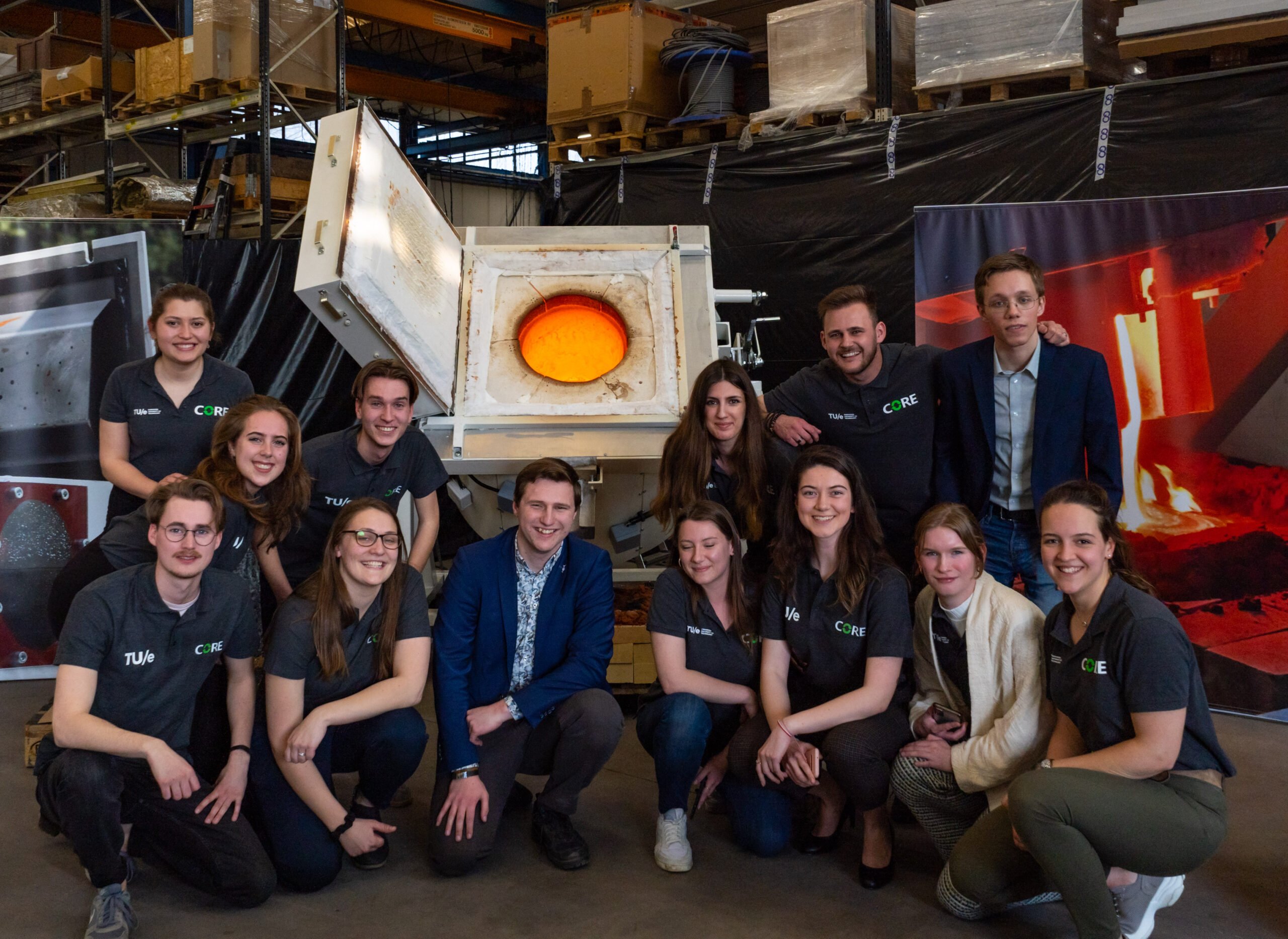
This furnace is an important step towards the plant that CORE ultimately intends to build, says Niels Bongers, chief technology officer at CORE Chemistry, a spin-off from the CORE student team. In that factory, waste streams such as fly ash, which is left over after burning e.g., biomass and coal must lead to new and safe products. The furnace is an ingenious solution for both companies that want to get rid of their waste and companies that want to make new products from it.
Read more about the smelting process that CORE has developed here.
Heat
The team from Eindhoven University of Technology (TU/e) had already demonstrated with an earlier furnace that it’s possible to smelt metals into basalt. Bongers: “However, once it’s hot and molten, what can you do with it? What can you make out of it?” Bongers graduated last year with a simulation of how the process should run in a plant. Now that he can prove that it can be used to make products, he’s now eager to get to work in the factory. But things aren’t quite that far yet.
The student team presented their furnace yesterday to those from the waste industry and the energy world, among others. In the factory hall of the Global Oven Systems company, which helped the team to build the furnace, a group of around a hundred interested people were able to witness the heat of the furnace.
“Unfortunately, four heating ducts broke down yesterday,” says Dirk van Meer, co-founder of CORE Chemistry. “They’re easy to replace – it is a modular system – only the furnace does need to be cold first.” Because the preceding day ‘a bit of testing took place’, the furnace was still hot. “It takes a day or two to cool down from 1,400 degrees centigrade to zero degrees.” Therefore, it was impossible to show how a liquid that resembles honey is cast into a form of a product. As an alternative, the builders tilted the furnace and released the heat.
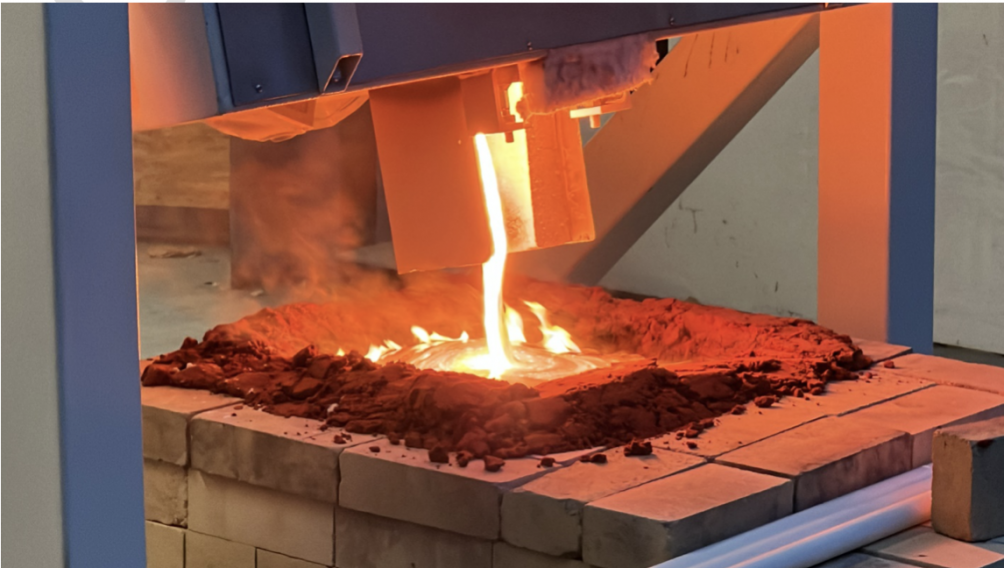
Railway ballast
The waste materials, such as fly ash and sludge, are fed into a large funnel, which then feeds these into the furnace. In the furnace, the substances are smelted to a red-hot liquid. This liquid can be processed on a molecular level which can be used to create new materials. By pouring this liquid into a mould, a variety of products can be made, such as basalt garden tiles or the stones that shore up railway tracks, i.e., ballast.
“When we started with CORE, we were chiefly concerned with the technological process,” says Van Meer. “The question of whether the market would be interested in it came later.” Through the original mastermind of the plant, Gabby van Meer and Dirk’s father, the team came into contact with railway operator ProRail. Railway ballast turned out to be a viable product.
Read more about the origins of CORE here.
The rail ballast manufacturing chain is currently still linear, according to a press release from team CORE. ProRail generates a waste stream of 300 kilotonnes per year. This is currently being disposed of in landfills. Forty percent of the CO₂ emissions from this railway ballast are attributable to extraction and transport and to processing in the Netherlands.
Prorail paid for at least half of the feasibility study on the furnace, Gabby van Meer explains. “Other market parties were willing to help pay for it, but ProRail first wanted to test whether the material was at all suitable for ballast on the tracks.” The company would subsequently share its knowledge with the market. “Which is why we are disclosing this now.”
Appeal to the market
Dirk van Meer: “This was the final preparation for the plant in Moerdijk (the intended location for the plant, ed.). In effect, today is a presentation to the market. We have proven that it is technically possible, but we are just a student team. So, market -please take it up.”
What is needed above all is to succeed in making large quantities of it. The Magma furnace shows that it is can be done, but on a small scale. Large quantities are needed for the railways, says Simon Lubach, climate neutral infrastructure consultant at ProRail.
Lubach: “But if it does work out, it would definitely be a breakthrough. Then we wouldn’t have to rely on other countries for ballast. The railway manager currently sources materials for ballast from countries such as China, Spain. Norway and Austria. “If it can be made in the Netherlands, it will make a huge difference to CO₂ emissions. You have to consider about fifteen to twenty kilotonnes per year,” he says.
The use of ballast has also been a subject of discussion since a TV programme, Zembla, was broadcast about quartz dust. When ballast is processed, quartz dust is released, which is harmful to health. There is no quartz dust in CORE basalt. “This would make it a very good alternative”, Lubach adds.
Flourishing students
For Lubach, the furnace is the first step. There are still many more questions to be answered in order to make it into rail ballast. “How safe is the product? What are its long-term effects? And of course: can it be made in large quantities?”
Gertie Huitink, Head of Industries & Storage at Eneco, also sees great potential in the Magma furnace. “Eneco has been working for some time on the circularisation of fly ash,” he says. He met Gabby van Meer over two years ago. He told Huitink about CORE’s plans. Huitink was hooked. “We started with a bucket of basalt, which then became ten. This furnace shows that we can use our fly ash to manufacture products for others.”
Apart from that, Huitink really enjoys seeing students flourish. “They have the future. It’s great how our experience can be combined with their knowledge of new developments in technology. And that in turn has led to something like this furnace. And if we can now also mass produce, that’s even better.”
The financing of the plant was made possible by ProRail, the Eindhoven University of Technology (TU/e) and two TU/e alumni. Jan van Gemert (former CEO Gemco Casting) and Hans Fischer (former CEO TATA Steel).
View the coverage by Studio040 here.