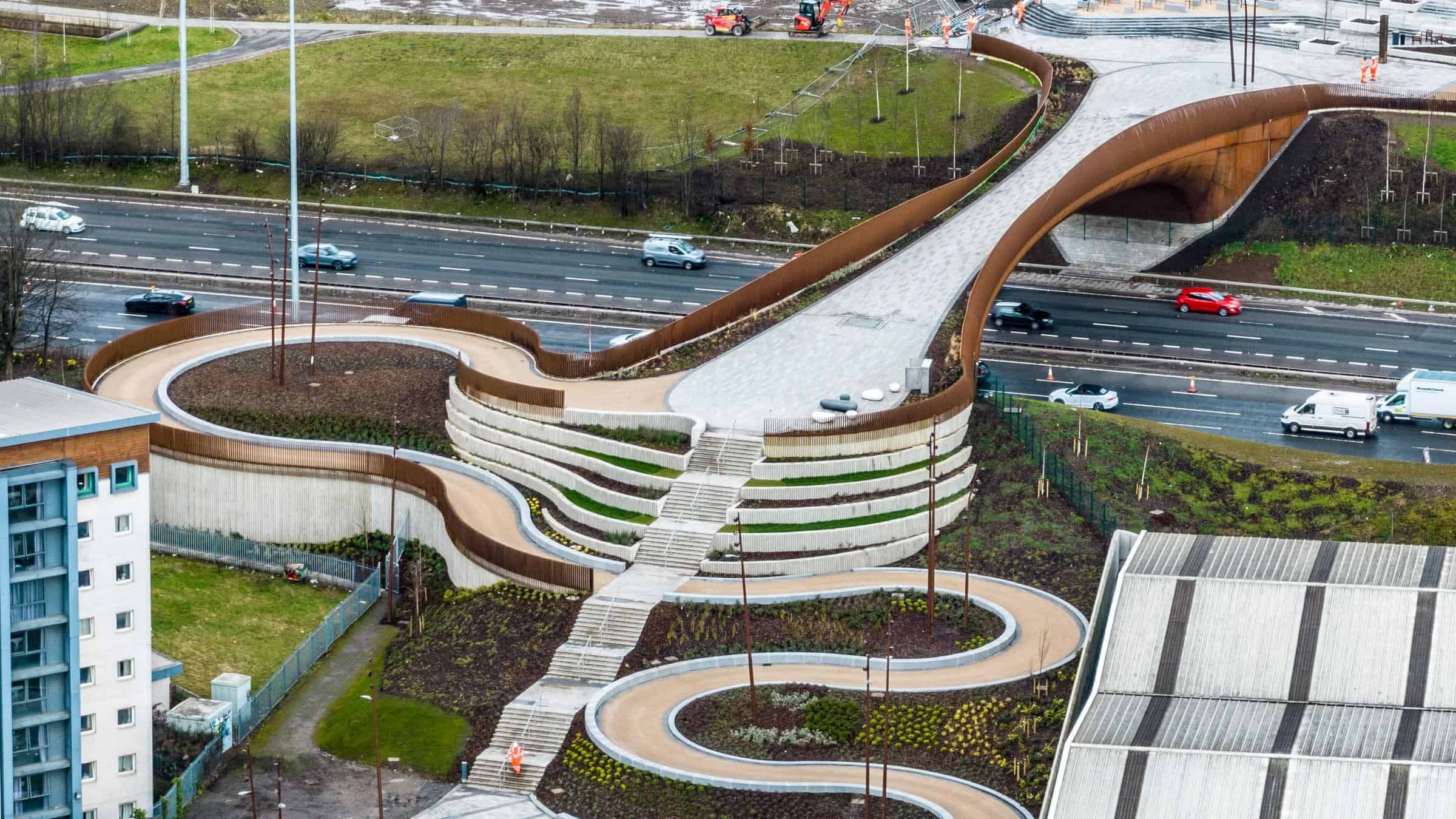
Glasgow’s stunning new “active transport” bridge is now open to the public, connecting over 800 new homes in the Sighthill area to the city center. This innovative bridge is part of a £250 million regeneration project, which is the largest of its kind in the U.K. outside London. The 2,420-tonne structure was installed during a 14-hour closure of the M8 motorway in the summer of 2021. It was opened this week.
The bridge is manufactured using Cor-Ten steel for a weathered appearance, reducing maintenance costs and reflecting the area’s industrial heritage. The project features the first use of 3D concrete printing in Scotland for the bridge’s staircase, making it the largest printed concrete construction in the UK. Clad in granite, the staircase offers an attractive, long-lasting, and slip-free finish. The bridge’s successful completion showcases the potential of cutting-edge digital techniques and collaboration in construction.
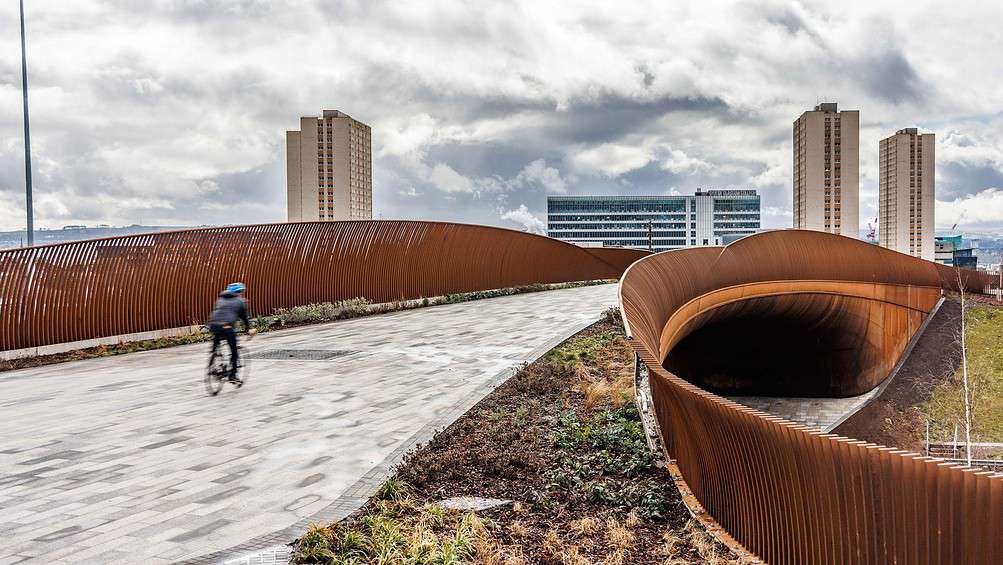
3D Concrete Printing: A Sustainable and Innovative Approach
3D concrete printing has numerous advantages, including creating intricate, unique structures that are difficult to achieve with traditional formwork. This innovative method is cost-effective, reduces waste by up to 40%, and improves carbon efficiency compared to conventional construction techniques [1]. The strength of the 3D-printed staircase is equal to that of on-site poured concrete, and the controlled environment manufacturing eliminates weather concerns and reduces on-site construction risks. Automated sensors are also used to ensure the quality of the mortar during the printing process.
BAM UK collaborated with Weber Bemix, a Netherlands-based concrete printing expert, to print the staircase components [1]. The partnership between BAM and Weber Bemix has a history of successful projects, including the world’s longest 3D concrete printed bridge in Nijmegen, Netherlands, in 2021 [2]. Ian Steele, BAM Contracts Manager for the M8 Footbridge, expressed his delight with the project’s outcome and the potential for 3D concrete printing to modernize construction, reduce risk, improve efficiency, and lower carbon footprints [1].
Global Examples: The Netherlands Leads the Way in 3D-Printed Bridges
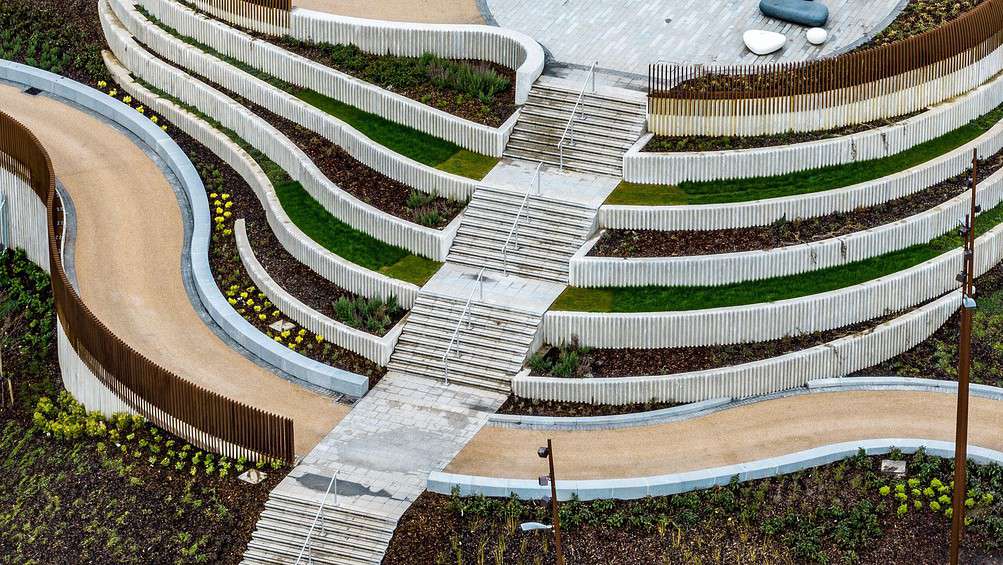
In addition to the Nijmegen bridge, the Netherlands is home to the world’s first fully 3D-printed, structurally pre-stressed concrete cycle bridge [3]. Developed by BAM Infra and TU Eindhoven, the bridge is part of the Gemert Noord-Om project in Noord-Brabant and was completed in September 2017. Spanning eight meters in length, the bridge crosses the Peelse Loop river in Gemert [4].
3D printing offers numerous benefits, such as reduced material requirements, less waste, and lower CO2 emissions. This innovative production method has the potential to enable on-site construction, minimizing environmental impact and shortening construction times. As a result, traffic disruptions due to road closures can be significantly reduced. Customization is another advantage of 3D printing, allowing for unique designs while maintaining cost-effectiveness and improving Building Information Management (BIM) [3].
Looking Ahead: The Future of 3D Concrete Printing in Construction
As 3D concrete printing technology continues to advance, its applications in construction are expected to grow. The successful completion of Glasgow’s active transport bridge and the Netherlands’ innovative cycle bridges demonstrate the potential for this technology to revolutionize the industry. Using 3D printing in construction projects can lead to more sustainable and efficient practices, reducing waste and carbon emissions while enabling greater design flexibility and customization.
With increasing interest and investment in 3D concrete printing, the aspiration is to establish a UK-based printing facility, further enhancing the country’s construction capabilities [1]. As more contractors adopt this innovative technology, the construction industry can continue to evolve, providing sustainable and cutting-edge solutions for infrastructure projects worldwide.
Sources:
[1] BAM
[3] BAM UK
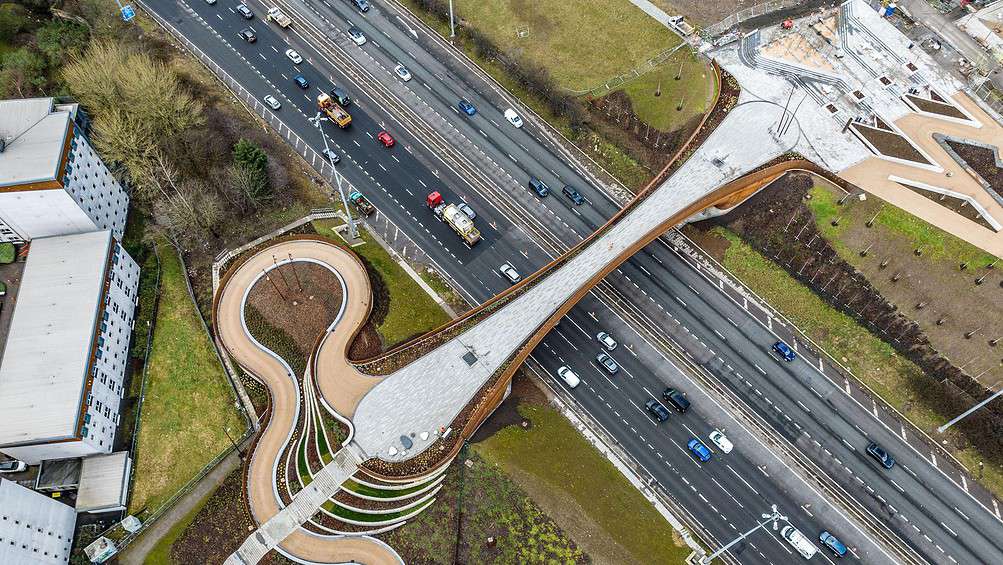