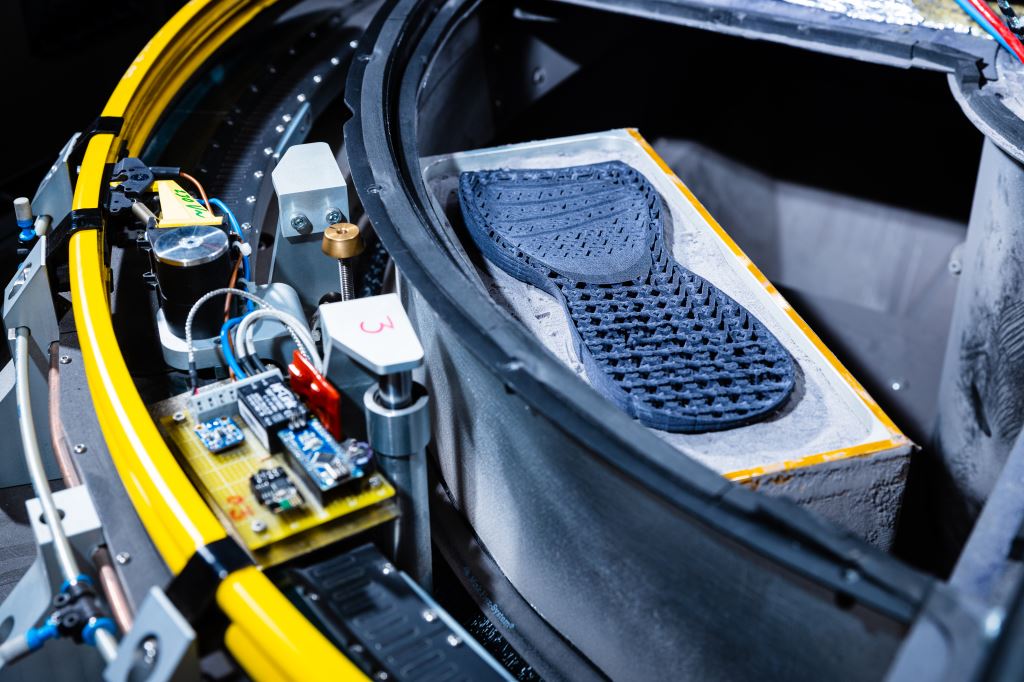
Een 3D-printer die binnen 20 minuten een op maat gemaakte inlegzool voor je sportschoenen print. Het is een van de machines waar verschillende bedrijven en kennisinstellingen binnen het Fieldlab MM3D (Multi Material 3D-printen) aan werken.
Op Brainport Industries Campus werken Industrio, AMPC Solutions en de Technische Universiteit Eindhoven aan vraagstukken uit het bedrijfsleven. Zo kan de zogenaamde carrousel 3D-printer van Industrio verschillende materialen printen voor bijvoorbeeld schoenzolen of inlegzooltjes. “De hak moet steviger zijn dan de voorkant. Hiervoor heb je verschillende materialen nodig. Binnen het fieldlab hebben we een pilotlijn opgezet om hiermee te testen”, legt projectleider Juan Pelucarte uit.
Een andere 3D-printer in het fieldlab kan per uur 180 gebitsafdrukken printen die worden gebruikt om beugels te maken met een vacuüm-former. In dit apparaat wordt een kunststofplaat verwarmd net zo lang tot deze buigzaam is, vervolgens trekt de vacuüm-former met luchtdruk de buigzame kunststof over de gebitsprint. “Hiervoor gebruik je weer andere technieken en materialen. Het zijn twee voorbeelden waar bedrijven in de markt mee bezig zijn. Binnen het fieldlab onderzoeken we een goede businesscase en zoeken we naar manieren om de productie op te schalen of uit te breiden.”
Metalen onderdelen laagdrempelig 3D-printen
Multimateriaal 3D-printen kan voor sommige bedrijven ook een goedkopere en laagdrempelige manier zijn om metalen onderdelen te vervaardigen. Hierbij heeft AMPC Solutions een oplossing bedacht. De Eindhovense start-up maakt printfarms, een soort kasten, waar meerdere consumenten 3D-printers tegelijk kunnen printen. “We begonnen in 2019 met een noodknop om alle printers in de kast in één keer uit te kunnen schakelen. Dit kan soms nodig zijn als er tijdens het 3D-printen iets misgaat. Na positieve reacties van bedrijven zijn we dit verder gaan uitbreiden. In onze printkasten kunnen we nu temperatuur en vochtigheid regelen. Ook werken we aan een systeem om fijnstof of gas, dat vrijkomt tijdens het printen, te filteren. Het doel is om het proces steeds meer te automatiseren, met printbeds die automatisch worden verwisseld bijvoorbeeld”, legt Arno Gramsma van AMPC uit.
Volgens Gramsma is de aanschaf van een 3D-metaalprinter voor kleine bedrijven een flinke investering. Het kan daarom, volgens hem, in sommige gevallen beter zijn om ‘gewone’ 3D-printers te gebruiken met een filament van kunststof en metaal. “Er hangt een flink prijskaartje aan industriële 3D-metaalprinters. Zeker als een bedrijf maar weinig print. Of niet helemaal zeker is of 3D-printen van metaal wel van toegevoegde waarde is. Dan is het niet handig om zo’n dure machine aan te schaffen.”
“Een filament van kunststof met metaalpoeder kan dan uitkomst bieden. Weet je wel? De lange kunststofdraden waar een Ultimaker, een huis-tuin-en-keuken 3D-printer, normaal mee print. Alleen bestaat deze draad niet alleen uit kunststof. Maar zit er metaalpoeder in het midden. Hierdoor kun je dus metaal 3D-printen zonder dat je een dure 3D-metaalprinter hoeft aan te schaffen.”
Met simulaties betere voorspelling maken van eindresultaat
Maar hiervoor zijn eerst nog een aantal stappen nodig. Eenmaal uit de printer moet de kunststof dat nog om het product zit, verwijderd worden. Als dit debinden klaar is, gaat het een sinteroven in om alle metaaldeeltjes in elkaar te laten smelten. Deze stappen kunnen bedrijven uitbesteden, maar AMPC levert ook complete systemen zodat maakbedrijven snel over geprinte onderdelen kunnen beschikken. Binnen het fieldlab onderzoekt AMPC Solutions samen met de TU/e naar manieren om deze processen te verbeteren.
Gramsma: “Het printen met deze metaalfilamenten staat in de kinderschoenen. De grote uitdaging is nog altijd of een ontwerp precies zo wordt zoals je had ontworpen. Tijdens het debinden vervormt een product en in de oven krimpt het. Maar het is lastig vooraf te zeggen hoe dit uitpakt. Een product krimpt niet overal evenveel. Samen met de TU/e werken we aan een model dat precies voorspelt welke invloed deze twee stappen op het 3D-geprinte product heeft. Door het printproces op allerlei manieren te simuleren, krijg je steeds meer inzicht Hiermee willen we software maken die ontwerpen automatisch aanpast aan het vervormen en krimpen in de oven.”
Gramsma ziet potentie in de ontwikkeling van nieuwe 3D-printtechnieken. “Deze verschillende technieken lenen zich goed voor digitalisering. Via het Internet of Things kun je allerlei sensoriek koppelen om het printen te monitoren. Hiermee kun je precies zien waar nog ruimte voor verbetering is. Ook AI speelt hier een belangrijke rol in. Met al deze data kun je heel precies voorspellen hoe producten uit een printer of oven komen. Het gaat het leerproces enorm versnellen. Voor engineers wordt het gemakkelijker om lastige vormen te creeëren. Met AI kun je straks een ontwerp genereren op basis van verschillende functies zoals druk of materiaaldikte. Je geeft een aantal randvoorwaardes en zegt tegen de software: ‘bouw het maar!’”
Platform waar bedrijven kunnen aanhaken
Uiteindelijk moet het fieldlab een platform worden waar bedrijven kunnen aanhaken om multi materiaal 3D-printen te industrialiseren. Projectleider Pelucarte: “Als bedrijf wil je niet dat je eerst 10 producten moet weggooien voordat er iets goeds uit de printer rolt. Voordat je kunt opschalen moet eerst het printproces op orde zijn. Op de campus laten we in een demo zien hoe we zo’n printproces verbeteren.”
Het fieldlab is onderdeel van het innovatieprogramma Fabriek van de Toekomst waar bedrijven, kennisinstellingen en overheid samenwerken aan verschillende thema’s rond smart industry. Het doel is om nieuwe productietechnieken, zoals multimateriaal 3D-printen sneller en goedkoper op de markt te brengen. Volgens de deelnemende partijen kan dit alleen door samenwerking. Ze delen faciliteiten en opgedane kennis wordt gedeeld binnen de verschillende fieldlabs op BIC. Het programma wordt ondersteund door de provincie Noord-Brabant.
Lees hier meer over het innovatieprogramma.
Volgens Pelucarte is zo’n subsidieprogramma goed om onderzoek te doen en nieuwe dingen uit te proberen. Maar moet het wel leiden tot eigen verdienmodellen. “Voor iedere euro die je uitgeeft komt er bijvoorbeeld 40 cent terug. Dit stimuleert wel om die activiteiten te ontplooien. We willen bedrijven helpen die overwegen om bepaalde onderdelen of gereedschap te 3D-printen. Bij het fieldlab kunnen ze zich aansluiten om een machine of printproces te ontwikkelen. Door ontwikkelkosten en kennis te delen, kunnen we sneller een machine maken voor specifieke use cases.”