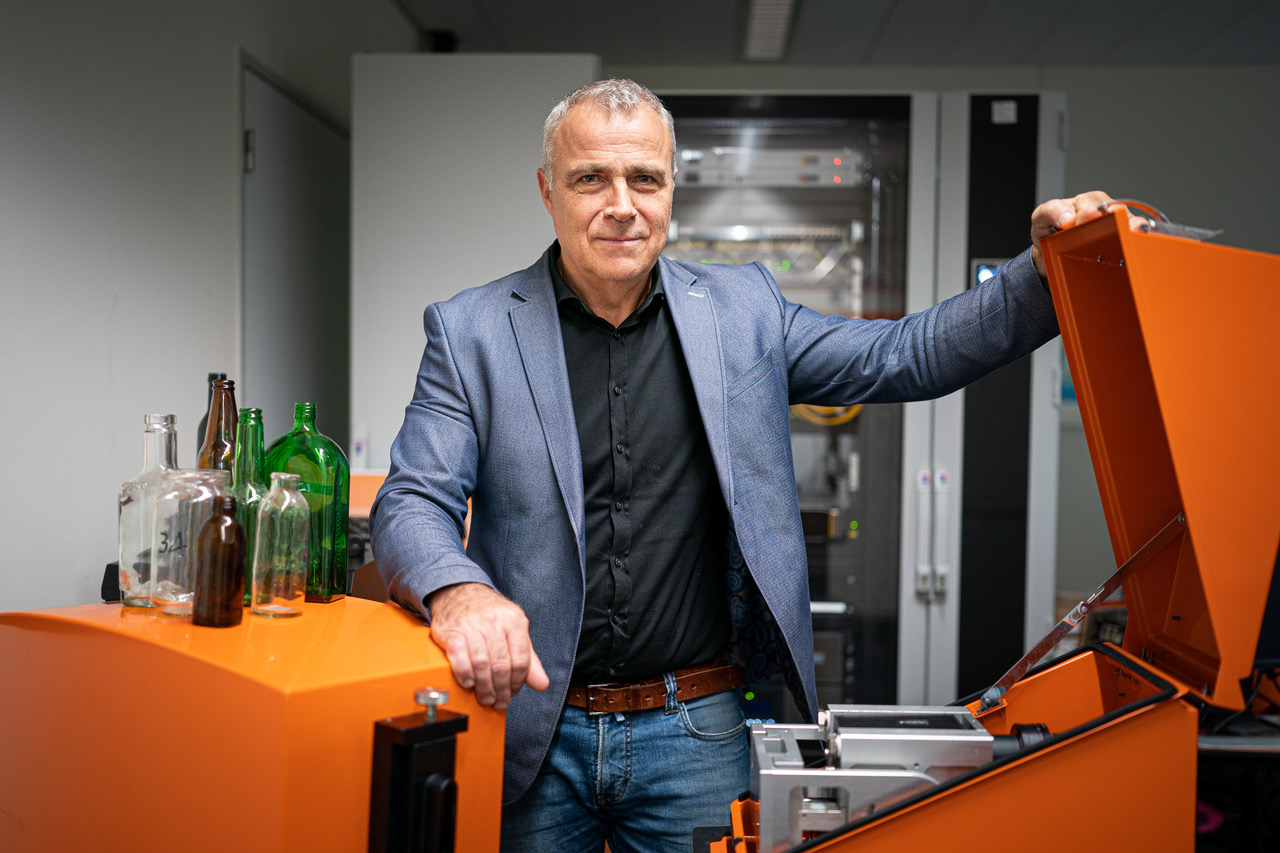
Van potten groenten tot flessen olijfolie: de supermarkt staat vol met verpakkingen van glas. En we maken er allemaal dagelijks gebruik van. Maar hoe werkt het productieproces? Is de glasindustrie eigenlijk wel duurzaam? Xpar Vision, een spin-off van de Rijksuniversiteit Groningen, richt zich op de sensor- en robottechnologie voor de wereldwijde glasindustrie. Daarmee kunnen producenten tijdens het maakproces voortdurend de kwaliteit van het glas controleren. Directeur Paul Schreuders beantwoordde zes vragen over de innovatieve technologie die het bedrijf ontwikkelt om zo de industrie te verduurzamen.
Hoe werken de sensoren die jullie ontwikkelen?
“Laten we bij het begin beginnen. Het maakproces van glazen potten en flessen begint met grondstoffen zoals zand en soda, maar ook met scherven van oude flessen, die worden samengebracht en verhit tot een gloeiende massa. Uit die massa worden druppels gevormd. Via een geleidingssysteem komen ze in mallen terecht en wordt er een pot of fles gevormd. Wij richten ons op het glasvormingsproces, dus het proces vanaf de druppel tot aan de fles.”
“Tijdens het gehele proces moet er gekeken worden naar de kwaliteit van het glas. In de praktijk blijkt dat zo’n 12 tot 15 van de 100 flessen niet voldoen aan de standaard. Je moet je bedenken dat er tot zo’n 40.000 flesjes per uur voorbij komen. Traditioneel gezien kijkt een operator naar de kwaliteit van de flessen, maar deze kan natuurlijk niet elk exemplaar controleren. Daarom is het inzetten van sensortechnologie heel slim. Onze sensoren kijken naar hoe de druppel geknipt wordt, hoe de druppel in de mal valt, en naar de temperatuur van de mallen. Hierdoor krijg je goed inzicht in de kwaliteit van de potten en uiteindelijk wordt de kwaliteit van de potten en flessen verbeterd.”
Wat zijn dan de voordelen van het werken met deze sensoren?
“Je kunt sterkere, lichtere flessen maken die minder fouten bevatten. Dat zit zo: het glas dat in de mallen wordt gegoten is beter controleerbaar. Daardoor heb je een constante verdeling van het glas over de mallen. Als je niet gebruikmaakt van sensoren en niet op tijd bijstuurt, zul je zien dat een glazen pot op sommige plekken dikker is en juist weer dunner op andere plekken. De sensoren zorgen ervoor dat er minder kans is op te dunne plekjes in het glas, dus hoef je minder glas te gebruiken.
“De flessen zijn dus lichter van gewicht. Dat heeft als voordeel dat je minder grondstoffen hoeft te gebruiken. Behalve dat het goedkoper is, is het natuurlijk beter voor het milieu. Daarnaast komt er minder CO2-uitstoot vrij tijdens het vervoeren van de lichtere flessen.”
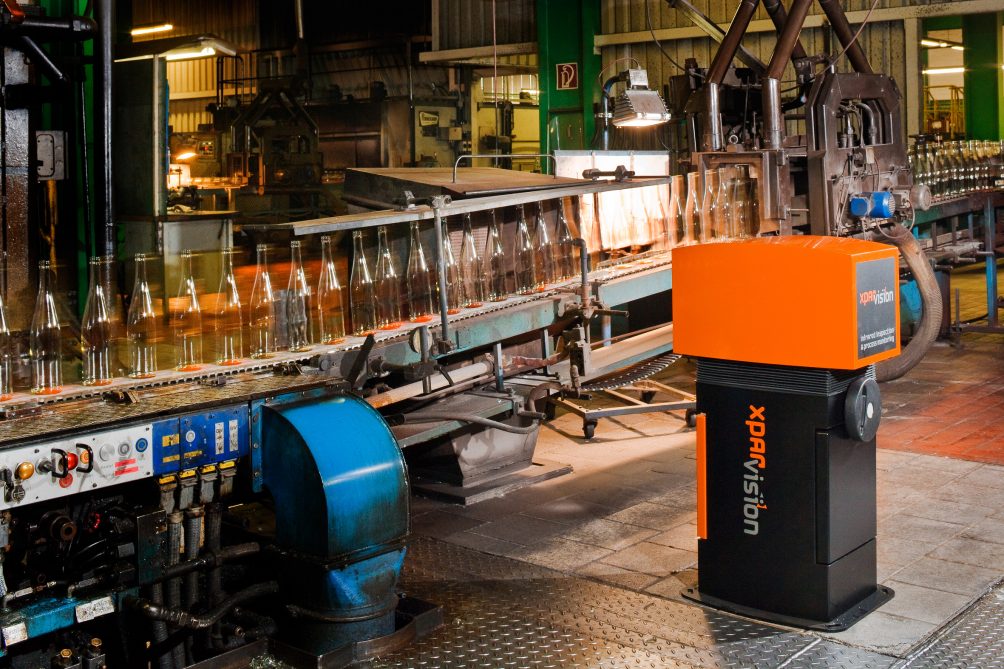
Hoe nieuw is het gebruik van sensoren in deze industrie eigenlijk?
“Twintig jaar geleden bestond er nog niets zoals sensortechnologie voor deze industrie. Wij zijn voor zover we weten de eerste die succesvol waren in het toepassen van sensortechnologie in het hete stuk van het maakproces. Het is natuurlijk ook een lastige klus om zoiets te ontwikkelen, want je hebt te maken met een hele uitdagende omgeving waarin de sensoren moeten opereren. De glasdruppels zijn zo’n 120 graden celsius. En de fles die uit de mal komt is 500 graden. Dat zijn waanzinnig hoge temperaturen. Het systeem moet 24 uur per dag draaien in een vochtige en vuile omgeving. De camera’s van de sensoren moeten beschermd zijn tegen vuil en tegen hitte kunnen. Om dit voor elkaar te krijgen, maken wij gebruik van speciale koelingmodules.”
Staat de glasindustrie open voor innovatieve oplossingen?
“Het is een industrie waar weinig verandering plaatsvindt, maar onze technologie wordt langzaamaan omarmd. De industrie is hard op weg om het glasvormingsproces beter te maken en begint langzaam de overtuiging te krijgen dat, wanneer het proces beter wordt, ze kunnen concurreren met karton en plastic vanwege de lagere kosten, energie en vermindering van de carbon footprint. Ook merk ik dat grote bedrijven als Heineken en Nestlé steeds meer druk zetten op glasfabrikanten om flessen lichter te maken, om zo de carbon footprint te verkleinen. Dat is mooi om te zien.”
Wat is momenteel jullie grootste uitdaging?
“Ik voorspel dat we een versnelling gaan zien in het aantal toepassingen van onze technologie, gezien het feit dat bedrijven zich bewuster worden van de duurzaamheid van het maakproces van glas. Dat betekent dus ook dat wij het aantal werknemers moeten gaan uitbreiden. Zij moeten immers de technologie verder ontwikkelen en bij klanten installeren en controleren. Het gaat nog een hele uitdaging worden om genoeg technisch opgeleide mensen te vinden die zich aan ons willen binden.”
Waar hoop je over vijf jaar te staan met je bedrijf?
“Op dit moment hebben we klanten in meer dan 35 verschillende landen. De meeste klanten zijn fabrikanten uit Europa en de Verenigde Staten, gevolgd door Mexico, Thailand en Turkije. We hebben in totaal ongeveer 600 installaties staan, verdeeld over de hele wereld. Dat is al een heel aardig aantal en we hebben er zo’n twintig jaar over gedaan om het voor elkaar te krijgen Maar ik denk dat we dit aantal over vijf jaar verdubbeld kunnen hebben. Wat we uiteindelijk willen, is dat in de nieuw gebouwde fabrieken onze technologie standaard ingebouwd zit. Ik hoop dat we tegen die tijd volwaardig deel uitmaken van het maakproces van glas.”
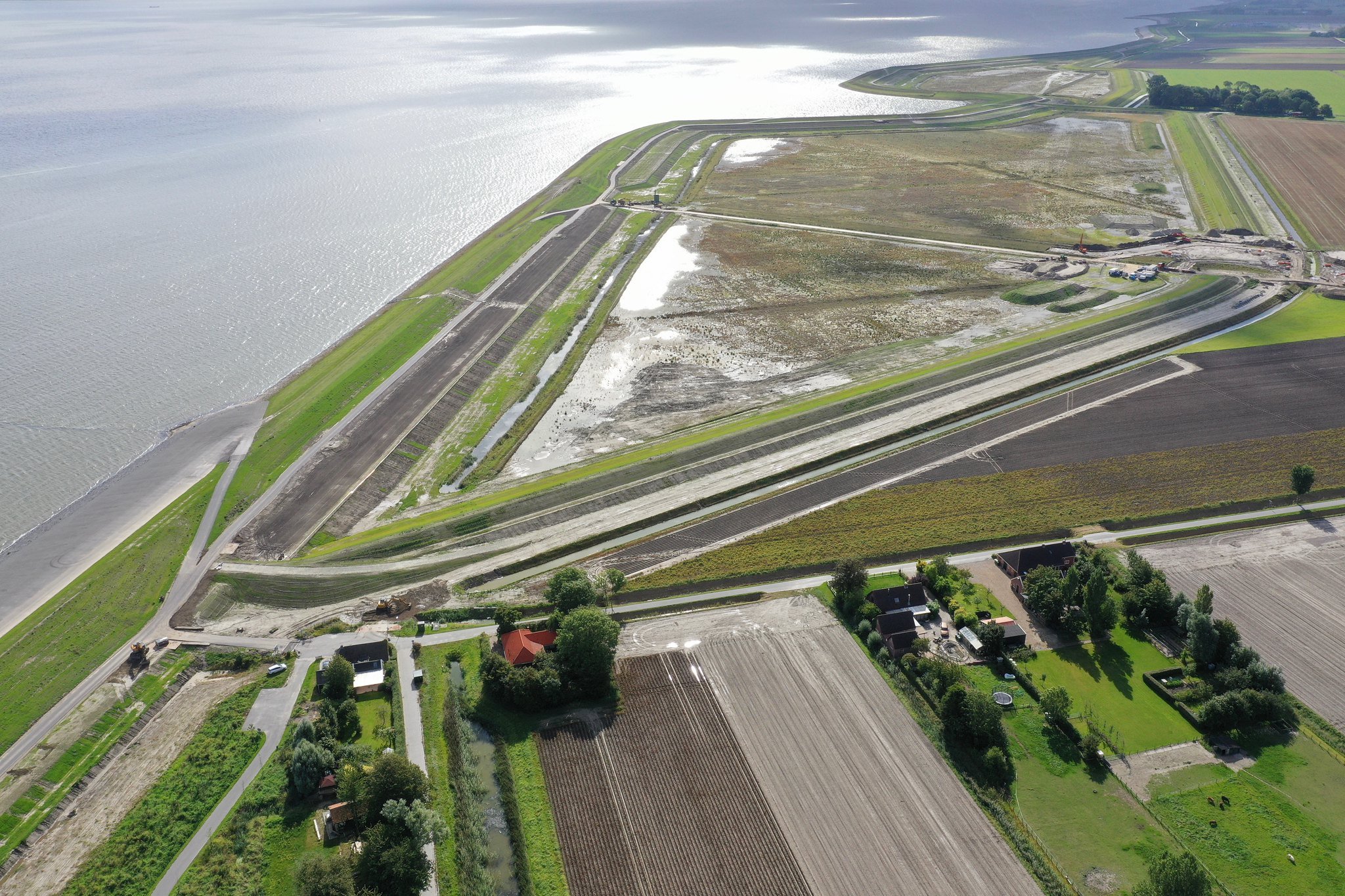