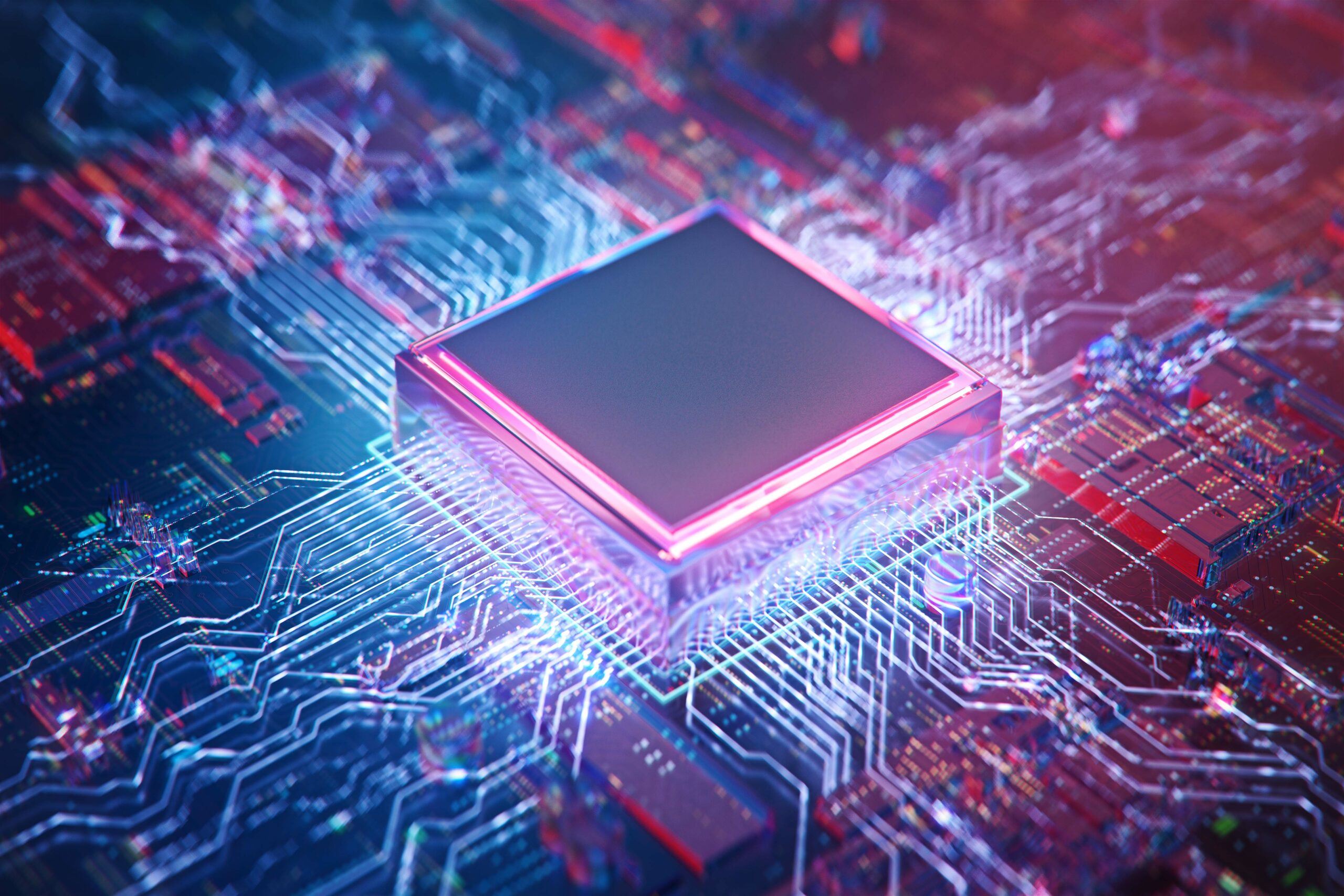
In the chips of today, gold wiring has been almost completely replaced by copper. NXP in the Dutch city of Nijmegen is now working on a new generation of chips in which precious metals are no longer needed to make connections.
Producing a chip without connecting wires is cheaper and more sustainable. However, such a switch cannot be made from one day to the next.
Leader
The development around making chips more sustainable has been going on for years. In 2005, NXP was one of the first semiconductor manufacturers to switch from gold to copper. “The notion was always that gold wire was by far the most suitable material for making the connections. But from a cost-saving perspective and with an eye on sustainability, we wanted to look for another solution”, explains Pascal Oberndorff, Research & Development packaging manager at NXP.
Less harmful
This required extensive research. Copper has different properties to gold. It is easier to mine, is less scarce and less harmful chemicals are used to extract the raw materials. As such, copper is better for the environment, but is the quality just as good for use in chips? The ultra-thin gold wires (approximately one twentieth of a human hair) bond and conduct well, and they are not susceptible to corrosion. Copper is different. Copper, for example, can rust. “By treating and wrapping the copper wires in a special way, the quality turned out to be even better than that of gold,” Oberndorff says.
100 kilometers of gold wire
NXP was a leader in this. After a merger with Freescale in 2015, the development proceeded even faster. By now, approximately 90 percent of the gold in new chips has been replaced by the thin copper wires. This yields cost savings of many millions of euros per year. Oberndorff: “Very little gold goes into a single chip, but because of the enormous number of chips that NXP in Nijmegen alone produces, about 15 billion euros a year, the amount of gold wire involved was about 100 kilometers in length per year, which has now been replaced by copper.”
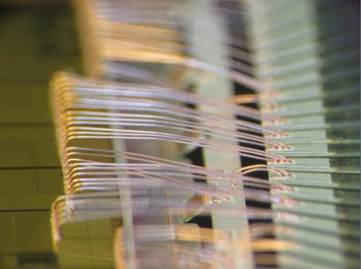
Chip without wires
The switch from gold to copper has been accomplished and since become commonplace in the semiconductor industry. At NXP, work is now also underway on the next step: a chip without wires. “In actual fact, the wires interfere with the signal. If you don’t use wires but solder the connections with tin instead then the signal becomes stronger and faster,” Oberndorff says. Better heat conduction in the new chip can also be achieved which allows for higher output and more functionality. “At the same time, this kind of connection is more sensitive, so once again, it requires a lot of research into how to make the chip extremely reliable.”
New packaging
Research is also being done on a new wrapping for the chip. “The plastic shell that surrounds the chip to protect it is up to five times larger than the chip itself. Since we want everything to be smaller and smaller, it would be a huge step forward if the wrapping were barely larger than the chip itself.” Another development is that in the future several chips can be put into one package.
Billions of chips are made in Nijmegen. Oberndorff: “However, the assembly of this newest type of chips, such as radar chips, is done in Asia in factories that specialize in this.”
Also interesting: Dutch automotive sector pushes safe, energy-efficient chips