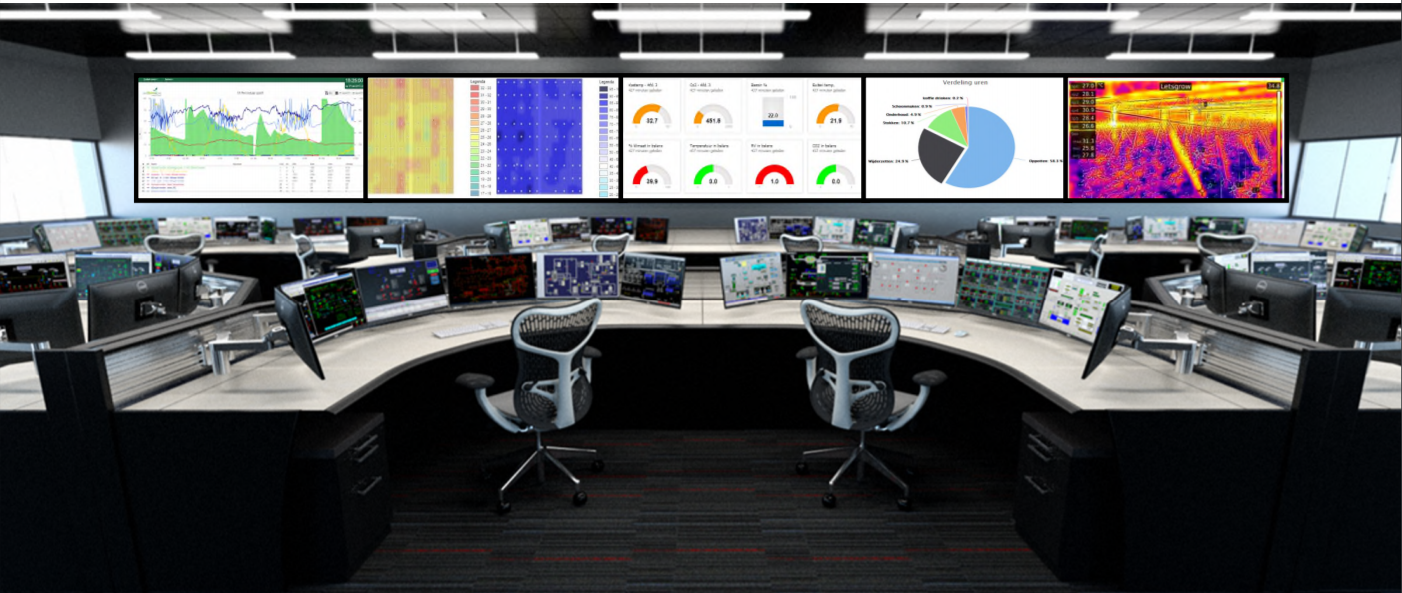
Cultivating crops in our modern Dutch greenhouses has entailed the use of a lot of technology for many years already. The first climate computers were introduced more than 50 years ago. These automatically sent information about the climate and the irrigation status, which was all still analogue back then.
This helped growers enormously. Previously, someone always had to stick around to manually open the windows or give extra water. Over time, a greenhouse has become a production system packed with high-tech components. The volume of information available to the entrepreneur has grown exponentially as a consequence.
The question nowadays is: How it is possible to make the right choice about how this ‘cultivation factory’ can be optimally managed based on this mountain of information? Especially when you realize that the size of these businesses is getting bigger and bigger. All the while, the number of people who have ‘green fingers’ is dropping.
Digitalization in greenhouse horticulture
Technology can play an important role in this. In previous columns, I wrote about innovation in greenhouse horticulture and the need to collaborate with high tech. Plus about the route to hands-free production in greenhouse horticulture.
Autonomous climate control systems that can determine the optimum greenhouse temperature and harvesting robots that support people in greenhouses are great examples of what is already possible these days. Yet these are all partial solutions in an enormously complex system. An entrepreneur at a greenhouse horticultural business not only wants to grow as many kilos of tomatoes as possible but also wants to do this as sustainably as possible. Which is why they take consumer demand into account, as well as the energy price, what supermarkets are demanding and a whole host of other factors. The modern greenhouse horticulture entrepreneur has an enormous amount of data for this from their ERP system, dashboards, cloud solutions, years of experience and often a substantial number of ‘Excel models’.
Horticulture is not unique in this area. Even the manufacturing industry, for example, faces these kinds of challenges. How do you simplify complex systems into something that is understandable and manageable? Two concepts that could help with this are Cyber Physical Systems and Digital Twins. Although there is some overlap in concepts and application, there are differences.
Digital Twin (DT)
Digital Twins have their origins in product life cycle management. The term was first coined in 2003, but the earliest practical applications did not appear until around 2013. A DT is a recreation of a physical or virtual object or system. A DT of a physical system is often represented in a lifelike way by using virtual or augmented reality. Data and models form the basis of a DT.
Applications for DTs can be found in the development of products or production processes and for training purposes. In greenhouse horticulture, for instance, the WUR is working on a DT of a tomato crop.
Cyber Physical Systems (CPS)
Cyber Physical Systems are seen as the core of Industry 4.0 in Germany. The term CPS was first used in 2006 and stems from the application of embedded systems. A CindusPS, like a DT, describes the integration between the physical and digital worlds.
While a DT uses a digital representation of the physical world, with a CPS, there is a direct link to the actual physical world. Consider, for example, a robot. Sensors and actuators can be seen as the basis of a CPS. At the moment, the applications of CPS are mainly found in (scientific) research. But over the coming years, frameworks will be developed that can be applied in actual practice. CPS can be used to establish real-time interaction of models and physical processes or commodities. This can be done in a robust, safe and efficient manner as well.
(System) developments in greenhouse horticulture
DT and CPS can also be used in combination with each other. A DT comprising data, apps and services as well as decision-making models can also include a digital representation of e.g., a picking robot. If this digital twin is linked to the real picking robot, it is then referred to as a cyber physical system.
For greenhouse horticulture, the ‘Growing-as-a-service concept is seen as the place where all the knowledge about autonomous production converges. You do not buy a greenhouse or a tomato factory, but x kilos of premium quality tomatoes per week. In order to produce these, you need, among other things, a suitable space, plant material, water, nutrients, knowledge of cultivation and a workforce. All of these components can be seen as building blocks that are already in the process of being developed at the moment.
Harvesting robots
As an example, the Blue-Radix company is developing AI models for autonomous climate control in greenhouses. Others are also working on these kinds of building blocks. Furthermore, there is already a great deal of data available from all kinds of sensors in greenhouses. Several companies are also working on robots that can assist in predicting the harvest, detecting diseases and pests and the harvesting itself. If these various data sources are combined with the knowledge of the grower in what is known as data-driven cultivation, numerous other possibilities present themselves.
The following challenge is to combine and link everything inside and outside the greenhouse. Here, the industry can serve as a good example for greenhouse horticulture. Plans are now underway to combine the first building blocks into a digital twin. When considering how robots and other systems in greenhouses are controlled, the development of cyber physical systems seems a logical next step. It will take some time, but I certainly think that the day will come when the knowledge from data, sensors and models will instruct a robot how to pick tomatoes!
About this column
In a weekly column, alternately written by Bert Overlack, Eveline van Zeeland, Eugene Franken, Helen Kardan, Katleen Gabriels, Carina Weijma, Bernd Maier-Leppla and Colinda de Beer, Innovation Origins tries to figure out what the future will look like. These columnists, sometimes joined by guest bloggers, are all working in their own way to find solutions to the problems of our time. So tomorrow will be good. Here are all the previous articles.