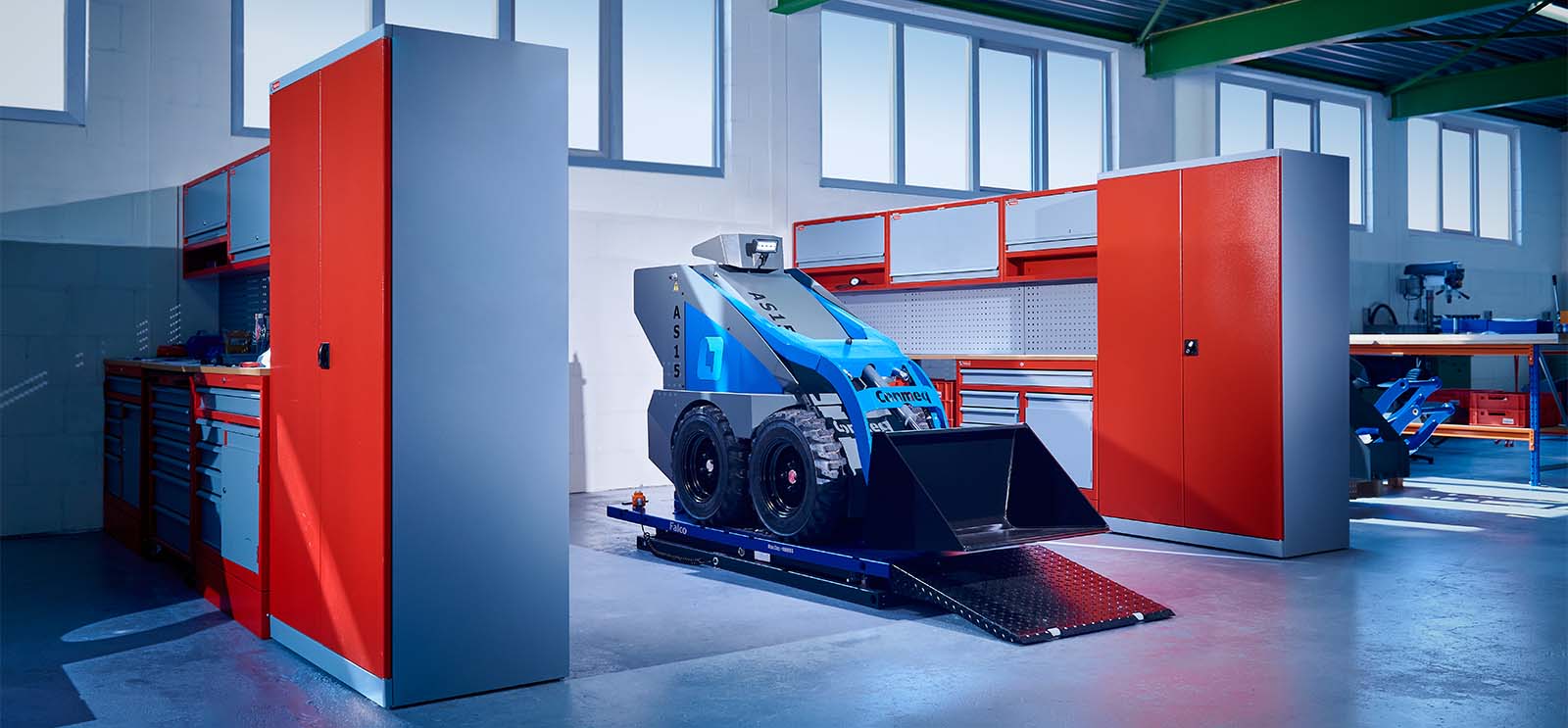
Conmeq developed from scratch an electric loader that makes physical work such as paving or demolition jobs much easier. To do this, in 2019 Conmeq sought cooperation with ELEO, which makes battery systems for loaders. ELEO will supply at least one thousand battery systems over the next three years. They have been manufacturing these loaders since 2020. Customers come from the Benelux, but “now we are really going into the European market”.
This has been made possible in part by a collaboration between Conmeq and Vermeer, an American machine manufacturer. Vermeer will handle distribution within Europe, Verkaik says. “That means a lot of sales are bound to follow. Therefore, enough has to be produced to meet the demand. Our batteries are also needed for that. Which is why we have officially laid down our collaboration in a cooperation agreement. From now on, we will be supplying batteries to Conmeq in a continuous stream.”
It is a fantastic deal for ELEO, Verkaik lets us know. “It shows that our product is well received. It also lays a good foundation for the coming years, because it guarantees good sales.” The company has started building a new factory where battery production capacity can be significantly increased to 500MWh, which is equivalent to about 10,000 battery packs. There is also room for high-tech R&D labs to develop battery technology further. Verkaik expects construction to be completed by mid-May 2022.
Penetration of electrification
The company traces its origins to the Storm student team back in 2014. There, the three founders, Verkaik, Jeroen Bleker and Bram van Diggelen gained experience with electric mobility. Two years later, the team rode an electric motorcycle around the world in eighty days. “A wonderful way to showcase to the world that it is possible to ride electrically everywhere.” That motorcycle adorns the central hall of the Automotive Campus in Helmond, where the company’s office and production hall are now located.
According to Verkaik, electrification has not yet penetrated the construction and agriculture sectors. “Apart from the fact that it’s a fairly conservative market, there are so many different types of machinery. There is no standard for electrifying them. Each machine is used in a different way. That in turn affects the battery pack. It’s often challenging to achieve a certain level of scale there.”
Conversion
The fact that the loader has been completely rebuilt has the added advantage that electric motors drive the wheels, Verkaik adds. “If you convert a diesel engine, there are still hydrostatic motors in it. Those are a lot less efficient and that means you don’t make as good use of the batteries that are in there.” That conversion is often done from an existing design of a diesel version, Verkaik explains. “That design is modified to fit a battery. It’s not the case that an existing machine is actually modified.”
According to Verkaik, the loader will pay for itself. “Because of the efficient use of energy, the costs for energy are very low. Also, the maintenance costs are almost zero.” This last point is due to the electric motors. “It is not just better for the environment, but it is also economically interesting.”
The loader has a load capacity of 500 kilograms and offers 70 different types of attachments. Four independent electric motors and the batteries power the vehicle. This accounts for a capacity of 15kWh. This enables a customer to use the machine all day, without having to recharge in between, Verkaik points out.
“You can use it for a variety of tasks from demolition to cleaning, or moving stones or bales of hay, for example. Depending on what the loader is going to be used for, a customer can add more or fewer batteries. “Someone who puts a demolition hammer on it uses a bit more than someone who moves a few hay bales every now and then.”
As a result of the collaboration between the American Vermeer and Conmeq, the machines are sold worldwide. “Although the focus remains on Europe,” Verkaik notes, “that’s where the demand for these types of machines is greatest.”