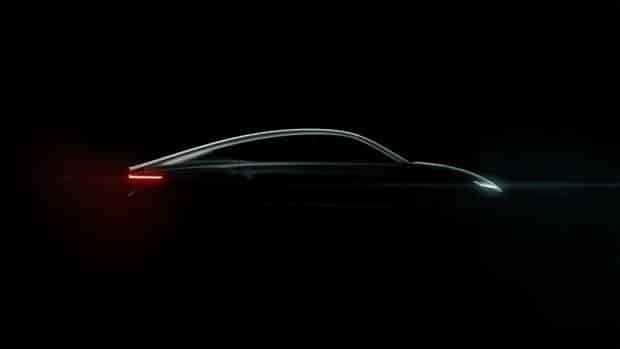
Five months ago, we decided to advance the construction of Lightyear’s prototype. Not an easy decision, but it was necessary to test some of the concepts we had on paper with reality at an early stage. It meant a financial risk, it meant a completely different focus, it was the start of 5 months with highs and lows but also with a team that came out stronger.
It was the first real test for the 130 people who joined Lightyear in the course of 1.5 years. The proof of the pudding… can we deliver with this team? The workload embraces the company like a tidal wave: first the architects who, each responsible for their own part of the vehicle, have to go through all the connections between the different systems in a short period of time: Exterior with interior, chassis with drive, software with all the electricity in the car and hundreds more of these connections. Which production methods are applicable, taking into account vibrations, temperatures, the order of assembly, strength, and so on.
Next phase: detailed design, together with the suppliers. Without input from the suppliers, you design something that cannot be made. The level of detail is high. Up to which two panels are connected with which screw and which curve ensure that the exterior and interior come together to within a millimetre. How do we ensure that the fabrics of the interior are neatly stitched and that the edges are not visible? How do we ensure that all electronics are supplied with both power and the right signals? Up to the interior lights in the trunk.
Not much later: placing orders. The prototype consists of thousands of separate parts, which often have to be ordered separately from different suppliers. The phones are working overtime and the brand new purchasing team is rapidly ordering the parts that came off the drawing board less than a day ago.
Parts come in from all over the world. Most of them from Europe, but also from the US and China, many of them coming to our production facility in Helmond with weeks of delivery time. This is where the first assembly work begins. First the chassis, the backbone of the car. The contact points with the exterior, interior, powertrain and thermal system are measured down to the last millimetre and adjusted where necessary. Then exterior. Would the supplier’s panels fit exactly on the chassis? Is every single part drawn exactly right? Will we be able to limit the gaps between the panels to just a few millimetres?
Then there is the final phase after the car has returned from the painter. First things first: Everyone tapes off all their sharp accessories and pieces of clothing. Jeans full of tape, watches off, and yes, even rings off. Miles of cabling goes into the car, all tested beforehand. Motors are united in the car with the battery and solar panel. Tested before in the lab, but now also in the car: can the engines make their first laps in the car?
130 people, thousands of anecdotes, long days, short nights, partners who go to great lengths to assist us, and as the weeks go by there is more and more applause. This is the story of a team with one goal. And, of course, a healthy amount of passion to make the world a better place.
We are proud to show you our blood, sweat and tears next Tuesday.
About this column:
In a weekly column, alternately written by Eveline van Zeeland, Jan Wouters, Katleen Gabriels, Maarten Steinbuch, Mary Fiers, Carlo van de Weijer, Lucien Engelen, Peter de Kock, Tessie Hartjes and Auke Hoekstra, Innovation Origins tries to find out what the future will look like. These columnists, occasionally supplemented with guest bloggers, are all working in their own way on solutions for the problems of our time. So tomorrow will be good. Here are all the previous episodes.