
With the commissioning of the HYBRIT pilot facility, the steel and iron industry has taken a huge step in making their production more sustainable. The rock cavern storage facility for the storage of fossil-free hydrogen gas is the first of its kind in the world. The test period will continue until 2024.
The HYBRIT initiative was launched in 2016 by steel producer SSAB, the LKAB mining company, and state energy company Vattenfall. The hydrogen storage facility will play a very important role in the overall value chain for fossil-free iron and steel production. Producing fossil-free hydrogen gas when there is a lot of electricity and using stored hydrogen gas when the electricity system is under strain, will ensure the production of sponge iron, the raw material behind fossil-free steel.
“The fact that this technology is now working is great news and is an important milestone in the development of a fossil-free value chain for ore-based iron and steel production. The use of large-scale hydrogen storage means that the industry will have a more robust and plannable supply of hydrogen from fossil-free electricity, even when the electricity system becomes more dependent on the weather. This enables us to make very efficient use of our fossil-free wind power production,” says Mikael Nordlander, Director of Industry Decarbonisation, at Vattenfall.
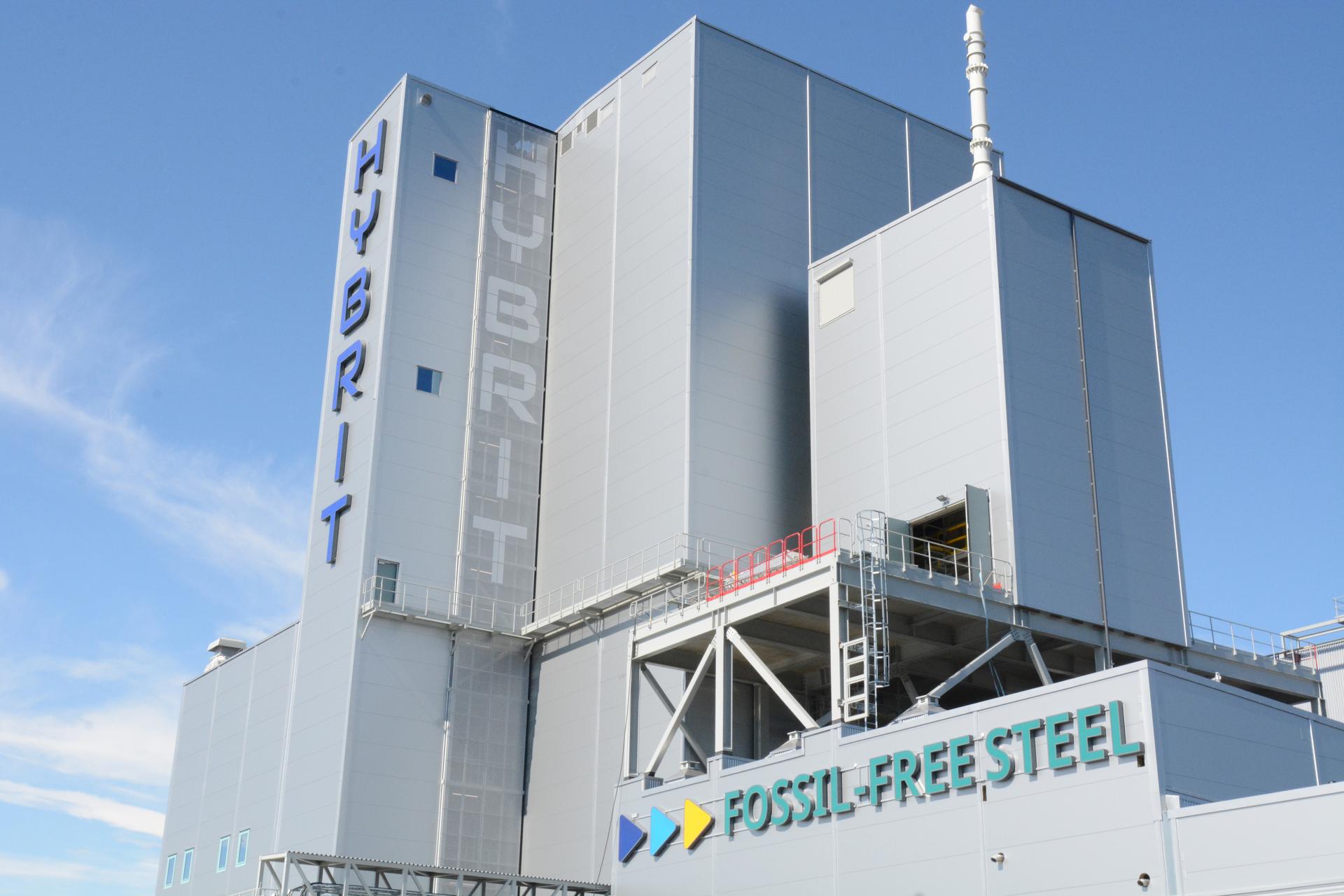
Sealed rock cavern
The pilot facility works according to its design and meets all safety requirements. The technology for the storage of gas in an underground lined rock cavern (LRC) involves the cavern walls being lined with a sealing layer. The pilot facility is the first in the world to test the technology with repeated filling and emptying of hydrogen gas. The pilot facility’s size is 100 cubic meters. At a later stage, it may be necessary to keep 100,000 to 120,000 cubic meters of pressurized hydrogen gas in full-scale storage, which is enough to supply a full-size sponge iron factory for about three to four days.
“It’s very positive for us that the hydrogen gas storage pilot facility is up and running and that the technology has worked as it should up to now. That’s another important milestone. Now we’ll bring the plan to completion with test campaigns and collect important data and knowledge to make a full-scale facility possible,” says Martin Pei, CTO at SSAB.
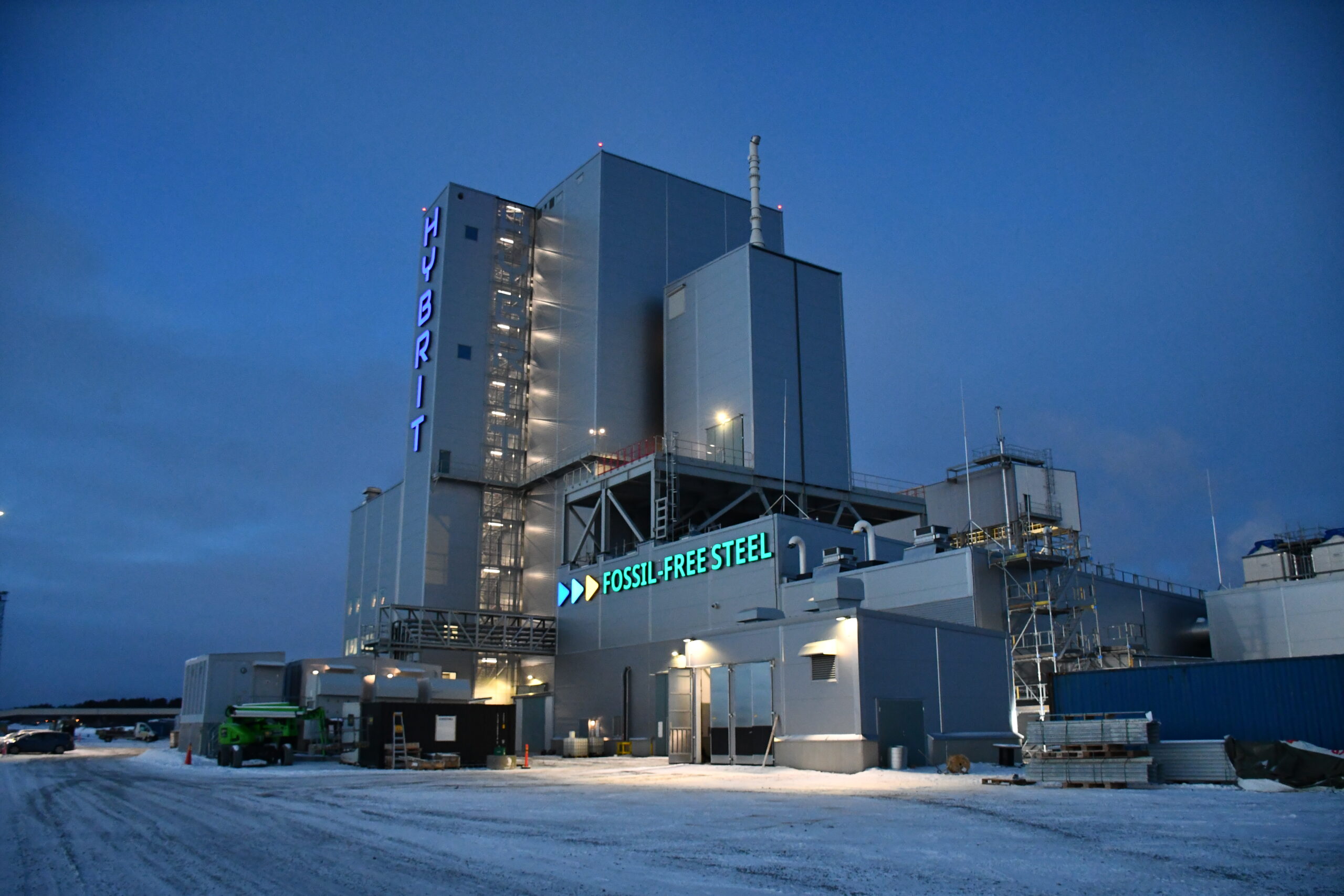
Selected for you!
Innovation Origins is the European platform for innovation news. In addition to the many reports from our own editors in 15 European countries, we select the most important press releases from reliable sources. This way you can stay up to date on what is happening in the world of innovation. Are you or do you know an organization that should not be missing from our list of selected sources? Then report to our editorial team.