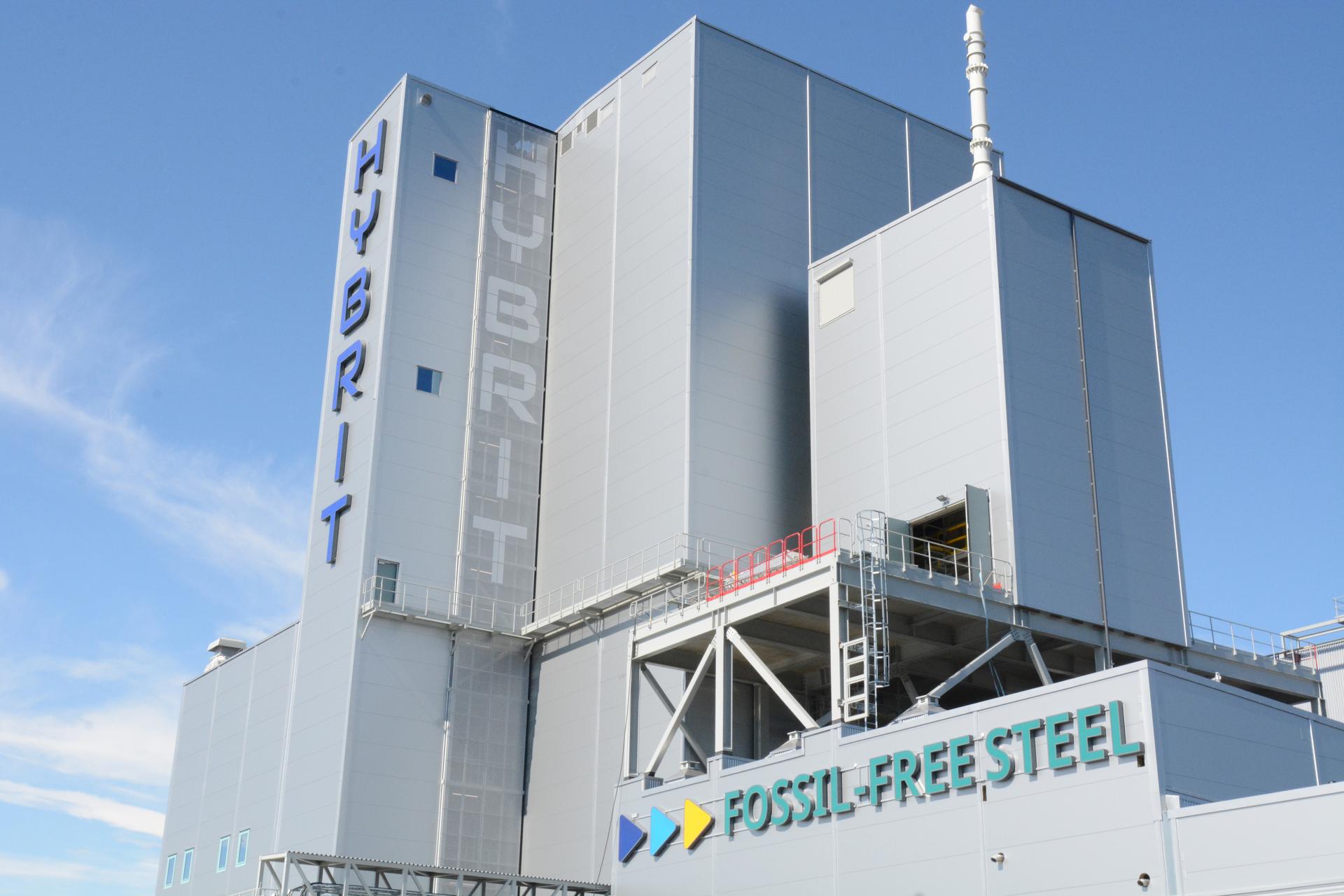
The amount from the European Recovery Fund has yet to be handed over to Sweden. And since the political shifts last fall, the exact allocation of that sum is still unclear. Nevertheless, the government is already disbursing money from the corona recovery fund.
Here’s the thing: Sweden has been looking for items in its state budget that match the aspirations of the European Recovery Fund. Part of that budget include the so-called Klimatklivet (the Climate Transition) and the Industriklivet (the Industry Transition).
IIn fact, these are subsidy funds managed by different government agencies, such as the Energy Agency, the Transport Authority and the Nature Preservation Institution. These various government agencies are authorized to provide financial support for projects – from companies, organizations or private individuals – that contribute to the energy or climate transition of Sweden. The state is assuming that these projects will be paid back by the corona recovery fund retroactively.
The portion of the pending EU recovery funds that Sweden plans to spend on energy transition is likely to be 13.8 billion Swedish kronor, about 1.3 billion euros. Of this, over 270 million euros should go to the transition of the industrial sector, over 500 million to solutions for climate change, 375 million to interventions to conserve energy in apartment buildings and 140 million euros for investments in the railroads.
Circular economy
One area of focus is the circular economy. The Swedish Energy Agency, on behalf of the RRF, has awarded the company Stena Recycling AB 6.5 million euros to invest in a battery recycling plant. The plant, located in Halmstad, should contribute to the environmentally friendly processing of discarded lithium-ion batteries.
With the advancing electrification of society and the development of a more sustainable energy system, the need for batteries and accumulators is also steadily growing. The production and further development of batteries is a prerequisite for the reduction of CO2 emissions in e.g. the transport sector. But in order to minimize the environmental impact of the growing battery production, improved recycling methods of end-of-life batteries are a must. The more batteries that we produce and use today, the more that will continue to end up in landfills in the future.
Accumulators
Currently, there are a handful of European recycling sites for lithium-ion batteries from hybrid and electric cars. These sites typically use smelters that emit large amounts of greenhouse gases. Backed by the European Recovery Fund, Stena Recycling believes it can develop a new technology that processes depleted batteries more efficiently and with a smaller footprint.
“Electrification is a crucial piece of the puzzle in the transition to a fossil-free society,” states Robert Andrén, the director of the Energy Agency, said. “Batteries are going to be a core part of the future energy system.” The recycling project, he went on to say, means “that we will be able to create a value chain for batteries that is sustainable and circular.”
New technology
In a nutshell, Stena Recycling’s new technology entails grinding used batteries in an oxygen-free environment. A sophisticated process then separates the different components so that the valuable metals from the batteries can be reused. Nickel, cobalt and lithium are extracted from the so-called ‘black mass’. Estimates are that this new technology will save around 25,000 tonnes of CO2 emissions on an annual basis.
“We are delighted that our funding application has been approved and we believe it is important to be involved in closing the loop for valuable metals in batteries,” said Fredrik Pettersson, CEO of Stena Recycling Sweden. The battery recycling plant should be ready to be put into operation by early 2023.
Hybrit
Another project that has received an amount from the transition subsidy pot is Hybrit (which we previously published an article about). HYBRIT (Hydrogen Breakthrough Ironmaking Technology) is an initiative of a consortium of the SSAB steel producer, the LKAB mining company and the state energy company Vattenfall. They have jointly set themselves the goal of manufacturing ‘green’ or emission-free steel. The entire chain needs to be cleaned up: from the extraction of iron ore to the steel that is ready for sale.
What makes today’s steel production so pollution-prone is the process that takes place in the blast furnaces. The Swedish SSAB plant ships coal from Australia and the United States which is converted into gas and coke by the steel manufacturer. At temperatures above the melting point of iron, hot metal is extracted from iron ore using coke in the blast furnaces. One and a half tonnes of carbon dioxide: this is ultimately the unwanted by-product of roughly one tonne of steel.
The Hybrit pilot plant is located in the northern Swedish town of Luleå, near its polluting counterpart, the conventional SSAB plant. It is here, in a fifty meter-high grey container, that experiments are carried out involving the replacement of coke with hydrogen. The residual product of this production process is this time not CO2, but rather H2O, i.e. water. Energy supplier Vattenfall is supplying the hydrogen which, it is believed, will continue to be produced exclusively from renewable energy sources.
“The first test phase is complete,” says Anja Alemdar, head of public affairs at Vattenfall Sweden. “We have produced about 100 tonnes of directly-reduced iron in the pilot plant. By doing this, we are demonstrating that it is feasible to reduce iron ore using fossil-free hydrogen gas.” If all goes according to plan, fossil-free steel production should be at full capacity by 2026.
Support us!
Innovation Origins is an independent news platform that has an unconventional revenue model. We are sponsored by companies that support our mission: to spread the story of innovation. Read more.
At Innovation Origins, you can always read our articles for free. We want to keep it that way. Have you enjoyed our articles so much that you want support our mission? Then use the button below: