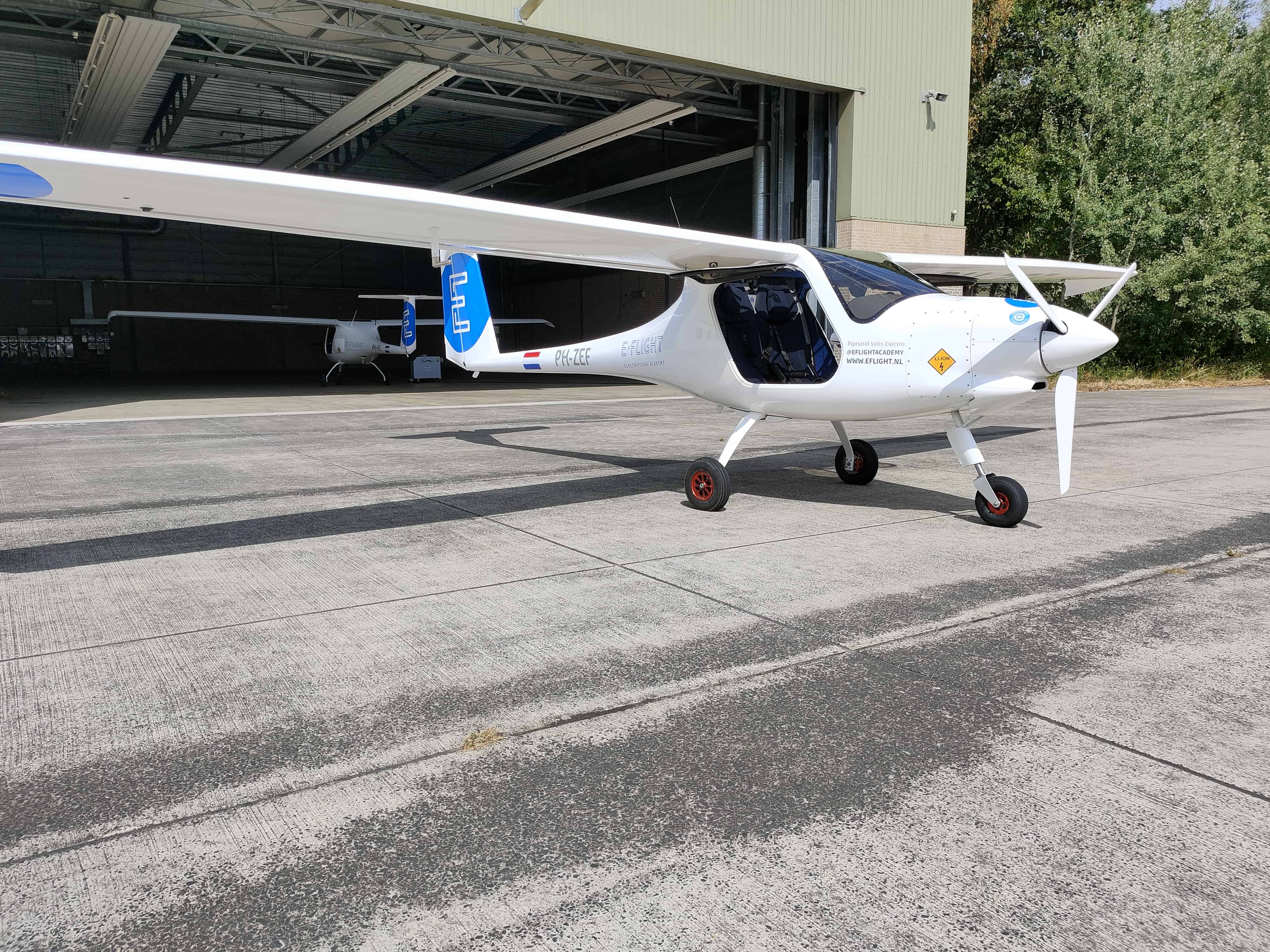
The aviation industry still has a huge lag to overcome in terms of sustainability. In 2020, the Dutch aviation sector emitted 7.6 billion kilograms of CO2. The more kilos that are released into the air, the higher the amount of CO₂ emissions. In other words: the lighter the aircraft, the lower the emissions. The Enschede-based ThermoPlastic Composites Research Center (TPRC) conducts research into the use of thermoplastic composites for the construction of aircraft.
Already half of the weight of the latest Boeing and Airbus airplanes is attributable to composites. Thermoplastic composites – fiber-reinforced plastics – are lightweight, strong, easy to process as well as recyclable. In the transition to a more sustainable industry, that all sounds very promising. Yet much is still unknown about the physical mechanisms at play, especially when it comes to the bonds between different materials such as metal and thermoplastic composites.
Lightweight design for more sustainable transport
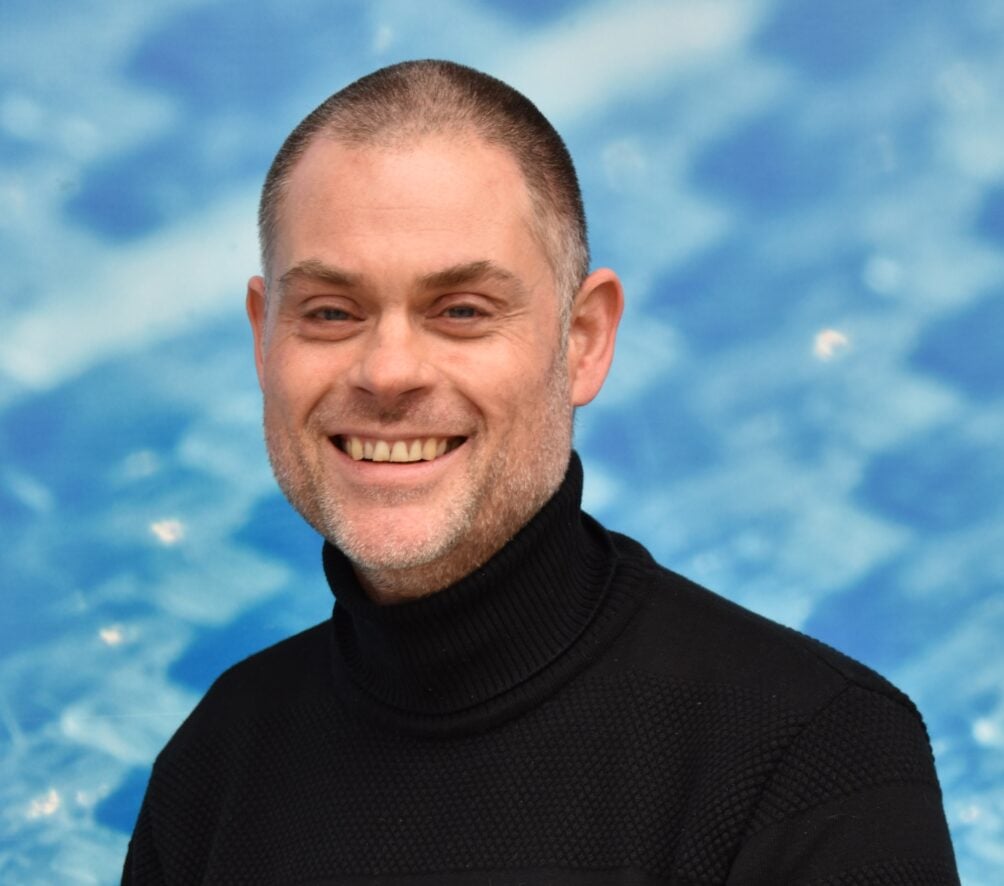
When technical director Sebastiaan Wijskamp started at TPRC in 2015, this research was still in an exploratory phase. “Back then, we were looking at how we could incorporate the material into parts of an aircraft that are subject to less strain. Now our focus has shifted to applications in the primary structure of heavily loaded parts. In recent years, there has been a certain shift in what is acceptable. An aircraft must be recyclable and manufactured in the most sustainable way possible. ‘What do we do with manufacturing waste?’ is now a considerably more important issue for aircraft manufacturers than it was a decade ago.” By now, it is a well-known fact that thermoplastics are more energy efficient when processed into an end product.
Meanwhile, the TPRC consortium is now made up of 21 partners from the Netherlands and abroad. About seventy to eighty people participate in the biannual Technical Advisory Board (TAB) conference. “You can see that this knowledge is steadily gaining traction. We are working with competing companies. We are able to do that because we are an independent research center that solves fundamental problems.”
“In recent years, there has been a certain shift in what is acceptable. An aircraft must be recyclable and manufactured in the most sustainable way possible. ‘What do we do with manufacturing waste?’ is now a considerably more important issue for aircraft manufacturers than it was a decade ago.”
Sebastiaan Wijskamp, TPRC
Rising interest
TPRC sprang from the Manufacturing Technology department at the University of Twente, which was active in plastics and more specifically in thermoplastics. Aircraft parts manufacturer Fokker and Toray Advanced Composites funded the research at the university. “This is how thermoplastics became a spearhead for Twente and why we have built up a treasure trove of specific knowledge and companies in the region,” Wijskamp explains.
When aviation and aerospace company Boeing also stepped forward, they decided to establish a joint research center. The partners are now investing together in research that they would otherwise have had to conduct separately.

Research on the properties of thermoplastic composites ©Erik Brinkhorst
Sustainability is attracting more and more attention. Nevertheless, Wijskamp has noticed a disconnect between fundamental research and application. It takes time to actually turn all the knowledge gathered by TPRC into large-scale applications. “That works best in places where airplanes are actually being built. But, with companies like Fokker and the expertise of the University of Twente and Twente Airport, we do have a really solid ecosystem. Both on a national and an international level. Kennispark Twente, of which our research center is a part, exudes that as well. We all stand to benefit from that. We are all doing each other a favor in terms of knowledge and progress.”
H2 Hub Twente
Fuel is another key focus area in the transition to making aviation sustainable. H2Hub Twente is a physical base where business owners and educational institutes work together on research and development and applications of hydrogen technology. Also in this case, the goal is for the 25 partners to pool their strengths to work on technical developments in hydrogen, so that no one has to reinvent the wheel themselves. There are currently around five projects underway, one of which is the H2 Big Drone-project.
Start-up Drone4, part of Machinefabriek Boessenkool, is leading the way. The name says it all: at the Boessenkool machine factory, they mainly design and develop machinery. “Drone4 is definitely a maverick,” Eelco Osse admits, he is the owner and CEO of the company. “We work a lot with farmers, in the design of electric tractors, for instance. They prefer to have as little soil disturbance on their fields as possible. So, then there is only one solution: the tractor has to be airborne.”
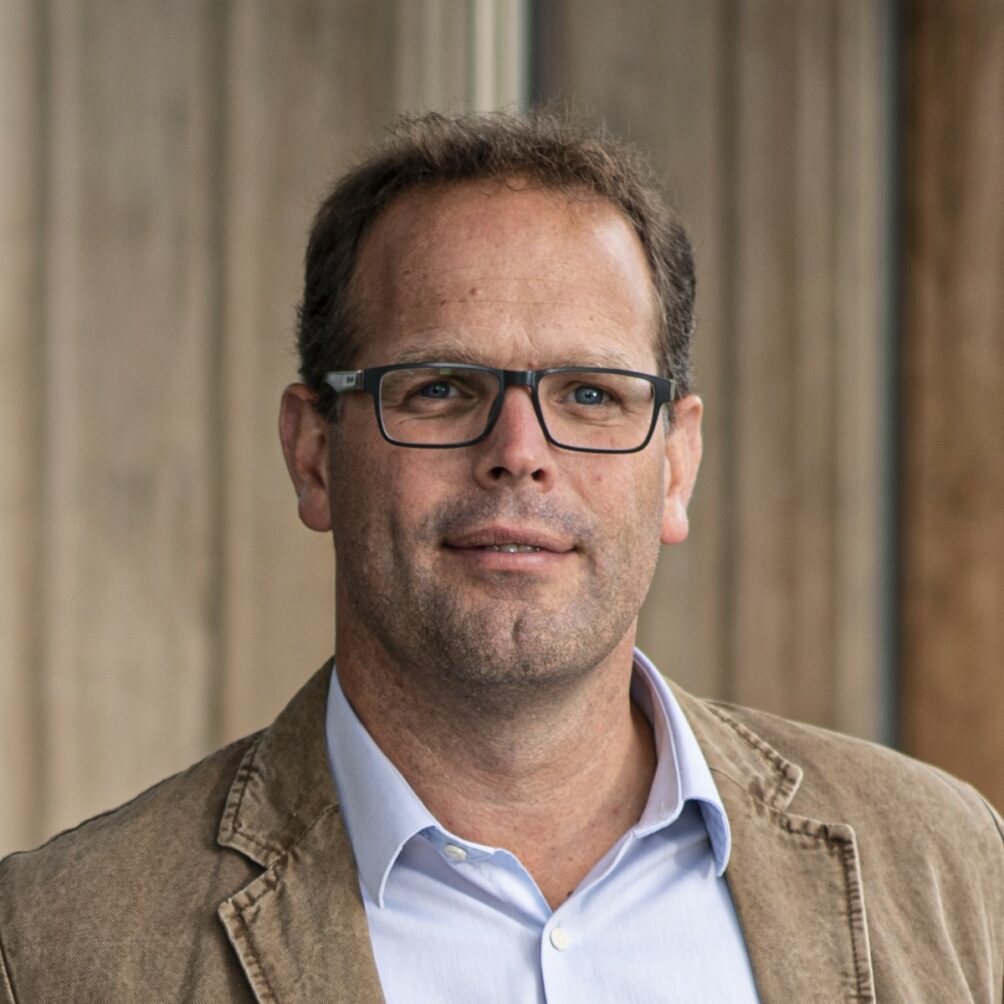
Hydrogen: cryogenic or ‘pressurized’
The drone also needs to be able to fly on hydrogen. Fossil fuels are actually “no longer an option” in this day and age, Osse points out, and battery development is progressing far too slowly. Also, hydrogen has a high energy density, which means it is not so heavy to transport a lot of energy that way.
Which is why the start-up, together with Saxion University of Applied Sciences, is developing a drone for agricultural uses, defense, transport and logistics that has a long range. The main focus here is on extending the radius of action.
The company has not yet decided whether to use pressurized or cryogenic hydrogen (extremely cold, liquid hydrogen). Under pressure, the volumes are still fairly large. By way of illustration, a drone currently has a diameter of about four meters; therefore, to carry enough fuel, a tank would have to be suspended underneath a drone that is twice its size. But cryogenic fuel also has drawbacks. It is more expensive and more high-risk.
Laws and regulations as major obstacles
One of the greatest challenges Osse faces is dealing with laws and regulations. “An electric version of the agrodrone has been ready in a technical sense for two years now. But nothing is allowed commercially speaking. On the one hand, we are ahead in terms of development, but at the same time, we are also lagging behind due to the regulations.”
According to European laws and regulations, only drones up to 25 kilograms can gain certification, while Boessenkool’s drones are already heavier than that without a load. Consequently, the company is at the mercy of use-case certifications. “We have to describe in detail to the Netherlands Vehicle Authority (RDW) what we intend to do with the drone. And as far as the regulations are concerned, we have not even tackled hydrogen as a fuel then, that phase still lies ahead of us. The hydrogen hub plays an important role because the bodies that set the rules are also seated at the table there.”
Twente Airport wants to be a testing ground for innovations in aviation
At Twente Airport, the foundations were laid for the region’s strong proposition for aviation. In the period between WWII and 2008, the airport was in use as a military airport. After the site was closed, it was bought by the Province of Overijssel and the Municipality of Enschede in 2010. Nowadays, it is known as the Technology Base. It has not managed to be used as a commercial airport for vacation flights, but in 2015 the decision was made to keep the airport open as a small-scale airport for business jets, the flying and gliding club, and the decommissioning of aircraft, among other things. Twente Airport opened as a civilian airport in 2017.
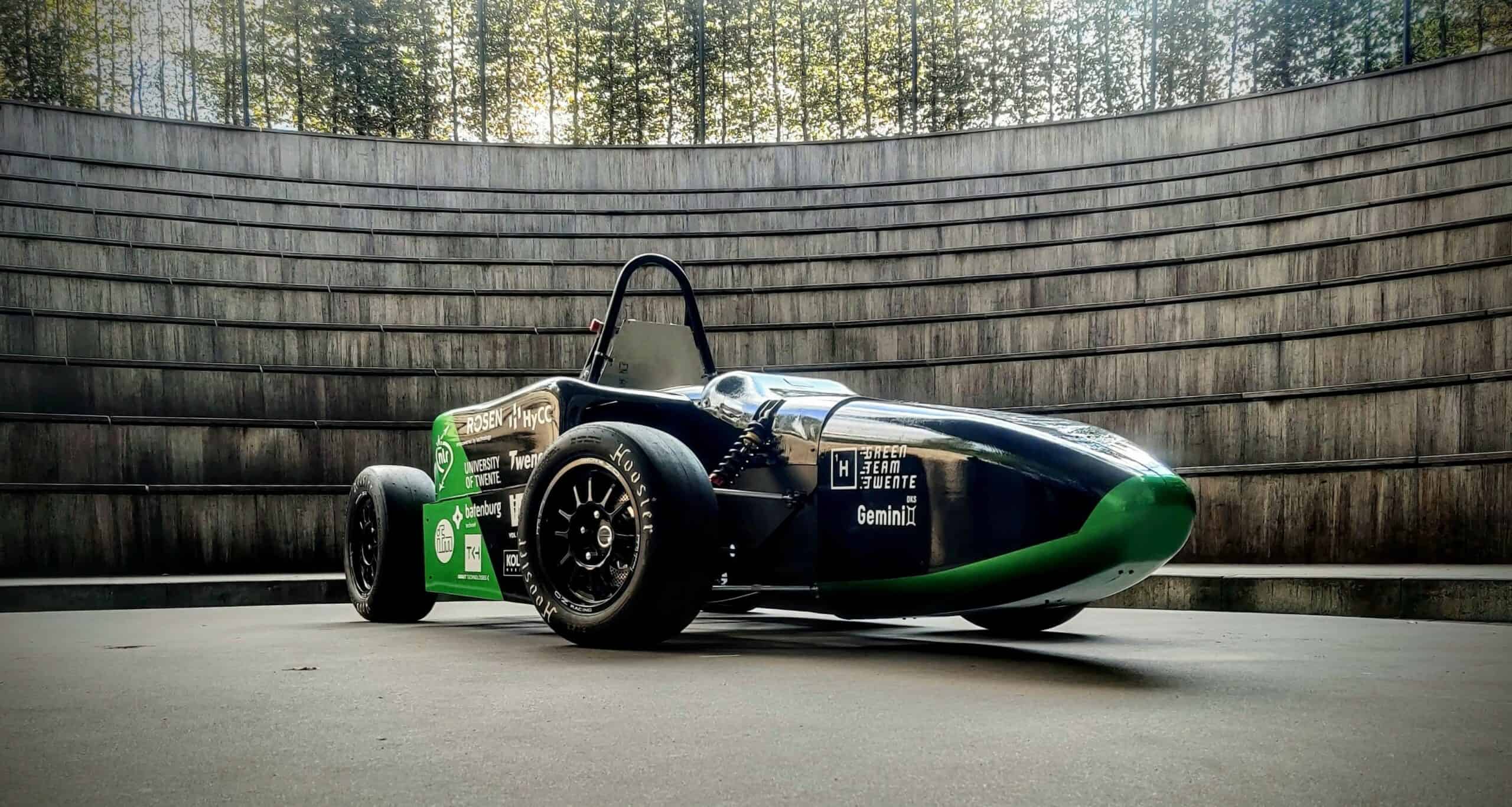
Technology Base
At the neighboring business park, Technology Base offers entrepreneurs the space and opportunity to develop innovative ideas, industrial research, test manned – and unmanned aviation systems and set up companies in the fields of advanced materials & manufacturing as well as safety & security.
A major advantage is that the site is completely closed off, you can only enter either according to a license plate number or with a QR code. “The other day, some students from Drone Team Twente from the UT tested their drone there. That didn’t go well, the drone crashed on the runway. But the great thing is that this can just be done without causing any unsafe situations for bystanders. The air traffic control system provides at least 24 hours’ notice, so even if there is a crash, there is plenty of time to clear the runway. There is literally and metaphorically plenty of room here for testing and experimentation,” says Marieke Vizée, communications advisor at Technology Base.
Technology Base has installed three thousand solar panels on top of its hangars. Because the airport was part of the Royal Netherlands Air Force for many years, it has its own independent energy network with ample capacity. Recently, the E-Flight Academy, which trains pilots to fly electrically, installed a mobile charging station there for a pilot project. According to Vizée: “Electric vehicles can now land at our airport and be fully recharged very quickly.”
“The other day, some students from Drone Team Twente from the UT tested their drone there. That didn’t go well, the drone crashed on the runway. But the great thing is that this can just be done without causing any unsafe situations for bystanders… There is literally and metaphorically plenty of room here for testing and experimentation,”
Marieke Vizée, Technology Base
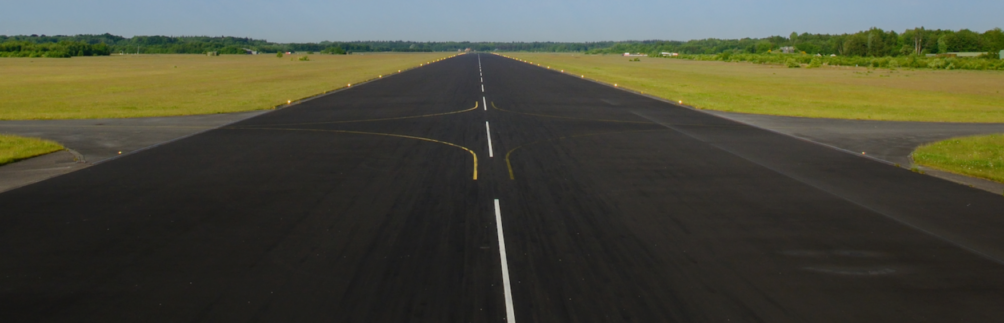
‘Regularly, something catches fire here‘
Space53 – the first test- train and development site for unmanned aircraft in the Netherlands – has also established itself on the site. This cluster of companies, government and knowledge institutions, which the drone of Machinefabriek Boessenkool is also a part of, works together with the fire brigade a lot.
“Twente is one of the first fire brigades to use drones as eyes in the sky when extinguishing fires. They use this additional information so that their efforts are more effective and efficient. Unfortunately, the laws and regulations currently do not allow drones to fly out of the pilot’s line of vision yet, but at Technology Base, experts from the fire brigade, Saxion University of Applied Sciences and University of Twente are already conducting extensive tests on unmanned flights with a sniffer drone. As soon as the legislation allows it, the fire brigade can send the drone ahead so that it can ‘smell’ whether hazardous substances may have been released, for example, without having to expose any firefighters to these,” Vizée explains.
The Battery Safety Lab tests batteries and battery storage systems at the Technology Base. “Storing energy still poses risks and must be done in a very safe way. That’s why they are also on our site. Something regularly catches fire here, but we are completely used to that,” Vizée smiles.
Cumbersome laws and regulations
But despite Twente Airport being completely closed off, the H2 Big Drone project is not allowed to make test flights there either with drones that weigh more than 25 kilograms. Osse: “If it’s not allowed there, where is it allowed? You have to start somewhere and gain experience.” He sees companies in countries with more flexible laws and regulations moving forward at a much faster rate. “It would be such a shame if we miss the boat. Twente has all the facilities to at the very least make more test flights. The only solution is to have more flexible laws and regulations.”
“If it’s not allowed there [Twente Airport, red.], where is it allowed? You have to start somewhere and gain experience.”
Eelco Osse, Machinefabriek Boessenkool
Vizée agrees with this. “Our location lends itself perfectly to these kinds of experiments and could actually help to relax the laws and regulations. There is plenty of room at our location to conduct test flights with the H2 Big Drone. Tests can be carried out here under realistic conditions until they prove that it can be flown safely. If something goes wrong during the test phase, then there is no need to worry. Twente Safety Campus is also housed on our grounds. They are specialized in fire safety, also when it comes to extinguishing hydrogen, which is relatively new.”
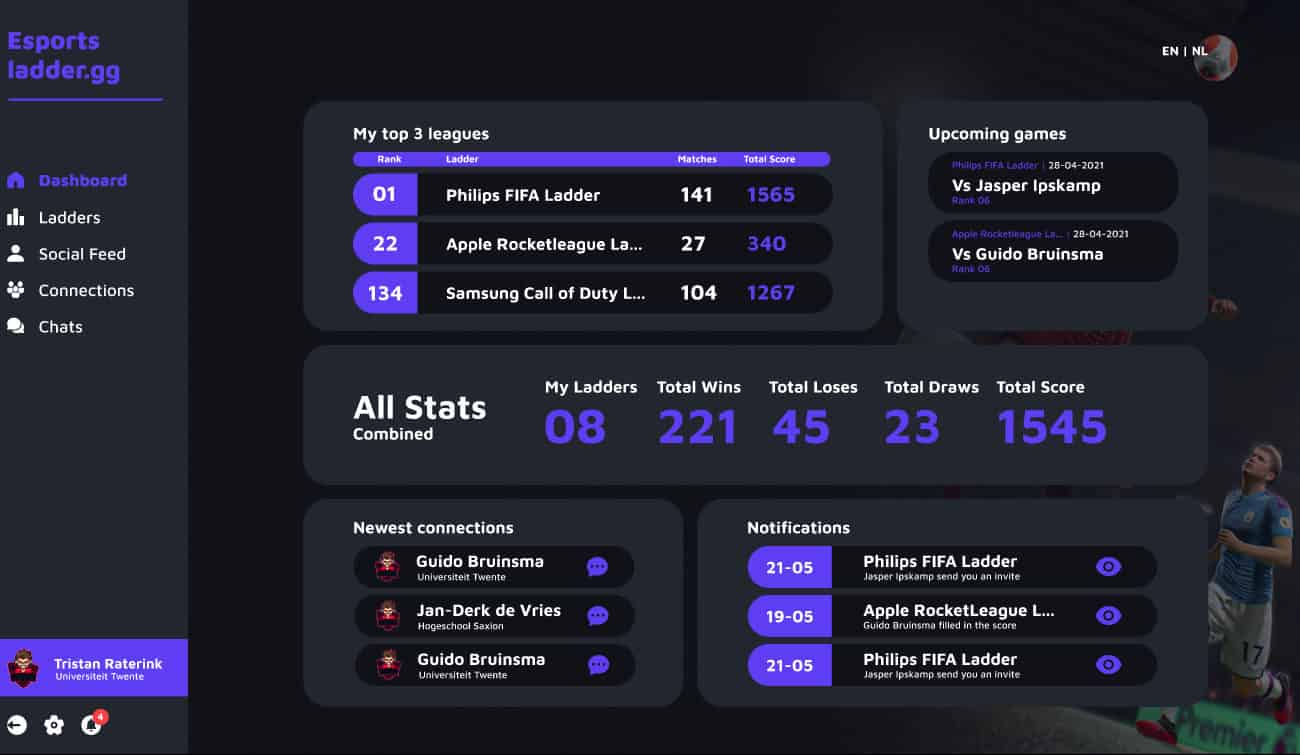