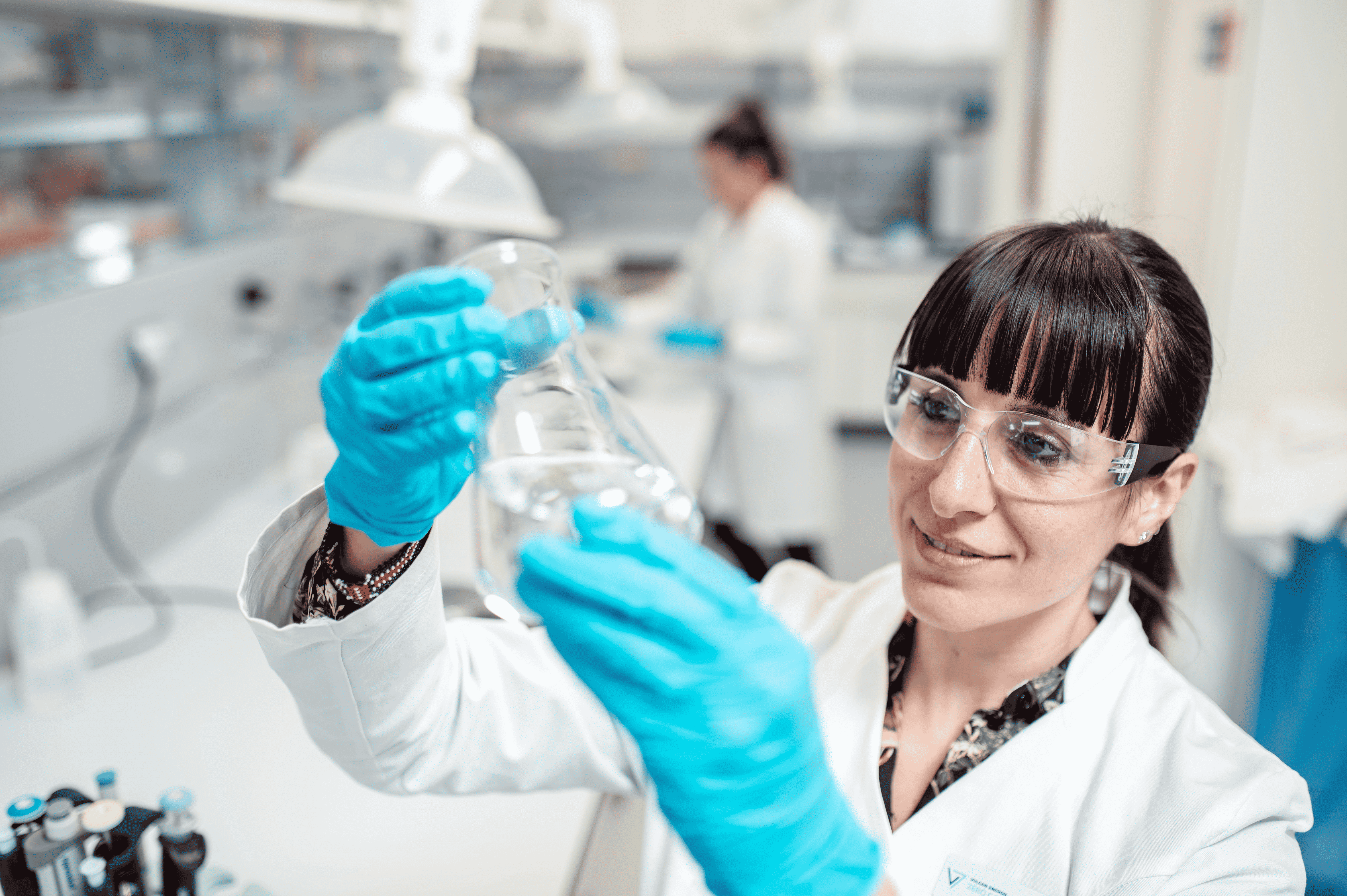
Ancient castles, romantic landscapes, and lithium. All three can be found in the Upper Rhine Valley. While the first two might represent good reasons to visit the region – an area stretching alongside the border between Germany and France – the third can have a broader impact on our lives, as it is the most-needed material for electric vehicles (EVs) batteries.
- Vulcan Energy will produce lithium in Germany in a climate-friendly way.
- The company uses geothermal power and established technology in the chemical industry for its process.
- European automakers signed deals with the company as production is set to start by the end of 2025.
This region is where, with its Zero Carbon Lithium™ initiative, Vulcan Energy wants to make a difference. The German-Australian company developed an innovative lithium extraction process that combines geothermal energy and industry-proven refining processes. This results in an environmentally friendly manner of producing the material.
Current lithium extraction methods – hard rock mining and evaporation ponds – utilize massive fossil fuels, chemicals, and water inputs. “If you think that for every ton of lithium hydroxide produced, 15 to 30 tons of CO2 are emitted, it is a big figure, and we think we can have a material decarbonizing effect,” says Francis Wedin, chair and founder of the company, which employs over 320 people.
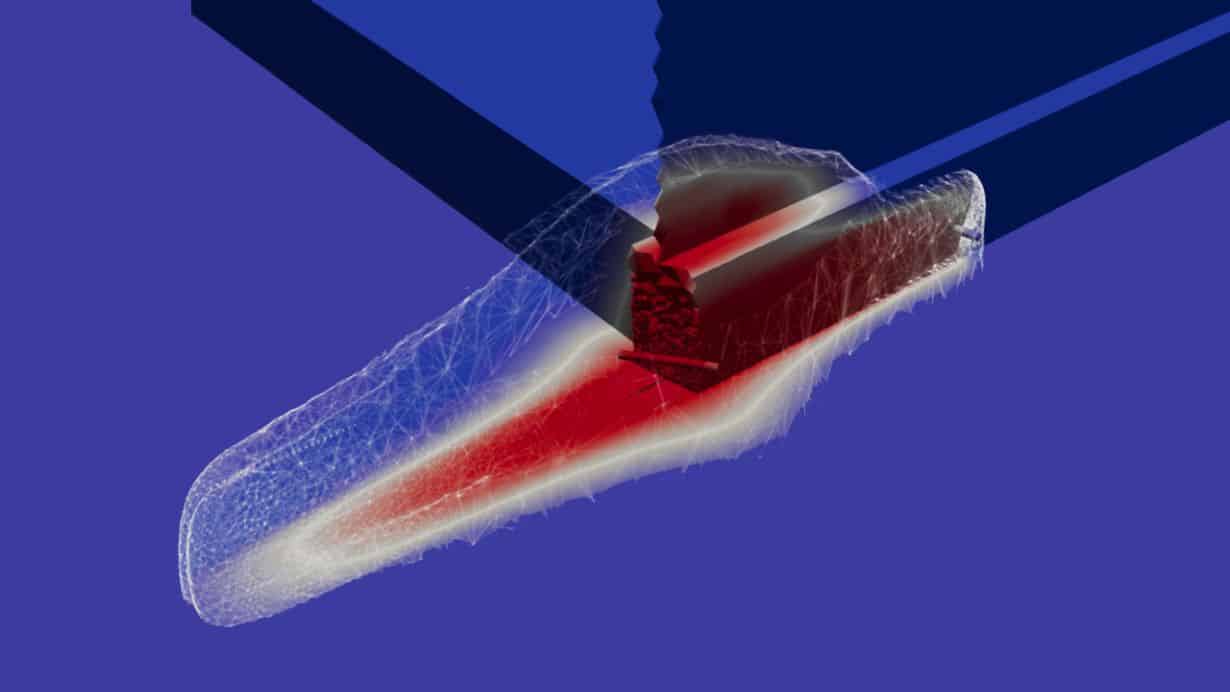
Pumping brine up, lowering emissions down
A geologist by training, Wedin previously founded a lithium extraction company in Australia in 2014 after learning about the surge the lithium market would have had in the following years. The venture was relatively successful, with its founder stepping out in 2018 following a takeover. “Through that journey, I learned how high the carbon footprint of lithium production is. I then started looking at ways to decarbonize it. It all began with a clear brief: using commercially proven methods and bolting them together to engineer out fossil fuels,” he explains.
Vulcan’s lithium extraction process relies on lithium adsorption, which has been commercially available for nearly 30 years, and chemical procedures used in the chlor-alkali industry – a branch of the chemical industry that uses these methods to produce chlorine, for instance – for a century. Geothermal wells are drilled underground, bringing hot brine to the surface and transforming steam into electricity or renewable heat. In conventional geothermal plants, brine would be pumped to the underground again. Instead, it goes to a direct lithium extraction plant, passing through resin-filled columns that adsorb lithium. The remaining brine is pumped to the underground reservoir.
The resin beads are then washed with water, concentrating the solution with renewable energy. This produces a lithium chloride concentrate, which is transported to a lithium processing plant. There, it gets electrolyzed, finally becoming battery-grade lithium hydroxide. Besides low water and land area consumption – compared to conventional extraction methods – Vulcan claims its process creates a surplus of renewable power that the company pumps to the local district heating network.
European lithium
Having these reserves in Europe is critical, as the Old Continent strongly depends on Chinese imports of the material or battery packages. The European automotive industry struggles for survival amid fierce competition from China, which has the advantage of a more established battery value chain, controlling lithium sourcing, refining, and transformation.
Therefore, the European car industry warmly welcomed Vulcan’s venture, to the extent that Vulcan’s first five years of production are fully booked already. Stellantis – the group owning Citroen, Fiat, and Peugeot, among others – invested €50 million in the company, becoming the second largest shareholder. Renault and Volkswagen signed agreements with Vulcan and will use European-mined and produced lithium in their car batteries, with LG also committed.
“I think we play an important role in helping the European car industry survive and also building up an industry we are proud of. We want to produce the greenest lithium in the world in Europe to produce the greenest batteries in the world,” states Wedin with a sense of pride.
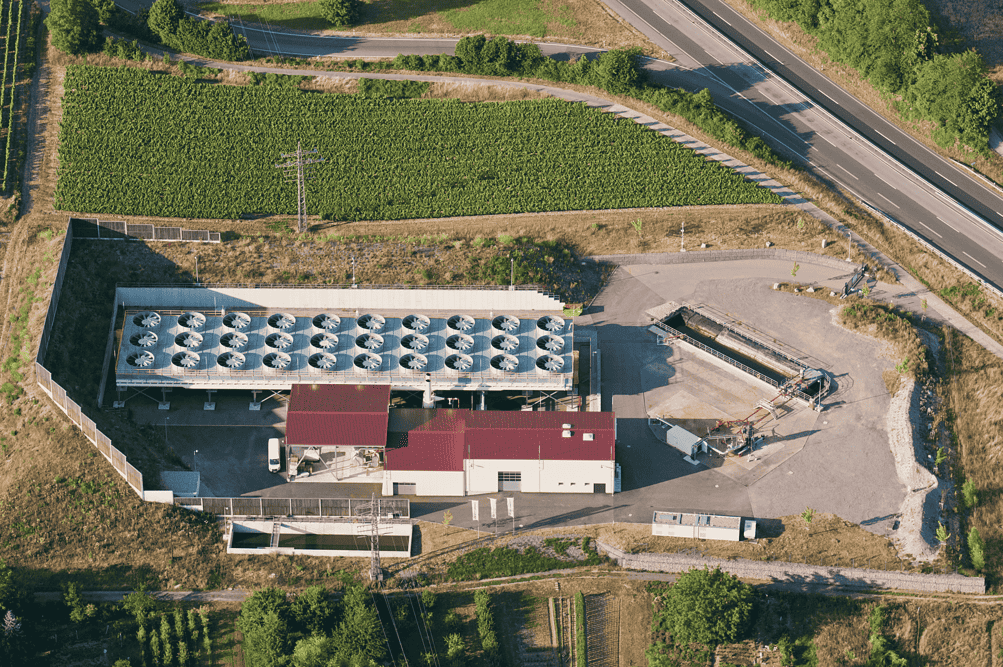
Cheaper electric cars?
One of the factors hampering the sale of EVs in some European countries is their high cost. The battery is the single most expensive component of an EV, with lithium prices heavily contributing to that. “We will be a very low-cost producer because we are processing a waste product from a geothermal plant. It is a green and cheap process, too,” underlines Wedin.
A ton of lithium deriving from hard rock mining costs about $6855. The exact amount of material extracted using evaporation ponds – the most used technique in South America’s brines – comes at over $5870. Vulcan estimates it can produce a tonne of lithium for approximately $4,000. Lower costs also have to do with the fact that Vulcan bet from day one on established technology, integrating different processes together to reduce energy and reagent inputs.
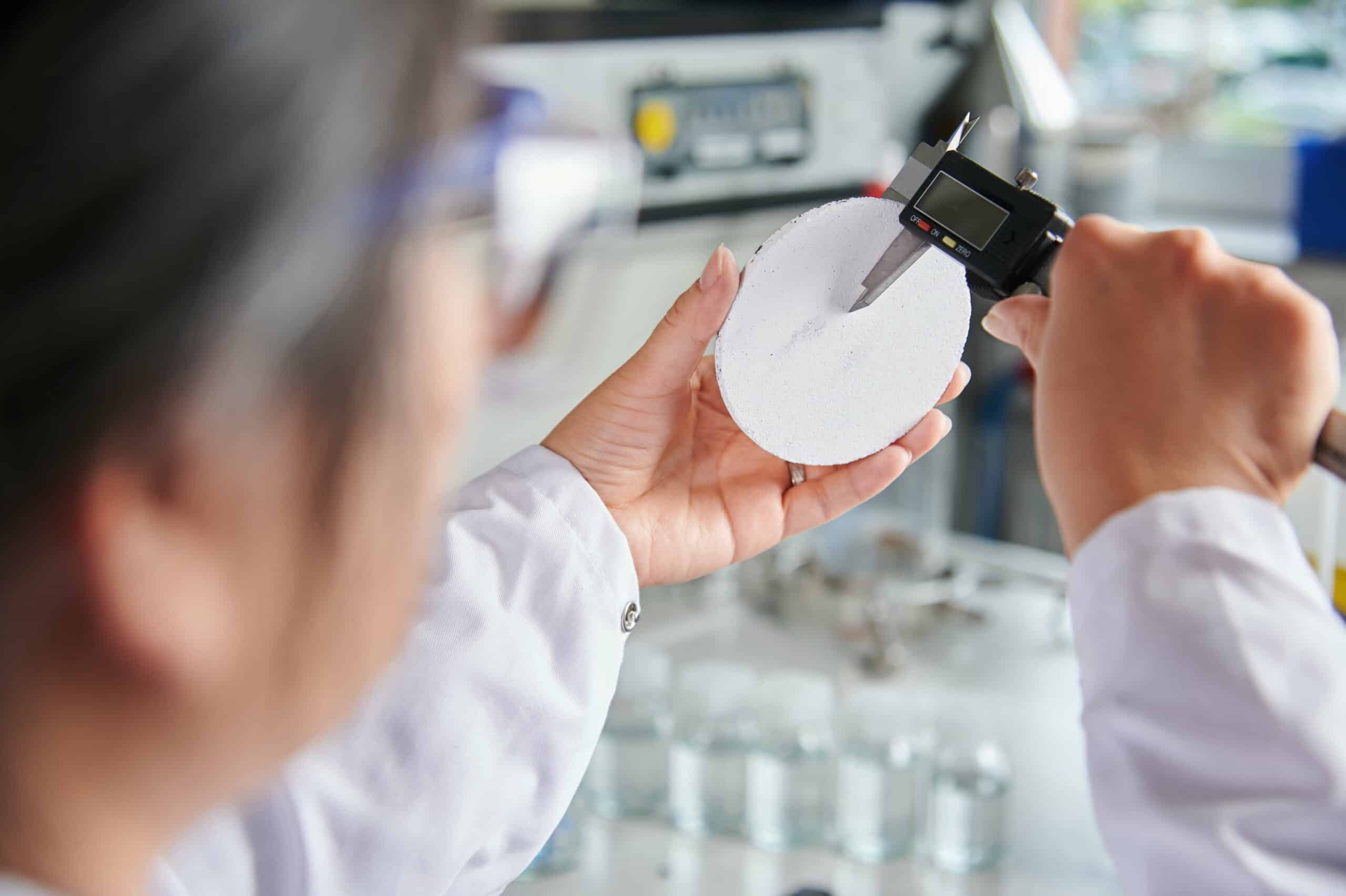
Ready to go
The technology is here, and Vulcan is ready to start operating; the goal is to begin production at the end of 2025. In 2022, the company acquired a geothermal plant in Insheim, Germany, where lithium extraction will happen. Additionally, the company is building a chemical plant in Frankfurt that will take care of the last part of its process: transforming the extracted raw material into battery-grade lithium hydroxide.
“In the coming two years, I hope to successfully execute our phase one commercial development, becoming Europe’s first domestically produced lithium with zero carbon emissions. In the meantime, if we can work with our partners to license our technology to be used in other parts of the world, it would be great,” says Wedin.
Besides, the company needs to raise €1.5 billion in the following months, adding up to the €350 million collected since its founding. Further opportunities will arise by licensing the technology to be used elsewhere in the world, although with an entire focus on execution in the Upper Rhine Valley. Vulcan is exploring other potential European extraction sites, having acquired an early stage permission for a location close to Cesena, Italy.
Motivation
Wedin points at people when asked about the key factor that will make the difference in meeting all Vulcan’s milestones. “Bringing in people from the oil, gas, and chemical industries who built large-scale projects before will make a difference. Many people in our company used to work in those industries and are highly motivated to work in decarbonization projects,” concludes Wedin.