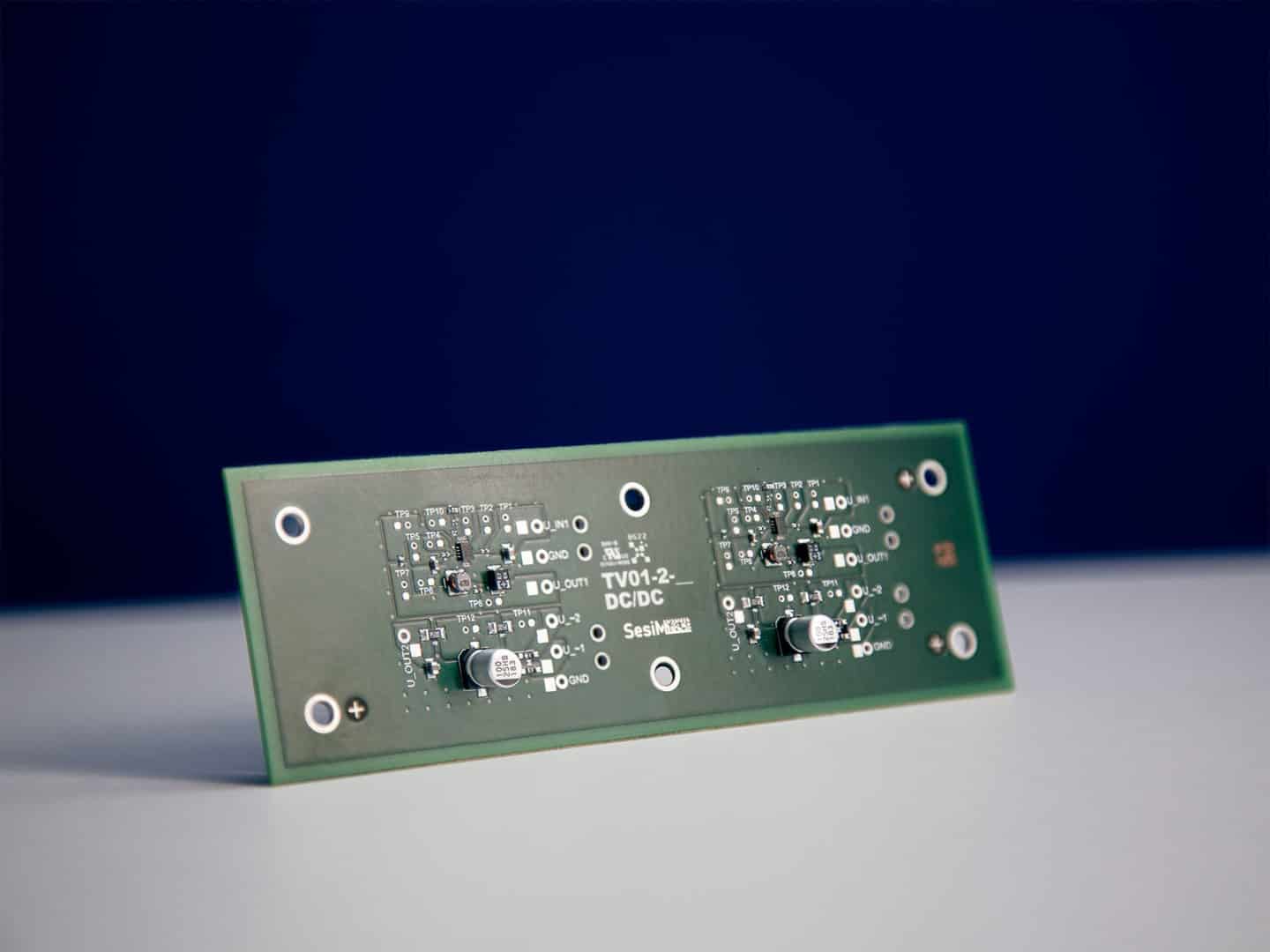
A new method will make it possible for electronic systems to detect signs of wear or manipulation at an early stage before an actual failure occurs. This new process is initially being developed and tested for safety-critical applications in the automotive and rail sectors. The basic principle can, however, be transferred to many more application areas, says the Fraunhofer Institute for Reliability and Microintegration in a press release.
The problem for safety-critical systems has often been solved in practice with overdesign and redundant features. One such example is electronic systems or parts thereof that are installed in duplicate so that when a fault occurs, the backup system can take over until the problem is fixed. A research project at Fraunhofer contributes to a future of more elegant, sustainable, and energy-efficient solutions in this area. As part of the SesiM project, Fraunhofer researchers are working with other mobility and artificial intelligence partners to find self-validation solutions for complex electronic systems.
“We are more interested in the state before the electronics are broken than when they are actually broken,” explains Dr. Johannes Jaeschke, electrical engineer, and the Fraunhofer Institute. “Long before a system fails, certain functions can be compromised, for example, when materials become brittle. The mechanical stability of the component often does not provide early enough detection of signs of aging. This makes it a struggle to monitor electronic systems.”
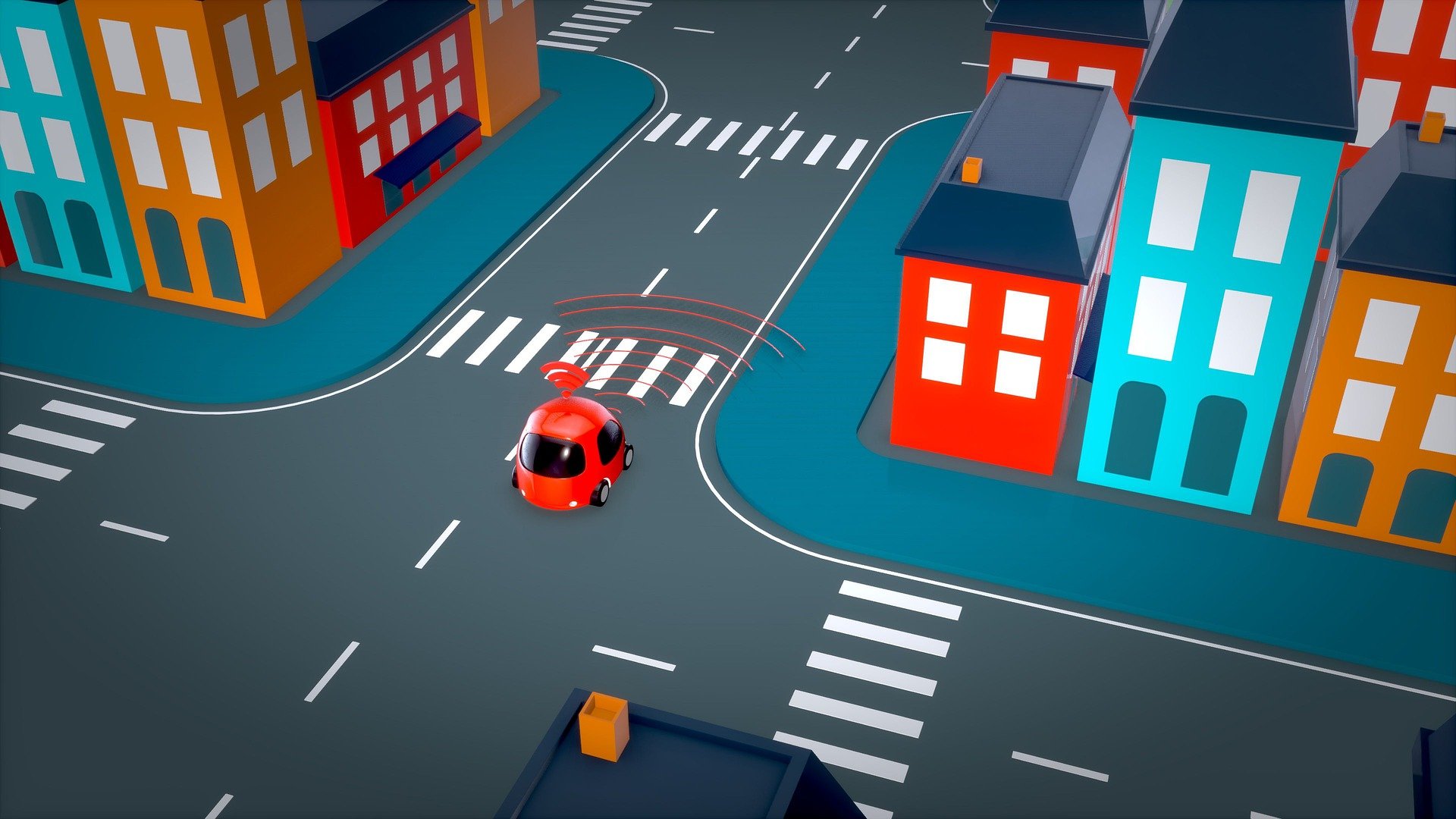
Making gray from black and white
The project’s researchers use a so-called grey box model. It has acquired this name as it is based on both white box and black box approaches. The white box model is based on physical processes and modeled around boundary conditions such as temperature or humidity. Because it is clear how this type of model functions, it is called a white box model. However, the more complex an electronic system is, the harder it is to map and monitor it on a purely physical level in a holistic manner. Complex structures and large amounts of data are no problem for data-driven models that use artificial intelligence. However, what happens inside these systems remains unclear – hence the name black box model.
For many years, Fraunhofer has been working intensively on electronic systems at a physical level. With their expertise in measurement technology and design, the researchers can develop models for condition monitoring and forecasting based on physical processes. “We can combine the best of both worlds in grey box models,” summarizes Jaeschke. “This is why we are also referring to it as hybrid modeling. We can process a vast amount of data while, at the same time, understanding the physical reasons behind changes in the signal. This way, we can increase trust in our data.”
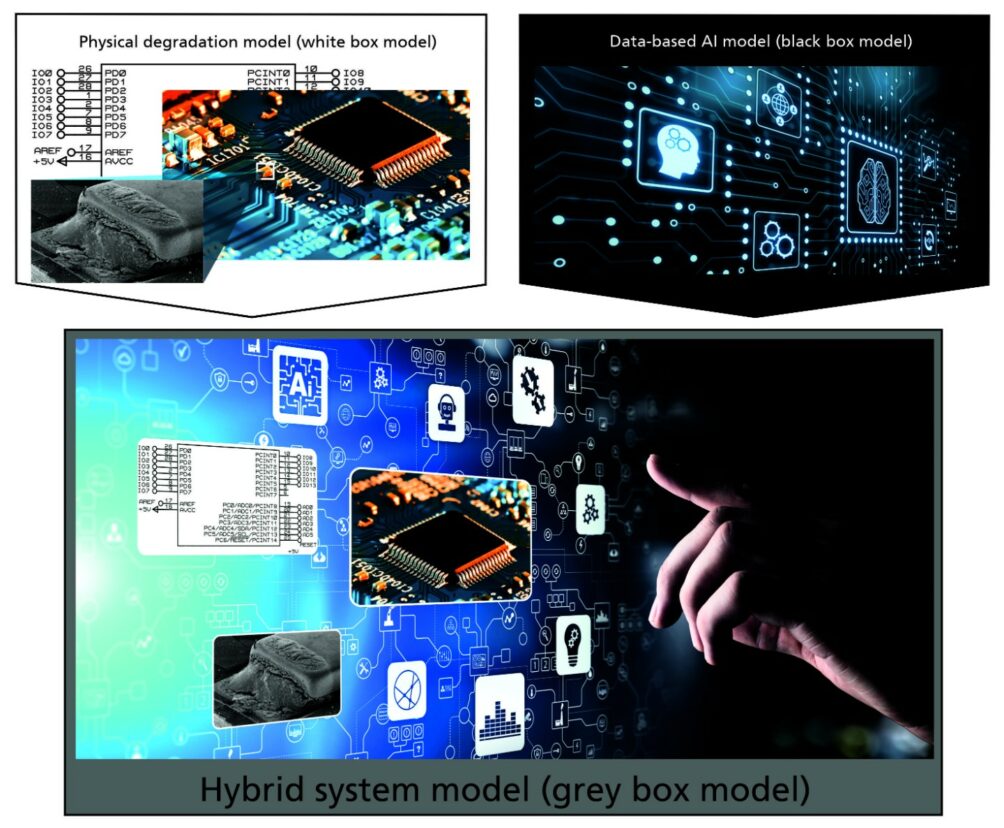
Prototypes
To date, practical applications of grey box models are largely unchartered territory. So, after an initial design phase, the SesiM researchers are now also working on describing simple circuits that will increase in complexity as the research project progresses. The test PCBs are measured and tested during production and then in their operating state. “By doing this, we are generating a digital fingerprint for our test wiring,” explains Jaeschke. This means that data will be collected even under extreme boundary conditions.
The next step is to identify the parameters within the large amount of data that are relevant for mapping the system and then, taking into account the physical knowledge, to create a model that detects deviations from a predefined ideal state. External manipulations should thereby be recognized as quickly as possible, and wear can be forecast early on. At a later point in the project, the test PCBs will then be transferred to prototypes for automotive and rail applications, which will be used to analyze the models created extensively.
Potential for a range of applications
In the future, it may therefore be possible for an integrated intelligent system in a car to provide an early warning for a problem with the electronics, offering a self-diagnosis. When servicing a car, mechanics will then be able to view all of the information collected by the vehicle about its condition and make targeted repairs on the basis of this information.
The overarching aim of SesiM is to initially prove that the basic principle that electronic systems can self-validate using grey box models actually holds true. Jaeschke has faith in the idea: “If we succeed, our approach will significantly contribute to increasing the reliability of electronic systems. It is hugely important, particularly in the safety-critical mobility sector, and would further strengthen the reputation of automotive and rail technology developed in Germany.”
A follow-up project by researchers at Fraunhofer will focus on the topic of aviation. Applications outside of the mobility sector are also possible — for example in medical engineering and offshore windfarms, for which regular external monitoring and preventative maintenance are difficult to carry out.
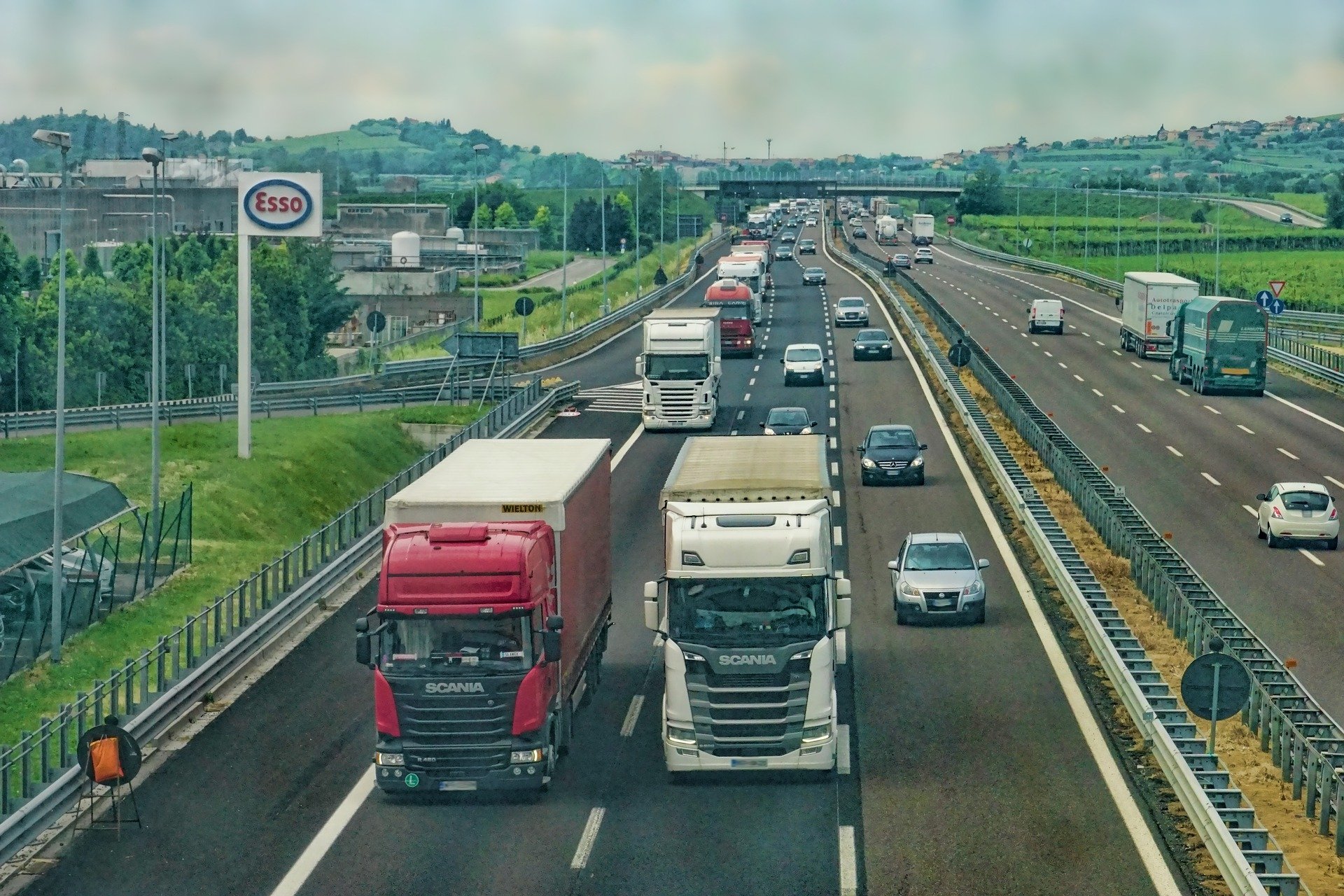
Selected for you!
Innovation Origins is the European platform for innovation news. In addition to the many reports from our own editors in 15 European countries, we select the most important press releases from reliable sources. This way you can stay up to date on what is happening in the world of innovation. Are you or do you know an organization that should not be missing from our list of selected sources? Then report to our editorial team.