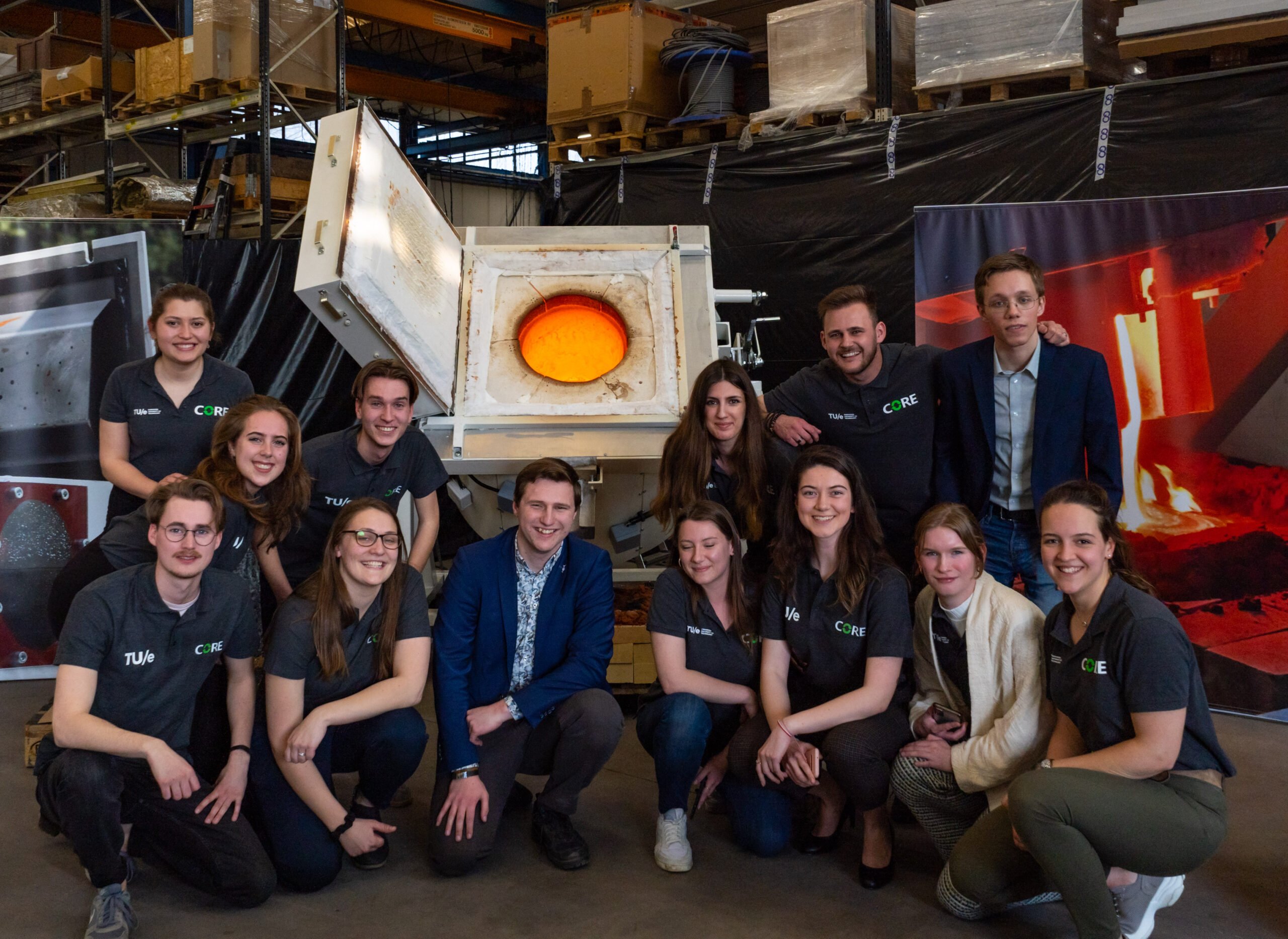
Deze oven is een belangrijke stap richting de fabriek die CORE uiteindelijk wil bouwen, zegt Niels Bongers, chief technologie officer bij CORE Chemistry, een spin-off van het studententeam. In die fabriek moeten afvalstromen als vliegas, die overblijven na verbranding van onder meer biomassa en steenkool, tot nieuwe en veilige producten leiden. De oven is een vondst voor zowel bedrijven die van hun afval af willen als bedrijven die er nieuwe producten van willen maken.
Lees hier meer over het smeltproces dat CORE ontwikkelde
Hitte
Met een eerdere oven toonde het team van de TU Eindhoven (TU/e) al aan dat het mogelijk is om metalen te laten smelten tot basalt. Bongers: “Als je het maar heet genoeg maakt. Maar als het dan heet en vloeibaar is, wat doe je er dan mee? Wat kun je er dan van maken?” Bongers studeerde vorig jaar af op een simulatie van hoe het proces in de fabriek zou moeten lopen. Nu hij met deze oven kan aantonen dat er producten mee te maken zijn, staat hij te popelen om met de fabriek te starten. Maar zover is het nog niet.
Het studententeam deelde de oven gisteren met mensen uit onder meer de afvalindustrie en de energiewereld. In de fabriekshal van het bedrijf Global Oven Systems, dat het team hielp de oven te bouwen, kon een gezelschap van zo’n honderd geïnteresseerden de hitte van de oven ervaren.
“Helaas gingen er gisteren vier verwarmingsbuizen stuk”, zegt Dirk van Meer, mede-oprichter van CORE Chemistry. “Ze zijn makkelijk te vervangen – het is een modulair systeem – alleen moet de oven dan wel koud zijn.” Omdat de dag voorafgaand nog “even werd getest”, was de oven nog heet. “Het duurt een dag of twee om van 1400 graden naar nul graden te koelen.” Laten zien hoe een als honing uitziende vloeistof in een productvorm wordt gegoten, kon dus niet. Als alternatief kantelden de bouwers de oven en lieten de hitte vrij.
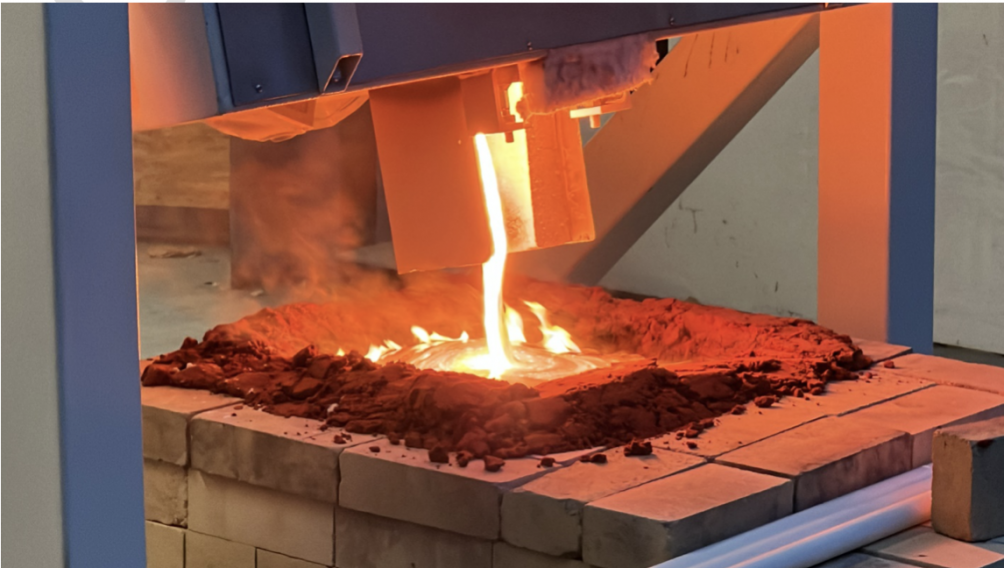
Spoorballast
De afvalstoffen, zoals vliegas en slib, gaan in een grote kelk, die vervolgens de oven ingaat. In de oven smelten de stoffen tot een gloeiendhete vloeistof. Die vloeistof is moleculair te bewerken, waardoor er nieuwe materialen ontstaan. Door deze vloeistof vervolgens in een mal te gieten, zijn er verschillende producten van te maken, zoals basalttuintegels of de stenen rond het spoor; ballast.
“Toen we met CORE begonnen, waren we vooral bezig met het technische proces”, zegt Van Meer. “De vraag of de markt erop zat te wachten, kwam pas later.” Via de oorspronkelijke bedenker van de fabriek, Gabby van Meer en vader van Dirk, kwam het team in contact met spoorwegbeheerder ProRail. Spoorballast bleek een geschikt product.
Lees hier meer over het ontstaan van CORE
De productieketen van spoorballast is nu nog lineair, aldus een persbericht van team CORE. ProRail heeft het een afvalstroom van 300 kiloton per jaar. Die is nu bestemd voor de stort. Veertig procent van de CO2 uitstoot van deze spoorballast is gerelateerd aan winning en transport en aan bewerking in Nederland.
Prorail betaalde zeker de helft van de haalbaarheidsstudie naar de oven, laat Gabby van Meer weten. “Andere marktpartijen wilden meebetalen, maar ProRail wilde eerst toetsen of het materiaal überhaupt geschikt zou zijn voor de ballast op het spoor.” Daarna zou het bedrijf de kennis delen met de markt. “Vandaar deze onthulling.”
Oproep aan de markt
Dirk van Meer: “Dit was de laatste voorbereiding voor de fabriek in Moerdijk (de beoogde locatie voor fabriek, red.). Vandaag is eigenlijk een presentatie naar de markt. We hebben technisch bewezen dat het kan, maar wij zijn ook maar een studententeam. Dus markt: pak het alsjeblieft op.”
Het is vooral nodig er grote hoeveelheden van te kunnen gaan maken. De Magma-oven toont aan dat het kan, maar wel op kleine schaal. Voor het spoor zijn grote hoeveelheden nodig, zegt Simon Lubach, adviseur klimaatneutrale infrastructuur bij ProRail.
Lubach: “Maar als het lukt zou het wel een doorbraak zijn. Dan zijn we voor ballast niet meer afhankelijk zijn van andere landen.” De spoorwegbeheerder haalt nu het materiaal voor de ballast uit landen als China, Spanje. Noorwegen en Oostenrijk. “Als het in Nederland gemaakt kan worden scheelt dat enorm veel CO2 uitstoot. Dan moet je denken aan zo’n kilo ton 15 tot 20 kilo ton per jaar.”
Ook staat het gebruik van ballast, sinds een uitzending van Zembla over kwartsstof, ter discussie. Bij het verwerken van ballast komt kwartsstof vrij, wat schadelijk is voor de gezondheid. In het basalt van CORE zit geen kwartsstof. “Daarmee zou het een goed alternatief zijn”, aldus Lubach.
Florerende studenten
Voor Lubach is de oven een eerste stap. Om tot spoorballast te komen zijn er nog veel vragen te beantwoorden. “Hoe veilig is het product? Wat zijn effecten op de lange termijn? En natuurlijk: is het in grote hoeveelheden te maken?”
Ook Gertie Huitink, Head of Industries & Storage bij Eneco, ziet veel heil in de Magma-oven. “Vanuit Eneco zijn wij zijn al een tijd bezig om vliegas circulair te krijgen.” Ruim twee jaar geleden kwam hij met Gabby van Meer in gesprek. Die vertelde Huitink over de plannen van CORE. Huitink raakte enthousiast. “We zijn met een emmertje basalt begonnen, dat werden er tien. Deze oven laat zien dat we met onze vliegas producten kunnen creëren voor anderen.”
Daarnaast vindt Huitink het “gewoon erg leuk om te zien hoe studenten gewoon floreren”. “Zij hebben de toekomst. Het is mooi hoe je onze ervaring kunt combineren met hun kennis van nieuwe technologische ontwikkelingen. Dat dat dan weer uitgroeit tot zoiets als deze oven. Als we nu ook nog grote hoeveelheden kunnen maken, dan is dat alleen maar nog mooier.”
De financiering van de installatie werd mogelijk gemaakt door ProRail, de Technische Universiteit Eindhoven (TU/e) en twee alumni van de TU/e. Jan van Gemert (voormalig CEO Gemco Casting) en Hans Fischer (voormalig CEO TATA Steel).
Bekijk hier de reportage van Studio040