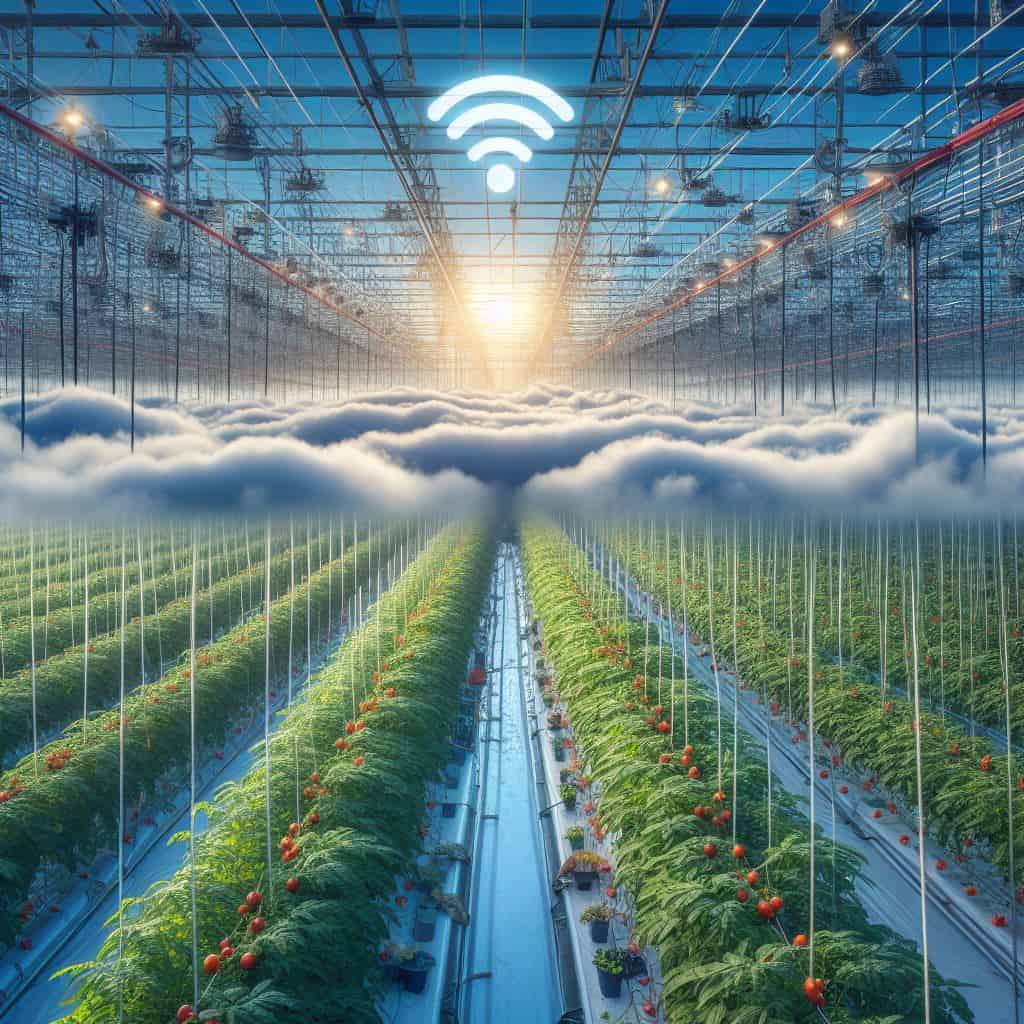
The developments of robotics and AI in greenhouse farming are moving faster than ever. The entrepreneur has the choice of more and more possibilities to help him in the field of repetitive labor like harvesting, support in cultivation in the form of models to set his climate computer, or taking measurements in his crop ‘digitally’. With all these new applications, more and more data is also becoming available on a farm. The first challenge here is to link all the data from the many digital services and products smartly. More about this interoperability challenge in a future column. The question for now is “How do we get all that data, mainly from the greenhouse, to where it is stored and processed?
Cloud computing
In 2006, Amazon launched its Amazon Web Services (AWS). The service allowed users to rent virtual machines as infrastructure for their data and applications. Salesforce began offering software-as-a-service (SaaS) over the Internet around 1999, enabling Cloud computing.
There are several definitions of Cloud computing, according to Gartner:
“Cloud computing is a style of computing in which scalable and elastic IT-enabled capabilities are delivered as a service using internet technologies.” In addition to SaaS, it can be Paas (platform-as-a-service) or IaaS (infrastructure-as-a-service). Currently, an estimated 90% of data worldwide is stored in the cloud.
Storage of data in the Cloud has advantages. No large investments in hardware are required, and scaling up and down of storage and computing capacity is relatively easy. However, there are also disadvantages. Just think of the rules of many countries regarding the ownership, storage, and processing of data.
For real-time applications, there is another major disadvantage: the latency or delay of data transfer over the network. For some applications, that delay is not a problem; think of sending once a day the total number of liters of water given in the greenhouse that 24 hours. But what if a robot needs to use vision to determine whether a rose needs to be harvested and then also needs to stop immediately and point out the rose in question with laser light?
Or, more importantly, if a logistics system in the greenhouse needs to determine in real-time whether it is in danger of knocking over a human or has reached the end of its path. Not stopping in time can have hefty consequences! At these times, data will usually be processed not in the Cloud but “close by” or even in the system.
Edge and fog computing
Edge computing is about bringing computing closer to the data source. It is based on processing data at the “edge” of the network. This reduces the amount of data that must be sent to the Cloud for processing, reducing network latency and improving overall system performance.
Fog computing is a distributed computing model designed to complement edge computing. It extends the capabilities of edge computing by providing a layer of computing infrastructure between the edge devices and the Cloud. This infrastructure, called the fog layer, provides additional application and data services to edge devices.
However, there are quite a few challenges with fog computing. Edge applications in a greenhouse, for example, involve many different applications/devices, all with their own protocol, authentication, and security issues. Therefore, new standards are essential!
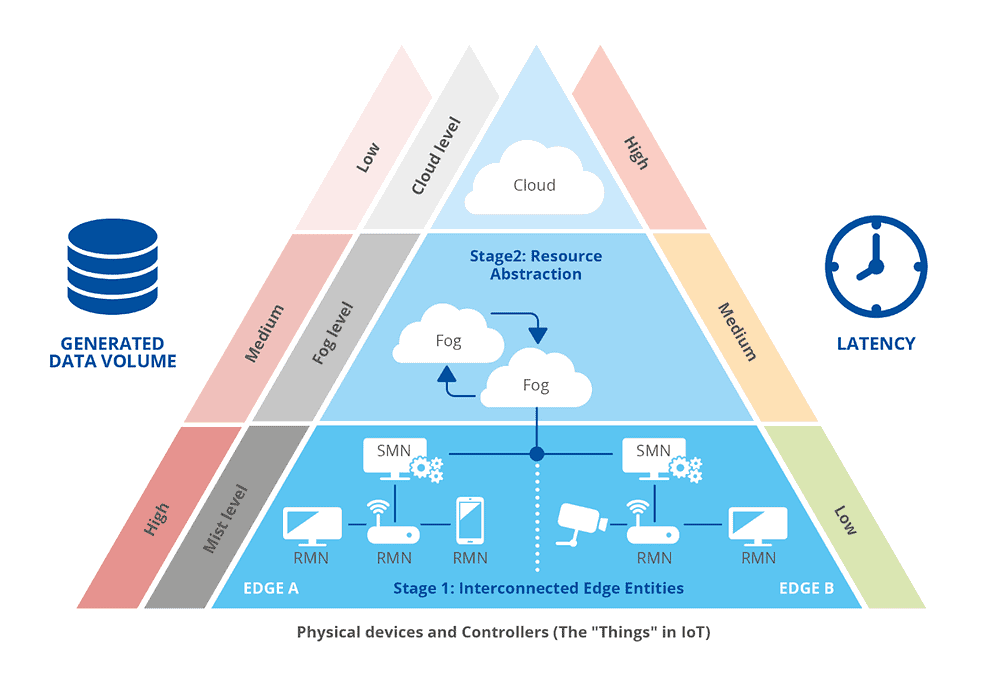
5G
Without edge computing, 5G is a fast network technology developed to transport large amounts of data with low latency and high speed. When many sensors with different types of data use the network, even a 5G network can quickly become overloaded. Therefore, it is important that where possible (part of) the data is processed “on the edge. In addition, using the technique of ‘slicing’, it is possible to divide the network into ‘slices’, each processing a different part of the data stream. Hereby, a difference can be made in speed, latency, and priority of the data in the different ‘slices’.
In greenhouses, 5G offers a solution for transmitting the ever-increasing data collected by sensors and robots. Wifi is often absent throughout the greenhouse or does not work well due to all the steel, glass, water, and dense crop in a crop like tomato. So, technology developers now often develop their solutions with beacons or radio links. The disadvantage is that a horticultural entrepreneur generally uses systems from different suppliers. Thus, each supplier may have to install a different system, resulting in high costs and high maintenance.
Meanwhile, since the end of 2023, a practical 5G test site has been set up on a semi-practical scale in the field lab’s tomato greenhouse, offering data-driven growing at Tomatoworld in Honselersdijk. Together with researchers from TU Delft, TNO, and the company MCS, a private 5G network has been set up that companies can use to prepare their sensors, robots, and other systems in the greenhouse for the commercial introduction of 5G.
Towards a hands-free greenhouse
With the technology available, developers can increasingly make trade-offs about what data to process and store where. Where that will be depends on practicality, risk, and cost.
For a robot where real-time actions are important, processing in the robot itself is now often chosen. High computing capacity and storage combined with low latency then requires, for example, an industrial PC built into the system. Such a PC increases the cost and the weight of the system. Built into an autonomous robot platform, there is a need for larger batteries if the system can still work for a good number of hours without recharge. The moment a lot of data can be sent very quickly with a 5G connection in the greenhouse to a server located, for example, in the company’s barn, the calculation is performed there, and the result returns to the robot almost without delay, the system can become much lighter and cheaper!
Also, sensors or actuators, which are always essential to keep working, can easily be made wireless with a stable and fast connection. With a wireless temperature sensor, it is less of a problem if once a measurement is missing due to an inferior data connection. Therefore, wireless temperature sensors have been available for the greenhouse for years. Wireless control of taps in a tomato greenhouse is a different story. It is often technically possible, but with the ever-growing greenhouses, you don’t want to risk thinking that a water-poisoning tap has been closed wirelessly but hasn’t happened due to a poor network connection!
With all the new developments, there are more and more opportunities to achieve a hands-free greenhouse! How long do you think it will be until we pick a tomato with a robot?