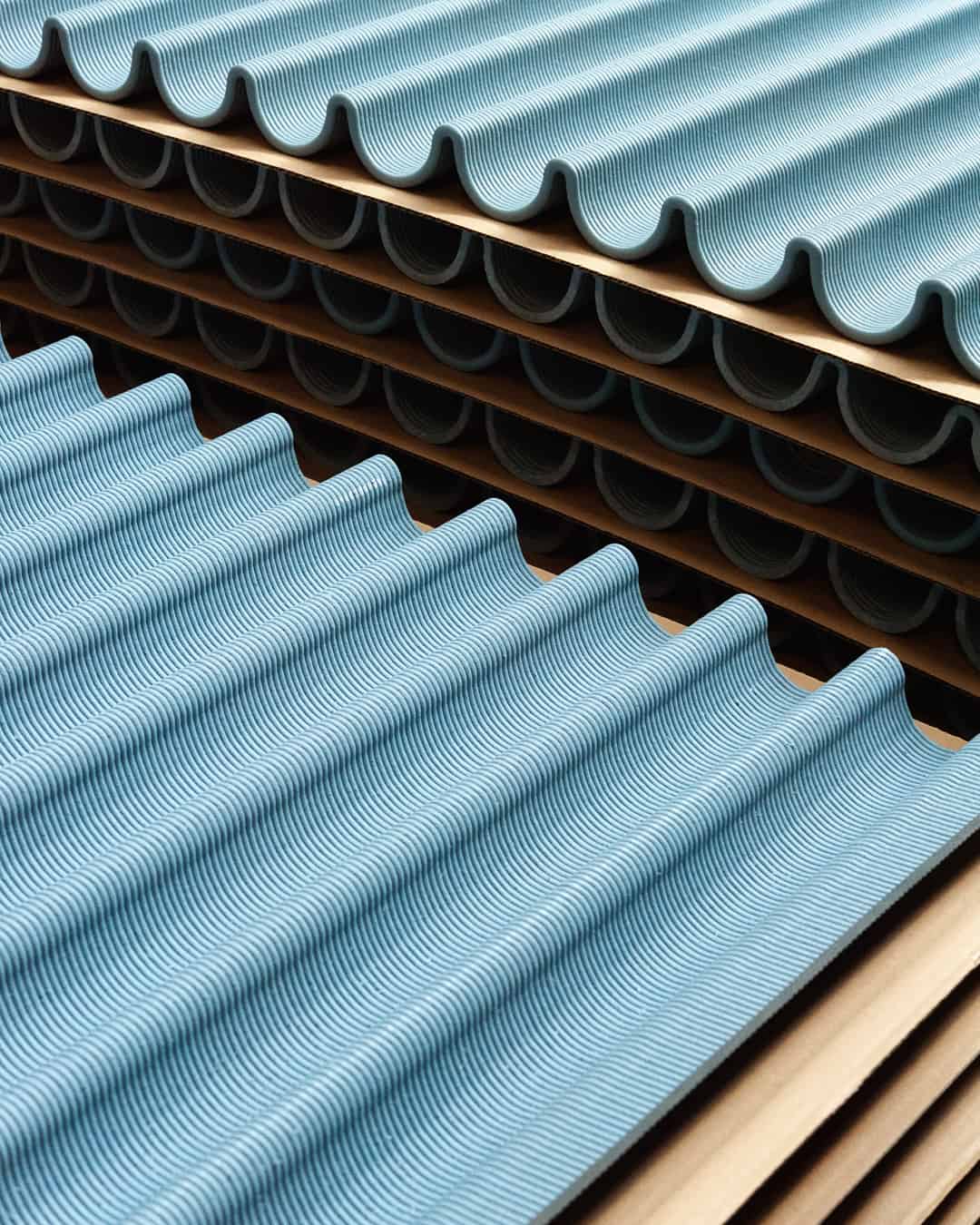
Europe is moving towards a fully circular economy. More and more laws and regulations are being introduced that entrepreneurs have to comply with. They can make a big impact by making the design of their buildings more sustainable. Start-up Aectual creates interior design through a data-driven 3D printing process from waste, taking the construction industry to the next level. “We want to shift the focus from what ‘sounds green’ to what actually ‘is green’,” says Hans Vermeulen, ceo and co-founder of the company.
Why you need to know this:
We need to get rid of the idea that discarded products belong in the ‘waste’ category. We can reuse used items as raw materials for new interiors. Aectual shows how.
Plastic from the sea, used packaging: some see it as waste, but Aectual uses it as a valuable raw material for 3D printing interiors. The products that roll out of the printers are certainly not inferior to ‘regular’ interiors. The fact that the floors, facades and acoustic panels are made from plastic waste is not apparent. In short: the Amsterdam-based company is progressive. That is why the company was recently awarded the Fit For the Future Certificate by Vodafone Business; a certificate for companies that score above average on a number of FFtF criteria, such as technological development and ability to move with a changing market.
More and more measures
Companies and institutions in Europe will increasingly focus on sustainability in the coming years. With the Green Deal, Europe is aiming for sustainable, circular products, among other things. Attention to circularity is also on the national level. In the government-wide programme Nederland Circulair in 2050, the government describes what is needed to deal more economically and smartly with raw materials, products and services. The Dutch government set itself the goal of fully circular procurement as early as 2030.
However, it will take some time before the majority of Dutch companies follow suit. Although some eighty per cent of entrepreneurs were taking measures to become more sustainable by 2023, especially in the field of energy, only 15 per cent have undertaken initiatives related to the circular economy, which means being environmentally conscious in dealing with raw materials and waste.
A dynamic world
The construction sector in particular still has a long way to go, knows architect and ceo Hans Vermeulen, who at the start of his career never thought he would start a company focused on 3D printing. “Years ago, as an architect you were concerned with designing design that would last for a very long time. Today, however, hotels, shops and offices change their interiors on average every five to seven years. A shame if all the materials used then end up in landfills. With our solution, buildings are brought back up to date in a sustainable way.” It works like this: “We create a digital design file for the customer based on their requirements. This file can then be sent to any 3D printer suitable for it. Once companies want to get rid of their product again, we take it back, grind it into new granules and use this material again for new products.”
The benefits of 3D printing
Waste-based printing not only reduces waste, but also CO₂ emissions (namely: 80 per cent CO2 reduction per cyclys). Using recycled material requires less energy and raw materials than traditional production methods.
The printing process itself is also sustainable. This makes it possible to create unique, customised designs for customers. Stockpiling excess stock, some of which often still ends up in landfills, is no longer necessary. “Moreover, we work with customised print files. So there is no cutting loss. This also saves a lot of waste and energy. Certainly also advantageous for the excel sheet, by the way. The cost side, so to speak,” Vermeulen says with a laugh.
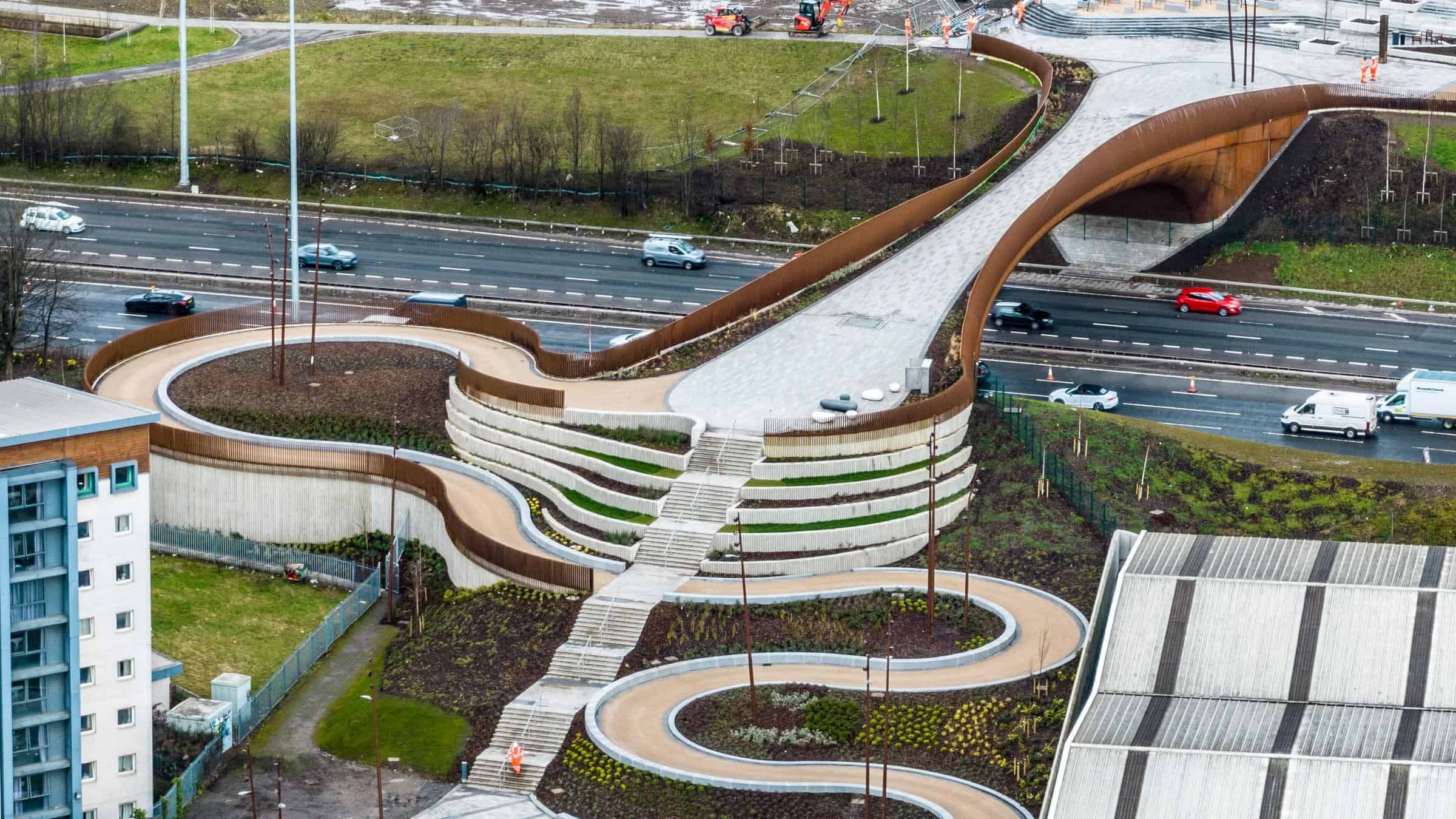
Interior made of milk cartons
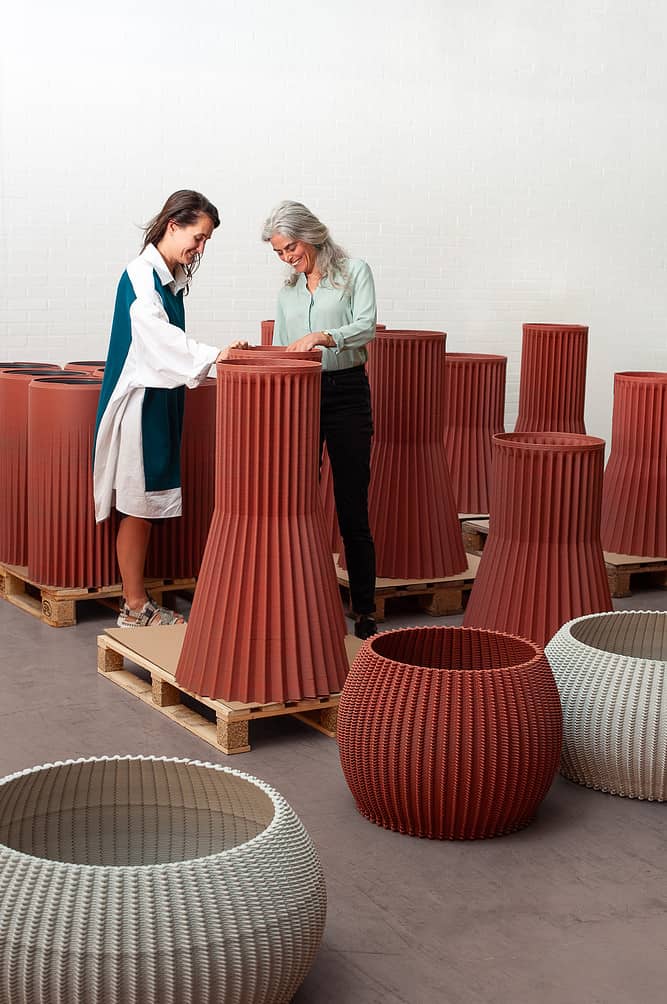
Among other things, the Amsterdam-based company processes used milk cartons in its waste streams. “We work together with Tetra Pak. They produce some two hundred billion packages a year. Three-quarters of these consist of cardboard, which is recycled into toilet paper, for example. The remaining 25 per cent of the packs consist of plastic and aluminium, to prevent leakage and extend shelf life. We use this residual material in our products, which can be found in all 160 Tetra Pak offices. Think stools, planters, wall panels, room dividers and window screens.” Aectual also produced 3D-printed flooring for several Nike shops worldwide.
Aectual is also looking to collaborate with smaller companies and young designers. “We want to open up design to everyone,” Vermeulen explains. Therein lies immediately the big challenge. “Large-scale 3D printing is a growing market, and fortunately the number of 3D printers that can work on a large scale is increasing worldwide. Ultimately, the idea is that we will also produce more and more locally, so that we can significantly reduce the number of transport movements.”
A(e)ctual green
Meanwhile, the company has built up a very extensive database of products. Vermeulen sees opportunities to make smart use of this rich source of information in the future. “We are aiming for a system where not only individual floors or wall panels are printed, but where our customers can put together a complete building. They can choose from different material types and designs, while our system shows details about the ecological footprint, production location and so on. Ultimately, we want companies and agencies to do more than just tell pretty stories about how sustainable they are. We hope to shift the focus in the construction industry from ‘what sounds green’ to what is actually ‘ green’.”