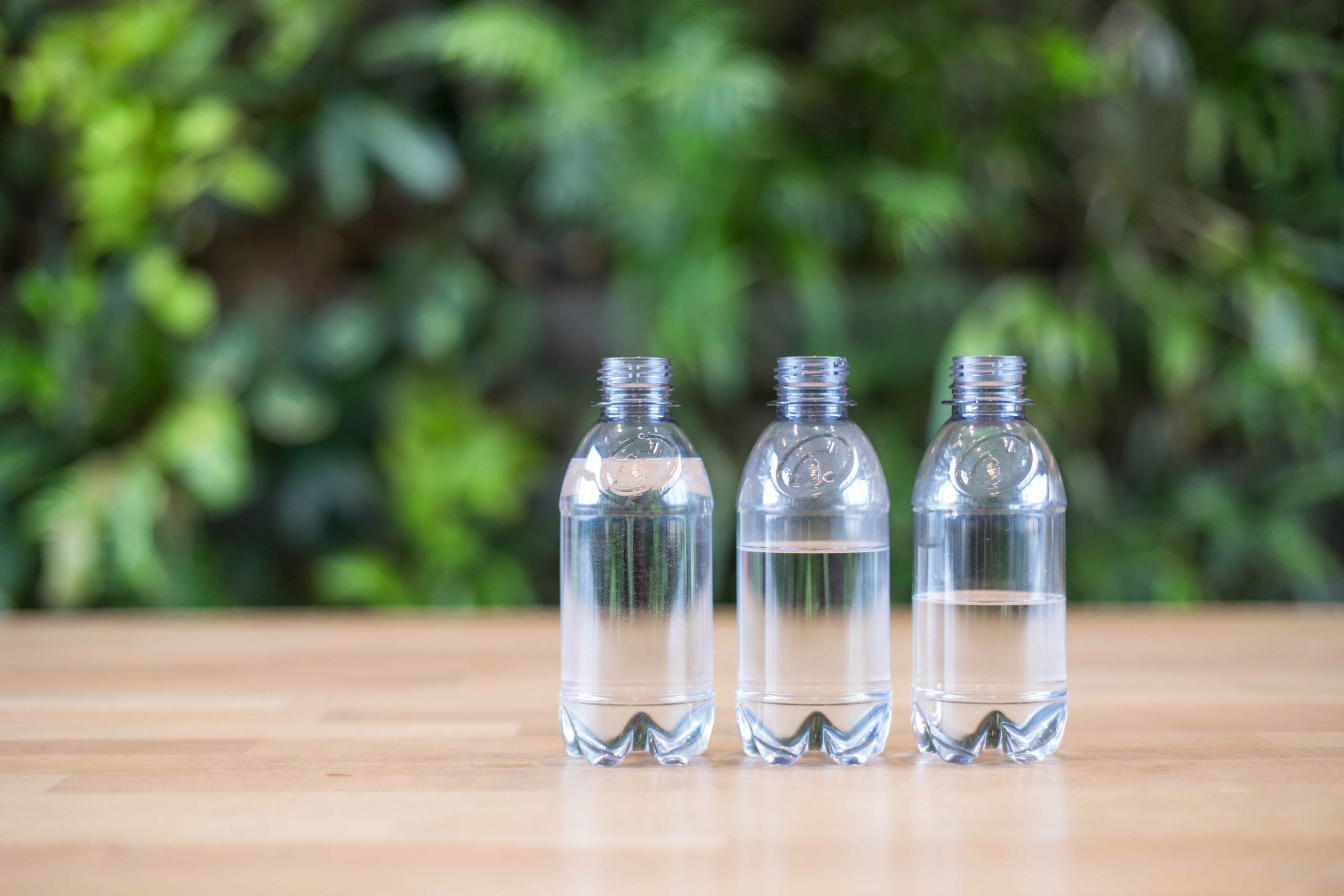
In two years time, Avantium plans to open the world’s first commercial FDCA (furandicarboxylic acid) plant in Delfzijl, The Netherlands. FDCA is the main building block for bioplastics. But it’s not quite that far yet. First, the company still has to make an investment decision on building the plant so that it can start operating in 2023. “We can’t wait until you can actually find PEF in the supermarket,” says Caroline van Reedt Dortland, Director of Communications at Avantium.
At the moment, petroleum is still indispensable in the production of plastic for bottles or packaging. But this is no longer necessary for making Avantium’s bioplastic PEF. Plant-based sugars from such sources as wheat and corn are needed for this purpose. “PEF is a solution to the plastic problem and has all the characteristics to become a real game changer,” says Van Reedt Dortland.
Both from a technical and commercial point of view, Avantium is ready to make this breakthrough. In recent years, the company has further developed PEF and carried out research into bioplastics, and also with customers. “This has shown that PEF is not only a sustainable alternative to conventional plastics such as PET, known from soft drink bottles, but it also has superior properties,” says Van Reedt Dortland.
Special properties
The bioplastic that Avantium has developed also has special properties. Van Reedt Dortland thinks that this new variant will eventually be able to replace the current packaging of PET soft drink bottles ” To ensure that PET has the right properties, nylon is often used in the inner layer of PET bottles, so that carbonated drinks, for instance, can be kept for a sufficient amount of time. But PET with nylon cannot be recycled well and goes straight into the incinerator. Nylon could eventually be replaced by PEF, so that these bottles would be more easily recyclable.” Should PEF products accidentally end up in the environment, the decomposition process is much faster than that of conventional plastics. “Whereas, for example, a normal PET bottle takes 500 years to decompose, a PEF bottle is already broken down within one year under compostable conditions.”
The bioplastic also features other advantages. For example, it has superior barrier properties. Products in PEF packaging have a longer shelf life compared to conventional plastics, such as PET bottles. “PEF lets less oxygen through than PET, so drinks last longer. And carbon dioxide doesn’t escape out of a bottle made of PEF as easily. As a result, the bubbles in drinks such as cola don’t escape as easily.”
From lab invention to commercial product
The technology to convert sugars into plastic was developed fairly recently by Avantium itself back in 2007. “It all started when our Chief Technology Officer, the brains behind the technology, grabbed a bag of sugar from the cafeteria,” says Van Reedt Dortland. “He experimented with that sugar and eventually developed PEF in the lab.” The product was then further developed and a pilot plant was set up in Geleen in 2011. ” There, we demonstrated that the technology works on a large scale and that it can be exploited commercially. The next big step is the commercial plant that we plan to build in Delfzijl.”
Next steps in the process
However, in order to take that next step, a number of preconditions still have to be met, including securing financing for the factory. The company is now in talks with banks, among other parties, for the final part of the financing. If everything goes according to plan, the PEF factory in Delfzijl will be operational in 2023. A total of approximately €150 million is needed to build the plant.
Another prerequisite that must be met in order for the plant to actually open is the signing of enough purchase contracts. A large part of these have already been arranged. Avantium has concluded purchase agreements with, among others, the Dutch bottler Refresco and the Japanese Toyobo. Beer brewer Calsberg has also partnered with Avantium to develop a special product: A paper beer bottle called the Green Fiber Bottle. “Paper by itself does not have the right properties to package beer. Yet it can give shape to a bottle and strengthen it,” says Van Reedt Dortland. “In the new prototype, the outside is made of recyclable paper, and the inside is made of a thin layer of PEF.”
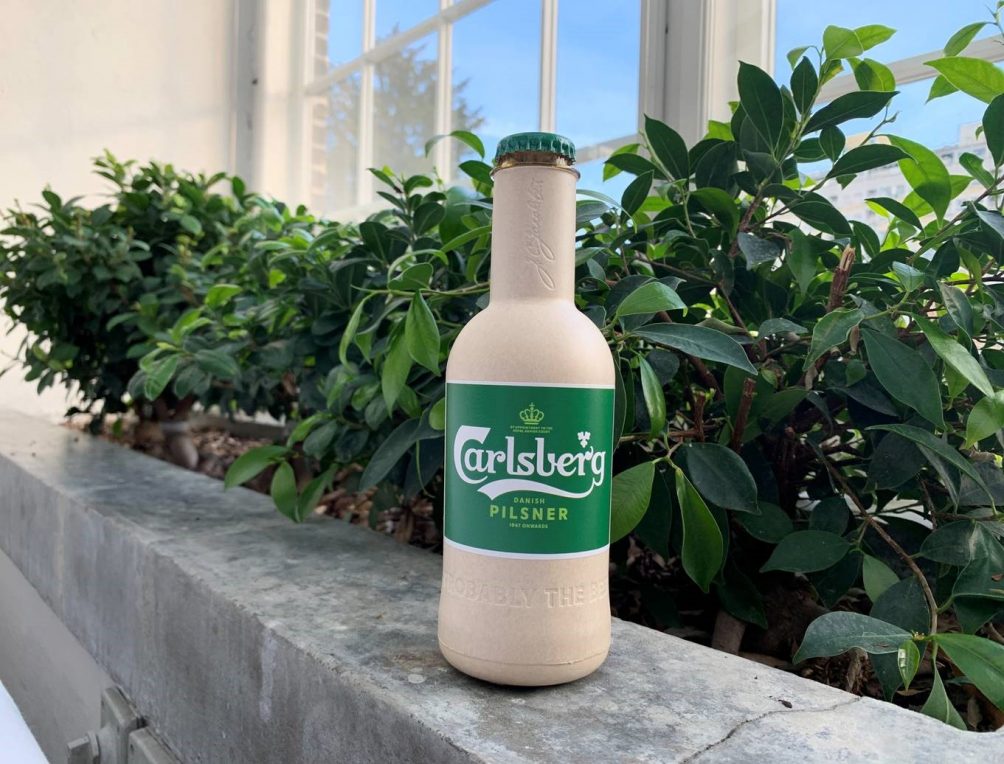
Two pilot plants in Delfzijl
In the past, Avantium built pilot plants in Delfzijl for two of its other technologies. The most recent one opened in 2019 at the Chemie Park Delfzijl. This pilot plant produces plant-based mono-ethylene glycol (MEG). This is an important step in commercializing the production of green MEG as a fossil-free feedstock for plastic materials.
That the province of Groningen has again been singled out for the construction of the commercial plant is no coincidence. “Groningen is a catalyst when it comes to green chemistry,” says Van Reedt Dortland. “In addition, the province of Groningen has ambitious goals where the reduction of CO2 is concerned.” For example, the province provided a funding package for the new plant worth €30 million in grants, shares and loans, which they used to help Avantium on its way.
Also read:
5G extends a helping hand to transport, healthcare and agriculture: Four future applications
Shortages in IT: ‘Even Archaeologists are being retrained’
Port of Lauwersoog on track to go green with ‘completely independent hydrogen supply chain’
The Groningen region is experimenting with hydrogen. ‘We want to scale up’
Old bus as a classroom: A sneak peak at the ‘creative Suikerterrein’ in the Dutch city of Groningen
Small, wooden windmill from Groningen incredibly popular: ‘Farmers down the road want one too’