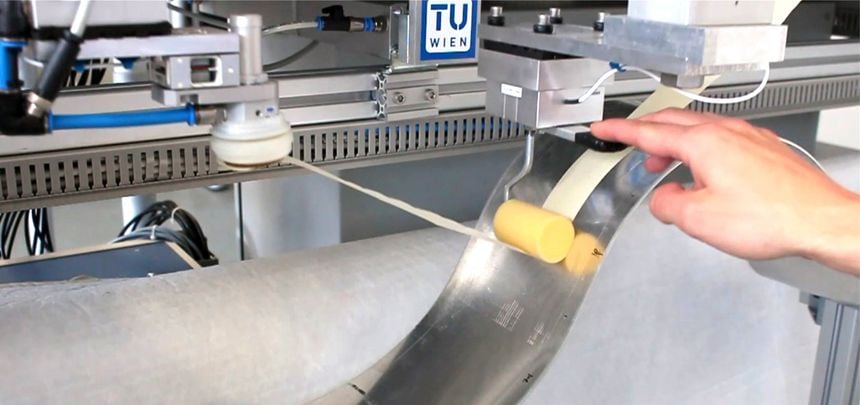
Robots can already do amazing things: They walk, dance and carry heavy loads. But when it comes to automating manual tasks that require dexterity and sensitivity, they still fail miserably. Particularly problematic is the processing of soft materials that are already deformed by gravity, such as adhesive films, leather or industrial textiles. These are materials such as those used in the automotive industry for lining fittings or in the steel industry for applying thin metal foils.
A challenging automation task
โAutomation is also always about understanding the situation at hand. Humans have this understanding, but it is generally not available to a machine,โ explains Professor Andreas Kugi, head of the Institute for Automation and Control Technology at the Vienna University of Technology and head of the Center for Vision, Automation and Control at AIT. When a person sees a wrinkle in a textile, for example, she knows exactly what to do with her hands to smooth it out. She effortlessly coordinates vision with dexterity and can adapt to different materials, shapes and structures. Robots are still a long way from these human capabilities. This is demonstrated, for example, by experiments in which robots are given the task of folding a T-shirt quickly without wrinkles.
Soft, flexible materialsโฆ
Kugi and his teams want to take this technology to the next level. Their research focus is not on mass production, but on highly flexible low-volume manufacturing; that is, automating specific functions that can be quickly learned and adapted to similar tasks.
Also interesting: Some hypes and missed opportunities in robotics
In cooperation with industrial partners, they have already had their first successes. They succeeding in gluing both straight and curved strips to a 3D bunny along precisely specified paths without wrinkles. The 3D bunny was chosen as a representative of a free-formed three-dimensional object. Such an object does not have a flat surface, such as a sphere or a cube, but curvatures in all spatial directions, such as a rabbit, a washbasin, a turbine blade, a shoe, and so on.
โฆand free formed objects
The challenge was to move the robot along the curved surface in such a way that all points along the path were reached without the tool rotating around the vertical axis. Such rotation would cause the adhesive strip to wrinkle. The basic research for this was carried out by the team at the Vienna University of Technology. The solution to the problem was provided by a new surface-based path control system that did not yet exist in this form.
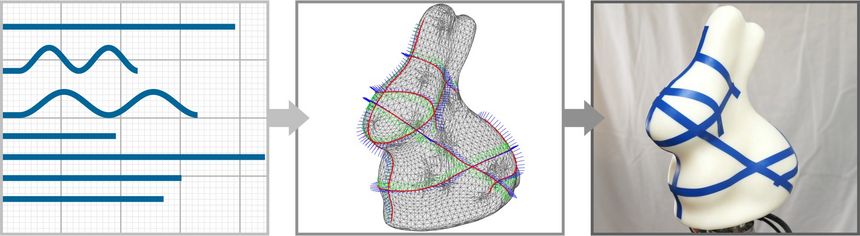
The researchers demonstrated the task prototypically on a 7-axis robot and a draping roller, with the draping roller mounted in a fixed position while the target object was moved by the robot. Thus, the 7-axis robot guided the 3D rabbit with all its curvatures in three-dimensional space along the draping roller in a targeted manner, whereby the designed control utilizes all degrees of freedom of the robot and tool to move in an optimal fashion.
Videos can be found at these links: https://www.acin.tuwien.ac.at/52f5/
https://doi.org/10.1109/TRO.2020.3033721
Fusion of sensors
This type of automation requires a variety of different capabilities from the robot. Depending on the size and shape of the object, its movements must be constantly adjusted and the forces exerted at the point of contact that are tangential (grazing) and orthogonal (perpendicular) to the surface must be specifically tuned. Here, the research teams work with different sensor concepts, including force sensors and camera systems. Choosing the right sensor technology and fusing the sensor data play a crucial role.
The professor and his teams are taking a holistic approach to research and approached the problem in a general way. He comments: โWe are dealing with arbitrarily curved, three-dimensional objects and want to do some work on their surfaces.โ In addition to bonding, this might include spraying, polishing, printing, sewing or cleaning.
Automation architecture
To achieve this flexibility, a suitable automation architecture must be designed. Subordinate control loops enable very simple and highly flexible motion planning along the surface of free-formed three-dimensional objects. Depending on the task, specific tolerances can be defined for the different grazing (tangential) and perpendicular (orthogonal) spatial directions with respect to the surface. When in contact with the surface, the desired stiffness behavior can also be set.
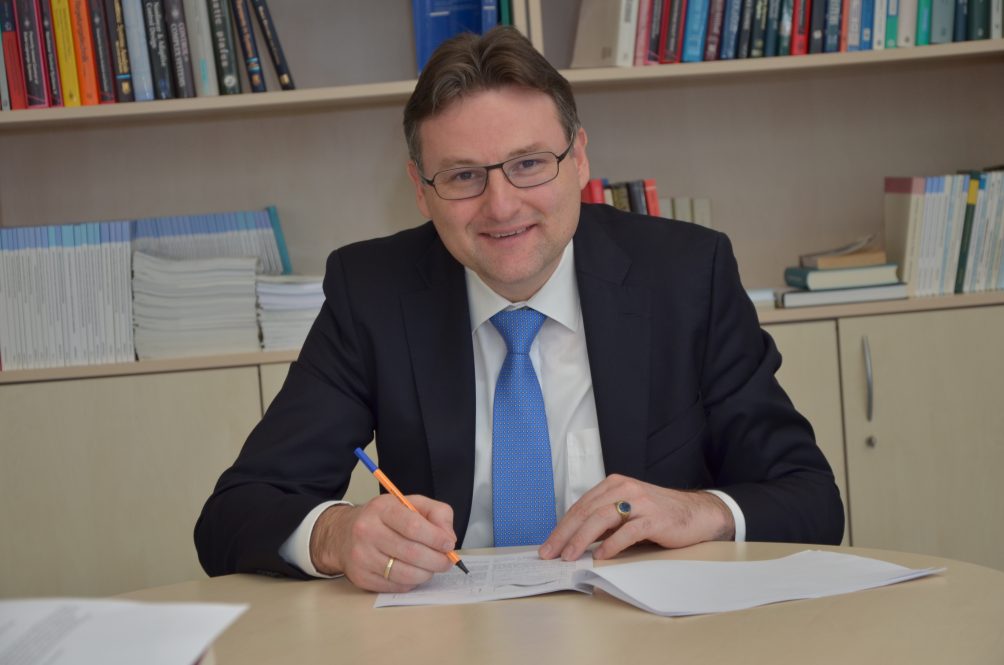
โIf we automate the spraying of surfaces, for example, we can specify not only the distance of the spray head from the surface but also the angle of the nozzle, including the tolerances allowed relative to the surface to obtain the most homogeneous spray layer possible on the three-dimensional surface.โ โ Professor Andreas Kugi
Cognitive layers
Currently, the research teams are working on the outer, cognitive layer of the automation architecture. This should make it possible to learn two things specifically:
- The distances and angles of the tool relative to the surface
- The contact stiffness for the respective applications.
This allows the desired processing tasks to be performed in the best possible way. When the robot has processed a certain number of parts, it has learned so much from them that it can apply this process to a new part that it has never seen before.
Demonstrate rather than program
Not all tasks can be performed by machines alone. Thatโs why the research teams are also working on methods that allow humans and machines to work better together.
โIf flexibility is required, then the question is how to teach the machine what to do as quickly as possible. One possible variation is for the robot to โask the human for helpโ when it canโt do certain tasks on its own.โ
โ Professor Andreas Kugi
With kinesthetic learning, the robot can simply be shown the task. This involves switching the robot to soft and compliant mode and guiding it along the surface, virtually showing it what to do. But for more complex tasks on surfaces of 3D objects, this can become very tedious. The researchers are therefore pursuing the idea of demonstrating new tasks with so-called โinstrumented tools.โ This is because if the robot uses the same tool as a human, the motion and force trajectories can be transferred to the robot very easily.
Coiling a rope
In one project, for example, the research team gave the robot the task of purposefully coiling a rope. It is not enough to simply specify the position in space; the tensile force must also be taught. The researchers therefore developed an instrumented tool that measures both how the human guides the rope and how much force is applied. The robot then mimics the entire process using an identical tool.
This form of automation is generally applicable to many industrial processes. However, it must be determined whether this is always the right approach, says Kugi. The key is to make the best possible use of the strengths of man and machine, as well as all available data from sensors and models from computer-aided design.
Also interesting: Sami Haddadin sees robots as human assistants