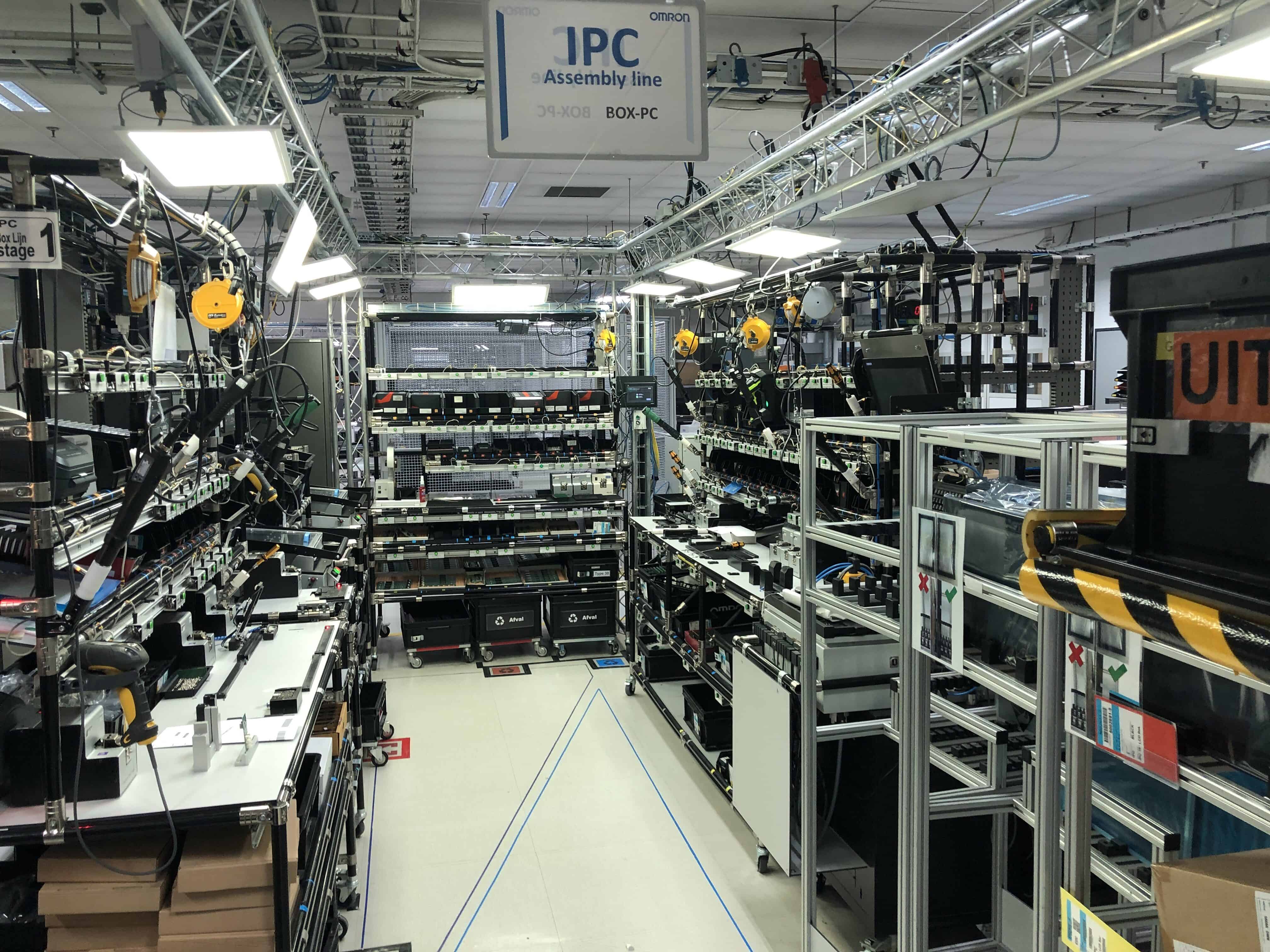
Die “Fabrik der Zukunft” mit dem Brainport Industries Campus (BIC) als Hauptsitz umfasst neun verschiedene Projekte oder Fieldlabs. Eins davon ist die “Digitale Fabrik”, die von Laurens Meijering von Brainport Industries geleitet wird. Ziel dieses Feldlabors ist es, die Bedingungen zu schaffen, unter denen die verarbeitende Industrie den Übergang zum vollständig digitalen Arbeiten vollziehen kann. Die Integration datengestützter Innovationen ist Teil dieser Aufgabe.
Im Fieldlab arbeiten Fertigungsunternehmen, Lösungsanbieter und Wissenseinrichtungen gemeinsam an einer Umgebung, die die Vorteile und Bedingungen der Digitalisierung in der Praxis demonstriert. Es finden Experimente statt, und es gibt Experten, die Interessenten bei den ersten Schritten begleiten.
“Letztendlich geht es für diese Unternehmen um Produktivitätssteigerung”, sagt Laurens Meijering. “Das kann die Maschine, die Produktionsstätte oder die Lieferkette betreffen; überall spielt die Digitalisierung eine Rolle. Das Ziel der Digitalen Fabrik ist es, diesen Prozess so zukunftssicher wie möglich zu gestalten. Dabei schauen wir auch auf (internationale) offene Standards, denn natürlich ist es am besten, wenn alle auf die gleiche Weise damit arbeiten.”
Vom digitalen Pflaster zur Blaupause
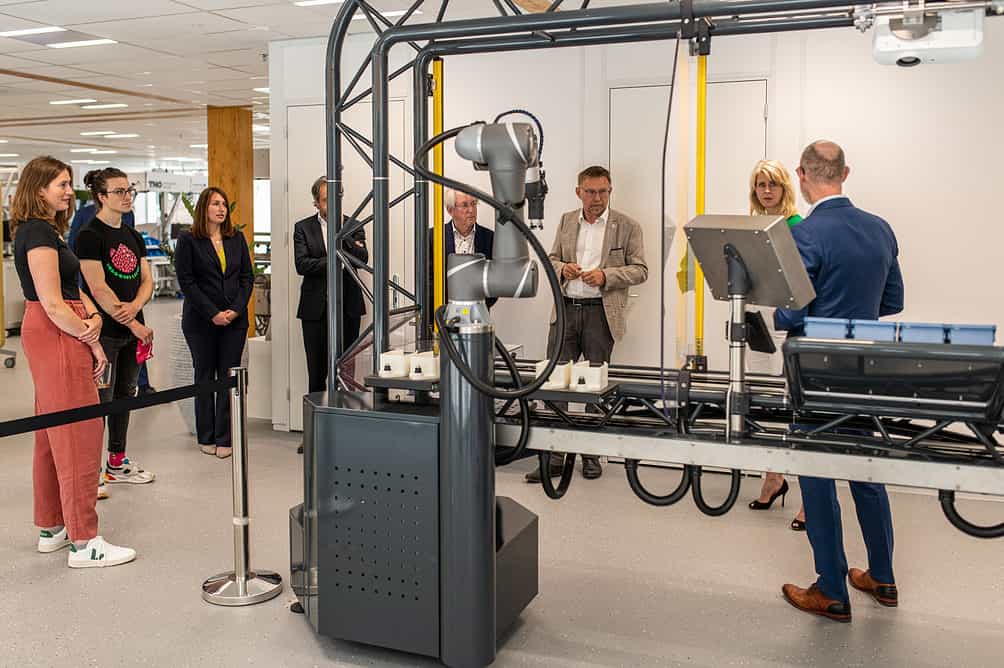
Während in der Vergangenheit hier und da ein “digitales Pflaster” aufgeklebt wurde, ist es laut Meijering für die Zukunft wichtig, Entwürfe mit digitalen Tools oder Apps zu erstellen. “So kann man nicht nur innerhalb der eigenen Organisation besser kommunizieren, sondern auch mit externen Parteien. Die Maschinen können leichter interagieren und die Mitarbeiter haben eine gemeinsame Wissensbasis.”
Aber ein solcher Plan ist immer noch recht kompliziert, zumal er auf vielen Ebenen funktionieren muss. “Datenaustausch findet überall statt. Zum Teil geschieht das auf der Grundlage bestehender Normen, es gibt aber auch eine Vielzahl von Normen, die noch entwickelt werden. Die Digitale Fabrik geht dies auf drei Arten an, sagt Meijering. “TNO, einer unserer Wissenspartner, erstellt einen Rahmen, der alle Normen enthält. Manchmal handelt es sich nur um Anwendungen, manchmal um kompliziertere Tools. Dies ist der Top-Down-Ansatz, die Grundlage für den Entwurf. Zweitens gibt es die Initiativen der Unternehmen selbst, die ihr eigenes Wissen einbringen und auf der Grundlage des Entwurfs Lösungen entwickeln. Das Schöne daran ist, dass diese Lösungen auch für andere geeignet sind und daher vermarktet werden können. Und schließlich gibt es das Fieldlab hier im BIC, das Erfahrungszentrum, in dem man all diese Entwicklungen mit eigenen Augen sehen kann. Sie können sich dann selbst ein Bild davon machen, was es braucht, um eine solche digitalisierte Produktionslinie zu schaffen. In der Zwischenzeit entwickeln wir das Schritt für Schritt weiter.”
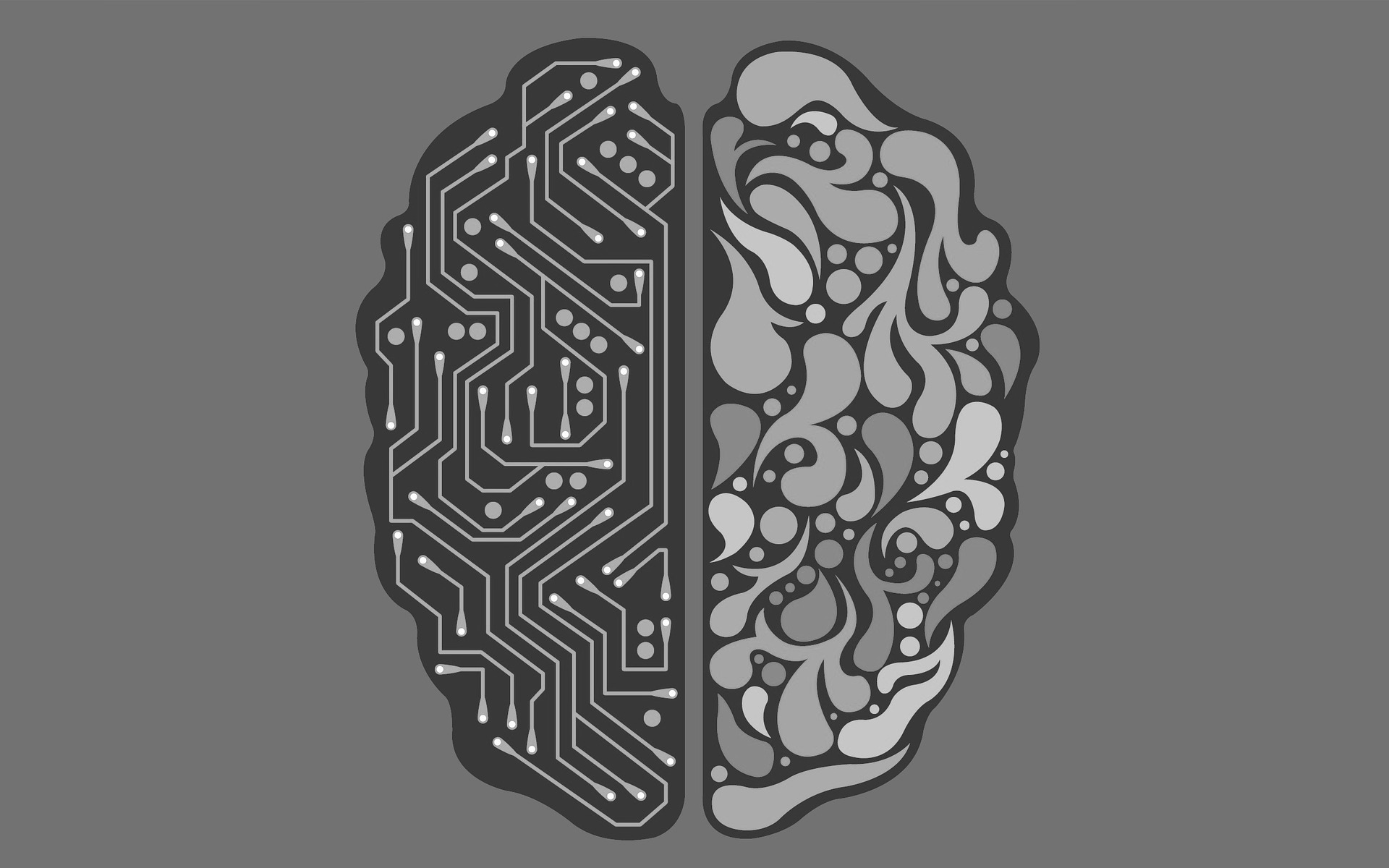
Mensch und Maschine
Omron ist eines der Herstellerunternehmen, die Mitglied sind. F&E-Leiter Tim Foreman sieht den doppelten Nutzen: “Als ‘Lösungsanbieter’ helfen wir mit unserem Wissen bei der Realisierung der Testumgebung, aber gleichzeitig ist es unser Werk in Den Bosch, das die Vorteile als erstes nutzen kann.” Dabei setzt er auf eine gute Zusammenarbeit zwischen Mensch und Maschine. “Gemeinsam mit TNO entwickeln wir die Produktionslinie neu. Wir befassen uns nicht nur mit Maschinen, sondern mit allem, was sie beeinflusst, einschließlich der Menschen. Maschineneffizienz ist nur eine Sache, Gesamteffizienz ist das Ziel. Mit TNO haben wir dies zunächst analysiert, um dann zu sehen, wie wir die Ergebnisse in das TNO-Konzept integrieren können.”
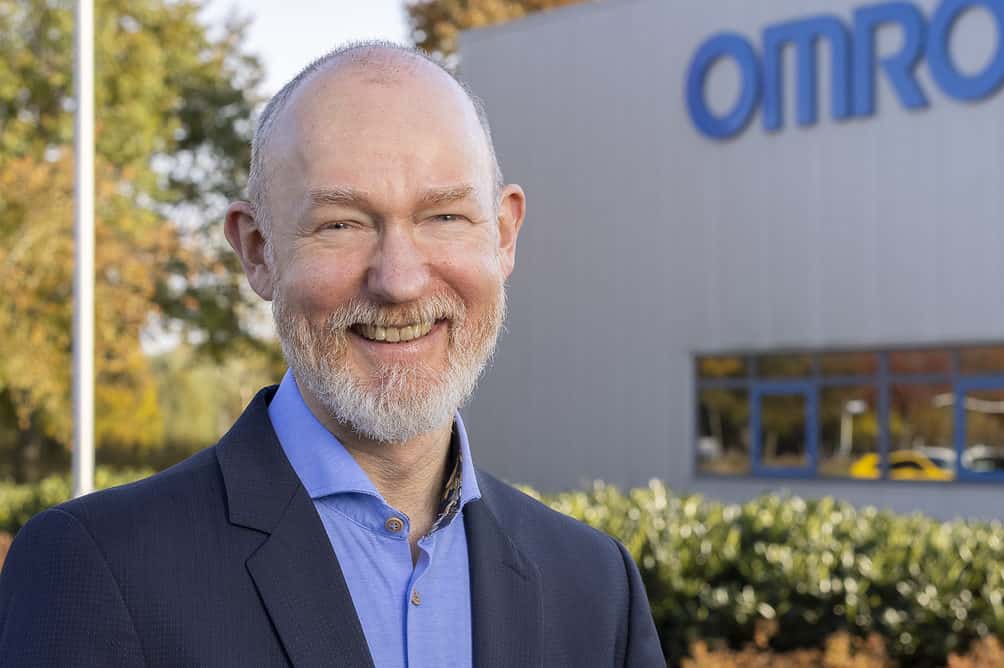
Dafür sind jedoch mehrere Partner erforderlich, insbesondere in der Kategorie der “Lösungsanbieter”. Eines davon ist Itility, ein IT- und Engineering-Unternehmen mit Sitz in Eindhoven. Der leitende Berater Geert Vorstermans war sofort von dem Projekt angetan, bei dem Omron Technologie und Daten kombiniert. “Unser Ziel ist es, die Gesamtressourceneffizienz (ORE) für das gesamte Werk mit seinen etwa 20 Produktionslinien um 10 bis 15 Prozent zu erhöhen. Wir beginnen zunächst in kleinem Rahmen, indem wir den Ansatz und das Konzept an einer Maschine testen und dann auf die gesamte Produktionslinie ausweiten. Auf diese Weise können sowohl Omron als auch Itility eine Technologie nutzen, die noch nicht zum Verkauf steht, aber getestet werden kann – eine Win-Win-Situation für beide Unternehmen.”
Das erwies sich bald als Erfolgsrezept. Vorstermans: “Eine ganze Fabrik digitalisieren zu wollen, ist zu viel, das funktioniert nicht. Mit Reden oder Warten allein kommt man aber auch nicht weiter, man muss mit etwas Kleinem anfangen. So nahmen wir die Blaupause und begannen mit der Suche nach Techniken, die uns helfen könnten. Was funktioniert und was nicht? Wir haben uns unter anderem für eine Produktionslinie, eine Maschine und einen Industriestandard für Maschinenzustände entschieden, und dann ging es los. Nach dem Entwurf begannen wir also, alle Felder auszufüllen. Daraus entstand eine dieser ‘Apps’, wie wir sie nennen, die jetzt auch in der Digitalen Fabrik zu sehen sind.”
Grenzen
Nicht alles funktioniert auf Anhieb, manchmal stößt man an Grenzen, sagt Foreman. “Einige Techniken sind zwar interessant, aber für unsere Zwecke nicht geeignet. Manchmal gibt es eine Funktionalität, die fehlt, und dann kann TNO sie in die Normungsgruppen zurückbringen. Das ist die Chance: etwas auszuprobieren, auf etwas zu stoßen und auf diese Weise weiterzukommen.”
Das Konzept der ‘asset administration shell’ ist so etwas. Man kann damit alle Teile einer Produktionslinie digitalisieren. Von der kleinsten Schraube bis zur größten Maschine. An sich ein großartiges Konzept, denn theoretisch kann man auf diese Weise die ganze Welt digital aufbauen, komplett mit materiellen Pässen und so weiter.”
Noch ist nicht alles auf diese Weise realisierbar. “Wir hatten zum Beispiel große Hoffnungen auf einen Weg gesetzt, auf dem wir anfangen wollten, Maschinenstatusdaten im Sekundentakt – oder schneller – auch in einer Anlagenverwaltung zu speichern. Aber es hat sich herausgestellt, dass das mit dem heutigen Stand der Technik nicht wirklich machbar ist.”
Andererseits hat eine ähnliche Idee für die Walzstraße bei Tata Steel funktioniert, fügt Meijering hinzu. “Das ist eine Straße, die Hunderte von Metern lang ist, mit Hunderten von Rollen. Diese verschleißen und müssen mit der Zeit ersetzt werden. Nicht zu früh und auf keinen Fall zu spät. Damals wurden digitale Peelings um eine große Anzahl von Walzen herum gebaut; sie sind immer noch riesig, aber besser machbar. Wenigstens muss man nicht auf die Millisekunde genau messen.”
Bis Ende 2023
Das Projekt Digitale Fabrik wird mindestens bis Ende 2023 laufen. “Aber natürlich bleibt diese Entwicklung nicht stehen”, sagt Meijering sofort. “Es kann immer besser und intelligenter gemacht werden. Dabei so klar wie möglich, mit den dazugehörigen Standards. Ich mache mir keine Illusionen, dass unser Projekt weltweit Standards setzen wird, höchstens beeinflussen. Aber wir versuchen, Entwicklungen aufzugreifen. Und inzwischen sind so viele Unternehmen zu uns gekommen, dass wir tatsächlich etwas für die Digitalisierung der Fertigungsindustrie bewirken konnten.”
Sind Sie auch an der Digitalen Fabrik interessiert? Dann melden Sie sich bei Projektleiter Laurens Meijering: [email protected]