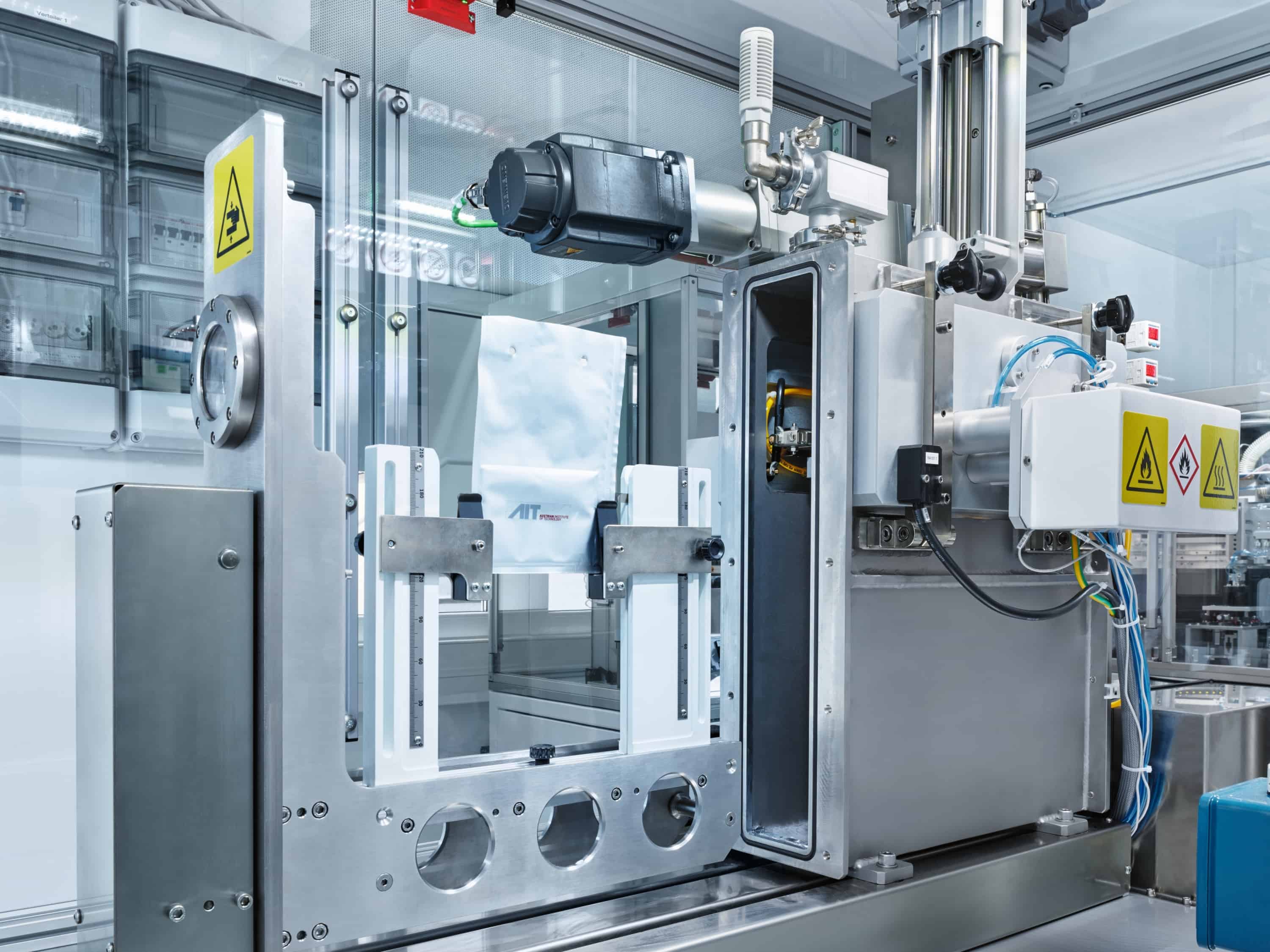
Elektrofahrzeuge sind wesentlich energie-effizienter als Fahrzeuge mit Verbrennermotoren. Trotzdem gibt es noch etwas, das uns von einer klimaverträglichen Zukunft des Verkehrssektors trennt: Die Fertigung der Kathoden für Batteriezellen, mit denen E-Fahrzeuge betrieben werden, ist enorm energie-intensiv. Zudem sind toxische Lösungsmittel in deren Herstellung involviert. Im Projekt BatWoMan will sich ein europäisches Forschungskonsortium dieser Herausforderung jetzt stellen. Beteiligt sind das AIT Austrian Institute of Technology, das Karlsruher Institut für Technologie, Fundació CIDETEC, Matthews International, die Universität Duisburg-Essen und die RISE Research Institutes of Sweden. Ziel ist es, eine nachhaltige Zellproduktionsprozesskette zu entwickeln und mit namhaften Industriepartnern zur Marktreife zu bringen.
Die Projektkoordination obliegt Katja Fröhlich vom AIT Austrian Institute of Technology in Wien, wo sie das Forschungsfeld Sustainable and Smart Battery Manufacturing leitet. Im Interview mit Innovation Origins spricht sie über die Herausforderungen.
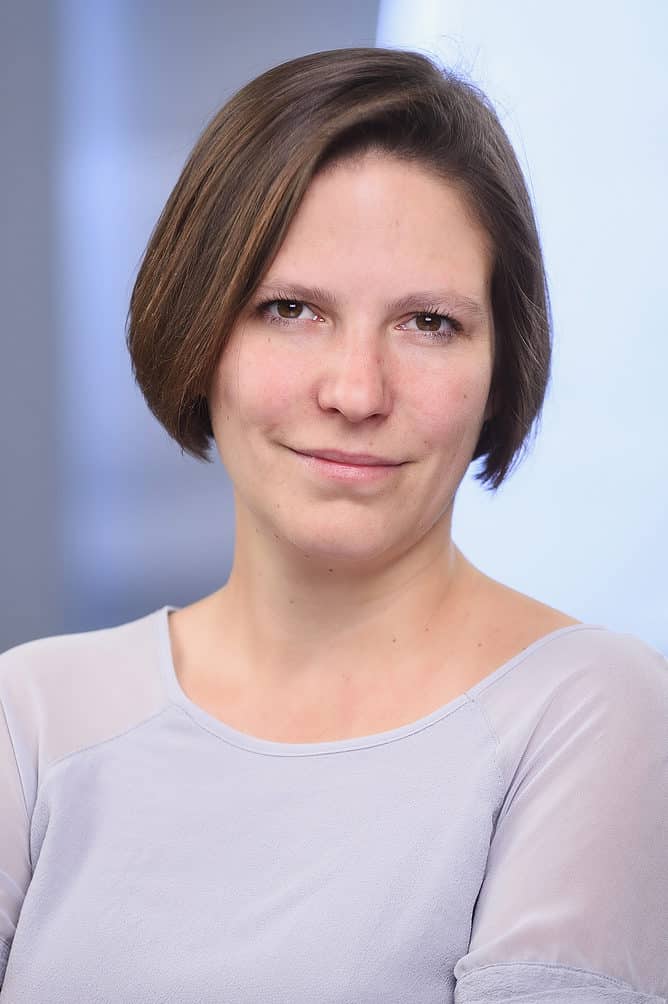
Was ist problematisch an gängigen Produktionsprozessen?
Momentan findet die gesamte Zellassemblierung in einer geschützten Atmosphäre statt – dabei müssen unter anderem Temperatur und Feuchtegehalt der Luft konstant gehalten werden. Das ist enorm energieaufwändig. Schon in unserem vergleichsweise kleinen Forschungsraum werden dabei circa 7000 Kubikmeter Luft pro Stunde umgewälzt. Die Trocknung erfolgt elektrisch oder mit Gas, um den Taupunkt von minus 40 bis 60 Grad zu halten. Außerdem braucht es zusätzlich eine Kühleinheit, um die Raumtemperatur in jeder Jahreszeit konstant zu halten.
In gängigen Fertigungsprozessen werden die Kathoden mit toxischen Lösungsmitteln verarbeitet und es sind mehrere Trocknungsschritte notwendig. Wir wollen die toxischen Lösungsmittel weitgehend mit Wasser ersetzen und den Trocknungsbedarf deutlich reduzieren. Das ist es, was wir in dem Projekt machen.
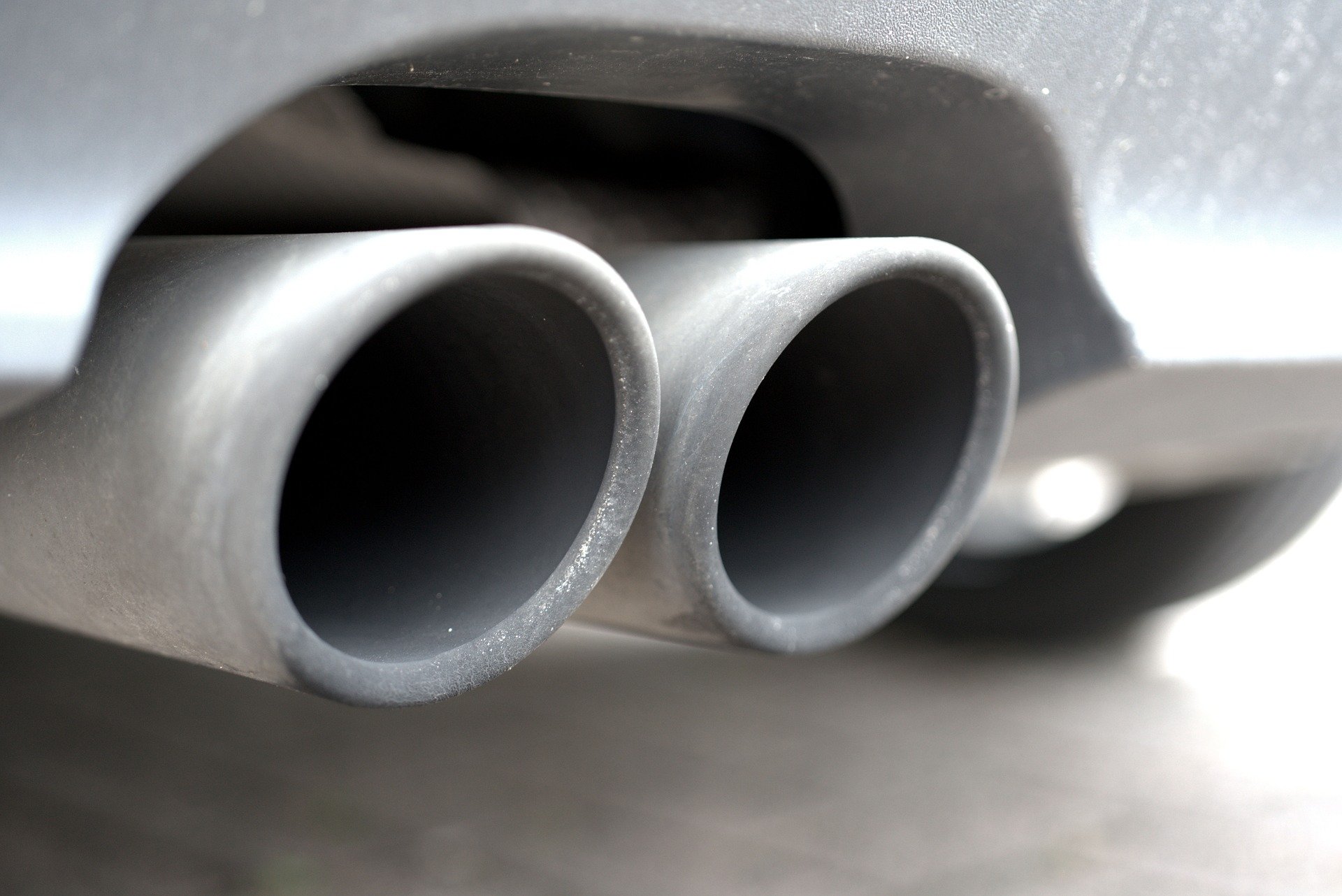
Wie ist das Projekt BatWoMan aufgebaut?
Wir arbeiten mit hochviskosen Schlicken, sogenannten Anoden- und Kathodenschlicken, die es ermöglichen, die Trocknung schon in die Kompaktierung der Elektroden einzubauen.
Nach der Kompaktierung werden die Elektroden strukturiert – weshalb wir von 3D-strukturierten Elektroden sprechen. Mit dem Effekt, dass die Elektrolyt-Füllung schneller und effizienter, aber auch mit weniger Elektrolyten durchgeführt werden kann. Dies spart Kosten und stellt einen neuen, innovativen Produktionsprozess dar.
Da wir die Elektroden auf Wasserbasis produzieren, gehen wir davon aus, dass nicht mehr alle Einzelschritte in geschützter Atmosphäre gemacht werden müssen. Wenn man nur die Elektrolytfüllung und die Kompaktierung in einer geschützten Atmosphäre machen könnte und dann den fertigen Zellstapel einfach in einer Trocknungseinheit trocknen, dann würde man in diesem Prozess schon sehr viel Energie sparen.
Auf die Füllung des Elektrolyten folgt dann die Formierung. Dabei kommen Anode und Kathode zum ersten Mal in Kontakt. Dieser Prozess basiert auf sehr niedrigen Strömen und ist daher langwierig. Manchmal entstehen auch Gase, die abgezogen werden müssen. Außerdem ist der Platzbedarf groß und liegt bei etwa 30 Prozent der gesamten Produktionsfläche. Ein Prozess, den wir im Projekt BatWoMan mit Maschinenansätzen optimieren wollen.
Im Projekt soll die nachhaltige Fertigung von Batteriezellen durch eine auf KI basierende Plattform digital unterstützt werden. Inwieweit kann diese unterstützend wirken?
Wir konzentrieren uns auf Mobilitätsanwendungen und dabei geht es sowohl um Recycling als auch um Wiederverwertung. Für beide Fälle ist es sehr wichtig, dass relevante Zellbauprozesse gespeichert und später ausgelesen werden können. Das gibt Aufschluss über den Lade- und Gesundheitszustand der Batteriezellen. Weiters werden in diesem Battery Data Space auch die Energiedaten der Batterie gespeichert, so dass am Ende der Produktion der tatsächliche CO2-Fußabdruck der Zelle abgelesen werden kann. Dadurch können Hersteller ihre Produktionsprozesse energieeffizienter gestalten.
Für eine solche Plattform spricht auch das zunehmend differenzierte Feld der Automotive, in dem an eine Antriebsbatterie für einen kleinen Familienwagen andere Anforderungen gestellt werden als an eine Traktionsbatterie für einen Sportwagen oder einen Kleinbus. Dabei wird man zwischen Kriterien wie preisgünstig, große Reichweite oder schnelle Bereitstellung von viel Energie entscheiden können. Auch das sind Anforderungen, die in Parametern auf einer solchen Plattform abgebildet werden können.
Was sind die relevanten Parameter für Recycling-Unternehmen?
Bisweilen erkennt man von außen bei einem Li-Ionen Akku noch nicht einmal aus welchen Hauptkomponenten er besteht.
Würde man die Materialien kennen, dann könnte man die Separation optimieren. Verschiedene Energiespeichersysteme enthalten unterschiedliche Arten von Materialien – und auch Recycling erfordert einen Energieeintrag und verursacht Kosten. Um abwägen zu können, inwieweit welcher Recyclingprozess wirklich sinnvoll ist, braucht es auch Daten wie die Dicke der Elektroden und deren Materialzusammensetzung. Wenn Energiespeicher zum Beispiel Kobalt, Nickel oder Mangan enthalten, dann sollte man diese Stoffe separieren, bevor der Recyclingprozess beginnt.
Wer soll Zugriff auf diesen Battery Data Space haben?
Es gibt Bestrebungen, einen europäischen oder auch globalen Battery Passport zu entwickeln. Die verantwortlichen Organisationen interessieren sich dafür, wie man die von uns entwickelte Plattform auf dieser Ebene integrieren kann. Auch dafür sind wir natürlich Ansprechpartner. Wer dann am Ende an welche Informationen kommt, wird letztendlich über diese Regulierungen zu klären sein.
Das Projekt BatWoMan soll gewährleisten, dass die Plattform dann zur Verfügung steht, wenn die Regulierung in Kraft ist. Wir schauen uns in dem Projekt an, welche Art von Data Space man braucht und wie man diesen implementieren kann. Dann erstellen wir die Plattform und untersuchen, welche Daten man wie auslesen kann. Da das Speichern von Daten einen Energieeintrag und Kosten verursacht, untersuchen wir auch, wie man das möglichst effizient machen kann.
Die Ergebnisse sollen die europäische Fertigung von Batteriezellen fördern. Inwieweit ist diese bereits vorhanden?
Derzeit findet die Produktion vorwiegend in Asien statt – und vor allem in China, wo bis vor kurzem noch über 80 Prozent der Batteriezellen weltweit hergestellt wurden. In den vergangenen Monaten wurden aber viele europäische Produktionsstätten angekündigt – sowohl von europäischen als auch von asiatischen Herstellern. Wobei sich die europäischen Zellproduktionsstätten stark auf nachhaltige Produktionsmethoden konzentrieren wollen.
Ist die Produktion in Europa wettbewerbsfähig?
Das muss man sicher unter Nachhaltigkeits- und Qualitätsaspekten betrachten. In der herkömmlichen Fertigung von Batteriezellen gibt es zum Beispiel einen hohen Anteil an Ausschuss. Bei hohem Qualitätsanspruch könnte dieser Anteil reduziert werden und man könnte einiges einsparen. Wenn von vornherein Recyclingoptionen eingeplant sind, dann können zumindest die eigenen Materialien wieder in den Kreislauf zurückgeführt werden. Weiters ist die Produktion von Batteriezellen in Europa auch eine Frage der Wertschöpfungskette. Es gibt Materialien, die man in Europa sourcen kann und Materialien, bei denen man an den asiatischen Markt gebunden ist. Das sind Dinge, die man sich ansehen muss, bevor man diese Frage abschließend beantworten kann.
Foto oben: Der Trockenraum im AIT Austrian Institute of Technology (c) AIT – Lang
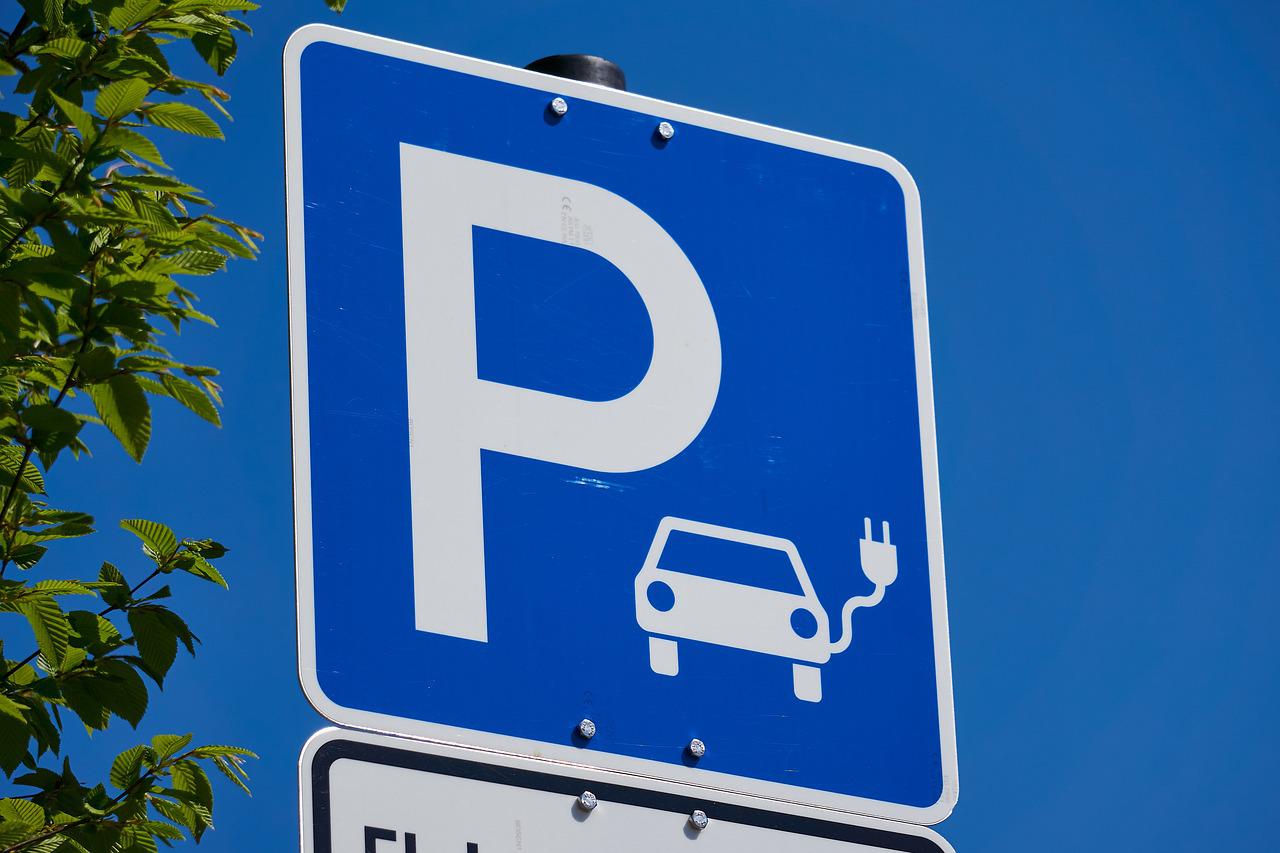