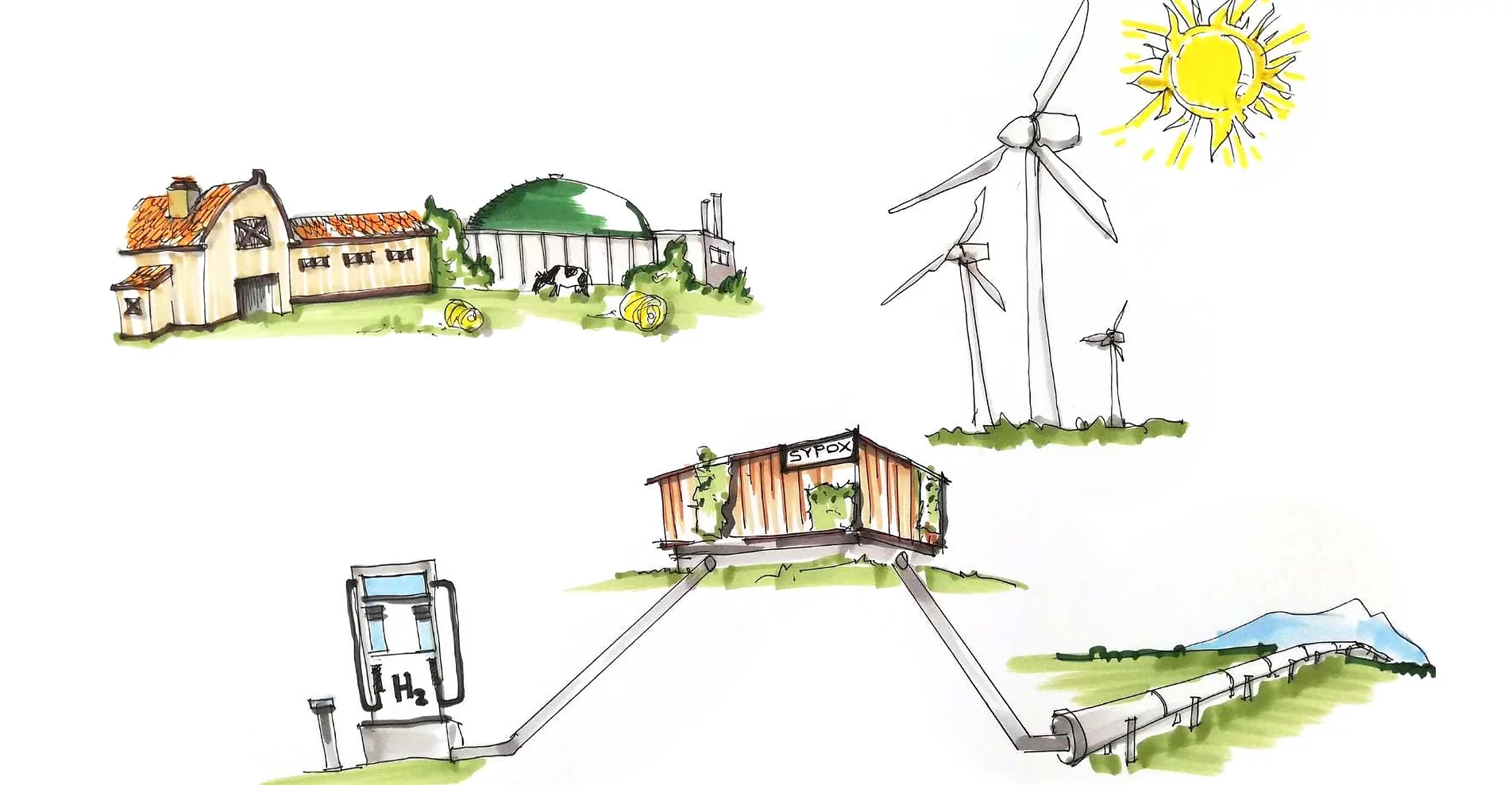
“Hydrogen is going to play a crucial role in the energy transition, for example, in industry and mobility,” says Gianluca Pauletto, CEO and co-founder of Sypox. The start-up – with its headquarters in Munich – has also recently set up an office on the Brightlands Chemelot Campus in the Dutch town of Geleen. While studying chemical engineering, Pauletto conducted research into the production of hydrogen from natural gas. As time went by, he came up with a plan to radically change the way hydrogen is produced. First of all, he no longer wants to generate the heat needed for the process with fossil fuels, but with renewable sources of electricity. “We are electrifying the chemical industry,” Pauletto sums up.
Major impact
Gigantic ovens are now used to produce hydrogen. Sypox wants to replace these traditional ovens that make use of fossil fuels with electric ones. “If we manage to apply our technology in existing processes to make hydrogen, we can reduce CO2 emissions of this industry by fourty percent,” he says. “We’ll make a huge impact on the world that way.”
There are also other advantages. “The electric oven that we are developing is much smaller than the existing ovens,” he says. “The current model is made up of two parts. On one side is a burner that burns fossil fuels and on the other side, is where the energy-intensive chemical reaction takes place. In our new solution, we bring these two parts together. We generate the heat in the same place where we need it for the chemical reaction. That in turn makes the furnace much more efficient and a hundred times smaller than the existing model.”
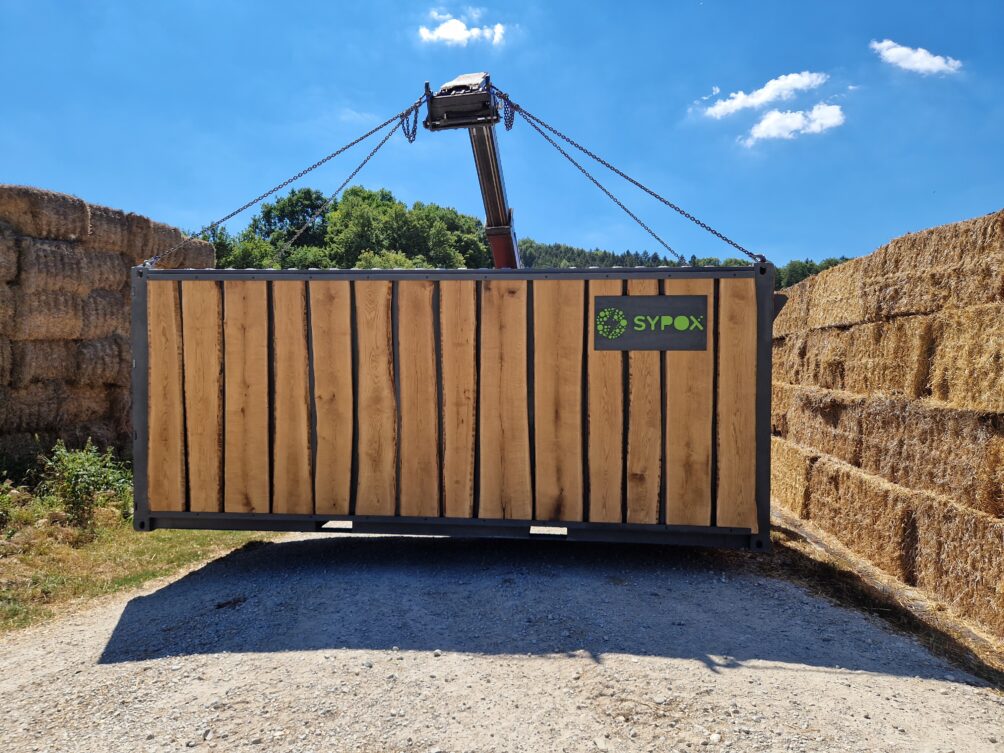
Entering the market
Bringing this type of new oven to the market is a long and complicated process. This is something that the founder of Sypox was quick to realize. That’s why he was looking for a way to enter the market at an early stage. “We want to do that by already commercializing our technology on a smaller scale. We are now focusing on smaller, decentralized applications,” he states.
Biogas
That’s how Pauletto ended up in the biogas industry, the second thing he wants to use to change hydrogen production. At the moment, biogas is still often converted into electricity. “This is happening on farmers’ land. They have loads of biomass, for instance, from land waste. This is converted into biogas using bacteria. Then the farmers convert the biogas into electricity using an internal combustion engine (an engine very similar to the one used in a car, just bigger). This started doing this about twenty years ago. Back then, technologies for generating renewable electricity were much less advanced than they are today. Since then, there are plenty of other ways to generate renewable energy.”
“The process of producing electricity from biogas is not efficient at all. The business case only still exists because of the subsidies that governments give for it. Those cash flows will probably stop soon because it is no longer profitable,” Pauletto says outlining the future. “We are providing a new technology so that farmers are able to convert biogas into renewable hydrogen.” This way, the biogas is upgraded to a product with a high level of added value, like renewable hydrogen, for a more sustainable future. What’s more, Sypox instantly has its first customer base for their technology.
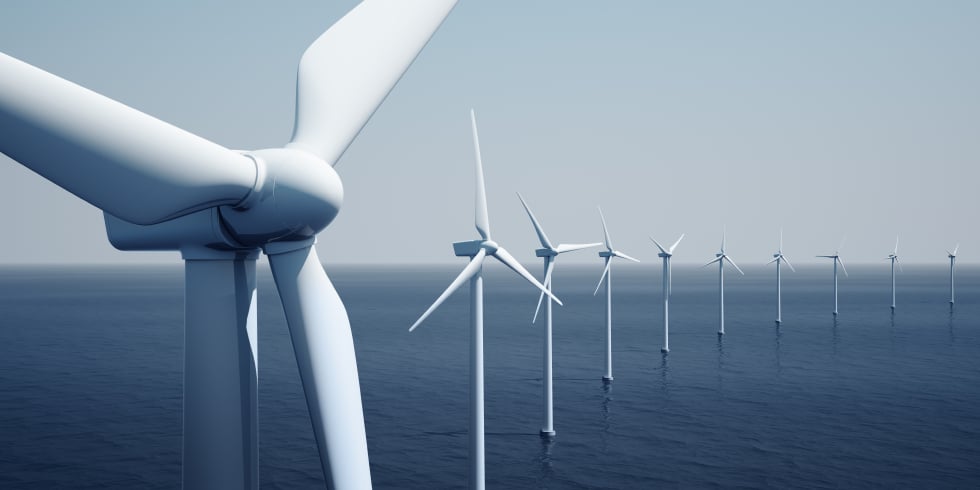
Decentralized hydrogen production
“The largest plant we have made so far produces fourty kilograms of hydrogen per day. The plant still needs to be two to three times bigger. Then companies will be able to use it,” he adds. By way of comparison, one kilo of hydrogen is roughly equivalent to driving a car hundred kilometers. The hydrogen generated by Sypox is suitable for use in mobility, for a start. The decentralized approach is ideal for this, Pauletto contends. “The use of hydrogen poses a few problems. Transport and distribution are very challenging because it has to be transported under high pressures.”
He cites Germany as an example: “There are now ten thousand biogas plants over there. They are evenly distributed across the country. If those biogas plants would now start producing hydrogen, you’d immediately have a good distribution throughout the country and you wouldn’t have to transport hydrogen over long distances.”
Scaling up
Sypox is currently working on a European project on a plant that can produce 400 kilograms of hydrogen per day. “In this project, the hydrogen that is produced is compressed and used at the plant straight away,” says the CEO. In addition to this project, Sypox itself is also carving out new paths. For one thing, they are setting up a pilot plant on the Brightlands Chemelot Campus. “The infrastructure needed there is already in place. Moreover, it’s a good location to make connections with the chemical industry and other partners and customers.”
Sypox is not the only company working on electrifying processes within the chemical industry and producing sustainable hydrogen. Pauletto: “Different companies, universities, and organizations are working on different technologies to make this happen. There are also so many different processes in the industry. Of course, a certain technology might be suitable for a range of applications, but I think having a variety of solutions is really important. Eventually, various solutions will hit the market and I am confident that Sypox’s technology will be one of them.”
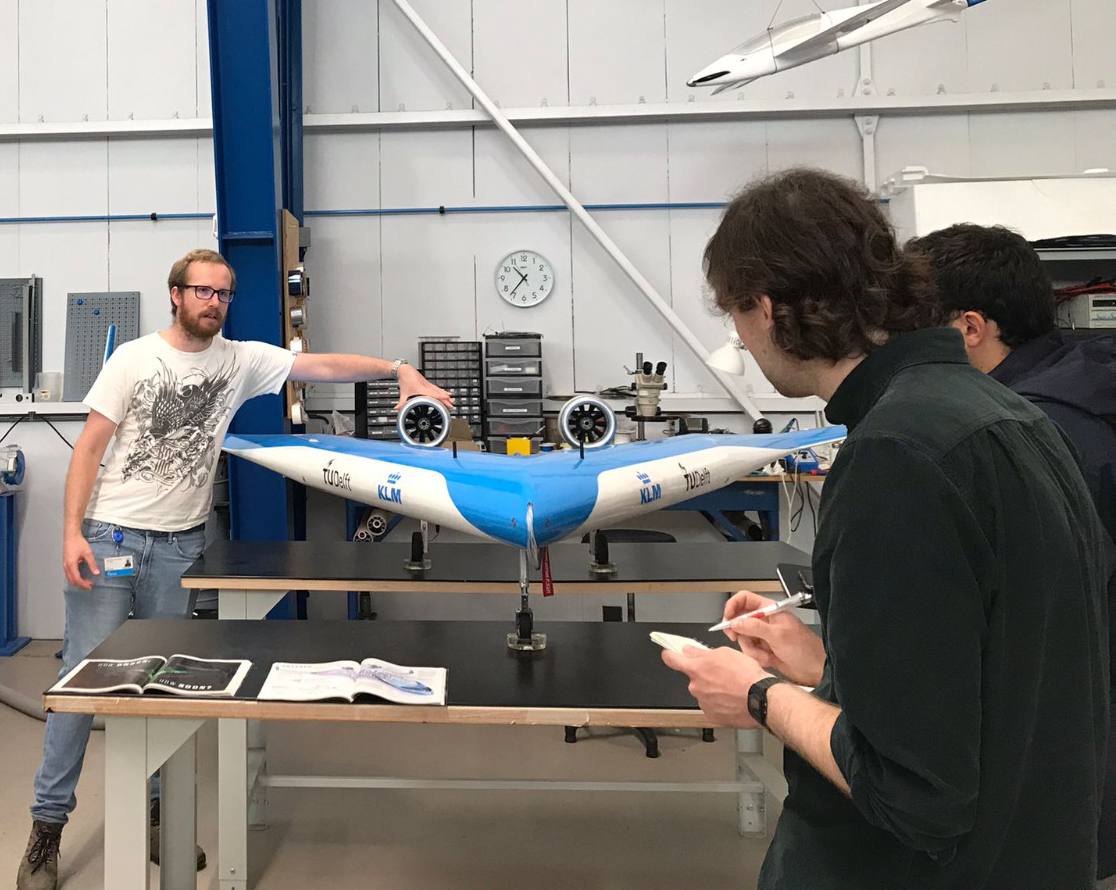