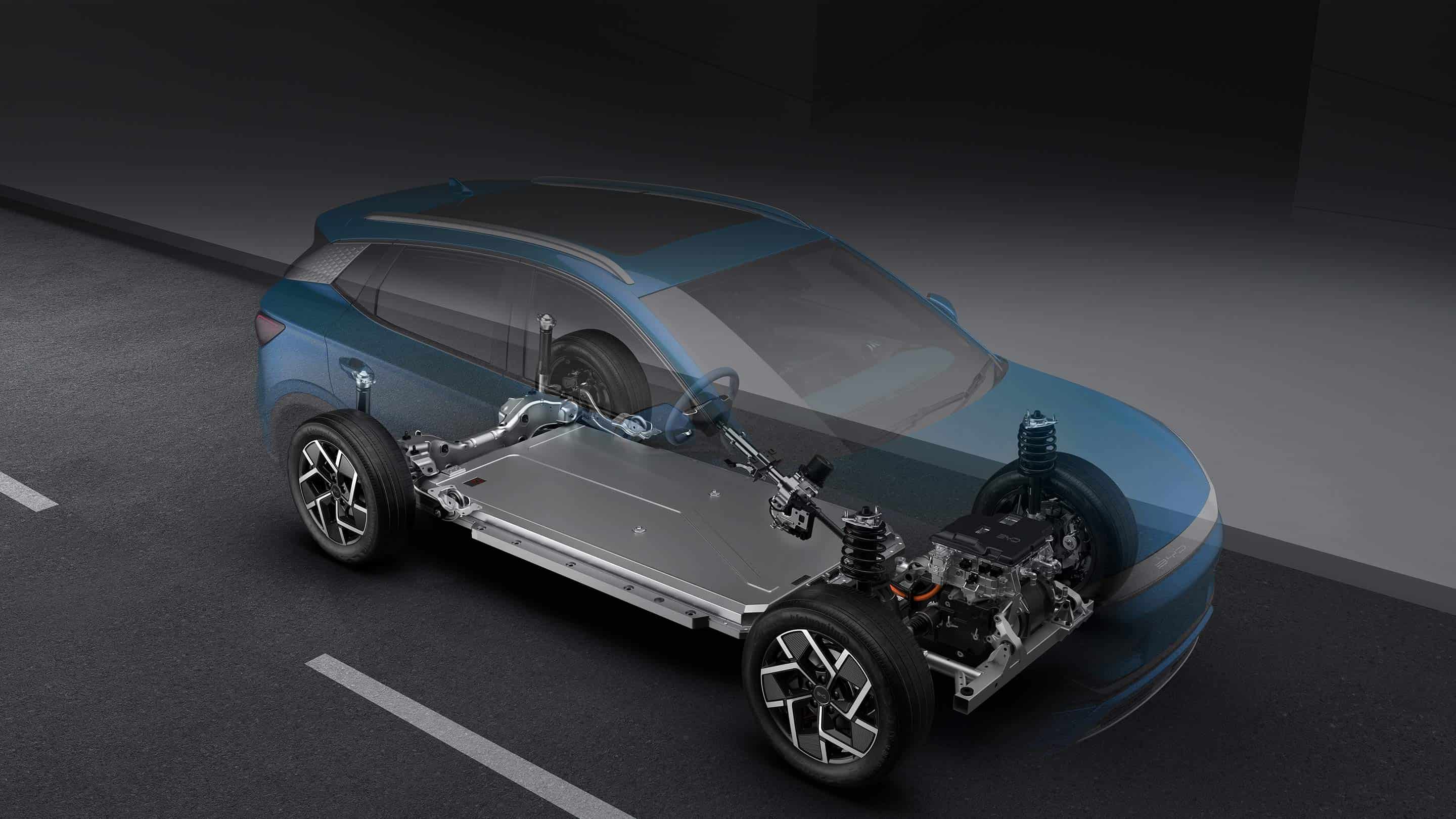
Altilium Metals, a Devon-based company, is trailblazing the green revolution with its innovative EV battery recycling technology. The only UK company recovering critical battery minerals from waste EV batteries, Altilium Metals has developed a novel process that extracts over 95% of critical metals, setting a new global standard. Its technology has been verified by the University of Plymouth and received considerable investment from the UK government’s Automotive Transformation Fund and Devon County Council’s Green Innovation Fund. The company plans to scale up its test facility, aiming to recycle one EV battery per day at its Tavistock technology centre by year-end. By early next year, Altilium intends to have its first recycling plant operational in Europe, with the capacity to recycle 24,000 batteries annually.
- Altilium Metals’ innovative EV battery recycling technology has achieved an unprecedented recycling efficiency of over 95% for critical battery metals.
- The company plans to scale up its operations from recycling one EV battery per day at its Tavistock technology center to having an operational recycling plant in Europe, capable of recycling 24,000 batteries annually.
- Altilium Metals’ pioneering technology significantly reduces the need for mining virgin materials, aligning with the UK government’s Critical Minerals Strategy and contributing to the transition to a circular economy.
Revolutionising the future of EV battery recycling
Altilium Metals’ pioneering technology is driving the transformation of the EV battery recycling industry. Through its UK subsidiary, Altilitech Ltd, the company has developed a unique process that not only recovers critical metals, such as lithium, nickel, cobalt, and manganese, from used batteries, but also achieves an unprecedented recycling efficiency of over 95%. This revolutionary technology is setting a new global standard, significantly reducing the need for mining virgin material, thus mitigating the environmental and social costs associated with mining.
This advancement in recycling technology is a significant stride towards achieving a circular economy. The process recovers and reuses critical metals within the UK supply chain, mitigating the risk to energy security posed by the UK’s dependence on global supply chains for these metals. By recycling locally, Altilium Metals prevents the loss of component value and the need to store and transport hazardous waste materials overseas. This approach aligns perfectly with the aims of the UK government’s Critical Minerals Strategy published in July 2022.
Scaling up operations
With the support of the UK government, Altilium Metals began studies in January 2022 on retrofitting their MEDET Solvent Extraction-Electrowinning (SX-EW) plant for processing end-of-life EV lithium-ion batteries. The company’s existing hydrometallurgical plant and its environmental permits give it a first-mover advantage in the European market for large-scale recycling of EV batteries.
While the Tavistock technology centre is set to recycle one EV battery per day by the end of this year, the company has grander ambitions. Altilium Metals has completed a feasibility study for the development of the UK’s largest EV battery recycling plant which will be capable of recycling a staggering 150,000 batteries per year. This new plant, expected to be operational by early next year, will be a significant contributor to reducing the carbon footprint of new EVs and promoting green recovery.
Creating jobs and bolstering the local economy
Altilium Metals’ commitment to Devon is unwavering. It plans to build its technical and project management functions in the region, creating new jobs and supporting apprenticeships, thus contributing to the low carbon industry. By 2026, the company expects to have created 250 new roles and recycled battery waste from over 150,000 electric vehicles. This aligns perfectly with Devon County Council’s commitment to supporting innovative businesses and projects that drive the transition to a Net Zero economy.
The company’s plans also extend to Teesside, where it will open a multi-million pound factory. This new facility will transform battery waste from over 150,000 electric vehicles into ‘Cathode Active Material’, a critical component of new batteries. The creation of between 100 and 200 high-value jobs before 2025, with additional jobs during the construction phase, will provide a significant boost to the local economy.