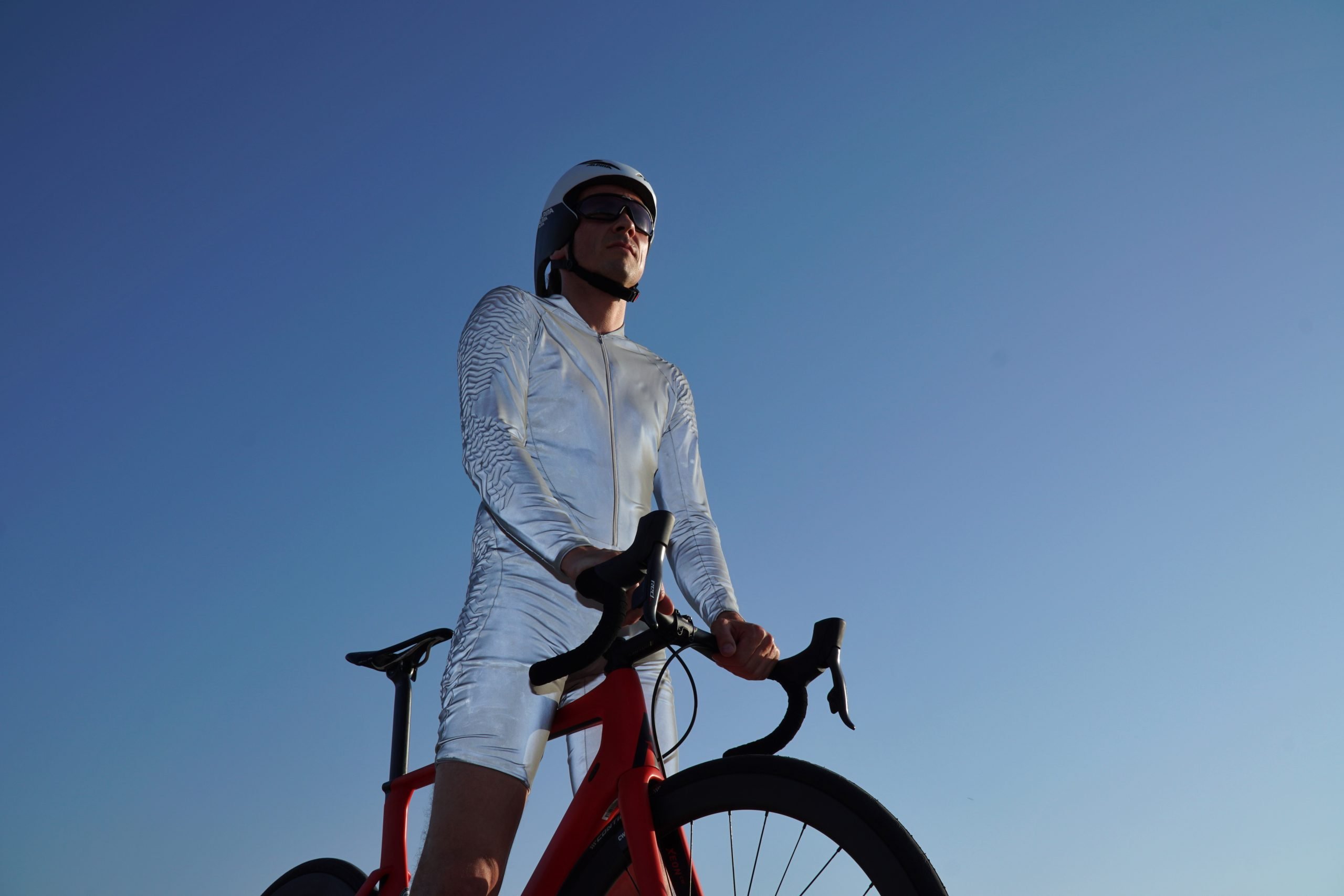
The Munich-based start-up GRDXKN has developed a new technology that gives textiles specific properties in the printing process. The innovative material can be used in many different ways – for example in the acoustic, interior and automotive industries. There are already pilot projects for protective sportswear on asphalt – such as biking, where functions such as durability, abrasion resistance and shock absorption are in demand. When simulating a fall at 30 km/h, a textile printed with GRDXKN showed the multiple abrasion resistance of Lycra.
We interviewed the company’s founder, Bastian Müller:
Bastian Müller (c) Natalie Weinmann
How did the idea for your start-up GRDXKN come about?
I studied product design at the Burg Giebichenstein College of Art in Halle an der Saale, Germany. In my master’s thesis, I dealt with luggage and the partially different demands on the material strength of, for example, luggage bags and handles. I wanted to work homogeneously and thought about how I could use textiles and techniques to partially create different functions. In doing so, I looked into printing processes and it quickly became clear that this was an approach worth pursuing, despite the fact that I was not able to solve problems such as material breakage caused by tension in my thesis.
After my first job working on the team of industrial designer Stefan Diez, I moved to the Akademie der Bildenden Künste in Stuttgart in 2014, where I worked as an assistant in the Industrial Design department. Here I had the opportunity to follow up on the work I started in my master’s thesis and solve the problems by cooperating with manufacturer using trial and error.
GRDXKN is a printing process, a technology – and then you decided to set up a PR label. What was the background for that decision?
In the development phase I tried to start a cooperation with a British manufacturer of bicycle saddles. After he retired, I decided to set up a PR label to show what was possible with the printing process. First it was a bag collection that I launched under the name Mimicri. The feedback was good, and when a colleague became interested in the label, I licensed it for the first time.
I wanted to further develop my printing process to show the full potential of the technology. In my thoughts, the e-bike quickly took me to clothing – and the lack of cool, lightweight, comfortable and protective cycling clothing. I developed various products, founded the Patronace PR label and exhibited them at the Eurobike, Ispo and Outdoor trade fairs. There was a lot of interest and in 2019 the ball started rolling. Now it’s time to explore different areas and develop appropriate products. A number of pilot projects are underway.
What is your motivation? What problem do you solve and why is that important?
We print on textiles thereby controlling the behavior of the material and its technical properties. The printing process is based on components from textile printing and coating technology. The main component is polyurethane. The process is water-based and solvent-free and thus much more sustainable than chemically processed polyurethane. The technology paves the way for a completely new design of protective clothing.

What was the biggest obstacle you have had to overcome?
The enthusiasm of industrial partners is high, but the patience for carrying out a pilot project is always a challenge. I am idealistic and think that a pilot project should not only be about numbers. First of all, I follow the ideal, even if I that means I have to decide differently for cost reasons. With that attitude I will hardly get an investor – I’ve already realized that – but I’m sure that the start-up can be transformed into a financially viable project. It also takes courage and I have decided to move forward with it.
What have been the best moments so far? What achievements made you really proud?
I am proud of our cooperation partners. The top ten in the sporting goods industry are in constant contact with us and are considering how they could use this printing process.
Where would you like to be with GRDXKN in five years?
I would like to continue working as a designer – and work on exciting new applications. Until then, I would like partners to incorporate this technology into their DNA. The structured surface of the protective textile can be seen from a distance, so manufacturers could brand that for themselves.
What makes your innovation better/different than existing things?
Integrated and washable protectors do not yet exist in urban biking. I haven’t found anything comparable yet.
Link to the Patronace video.
Interested in start-ups? Read all articles from our series here.