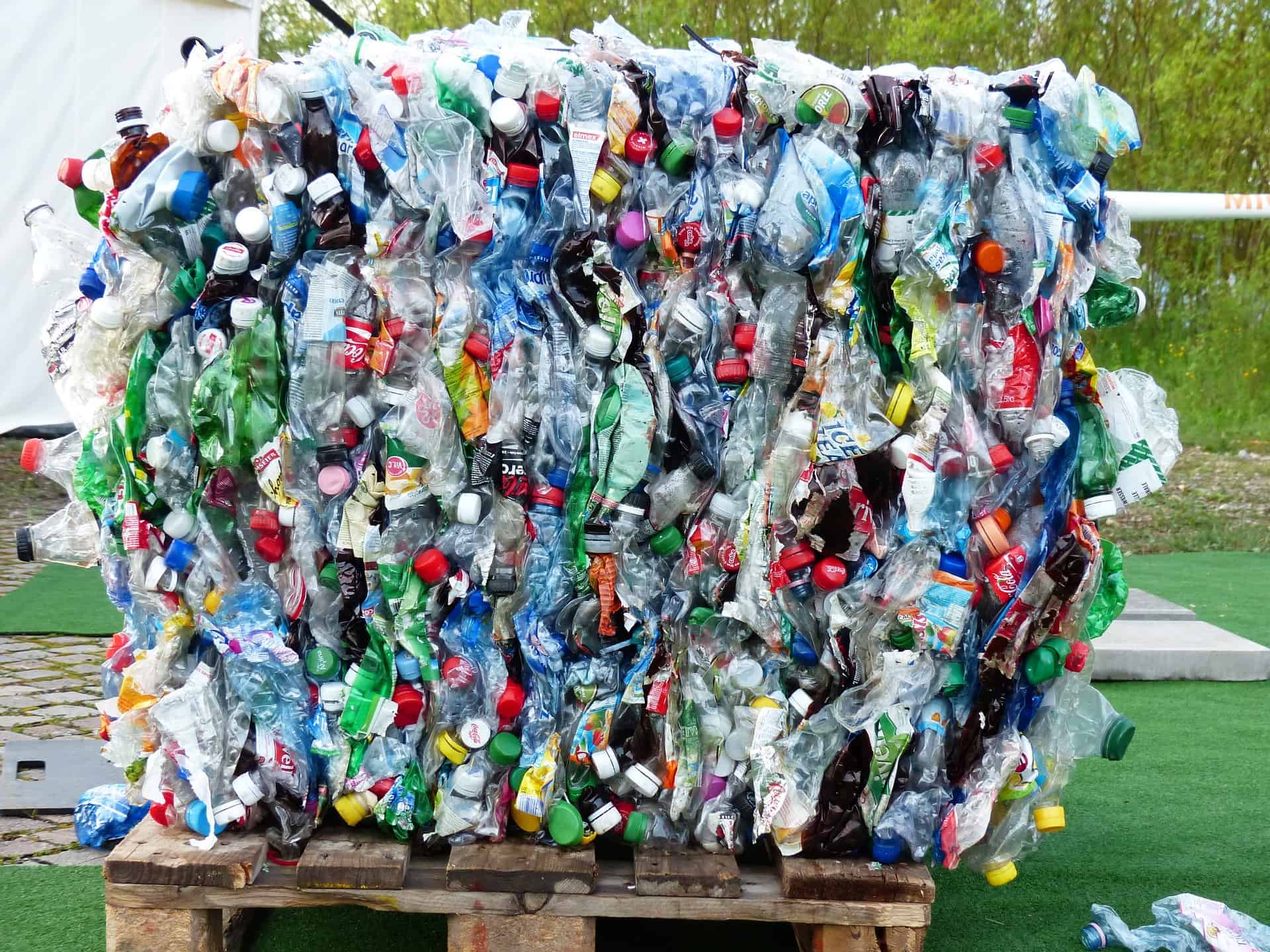
With a view to achieving a circular economy, the EU wants all plastic products to be made up of at least 24 percent recyclate by 2030. At the moment, the lion’s share of recycling is done using mechanical recycling technology. This entails collecting, sorting and crushing plastic waste into chips, after which they get cleaned. At the end of this process, clean plastic flakes are converted into pellets that form the basic raw material for new products.
Huge adverse impact of recyclate on quality
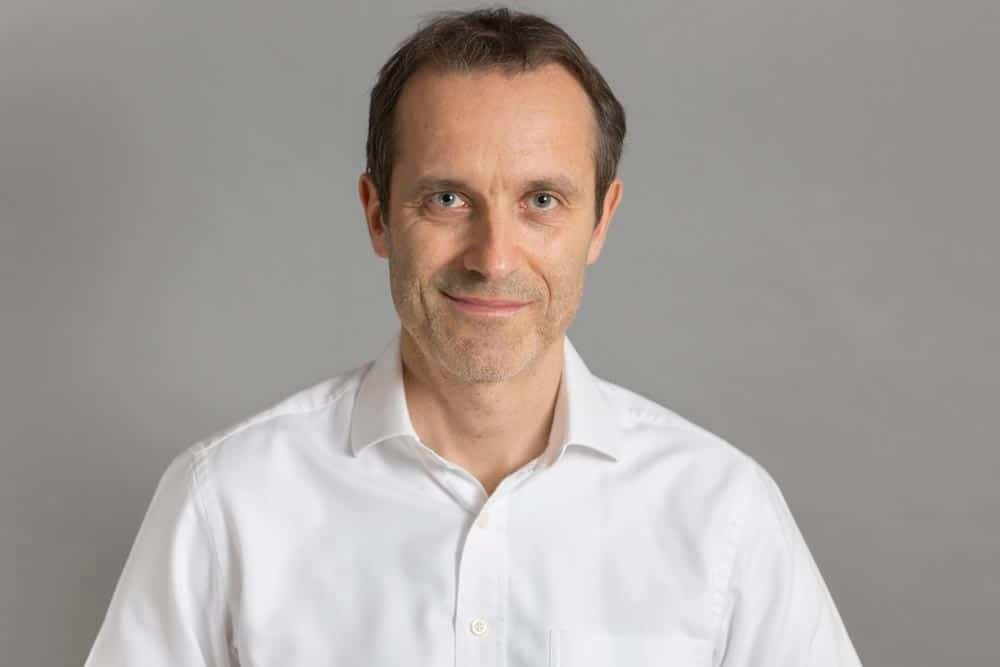
Norbert Fraunholcz, a raw materials technologist by trade, cannot see us meeting those EU directives just with this kind of technology. “Mechanical recycling is the cheapest way to go about it, but it has severe limitations when you look at to what extent it is capable of separating and removing contaminants from plastics. We definitely need this technology, but it is often not up to the task of meeting the guidelines for products that we need high-quality plastic for.”
By way of example, he cites a coffee maker that has a housing made of plastic. Currently, this is fabricated in most cases with hundred percent brand new plastic that has a high and consistent level of quality. “If you say, I want to replace some of the virgin plastic for recyclate, the overall quality tends to deteriorate very quickly. With 3 percent recyclate and 97 percent new plastic, you can dilute any contaminants. But, if you switch from three to thirty percent recyclate, that has a huge adverse impact on the quality, even though those figures are the ambitions of the EU. So other, more advanced technologies have to be applied.”
“If you switch from three to thirty percent recyclate, that has a huge adverse impact on the quality, even though those figures are the ambitions of the EU. So other, more advanced technologies have to be applied.”
Norbert Fraunholcz
Review of all available technologies
In 2018, Fraunholcz reviewed all the available recycling technologies – mechanical, chemical, solvent-based and biological. He then looked at applications for consumer products that are made of high-performance plastics, such as cars or electronics. Right now, around two to three percent of recyclate is used in these product categories. “That has got to be ten times as much. A huge challenge, especially for high-value plastics that have high standards of quality. For underground pipelines, the specifications the plastics have to meet are understandably much lower than for an automobile.”
Solvent-based recycling
Two-and-a-half years later, Fraunholcz is CEO of ReSolved Technologies. The name of his company implies which technology emerged from the competition as the most promising. “Solvent-based was an underrated technology, whereas I saw tremendous potential in it.”
Solvent-based recycling builds on mechanical recycling, Fraunholcz goes on to explain. Sorted plastic is dissolved in a liquid. The plastic solution that then forms is a homogeneous liquid which is much easier to purify and can be done more effectively in this form than plastic particles of various sizes and shapes that mechanical recycling makes use of.
Pure recyclate through selective dissolution
“Another advantage is that you can dissolve the plastic selectively. Paint or glue residues, for example, do not dissolve, and you can easily filter them out. That way, you end up with recyclate that has a much higher degree of purity.” Whereas with mechanical recycling, the cleaner the input material is, the purer the final product becomes, with solvent-based recycling this is much less the case. This technology is also capable of turning a dirty, low-grade product into a high-grade recyclate.
Where the market was not willing to pay the price for high-grade recyclate five years ago, Fraunholcz is seeing companies understanding more and more that mechanical recycling alone will not get them to where they need to be. “In the past, the price of recyclate was always lower than that of virgin plastic, but in recent years, we have witnessed a run on recyclate as more and more companies want to embrace circularity. So much so, in fact, that there is now a shortage in many markets, so the price of recyclate is often higher than that of virgin plastic. The greatest challenge now is to get advanced recycling technologies off the ground. There are still too few plants adopting these kinds of technologies. The thing that we need to do is to scale up.”
Future plans
Earlier this year, ReSolved Technologies received a Top Sector Energy grant from the Netherlands Enterprise Agency (RVO) that enabled it to set up a laboratory-scale test facility. Next year, Fraunholcz hopes to commission a pilot plant that will be capable of processing 25 kilograms of plastic per hour. To do this, he is hard at work raising investment. The plan is to build a demo plant by 2024 with a capacity of 4,000 tonnes per year.
Carbon & Circularity Credits
Apart from that, the entrepreneur plans to develop a credit system for the plastics industry over the next two years. Carbon credits are used to offset the CO2 emissions of one economic activity with credits from another economic activity. Take aviation as an example. This sector uses the fossil fuel kerosene. To offset that, they purchase carbon credits from a biomass project in Africa, for example, where CO2 is removed from the air by planting bamboo, among other things. This may sound like a great concept, but critics feel that by doing this, companies lack enough motivation to cut down on their own emissions.
No such system for raw materials exists as yet. “With recycling, you have a double advantage. It helps make products more circular and reduces CO2 and other greenhouse gas emissions.” So, he came up with Carbon & Circularity credits. These credits should be issued AND purchased within the same value chain.
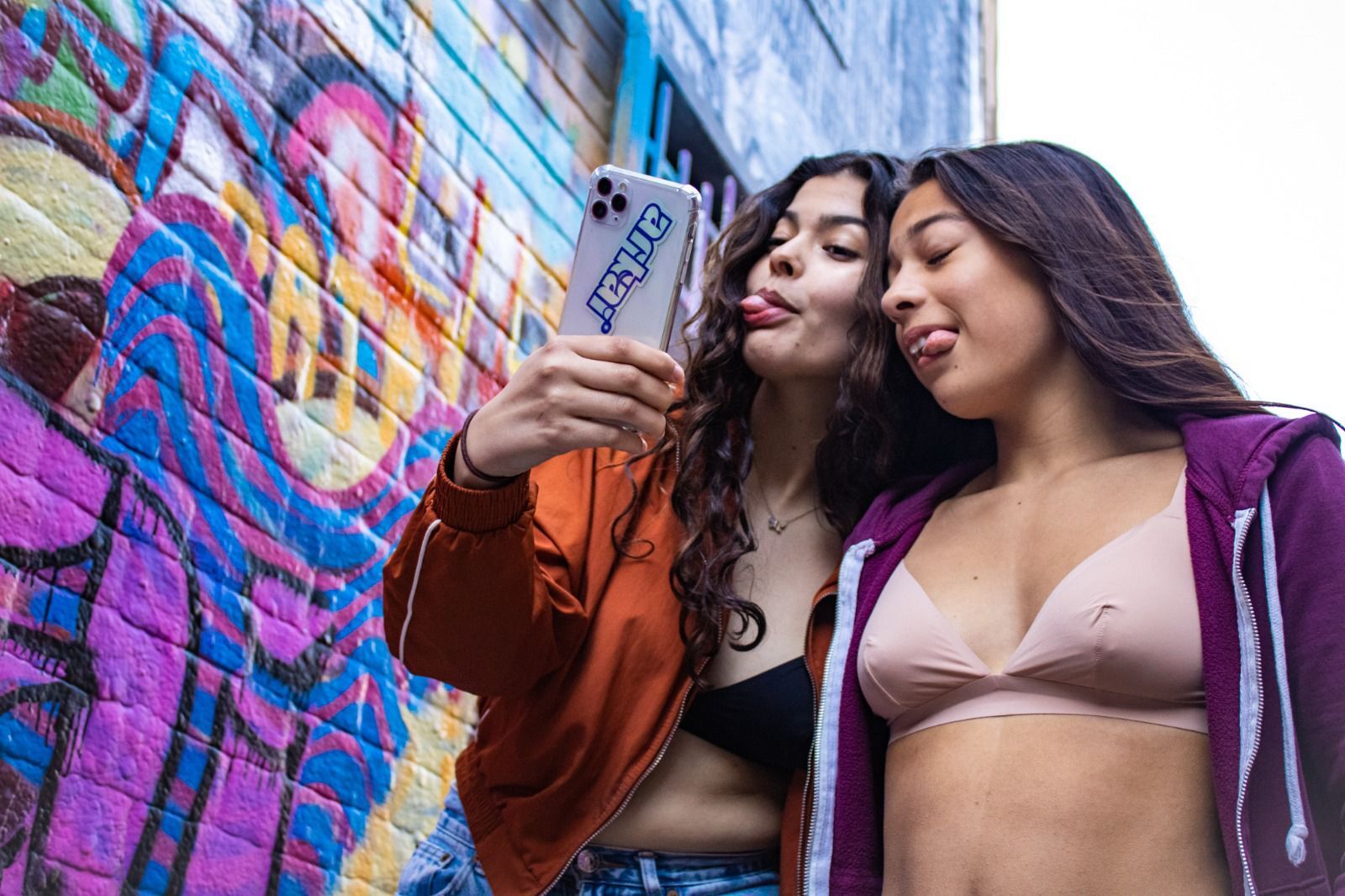
“The savings achieved and improvements in circularity are beneficial for the entire plastics value chain. The criticism that credits do not provide incentives to do better does not apply here. We can use them to get all kinds of projects off the ground. For instance, think of very low-grade plastic whereby its reuse is not profitable at the moment. We can then say to companies: if you pay us through C&C credits, we can also recycle those streams and feed them back into the plastics cycle.”
From Hungary to Delft to Geleen
Throughout his entire career, the entrepreneur has been concerned with waste streams. Thirty years ago, he left his homeland of Hungary for the Dutch city of Delft, where he earned his doctorate on plastic waste streams. Fraunholcz is now fluent in Dutch and still lives near Delft, although nowadays, he can be found increasingly more often in Geleen.
“The Brightlands Chemelot Campus is the right place for my company to be. All the infrastructure and facilities are in place. We hope to build our pilot plant there next year. Even though we are not a chemical company, the proximity to the chemical industry is really important to us. Being stuck somewhere in an ordinary industrial area is not going to get us anywhere. We need people who are used to dealing with chemical processes and their safety standards.”