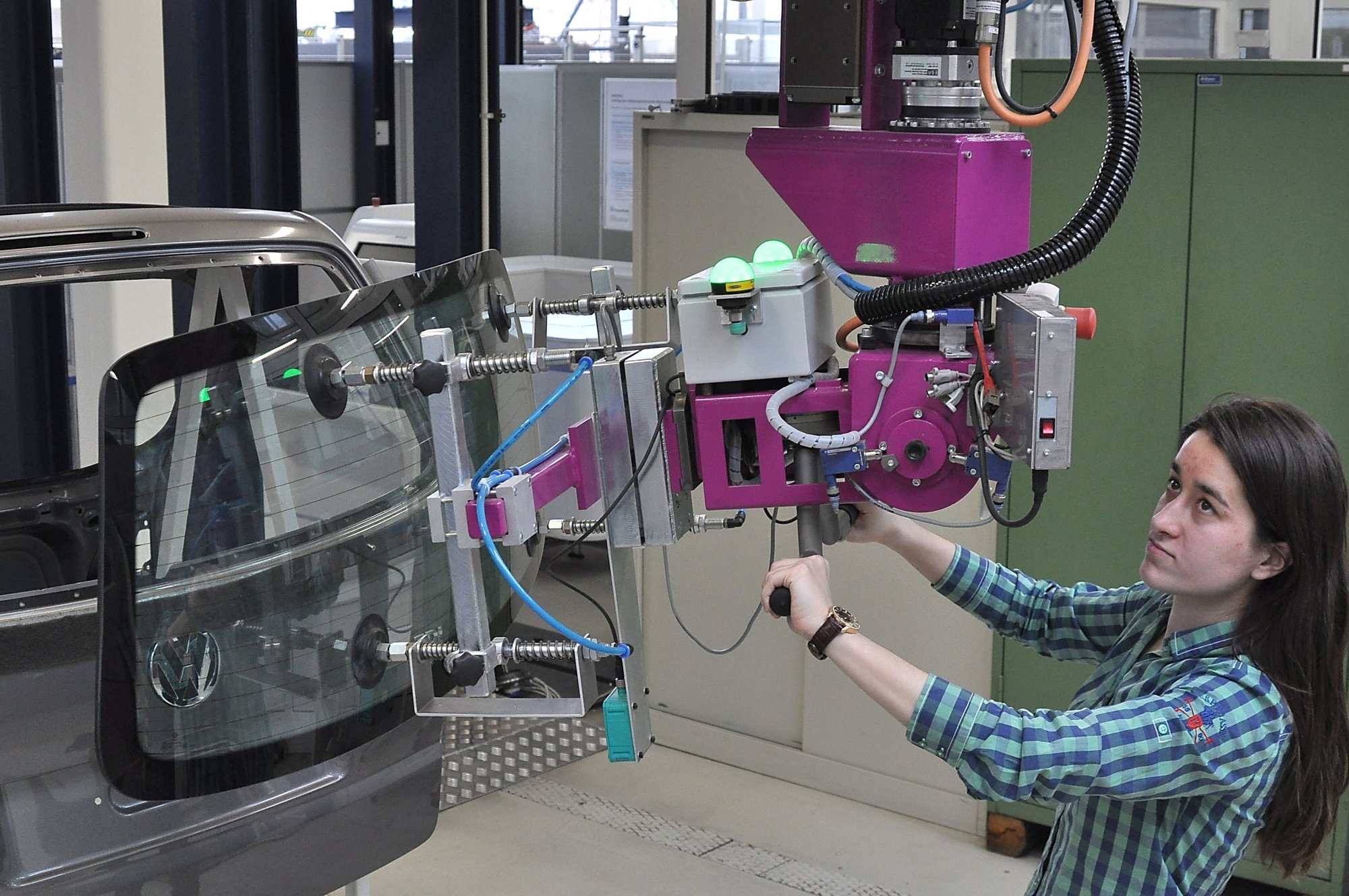
Die Industrie 4.0 verändert schon heute nicht nur die industrielle Produktion, sondern auch die Arbeitswelt. Digitalisierung, der wachsende Einsatz von lernfähigen Robotern und Systemen zur Steuerung von Produktion und Logistik lassen herkömmliche Berufsprofile veralten und neue entstehen. Allerdings fehlen immer noch Diagnoseinstrumente, um den sich vollziehenden Wandel genau zu beschreiben und Anregungen zum konkreten Handeln zu formulieren.
Frühzeitige Weiterbildung erhält Arbeitsplätze
Die Wissenschaftliche Gesellschaft für Produktionstechnik (WGP) will das ändern. Die WGP ist ein bundesweiter Zusammenschluss deutscher Professoren der Produktionstechnik. In ihrem jüngst vorgestellten Strategiepapier „Industriearbeitsplatz 2025“ stellt sie ein Analysemodell vor, das die verschiedenen Automatisierungsstufen untersucht und aufzeigt, wo Handlungsbedarf besteht. „Wir wollen als Zusammenschluss deutscher Professoren der Produktionstechnik unser Know-how einbringen, um diese Umwälzungen möglichst menschengerecht zu gestalten“, sagt Prof. Berend Denkena, Präsident der WGP und Leiter des Instituts für Fertigungstechnik und Werkzeugmaschinen IFW der Universität Hannover.
Ziel ist dabei, die Mitarbeiter eines Unternehmens möglichst frühzeitig durch Weiterbildung auf die Neuerungen vorzubereiten. „Unternehmen können dieses Modell nutzen, um den Automatisierungsgrad ihrer unterschiedlichen Produktionsprozesse zu bestimmen und daraus abzuleiten, wo Handlungsbedarfe bestehen“, ergänzt Prof. Peter Groche, Initiator des WGP-Standpunktpapiers und Leiter des Instituts für Produktionstechnik und Umformmaschinen (PtU) der TU Darmstadt. Außerdem erlauben die mit diesem Modell durchgeführten Analysen Rückschlüsse darauf, was sich in Bildungseinrichtungen und Ausbildungsgängen ändern muss.
Fünf Stufen zur Industrie 4.0
Für ihr Analysemodell haben die Wissenschaftler das Stufenmodell für das Autonome Fahren als Vorlage genutzt. Dabei beschreiben die einzelnen Stufen jeweils den Grad der Automatisierung, also den Entwicklungsstand auf dem Weg zur voll ausgereiften Industrie 4.0. Untersucht werden dabei die Material- und Informationsflüsse, der Anlagenzustand und die jeweiligen Produktionsprozesse.
Bei Stufe 0 hat die Produktionsanlage keine Verbindung zu anderen Systemen. Die Bediener sorgen für den Zufluss und Abtransport von Material sowie für den Informationsfluss ins übergeordnete Produktionssystem. Auf Stufe 1 ist die Anlage dann bereits mit einem übergeordneten Steuerungssystem verbunden. Flüsse von Material und Informationen in andere Systeme werden aber weiterhin von den Bedienern übernommen. In Stufe 3 ist die Produktionsanlage direkt mit anderen Systemen verbunden. Der Weg, den die einzelnen Werkstücke durch die Anlage nehmen, wird durch Sensoren in Echtzeit verfolgt. Dasselbe gilt für den Materialfluss von und zu anderen Anlagen. Verzögerungen fliessen sofort in die Planung ein.
Auf Stufe 4 ist der Vernetzungsgrad der Produktionsanlage noch höher. Teilweise kann sie mit den Bedienern und anderen Systemen autonom interagieren. Nun gehören auch mit Menschen kooperierende und lernende Roboter dazu. Stufe 5 schließlich beschreibt eine Anlage, die selbst lernt und mit den Produktions- und Informationssystemen innerhalb und außerhalb der Fabrik sowie mit dem Bedienpersonal interagiert. Sie wäre die Endstufe der Automatisierung und Digitalisierung.
Fazit: Ohne Menschen läuft es nicht
Allerdings sind auch auf dieser höchsten Entwicklungsstufe weiterhin Menschen gefragt. Zwar werden auch viele qualifizierte Tätigkeiten von Maschinen und selbstlernenden Computersystemen übernommen. „Auch selbstlernende Produktionssysteme müssen von Facharbeiterinnen und Facharbeitern zum Lernen angeleitet werden“, erläutert Prof. Bernd-Arno Behrens, Leiter des Instituts für Umformtechnik und Umformmaschinen (IFUM) der Leibniz Universität Hannover, sicher. „Und autonome Teilsysteme einer Produktionsanlage müssen überwacht und instand gehalten werden.“ Zudem entstünden neue Geschäftsmodelle, die auf datengestützten Dienstleistungen beruhen und somit auch neue Berufsprofile.
Die Industrie 4.0 könnte bewirken, dass sich auch einfache Tätigkeiten hierzulande wieder lohnen. „Es kann einen nicht zu unterschätzenden unternehmerischen Vorteil bedeuten, die gesamte Prozesskette an einem Standort überblicken zu können“, so Behrens weiter. Bislang hat die heimische Industrie nur die hochwertigen Jobs im Land behalten und viele andere Produktionsschritte an billigere Standorte verlagert.
Die Industrie 4.0 könnte bewirken, dass sich auch einfache Tätigkeiten hierzulande wieder lohnen
Ob die Industrie 4.0 tatsächlich mehr Jobs schafft als sie verschwinden lässt, bleibt jedoch abzuwarten. Aber das WGP-Analysemodell kann Unternehmen helfen, zu erkennen, in welchen Bereichen sie ihre Mitarbeiter weiter qualifizieren müssen und so Beschäftigung erhalten. Das würde sich positiv auf den Standortvorteil deutscher Unternehmen auswirken. Sie können nach wie vor im globalen Vergleich mit der hohen Kompetenz ihrer Mitarbeiter punkten.
Wirkung der Digitalisierung abhängig vom wirtschaftlichen Umfeld
Experten sind sich uneinig über die langfristigen Folgen der Digitalisierung und der Einführung intelligenter Maschinen für den Arbeitsmarkt. Während die WGP-Wissenschaftler eher optimistisch sind, sehen andere negative Folgen voraus. Bitkom, der Interessenverband der deutschen IT- und Telekommunikationsbranche, warnte im Frühjahr, dass bis 2022 in Deutschland bis zu drei Millionen Arbeitsplätze wegfallen würden. Und in einer Studie von 2013 zeichnen die in Oxford lehrenden Wissenschaftler Carl Benedikt Frey und Michael A. Osborne ein noch düsteres Bild. Danach stünden allein in den USA 47 Prozent aller Jobs zur Disposition. Die beiden berufen sich dabei auf Erkenntnisse zu den Folgen von Automation und Technisierung. Wobei heute nicht mehr nur manuelle Jobs, sondern auch geistige Tätigkeiten durch Maschinen übernommen werden. Außerdem dürfte sich die Qualifikation von Menschen zukünftig daran bemessen, wie gut sie mit intelligenten Maschinen zusammenarbeiten.
Und tatsächlich sind auch die WGP-Experten der Meinung, dass diese Fähigkeit große Bedeutung bekommen wird. Außerdem lässt das vielbeschworene Ende der Arbeit auf sich warten. Eine Studie des Mannheimer Zentrums für Europäische Wirtschaftsforschung (ZEW) zieht eine positive Jobbilanz. Zwar haben Modernisierungen in der Produktion in fünf Jahren rund fünf Prozent der Beschäftigten ersetzt, aber die Unternehmen auch produktiver gemacht. Sie produzierten nun günstiger und in größeren Mengen – stellten an anderen Stellen wieder Personal ein. Außerdem strahlte diese Entwicklung auf andere Bereiche der Wirtschaft aus, wo dann wiederum Arbeitsplätze entstanden sind. Am Ende hat die Digitalisierung zwischen 2011 und 2016 dann dazu geführt, dass die Zahl der Arbeitsplätze um ein Prozent gewachsen ist.
Allerdings funktioniert das nur in einem positiven wirtschaftlichen Umfeld. In einem Umfeld, das durch Stagnation und Handelskonflikte geprägt ist, dürfte die Wirkung der Digitalisierung eine andere sein.