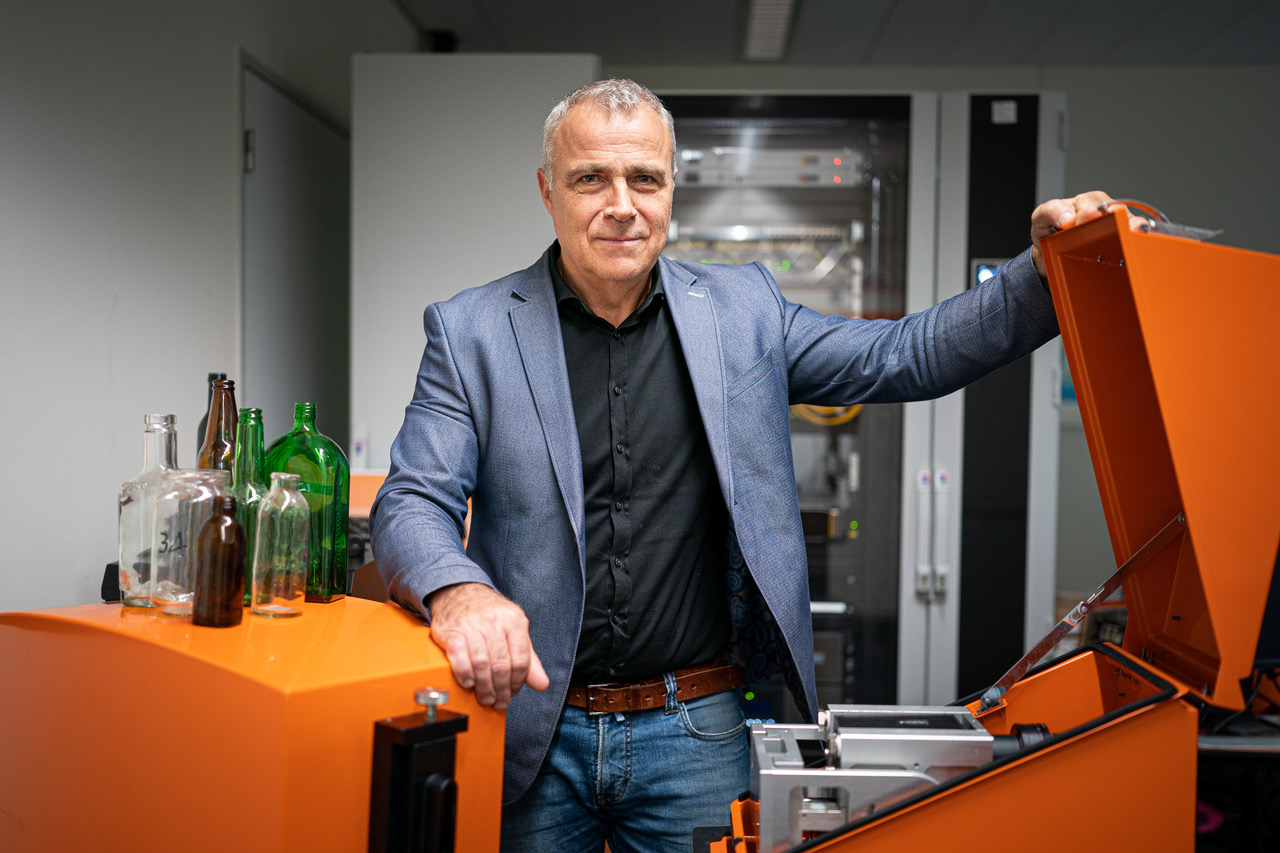
From vegetable jars to bottles of olive oil, supermarkets are full of glass packaging. And we all use them every day. But how does the manufacture process actually work? Is the glass industry truly sustainable? Xpar Vision, a spin-off from the University of Groningen in The Netherlands, focuses on sensor and robotic processing technology for the global glass industry. This enables producers to continuously monitor the quality of the glass during the manufacturing process. Director Paul Schreuders answered six questions about the innovative technology that the company is developing to make the industry more sustainable.
How do the sensors that you develop work?
“Let’s start from scratch. The process of making glass jars and bottles begins with raw materials such as sand and soda, as well as shards of old bottles, which are put together and heated to form a glowing mass. Droplets are formed from that mass. Via a conductive system, they pass into molds and a jar or bottle is formed. We focus on the glass forming process, that is, the process from the droplet to the bottle.”
“During the entire process, attention must be paid to the quality of the glass. In practice, about 12 to 15 out of 100 bottles do not meet the standard. You have to consider that up to about 40,000 bottles pass through every hour and traditionally an operator looks at the quality of the bottles, but obviously they cannot check every single one. That’s why the use of sensor technology is very smart. Our sensors look at how the droplet is snipped, how the droplet drops into the mold, and at the temperature of the molds. This gives you a good insight into the quality of the jars and ultimately improves the quality of the jars and bottles.”
So just what advantages are there to working with these sensors?
“You can make stronger, lighter bottles that have fewer defects. It goes like this: the glass that is poured into the molds is more controllable, therefore you have a consistent distribution of the glass across the molds. If you don’t use sensors and don’t adjust things in time, you will see that a glass jar is thicker in some places and thinner in others. The sensors ensure that there is less chance of thin patches in the glass , which is why you don’t have to use as much glass.”
“So the bottles are lighter in weight. That has the advantage that you do not have to use as many raw materials. In addition to being cheaper, it is of course better for the environment. Moreover, less CO2 is released during the transport of the lighter bottles.”
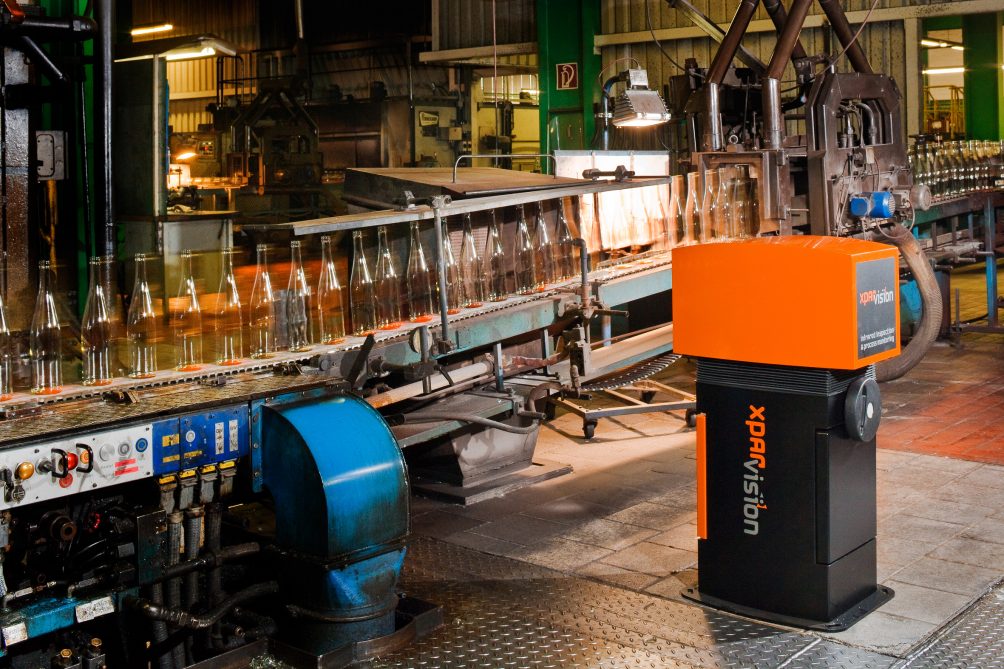
How new in fact is the use of sensors in this industry?
“Twenty years ago, no such thing as sensor technology existed in this industry. We are, as far as we know, the first ones who were successful in applying sensor technology in the hot part of the manufacturing process. Of course, it’s also a tricky task to develop something like this, because you’re dealing with a very challenging environment that the sensors have to operate in. The glass droplets are about 12000 degrees Celsius in temperature. And the bottle that comes out of the mold is 500 degrees Celsius. Those are insanely high temperatures. The system has to run 24 hours a day in a humid and dirty environment. The cameras of the sensors must be protected from dirt and be able to withstand heat. We use special cooling modules to achieve this.”
Is the glass industry open to innovative solutions?
“It is an industry where there is very little change, but our technology is gradually being embraced. The industry is working hard to improve the glass molding process and is slowly starting to believe that as the process improves, they will be able to compete with cardboard and plastic because of the lower costs, lower energy and reduction in the carbon footprint. I also notice that big companies like Heineken and Nestlé are putting more and more pressure on glass manufacturers to make bottles lighter so as to reduce the carbon footprint. That’s great to see.”
What is currently your greatest challenge?
“I predict that we are going to see an accelerated uptake in the number of applications for our technology, given that companies are becoming more aware of the sustainability of the glass-making process. So this also means that we need to start expanding the number of our employees. After all, they have to develop the technology further and install and monitor it at clients’ premises. It’s going to be quite a challenge to find enough technically trained people who are willing to commit themselves to us.”
Where do you hope to be with your company in five years’ time?
“At the moment, we have clients in more than 35 different countries. Most of our clients are manufacturers from Europe and the United States, followed by Mexico, Thailand and Turkey. We have about 600 units installed in total, spread all over the world. That is already a very respectable number and it has taken us about twenty years to achieve. But I think we can double this number within five years. What we ultimately want is for newly built factories to have our technology built in as standard. I hope that by then we will be a fully-fledged part of the glass making process.”
Read other stories about the dutch city of Groningen via this link.