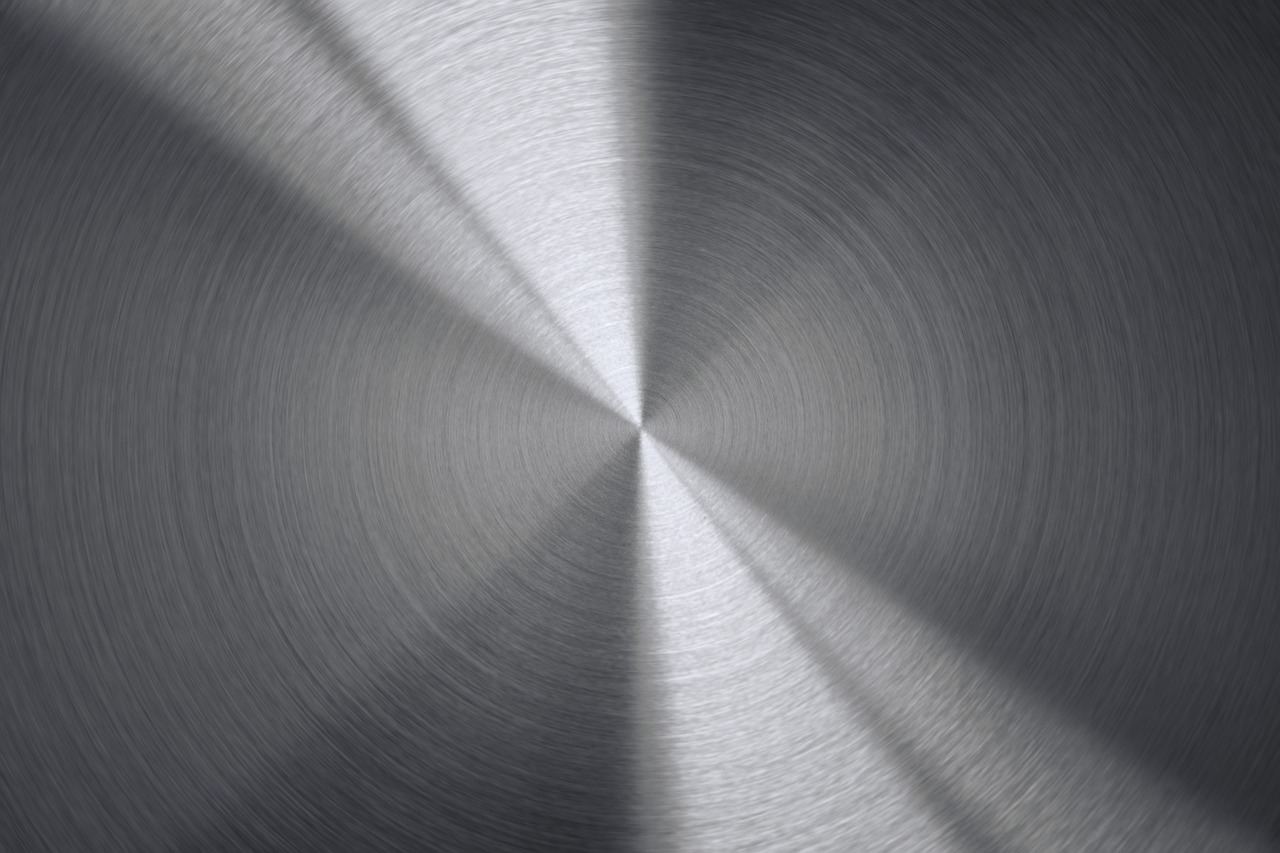
Dutch company Myne, formerly Reukema, is launching a digital recycling plant. Here, aluminium scrap is sorted by alloy by Artificial Intelligence (AI) and robots. This allows the raw materials to be used for high-quality products, the company said in a press release
- Dutch company Myne is launching the world’s first digital recycling plant, called Xorter, with AI and robots sorting aluminium, steel and copper waste.
- Xorter technology will also be applied to sorting copper, brass and zinc alloys in the future
- Myne is working with TU Delft on further innovations and the development of a prototype processing line to recover raw materials from electronic waste
In an economy where raw material scarcity is piling up, when metals are desperately needed to keep the economy going and for the energy transition, innovations like the factory (called Xorter) offer a concrete solution. Before the digital factory, high-grade raw materials were partially and unnecessarily disappearing into low-grade products such as gearboxes and engine blocks. In other words: downcycling. In the digital factory, scrap is used in goods that are in demand, such as cars. Material from which you can make a bicycle would rather not be used for a roadside post. For that, low-grade material is a better choice.
Technology leads to ‘green’ steel in future
Xorter technology will also be applied to sorting copper, brass and zinc alloys from waste in the coming years. Van de Poll: ‘So there is brass for water applications (free of lead in the alloy) and brass for locks, zips, screws. The latter has a different alloy and can therefore be used for other applications.’
To create the Xorter, Myne is working with TU Delft. Eventually, the aim is to also sort iron waste using the Xorter technology. Professor Dr Peter Rem, Professor of Resources & Recycling at TU Delft: ‘Iron waste also consists of different alloys. An iron can or car door does not have the same alloy as an iron beam in a building. Europe currently exports more than 24 million tonnes of iron waste outside Europe. Making this iron waste circular would produce truly green steel. Most of Europe’s steel is still made from iron ore in blast furnaces. This involves very high CO2 emissions and is therefore a huge burden on the environment. With the Xorter technology, we expect to be able to make high-quality steel from iron waste, reducing the negative impact on the environment by almost 90%’.
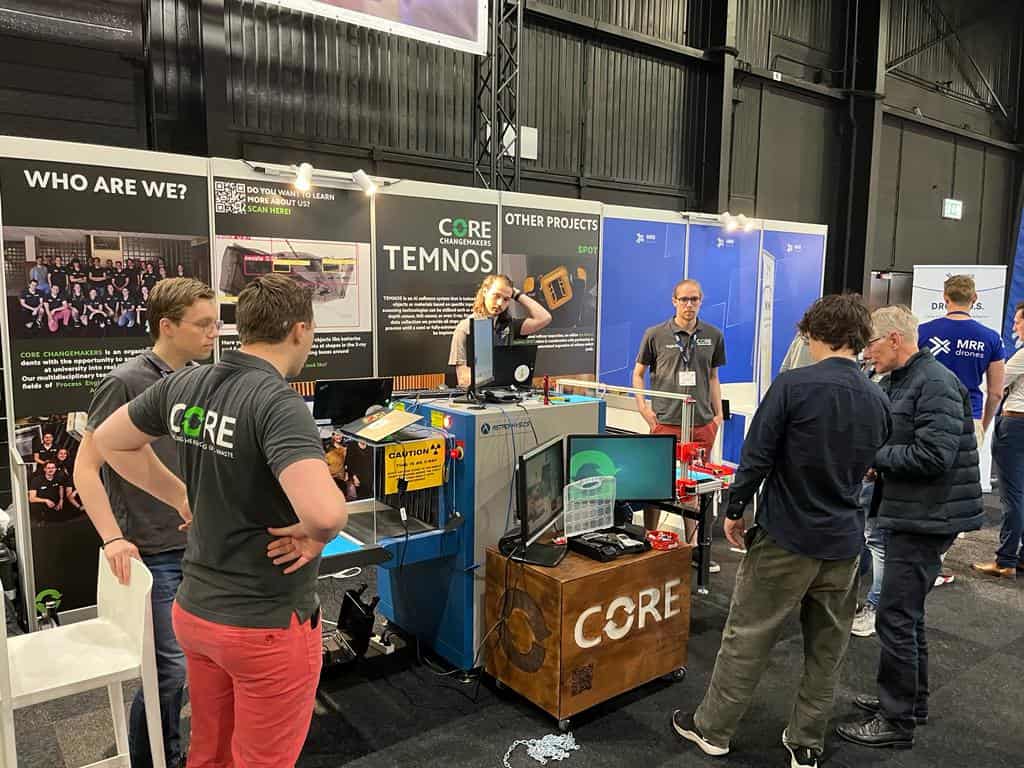
Scaling up
In the coming years, development and cooperation with TU Delft will continue apace. Van de Poll: ‘First we will make the Xorter technology robust in Harderwijk. Then we will scale up. The market is global and the problem of how to achieve high-quality circularity is topical and big. Europe alone could have hundreds of Xorters in terms of capacity.’