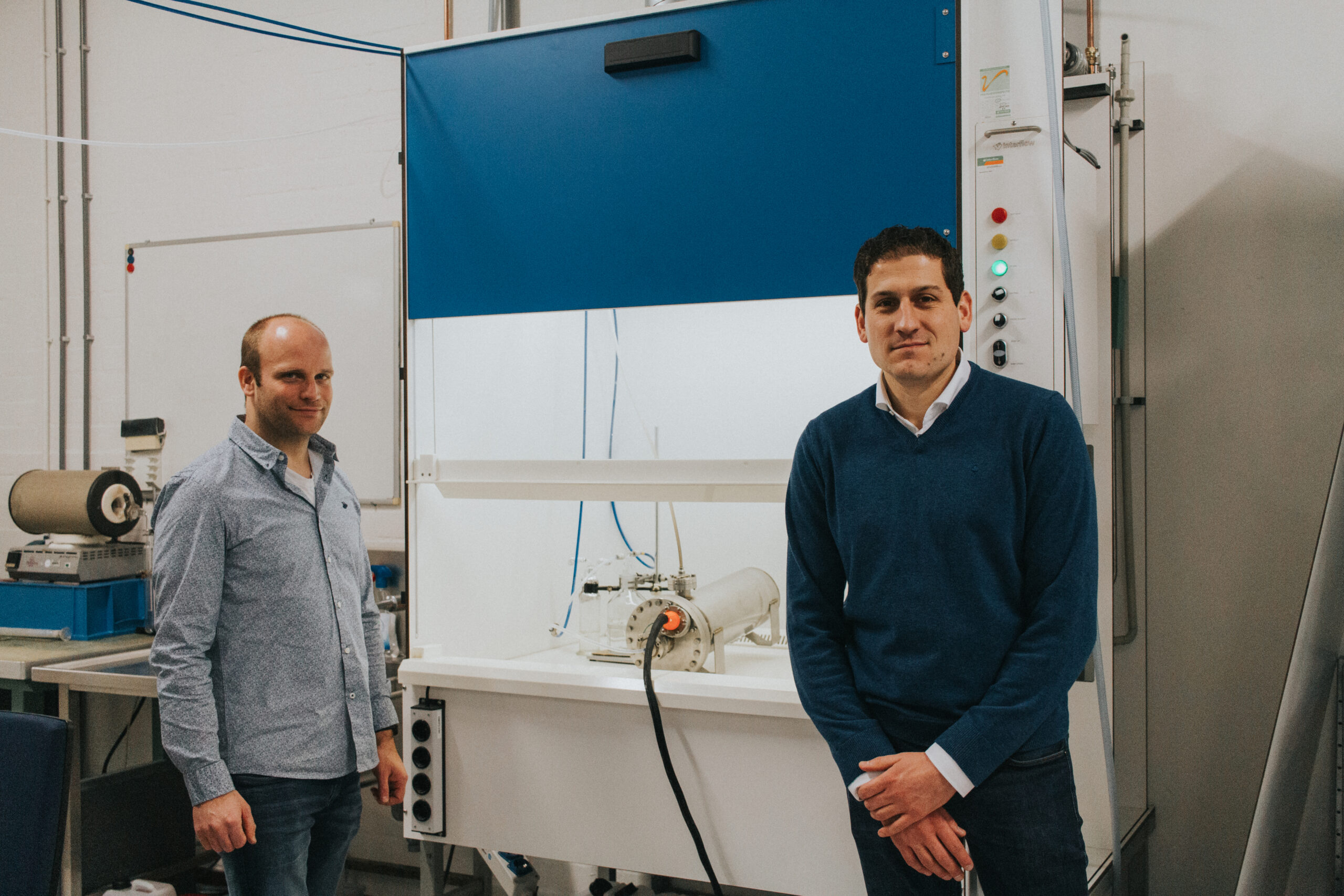
About AddCat
- Founders: Jacco Hoekstra, Gerald van Santen, Marc Evers
- Founded in: 2019
- Employees: 4 oprichters, 3 stagiaires en extra personeel huren we in waar nodig.
- Money raised: Combinatie van subsidies, leningen en investeringen
- Ultimate goal: Een wereld waar niemand hinder of gezondheidsgevolgen ondervindt van schadelijke industriële (geur)emissies
Jaarlijks sterven er wereldwijd zo’n 7 miljoen mensen vroegtijdig aan ziektes veroorzaakt door luchtvervuiling. Volgens advies van het WHO moet het gehalte vervuilende stoffen in de lucht, flink omlaag. Het Geldropse AddCat heeft hier iets op gevonden: een zuiveringssysteem met een uit metaal 3D-geprinte luchtfilter. CEO Gerald van Santen legt het in deze aflevering van start-up of the day uit.
Hoe werkt het?
“Iedereen kent de katalysator in verbrandingsmotoren van bijvoorbeeld auto’s. Deze is bedoeld om schadelijke uitlaatgassen te filteren. De vervuilde lucht loopt door een eenvoudige structuur met katalysatormateriaal waarmee de vuile stoffen reageren. Onze filter werkt op exact dezelfde manier. Maar omdat we de structuur van de katalysator 3D-printen kunnen we veel complexere systemen produceren waar de lucht doorheen loopt. Hierdoor legt de vervuilde lucht een veel langere weg af, we dwingen schadelijke moleculen om in contact te komen met het actieve katalysatormateriaal. Dit zorgt voor een betere luchtzuivering. We kunnen meer dan 95 procent van de schadelijke componenten uit de lucht verwijderen. Ook kunnen we energiezuiniger te werk gaan. De metalen structuren zorgen voor een goede warmte-geleiding en -beheersing in het proces.”
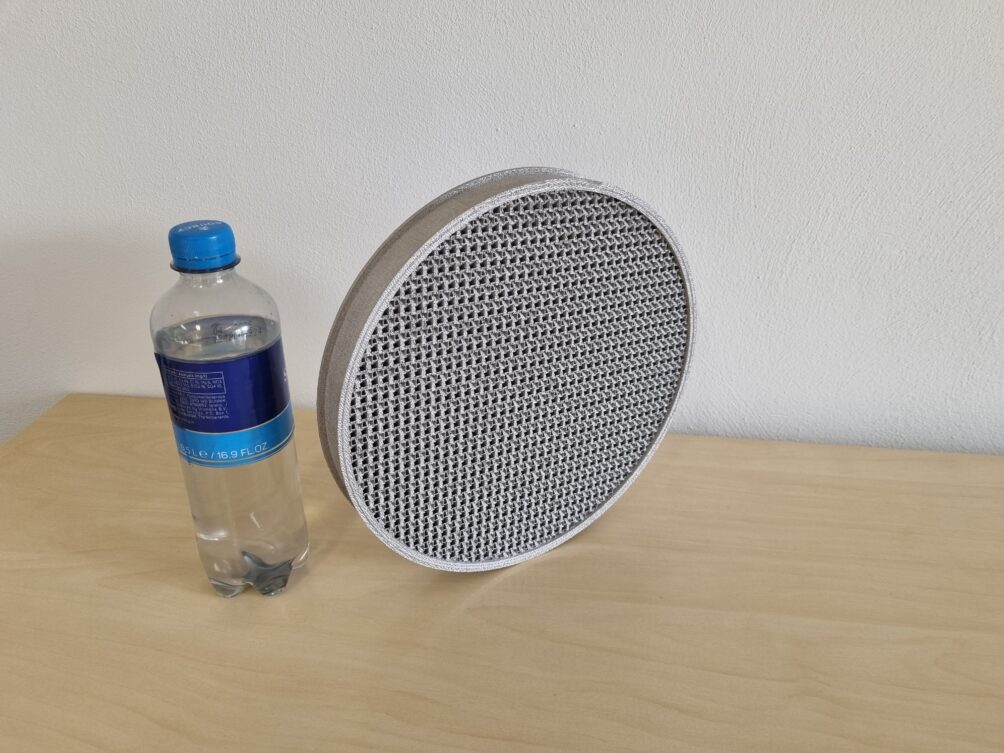
Waar richten jullie je op?
“In het begin richtten we ons vooral op de geuroverlast. Maar we zijn er achter gekomen dat het juist vaak om een combinatie van gassen gaat. Dus naast de geurende en schadelijke componenten, die onder de zogenaamde Vlucht Organische Componenten (VOC’s) vallen, ook ammoniak en methaan. Dat doen we als eerste in de markten voor mestverwerking, biogas en veehouderij. Een andere markt is de chemische industrie of asfaltverwerkers waar ook veel schadelijke stoffen worden uitgestoten.
Hoe ver zijn jullie in dit proces?
“We hebben heel veel verschillende prototypes van de 3D geprinte structuren getest. Omdat we samenwerken met bijvoorbeeld K3D en AMPC Solutions, 3D-printbedrijven in Eindhoven kunnen we snel nieuwe versies van de interne structuur van de filter maken. Doordat we in de incubator van de TBRM group in Geldrop zitten hebben we onze techniek snel kunnen opschalen. Intern is het volledige prototype gebouwd en zijn we in het afgelopen jaar zo’n 1000 keer opgeschaald. Van 1 kuub naar 1000 kuub gezuiverde lucht per uur.”
We hebben nu een technische beoordeling van een onafhankelijke partij, de Vlaamse kennisinstelling VITO. Hier hebben we reductiepercentages tot wel 98 procent gehaald. Met deze gegevens kunnen we potentiële klanten laten zien dat onze technologie wel degelijk werkt.”
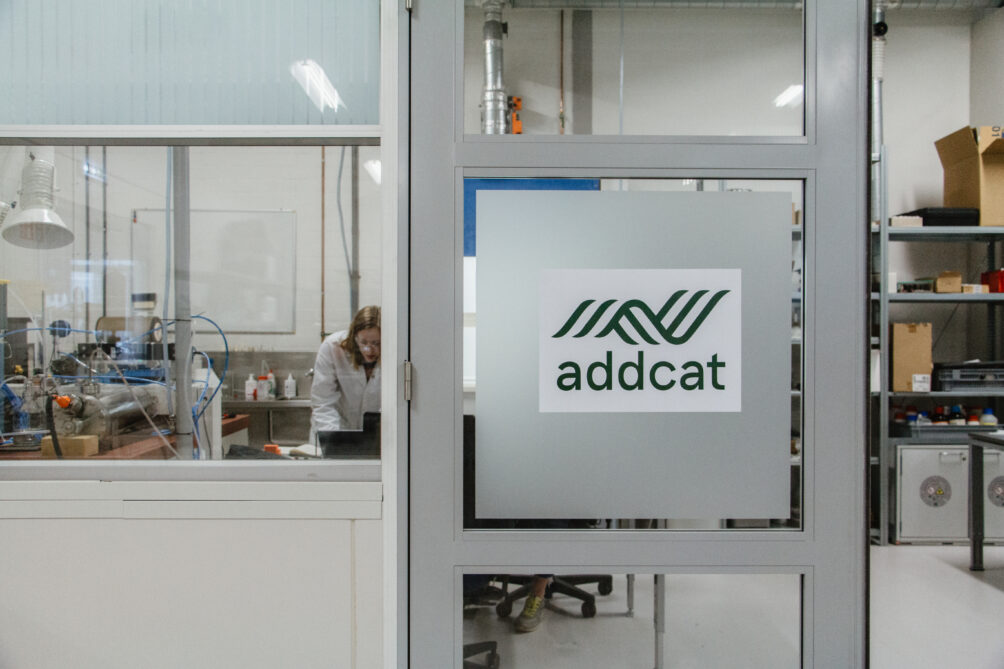
Hoe zijn jullie begonnen?
“Bij KMWE, een grote toeleverancier op het gebied van high tech machinebouw, is het idee ontstaan. De toenmalige CTO en een emeritus hoogleraar van de Universiteit Utrecht. Bij KMWE kunnen ze alles bouwen, maar de chemie-kant is minder sterk. Toen Marc Evers daar opstapte nam hij een deel van de inboedel en een patent dat al sinds 2010 op de plank lag over. We zijn heel klein begonnen en scharrelden eigenlijk alles wat we nodig hadden bij elkaar. We huurden spullen of kochten onderdelen via veilingsites. Momenteel bevindt 3D metaal printen zich in de industrialisatiefase, wij willen laten zien dat het ook mogelijk is om deze techniek op massaproductieschaal te gebruiken.”
Wanneer zijn jullie op de markt?
“Met deze validatie ontwikkelen we nu een systeem dat tot wel 50 duizend kuub lucht per uur kan zuiveren. Ook hebben we een patent gepubliceerd. Hiermee kunnen we 95 procent van de warmte die het systeem gebruikt, terug winnen. Hierdoor dalen de operationele kosten voor klanten flink. Deze module is klaar voor de markt. We willen dit jaar de eerste installatie volledig draaiend hebben bij klanten.”
Wat mogen we nog van jullie verwachten?
“Op dit moment bouwenwe onze prototypes zelf. We proberen low cost te ontwikkelen. Als we echt gaan opschalen qua productie, moeten we dit professionaliseren. Daarom maken we nu stappen in het engineeringsproces. We brengen de hele productie in kaart en zorgen ervoor dat we er klaar voor zijn als het daadwerkelijk zo ver is. Hiervoor hebben we veel aan de kennis en het netwerk van de verschillende engineers binnen de TBRM-incubator.”
“Ook werken we aan een project met Wageningen Universiteit aan onderzoek rond de verwijdering van methaan uit de lucht.”
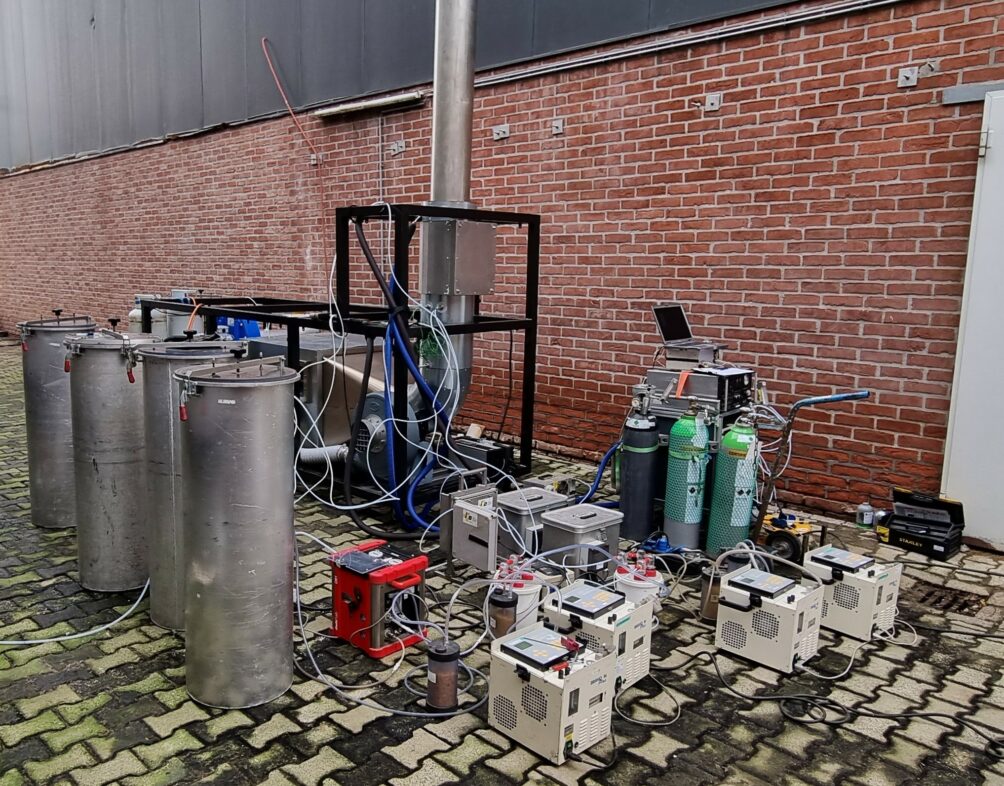
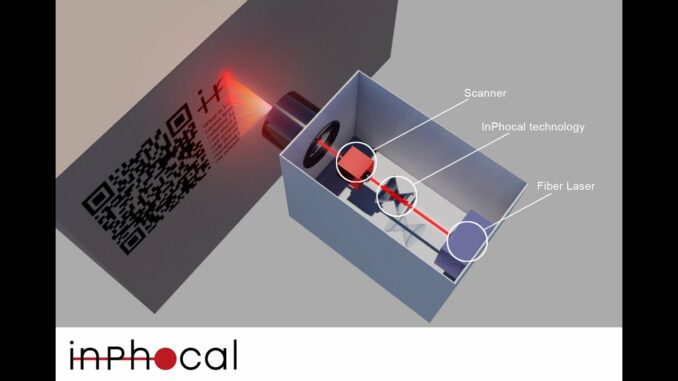