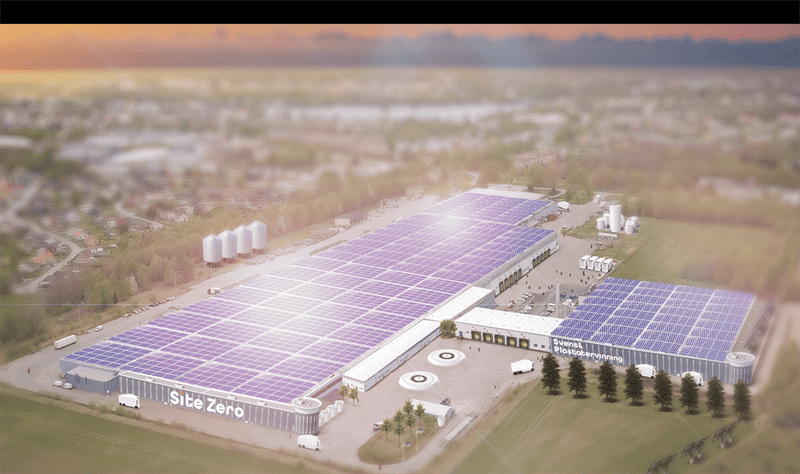
Site Zero, a revolutionary facility in Motala, Sweden, has begun operations as the world’s largest plastic-sorting plant. With an investment of SEK 1 billion, the plant distinguishes itself by being able to process all of Sweden’s plastic packaging waste. Boasting a sorting capability of 200,000 tonnes of plastic annually, Site Zero can sort 12 different types of plastics. The facility’s efficiency marks a significant uptick from 47 percent to an impressive 95 percent of recycled plastic packaging, drastically reducing the need for incineration.
- The world’s largest plastic recycling plant started operations in Sweden.
- Site Zero can handle handle up to 200,000 tonnes of plastic per year, increasing recycling efficiency to 95 percent.
Site Zero represents a monumental leap forward in recycling technology. Infrared cameras are at the heart of this advancement, enabling the facility to sort 40 tonnes of mixed plastic waste per hour. This sophisticated sorting process utilizes 60 Near Infra-Red (NIR) sensors along approximately five kilometers of conveyor belts. As a result, the facility can separate plastic packaging into 12 distinct types, including PP, HDPE, LDPE, PET trays, and PET bottles, both colored and transparent.
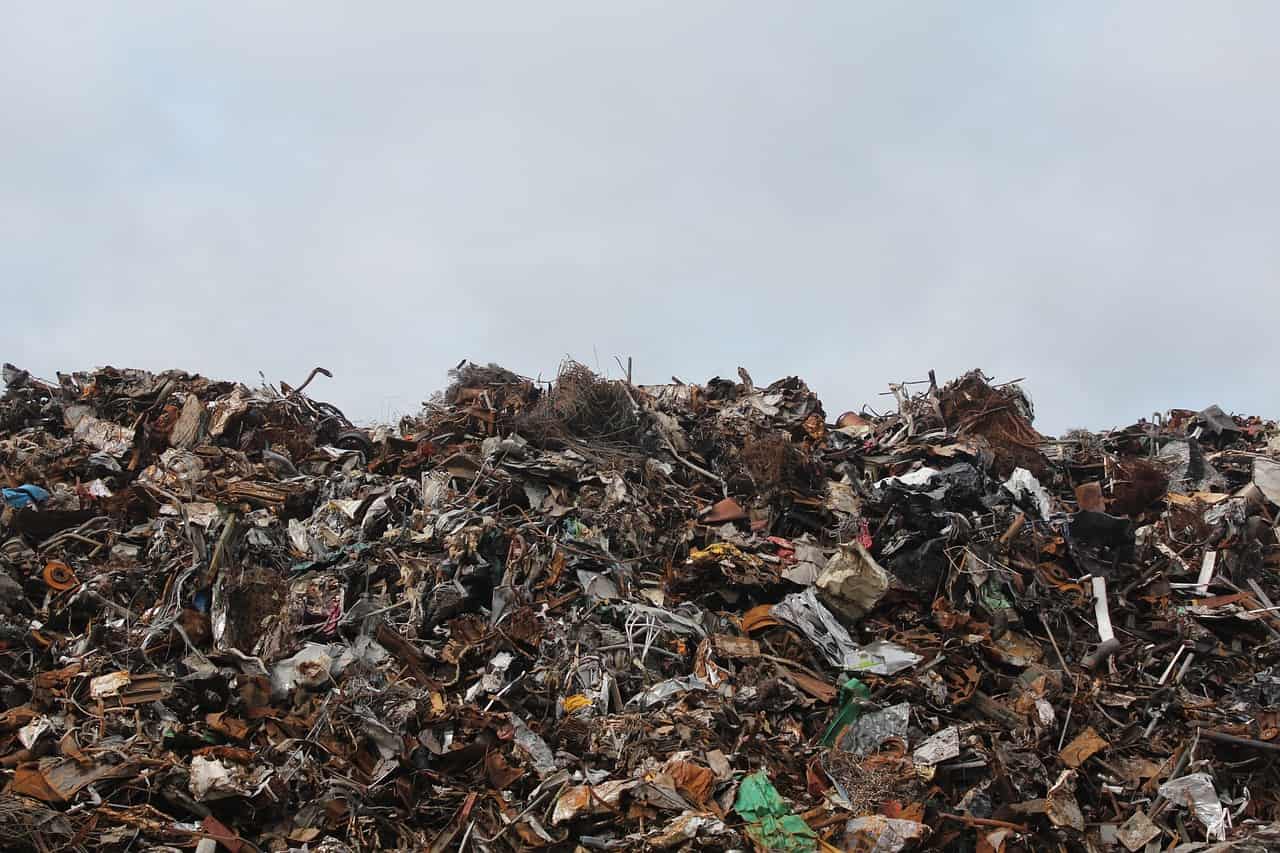
From game changer to green pioneer
Experts have hailed Site Zero as a ‘game changer‘. Åsa Stenmarck of the Swedish Environment Protection Agency and Robert Blasiak, a Stockholm Resilience Center researcher, affirm that Sweden is setting a new global standard in plastics recycling. The plant’s operation aligns with the urgent need to address the global plastic waste crisis, projected to triple by 2060. Currently, only a fraction of this waste is recycled, with the majority ending up in landfills or incinerated.
The future of plastic recycling in Sweden
Despite these uncertainties, the ambition of Site Zero is clear. The facility is part of a broader strategy to achieve zero waste and close the loop on plastics. By 2025, the site plans to include a washing and granulation station, furthering its aim to make the entire plastic flow in Sweden circular. The plant is a collaboration between Svensk Plaståtervinning, Sutco, and Tomra, with Tomra providing state-of-the-art sorting technology to maximize material recovery.
Mattias Philipsson, CEO of Svensk Plaståtervinning, has articulated a vision for Site Zero that encompasses “zero waste, zero downcycling, and zero emissions”. This commitment is reflected in the plant’s design, ensuring no packaging goes to incineration. Any residual plastic fragments after sorting are directed towards chemical recycling, new composite products, or used in energy recovery with carbon capture and storage.
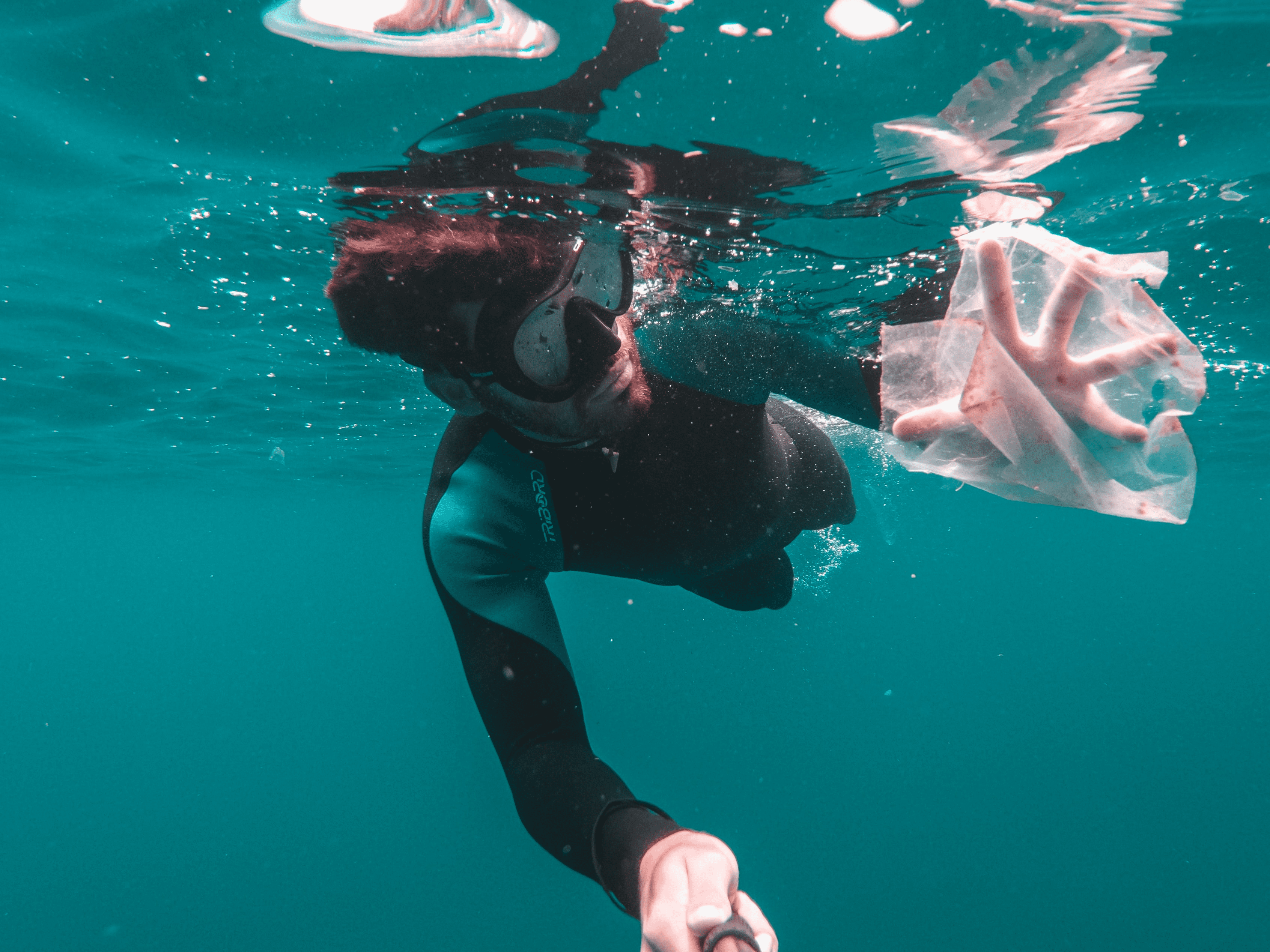
Collaborative efforts and technological marvels
The success of Site Zero is underpinned by collaboration. It is not just a facility; it is the culmination of efforts from various stakeholders in the recycling process. Producers and machine suppliers like Tomra have played a pivotal role in equipping the facility with over 60 Autosort machines capable of processing materials with up to 98 percent purity levels.
Oliver Lambertz, VP and head of operations and feedstock sourcing at Tomra Feedstock, emphasized the importance of Tomra Insight. This cloud-based data platform provides real-time monitoring of sorting lines. This technology is critical in achieving the high purity levels required for effective recycling.
With the inauguration of Site Zero, Sweden boldly stepped into the forefront of the fight against plastic waste. The facility embodies the country’s dedication to environmental stewardship and a circular economy. While performance data and details on the supply chain are awaited, the groundwork laid by Site Zero is undeniably transformative. It is a beacon of innovation, setting a national and global precedent for sustainable plastic recycling.