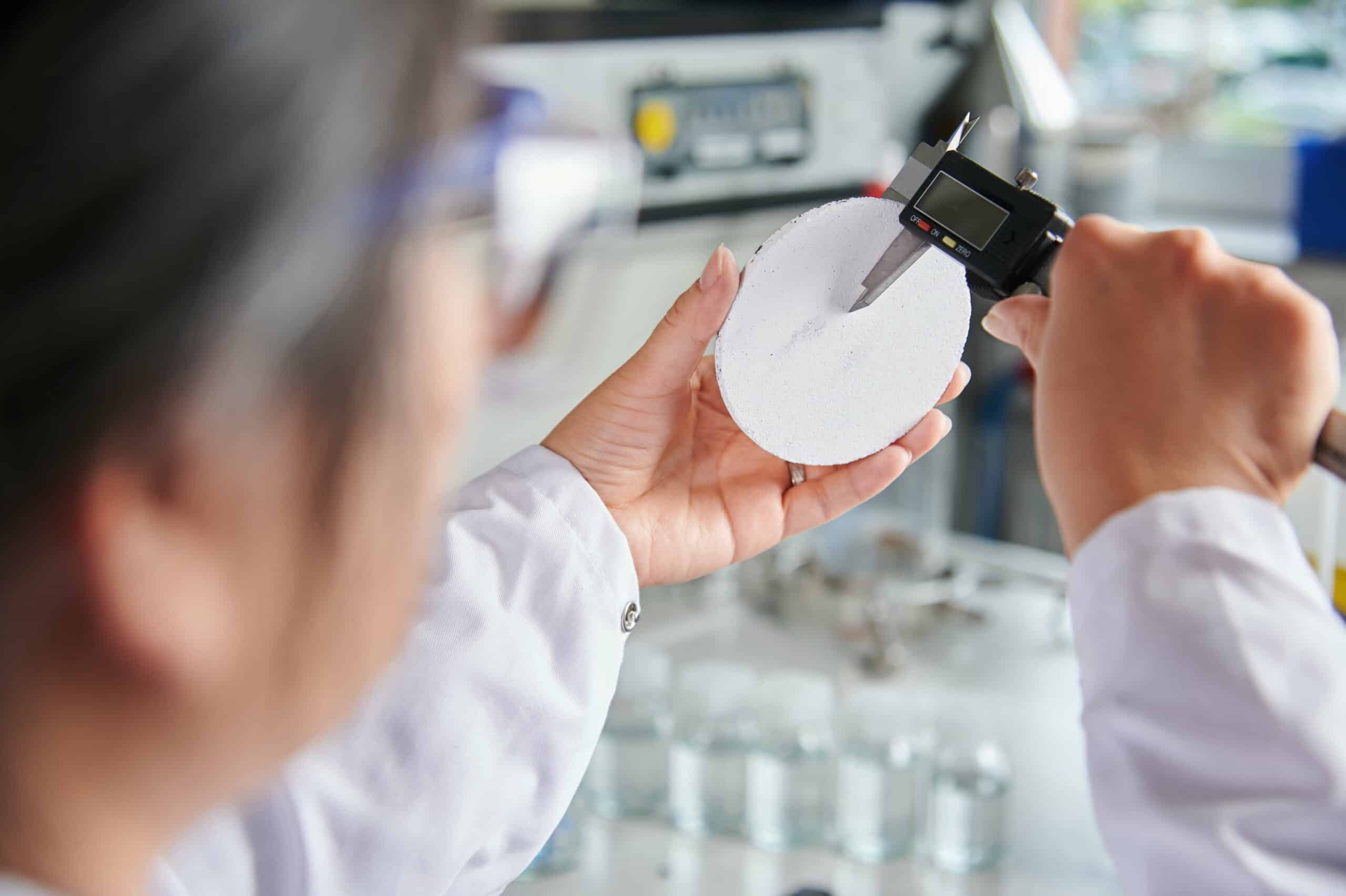
What do an electric car, a laptop, and an electric toothbrush have in common? They are all powered by a lithium-ion battery. These batteries are – at the moment – the most efficient ones on the market and in the past years, more and more objects in our daily lives have switched over to these batteries. As a result, prices have risen and will keep soaring as we shift towards electric mobility. The mining of raw materials comes at a high cost, as it takes a lot of fresh water, involves a lot of deforestation, and emits a lot of greenhouse gases.
However, this does mean that we need more batteries, which in turn means that the waste stream will increase in the coming years. Whereas there are efficient ways to recycle cobalt, copper, and nickel – other minerals used for batteries – lithium – Li – recycling is still not cost-efficient. Scientists at the German chemicals company Evonik are working on a new solution to tackle this problem, and have designed a membrane to selectively collect lithium ions from spent batteries.
“Its design is the key,” Elisabeth Gorman told Innovation Origins. She is the business development manager at Evonik. “The membrane composition selects lithium ions and allows them to move through the crystal structure that we’ve built.”
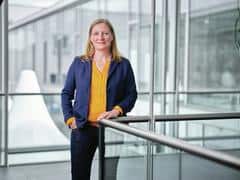
Elisabeth Gorman
Business development manager
Responsible for new business development in the field of lithium recycling at Creavis, Evonik’s strategic innovation unit and business incubator.
Hopping ions
German scientists opted for membrane electrolysis. In short, the process uses electricity to separate Lithium ions by a permselective ceramic membrane – a layer that is both semipermeable and allows ion exchange. Electrolysis is mostly known in hydrogen production, where power is applied to separate water into oxygen and hydrogen. The device to perform it is an electrolyzer, whose main elements are a positive electrode – the anode – and a negative one – the cathode. An ion-conductive membrane separates the two, allowing ions to move through when an electrical potential is applied. This component in Evonik’s method is what makes the difference.
“Compared to conventional techniques for lithium recycling, our electrochemical separation process can produce lithium hydroxide in one step and in very pure, battery-grade form. The technique has the potential to replace the current chemical precipitation process which uses large quantities of chemicals for solid-liquid separation,” Gorman stresses.
At first, lithium-containing wastewater from the black mass recycling process flows between the anode and the membrane. The black mass is the resulting mixture of metals from shredding batteries in a recycling plant – after plastic components are removed – and as such, also contains lithium. When electricity is applied to this water stream, lithium ions move through the ionic conductive ceramic membrane to the cathode chamber. Other ions and water molecules cannot pass through. Then, water on the negative electrode reacts with electrons to form hydrogen and hydroxide ions. These react with lithium ions to form lithium hydroxide, which is the product that is needed to produce new batteries.
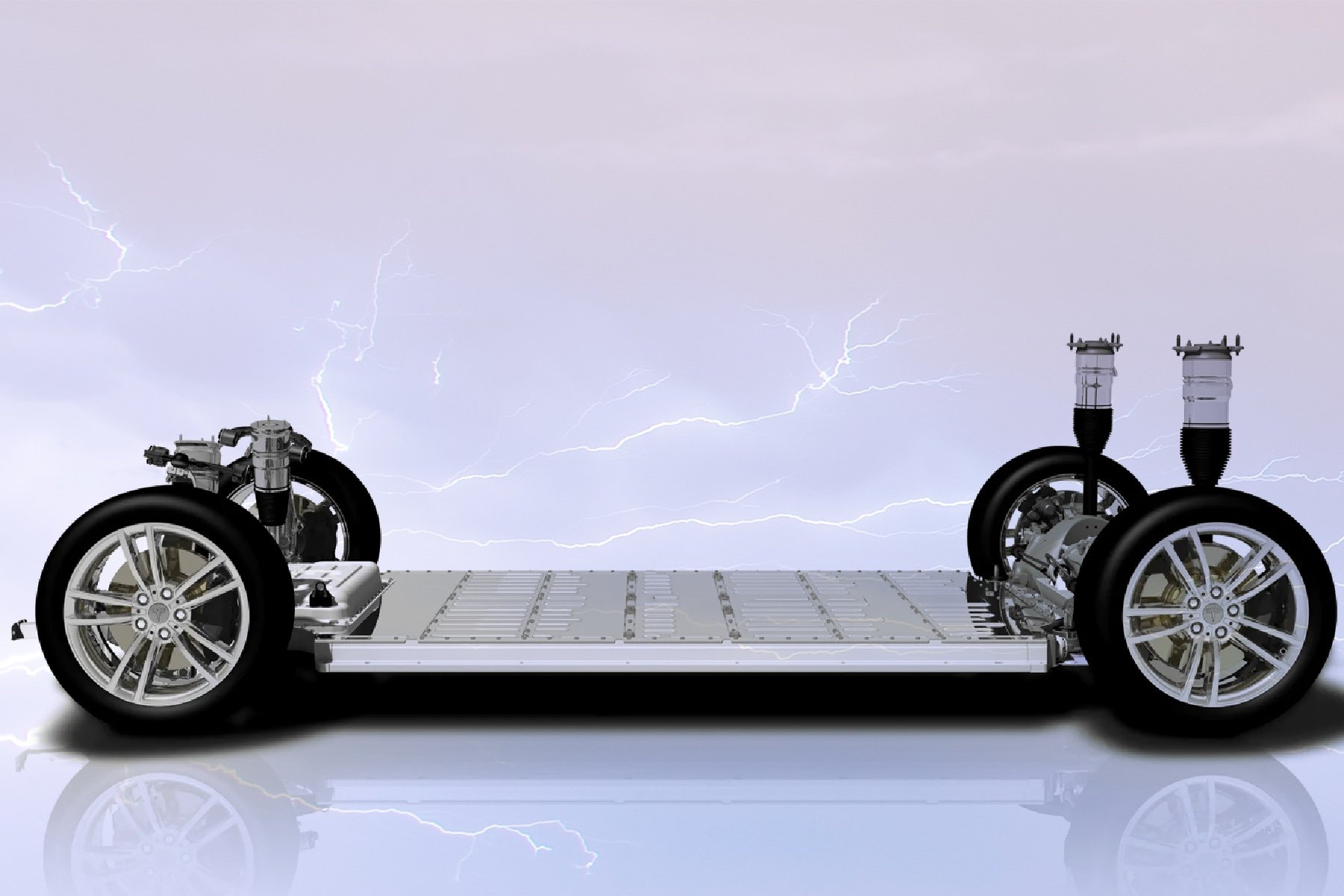
Recycling goals
“Lithium and rare earths will soon be more important than oil and gas. Our demand for rare earths alone will increase fivefold by 2030,” stated European Commission President Ursula von der Leyen when introducing the Critical Raw Materials Act.
In light of this, the European Commission is requiring higher efforts in Li recycling. As of today, it’s estimated that over 1.9 million tonnes are discarded every year. Recycling rates and collection vary depending on the type of battery. The proposed regulation calls for 35 percent recovery of lithium by 2026 – and double that by 2030. It also sets mandatory minimum levels for recycled content. Starting in 2030, the requirement for recycled lithium would amount to 4 percent, then increasing to 10 percent five years after that.r.
According to a paper published by the NGO Transport and Environment (T&E), targets should be set higher. “But by requiring recyclers to recover these small amounts of lithium – only 35 percent by 2030 – policymakers are missing out on a huge opportunity. The European battery industry cannot wait to start building up a domestic supply of critical metals,” the analysis states. T&E advocates for higher rates, as they are technically feasible according to industry best practices, citing an assessment issued by the Circular Economy Initiative Deutschland.
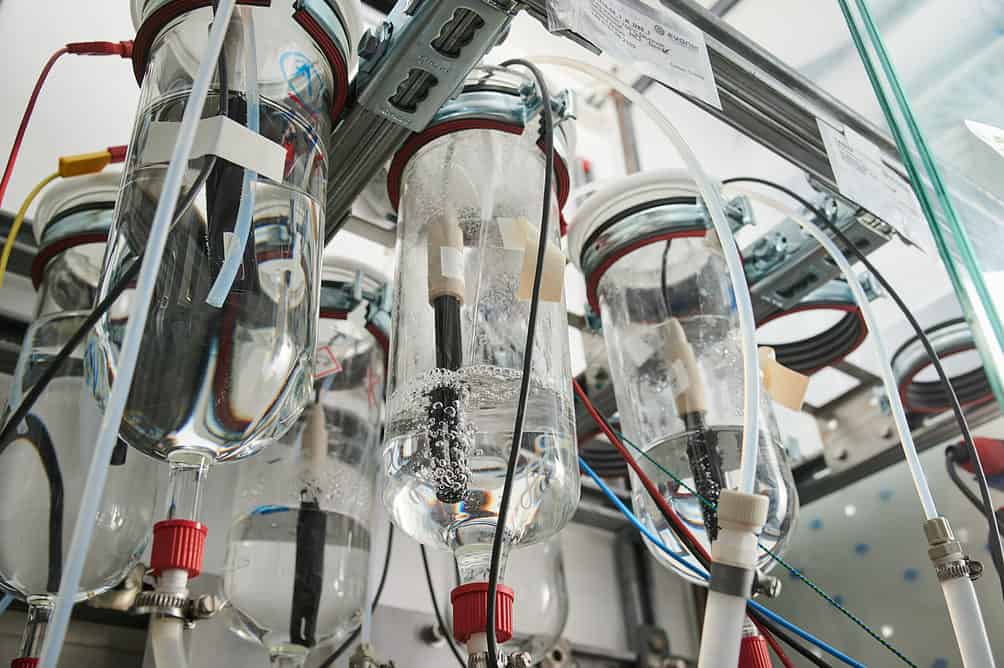
Second mining
Recycling lithium is, in a way, like mining it a second time. Still, Evonik’s concept could also be used in actual mining. Large deposits of lithium brine have been found in German soil. These are accumulations of saline groundwater enriched with dissolved lithium. These could well be the next source of lithium in the near future. Mining would follow the same principle as spent batteries.
“That’s the vision. However, we are in an R&D phase, and readapting the process to this kind of application will not happen within the next two or three years,” clarifies Gorman. In an effort to abandon imports of lithium from countries like Australia or Chile, tapping into European reservoirs would help the European battery industry. Not to mention that transportation from far away entails tonnes of greenhouse gas emissions.
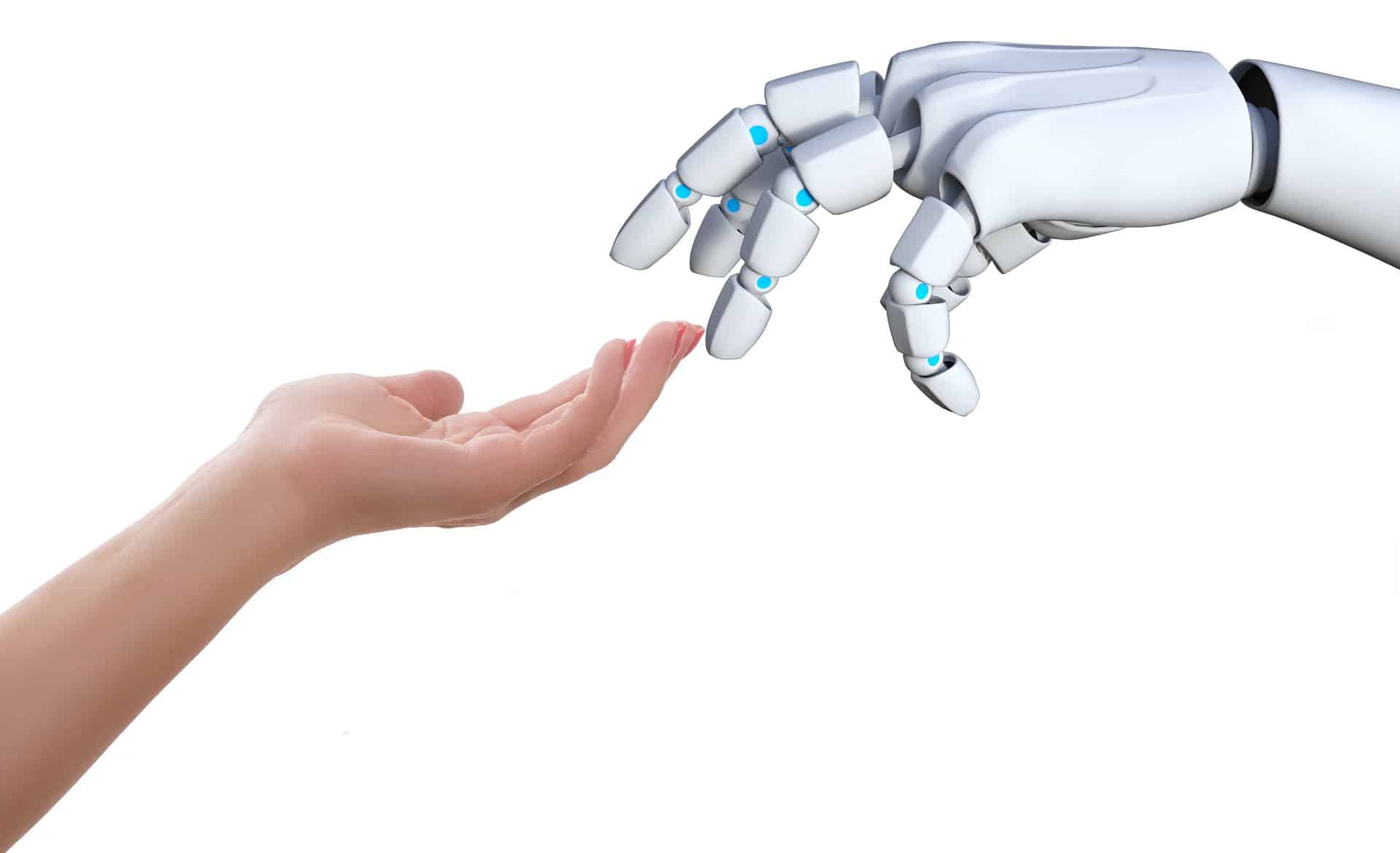
Battery gap
For now, Evonik is focusing on optimizing their method. The team will then work on some prototypes and pilot designs to start scaling up the idea. To achieve this, researchers will stack more electrolyzing cells together, thereby increasing the amount of processed wastewater. In the future, electrolysis could be done inside bigger recycling or battery-producing factories, and close the loop where it started.
Multiple companies have announced plans for battery plants – so-called gigafactories – in Europe, to accommodate the soaring demand. Some of these projects also envision the end-of-life recovery of batteries. On the way to battery independence, technology from Evonik will come in handy.