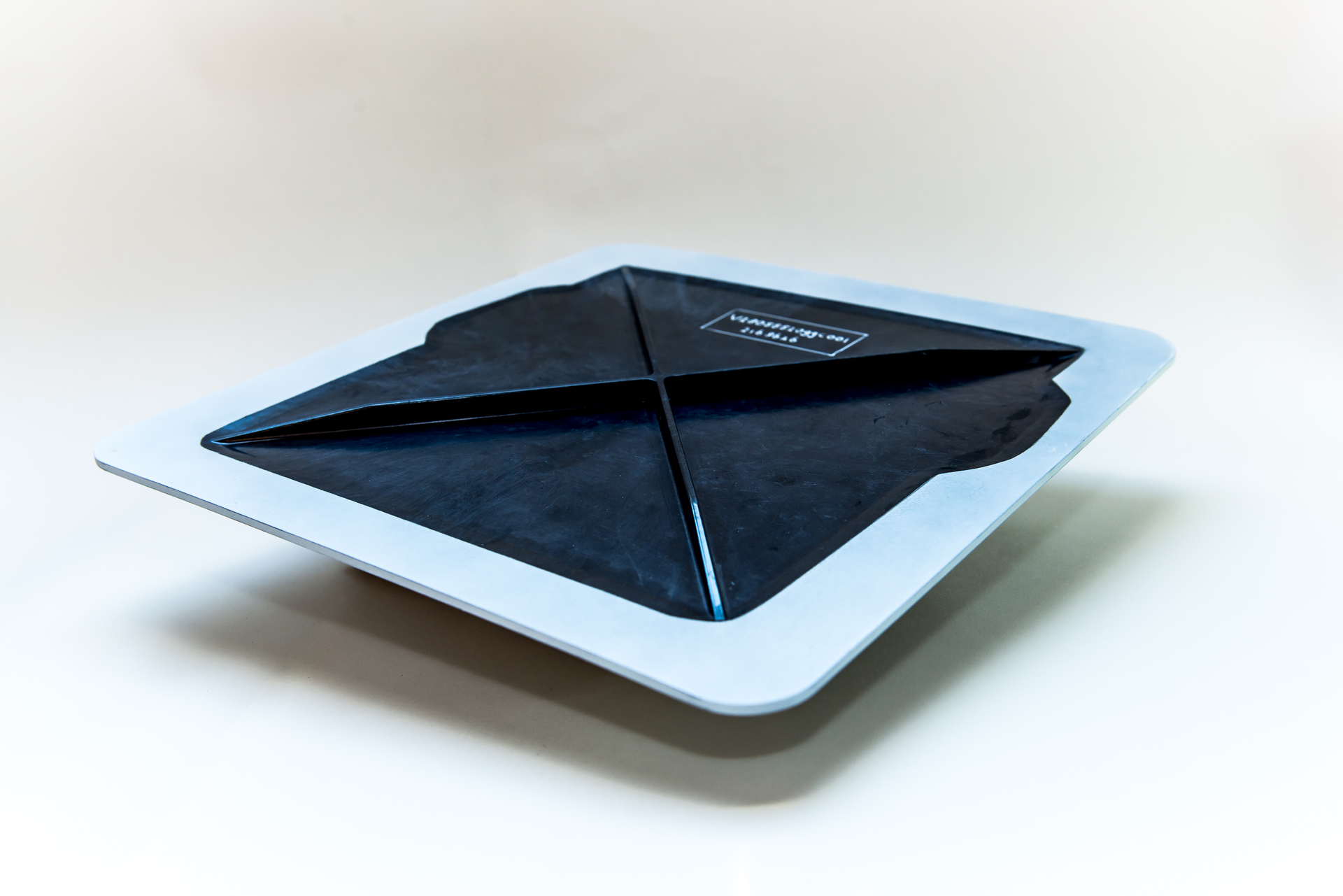
The manufacture of sustainable aircraft is a step closer thanks to an invention from the Saxion University of Applied Sciences in the Dutch city of Enschede. In cooperation with GKN Aerospace and other partners, the ThermoPlastic composites Application Center (TPAC, part of Saxion University of Applied Sciences) has found a way to recycle used aircraft parts made of thermoplastic carbon fiber composite. They subsequently develop new high-grade products from these. Parts based on this material have recently been successfully tested on a series of flights with rotorcraft.
According to Saxion, this application, which is made entirely from recycled materials, is a worldwide first in the aviation industry. It is the result of a fruitful collaboration between Dutch researchers and the industry.
Recycled waste material from thermoplastics
The parts – two compressed access panels made from recycled thermoplastic waste material – were developed in the Dutch TPC-Cycle research program. GKN Aerospace delivered the final product in June 2019. TPC-Cycle is managed by TPAC at the Saxion University of Applied Sciences.
Not only is the product made from recycled material 9 % lighter than conventional technology, it is also much more sustainable. According to TPAC’s calculations, the part reduces CO2 emissions during manufacture by approximately 80 %. In addition, the process that was developed delivers a much shorter manufacturing time and considerable cost savings.
Carbon fiber is as strong as steel. Yet it has the added advantage that it is a lot lighter than aluminum. Thermoplastic carbon fiber composite is already widely used in the aircraft industry for this reason. Whereas aluminum is easily recyclable this has posed problems for carbon fiber composite up until now. But this now seems to be achievable with the method from GKN Aerospace and TPC-Cycle.
Potential for other industries as well
“Not only are the successful tests providing significant added value for the aviation industry, but they also have plenty of potential for other industries where sustainability and the use of lighter materials are becoming increasingly important,” says Ferrie van Hattum. He is a lecturer in Lightweight Construction at Saxion and scientific director of the TPAC.
GKN Aerospace, the partner in this research program and the parent company of Fokker, is a leader in the thermoplastic technology field within the aviation sector. The company manufactures, among other things, thermoplastic composite rudders, elevator tails, and aircraft fuselage panels. These are all used on a wide range of aircraft.
About Saxion and TPAC
Saxion University of Applied Sciences focuses on education, research, and entrepreneurship. TPAC is a research center that conducts research based out of Saxion in collaboration with numerous companies, SMEs in the main. New technologies are being developed for the use of thermoplastic composites in a wide variety of applications. Apart from that, research is also being carried out into automating various processes. And into the recycling of thermoplastic composites.
Working with Saxion are ThermoPlastic Composites Application Center (TPAC), ThermoPlastic Composites Research Center (TPRC), GKN Fokker, Toray Advanced Composites (TAC), Dutch Thermoplastic Components (DTC), Cato Composites and Nido Recycling Techniek (NRT). Saxion students have also participated in this project.