Bike kostet 3490 Euro und das ist die Einstiegspreislage bei Premium-E-Bikes. Aber wir haben lokale Wertschöpfung und verursachen geringere CO2-Emissionen, als diese beim Transport aus Asienproduktion entstehen.
Was war das größte Hindernis, das du überwinden musstest?
Es war schwer, die 2 ½ Jahre bis zur Serientauglichkeit finanziell durchzustehen.
Wir haben eine biometrische Software entwickelt, die einer ISO-Zertifizierung bedurfte. Um sicherzustellen, dass wir die richtigen Körperdaten einsetzen, haben wir mit den Experten im Orthopädischen Spital Speising zusammengearbeitet und tausende Daten ausgewertet. Heute kann jeder in wenigen Minuten sein optimales Fahrrad konfigurieren – und das online. Es sind nur drei Daten einzugeben – Körpergröße, Schuhgröße und die Länge des Unterschenkels. Für den durchschnittlichen Radfahrer reicht das. Es soll einfach bleiben, damit es keine Messfehler und Unsicherheiten seitens des Kunden gibt. Das hat es in der Art noch nicht gegeben.
Auch der Holzrahmen war eine Herausforderung – nicht nur technisch, sondern auch wirtschaftlich. Aber My Esel ist durch die nachhaltige und regionale Herstellung gut angekommen und wir haben einige Förderungen bekommen. Mittlerweile finanzieren wir uns aber rein über den Verkauf.

Foto: Mit My Esel Rennrad I konnte 2019 erstmals ein Holzrad eine Bronzemedaille bei der WUCA 24 h Europameisterschaft erreichen.
Was waren die bisher schönsten Momente?
Wenn die ersten Prototypen da stehen, wird alles real, was man sich in zwei Jahren ausgedacht hat. Es ist das Gefühl dass man es geschafft hat. Auch glückliche My Esel-Kunden machen mich froh und zeigen mir, dass ich Unterstützer habe.
Wie schwer war es, eine Finanzierung für My Esel zu bekommen?
Wir haben das Kapital 2018 erhöht – mit vier Partnern, die smart money einbrachten und wissen, wie man eine große Produktion aufbaut. Sie haben My Esel als Kunden kennengelernt und hegen eine Leidenschaft für das Produkt.
Was wollt ihr im kommenden Jahr schaffen?
Wir werden im Frühjahr ein GPS-System lancieren und werden die erste Marke sein, die einen GPS-Tracker im Fahrradrahmen verbaut hat. Das GPS-Signal geht durch Holz durch – bei Alu und Carbon ist dies nicht der Fall. Dadurch ist My Esel im Falle eines Diebstahls ortbar und kann von der Polizei zurückgeholt werden.
Was macht dein Fahrrad besser/anders als existierende Dinge?
Es gibt nichts Vergleichbares. Die Produktion ist regional und dadurch nachhaltig und fair. Das Holz dämpft bei gleicher Steifigkeit besser – und wir fertigen nach Maß. Das bringt mehr Fahrspaß und man muss nicht so stark treten.
Danke für das Gespräch.
Hier finden Sie den Link zum My Esel Video
Sie interessieren sich für Start-ups? Lesen Sie hier alle Artikel aus unserer Serie: